Welsh Slate Aggregate Perfect for Tensar
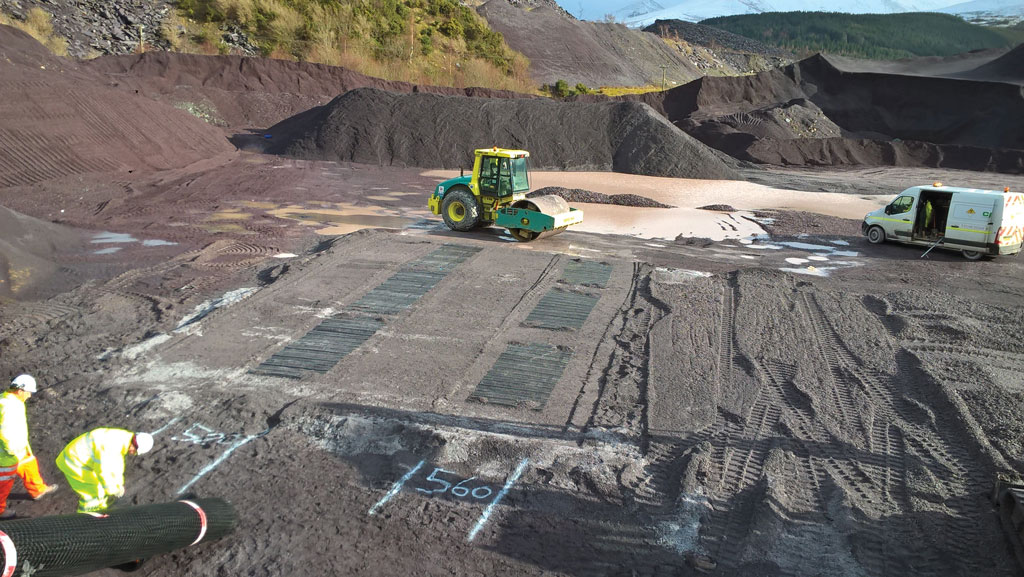
First published in the April 2019 issue of Quarry Management
New study shows slate by-product is cheaper than other aggregates for reinforced earth structures
Slate by-product as an alternative to traditional aggregate fill in reinforced earth structures has been shown to be up to 60% more cost-effective. This is the finding of an award-winning study supported by Welsh Slate, the UK’s leading natural slate manufacturer, and Tensar International, one of the world leaders in technology-driven soil reinforcement and mechanical ground stabilization.
The year-long study was carried out by Owen Bracegirdle, a consultant engineer at independent multidisciplinary engineering, environmental and project-management consultancy Egniol Environmental, based near Bangor in North Wales, just a few miles from Welsh Slate’s main Penrhyn Quarry.
Mr Bracegirdle chose the study, ‘Utilizing secondary slate waste aggregate as an alternative to common aggregate fill within reinforced earth retaining structures’, as his dissertation for a BEng (Hons) in Civil Engineering, and it helped him win the Chartered Institution of Highways & Transportation’s Cymru Wales region award for Emerging professional of the year 2018.
Tensar, who have already suggested slate as the aggregate fill for two major civil engineering infrastructure schemes scheduled to happen in the next couple of years, say it had been apparent, through extensive research and input from industry professionals, that secondary slate aggregate sourced from North Wales was not being used to its full potential. The study set out to establish if secondary slate aggregate (13mm blinding) from Penrhyn Quarry was acceptable for use as the aggregate fill within a Tensar reinforced soil retaining structure.
The selected secondary slate aggregate and all its associated parameters were compared with a commonly used primary aggregate fill (granite/limestone) to not only establish its structural performance and feasibility, but also, most importantly, to highlight the financial benefits of its use.
The study first researched current and relevant design textbooks, online literature and design standards, such as BS 8006, to establish the design requirements and parameters of a suitable aggregate fill within a reinforced soil structure. Observation and analysis of all relevant test results was then carried out to numerically compare slate aggregate against granite/limestone fill.
Additional site and laboratory testing was also undertaken as part of the study to address any gaps in the data. Most importantly, through research and testing, it was found that the reinforced earth design relied upon the reduction factors applied on Tensar geogrid grades.
These reduction factors are derived from the selected fill being used. It was concluded that the reduction factors RFCH (Chemical and Environmental Reduction Factor) and RFID (Installation Damage Reduction Factor) were critical in determining the feasibility of using the selected aggregate fill.
Installation damage testing was carried out at Penrhyn Quarry to ascertain the RFID for the secondary slate aggregate. This determined that the selected secondary slate provided varying design reduction and safety factors over the alternative aggregates.
These subsequent variances were inputted to two design cases. The design outputs highlighted the geogrid requirements and content for both the slate and granite/limestone design cases. The design outputs were also analysed taking aggregate costs into consideration and these highlighted that the slate aggregate not only performed successfully as a structural fill within a reinforced soil structure, but also provided a commercial benefit through substantial cost savings.
In summary, the study highlighted that, in the scenario modelled, the Welsh Slate 13mm blinding provided a 61.49% cost saving over the limestone equivalent. A limestone Type 1 sub-base aggregate (a larger stone usually used for highways applications) was also considered, with the Welsh Slate secondary aggregate delivering a 21.77% saving.
Craig Roberts, Tensar product and technology manager for walls and slopes, said the study was something Tensar had wanted to do for some time, as they had conservatively used slate fill previously on private schemes but required official test results for public projects.
‘We were more than happy to get involved as it served a dual purpose,’ he said. ‘We had always been confident that slate could be used as an alternative but now we have the proof, through testing, and this should give us an advantage at the tender stage. Without Owen and Welsh Slate, we would have had to get the testing done another way.’
He added: ‘Using slate could require additional stronger layers of geogrid, as the material can cause minimal additional installation damage compared with granite and limestone, which has to be accounted for within the design. But the additional cost of this is more than offset by the overall structure savings.’
Owen Bracegirdle said: ‘Being from the area and growing up around the slate tips, it was just something I wanted to do and was really interesting to me. I’m really happy with the results from a commercial aspect, and with the award from a personal one.’
Sean Edwards from the aggregates division of Welsh Slate, now part of Breedon Group, said: ‘We are always looking at ways to maximize the yield of material extracted and material recovery from historical slate waste tips and are delighted to have helped Owen not only reach this commercial conclusion, but also win an award in doing so.’
- Subscribe to Quarry Management, the monthly journal for the mineral products industry, to read articles before they appear on Agg-Net.com