Pioneer solve pump problem for Welsh Slate
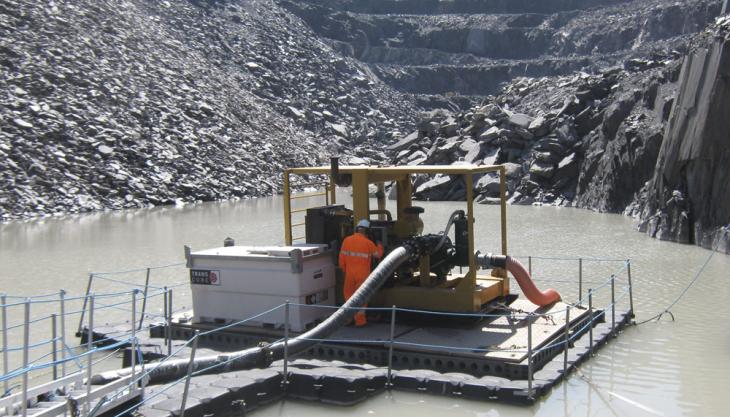
Change of pump system at Penrhyn Quarry saves money and reduces environmental impact
AN overhaul of the pumping system at their main quarry has seen leading UK slate manufacturers Welsh Slate achieve a hat-trick of benefits through increased production and reductions in not only their operating costs, but also their impact on the environment.
The company’s largest quarry, Penrhyn, at Bethesda, near Bangor, in North Wales – the largest single-site slate quarry in the world as well as the oldest, dating back some 400 years – has suffered a series of inefficient and expensive pump systems, and the latest, which was installed more than a year ago, has been no exception.
Given that 85% of North Wales slate now comes from Penrhyn, Welsh Slate’s purchasing manager Edward Griffiths decided the situation needed resolving once and for all and enlisted the help of Nottingham-based Pioneer Pump Solutions.
His brief to Pioneer was to minimize the environmental impact of the pumping application through better efficiencies, reduce operating costs, and increase plant production (the site produces 500,000 tonnes of usable slate annually for roofing, architectural materials, walling, rockery, paving and aggregate for gardening and construction) by reducing pump downtime (due to breakdowns) and faster dewatering, as flows of more than 100 litres/s are often required.
The existing system used two 2400 high-head 90kW submersible pumps and two diesel generators mounted on two pontoons with four 350m lengths of 6in and 8in hose, which often leaked. This system had to carry the water some 55m up and out of the quarry. The 90kW pumps were capable of pumping a maximum of 50 litres/s each, giving a less than ideal total of 100 litres/s.
Running an average 160h per week and using more than 7,000 litres of fuel, Welsh Slate’s annual fuel consumption was amounting to more than 374,000 litres and costing the company almost £250,000. In addition to this, the operation was producing almost 1,000,000kg of CO2.
Pioneer’s new scheme involved replacing the two submersible pumps with a single 150 clear-liquid medium-head 112kW diesel pump capable of pumping a minimum 100 litres/s, mounted on a plastic pontoon with one fuel tank and 30m of 8in wire-armoured hose, and renovating the existing 6in and 8in hoses.
Even with a 68kW decrease in power, the new scheme reduced weekly fuel consumption to 4,480 litres, the total fuel used per year to less than 233,000 litres, and the annual fuel bill to £150,000. At the same time, the operation’s carbon footprint has been reduced by 40% to just over 600,000kg of CO2.
Pioneer’s system has saved Welsh Slate more than £120,000 per year in operating costs (fuel + rental rates) and 370,000kg of CO2. Production has increased due to faster dewatering (flows of 102 litres/s are now the norm and can be increased to 140 litres/s, if required), while pump breakdowns – which were accounting for a loss in production of approximately one day per month – are now zero.
Edward Griffiths said: ‘It did feel like we were sending men down there all the time to repair the system. What was taking us 24h a day, seven days a week now takes just six hours in the morning. It’s hassle-free, fuel-efficient pumping.’
Pioneer’s general manager, Kieran Gagg, added: ‘When Welsh Slate contacted us, we saw it as an exciting opportunity to do what most would see as an impossible task and we are delighted it has been so successful for them.’
Welsh Slate is used worldwide on projects as diverse as Buckingham Palace and Blackpool Tower, the Welsh Senedd, and heritage buildings in Australia and New Zealand.