Ammann introduce the ARX 110-2 and ARX 90-2
TWO new articulated tandem rollers from Ammann offer advanced machine control that is designed to improve safety and productivity on the jobsite. The Ammann ARX 90-2 and ARX 110-2 articulated tandem rollers utilize the next generation of human-machine interface (HMI) to facilitate easy, efficient operation.
One component of HMI is fingertip steering (FTS), which makes the rollers more operator friendly, comfortable, and easy to control. FTS replaces the traditional steering wheel and allows operators to keep both hands on the armrests for enhanced comfort and control. It also offers palm support that prevents fatigue and injuries from repetitive motions.
‘Operators love the fingertip steering,’ said Josef Dementev, global product specialist at Ammann. ‘Their workday is much less stressful, which makes them more productive – and makes the jobsite safer too.’
The new compactors follow the Ammann Solid Power DNA and are said to excel in productivity, ergonomics, serviceability and sustainability, delivering a wide range of benefits such as operating weight, compaction width, variable frequencies, compaction power, and off-set mode (crab mode).
The machines are said to be most productive when used in high-volume asphalt applications such as highways, industrial developments, parking areas, and airfields.
In addition to fingertip steering, among other key features of the new rollers are the machine design, operator station, drum construction, and engine compartment. Immediately apparent is the fact that the ARX 90-2 and ARX 110-2 were designed without front and rear crossbeams. This modification provides superior visibility and improves safety. ‘The lack of beams was key to creating the new symmetrical cab, which is among the key enhancements,’ said Mr Dementev.
Design changes also make the machines more compact while expanding sight lines to all drum surfaces and edges. According to Ammann, the 360-degree visibility from the operator station establishes a new market standard. The spacious, symmetrical cab, which is suspended and isolated from external heat and vibration, integrates four ROPS posts directly in the main structure and close to doors, rather than in the cab’s corners, providing the operator with a superior view of the entire machine.
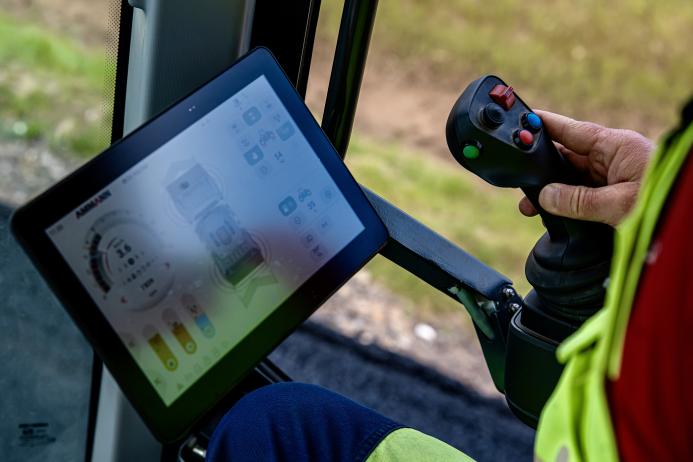
The innovative operator station has integrated, centralized controls that are easy to reach at all times, regardless of the seat position. This approach reduces reaction times for increased safety. The operator’s seat is fully adjustable, with a 270° rotation to optimize visibility from the cab, whilst a new 10in control display helps operators manage all machine functions simply, safely, and quickly. This includes vibratory parameters, lights, and ACEforce – Ammann’s proprietary intelligent compaction system.
In addition to displaying machine functions, the monitor provides an overview of fluid levels, indicators, machine status, and warnings. The display is installed on an adjustable support, in front of the operator, and moves with the seat for easy viewing when working in forward and reverse.
The operating width of the ARX 90-2 and ARX 110-2 is 1,680mm (66.1in). Standard on both rollers is a two-stage vibratory system with a range of frequencies that helps operators precisely adjust compaction output. The ARX 90-2 / ARX110-2 have adjustable frequencies ranging from 37–54Hz and are able deliver compaction output in the range of 47–120kN per drum. A high-frequency (HF) version – designed chiefly for the US market – has an enhanced vibratory system that can reach additional frequencies for further compaction speed.
The rollers are available in two main emission stages. Machines meeting US EPA Tier 4f / EU Stage V emissions standards for highly regulated countries are equipped with Perkins 904J diesel engines with power output of 90kW (121hp) and after-treatment technology (EGR+DOC+DPF+SCR). Machines for less-regulated countries (US EPA Tier 3 / EU Stage IIIA) are equipped with a Perkins 904D with power output of 90kW (121hp) with EGR valve.
The rollers also reflect Ammann’s commitment to lower the total cost of ownership and machine maintenance. Here, the focus has been to reduce the volume of fluids required and to make service points extremely accessible. This commitment – known as ECOdrop – makes all new products significantly more environmentally friendly.
As part of ECOdrop, the rollers utilize EcoMode, which enhances fuel economy and reduces fuel consumption by 8% compared with the previous generation. There are four main service intervals (250h, 500h, 1,000h, 2,000h) with integrated alerts to inform the operator when maintenance is due. In addition, an advanced drum drive system reduces gearbox oil usage by 25% compared with the previous generation of machines, whilst the drum bearing oil bath fluid has been reduced by 7%. The articulated joint and hydraulic cylinders are completely maintenance-free.
The minimal maintenance that is required is now faster and more convenient thanks to a highly accessible engine compartment with a robust design that protects all major components. All maintenance and service points are accessible from the ground and the machines are equipped with external drain points for all operational fluids such as engine oil, hydraulic oil, and coolant.
All rollers are equipped with an auto-diagnostics system that communicates with service technicians, whilst external testing ports on hydraulic components allow quick diagnosis and reduce machine downtime.
A wide range of options can make the machines more productive, comfortable and serviceable. Off-set (crab mode) improves machine versatility by increasing working width and permitting compaction close to curbs. The machine is also available in a ‘combi’ version, with four tyres to increase machine usage in a wider range of applications.
Moreover, the ARX 90-2 and ARX 110-2 can be equipped with an oscillation drum, which uses the back-and-forth movement of the drum with a constant static load to achieve compaction goals in sensitive applications (such as cold joints, thin layers etc). When oscillation is not required, the ARX 90-2 and ARX 110-2 utilize a second drum with a heavy-duty, two-stage vibrator and easy adjustment of amplitude and frequency.
The ACEforce system makes it easier for operators to track compaction progress. This measuring system shows the actual kB value on the display and thus significantly reduces the time required to achieve the maximum compaction level.