Condition Monitoring for Aggregate Screens
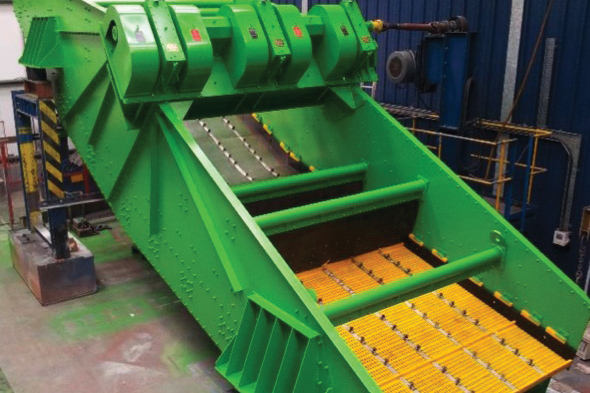
First published in the February 2016 issue of Quarry Management as Screen Saver
Jeff Buxton, group sales manager with Don Valley Engineering Ltd, discusses condition monitoring for linear screen drives and vibrating machines
As global demand for aggregate materials increases year on year, producers are under ever-increasing pressure to reduce their operating costs while delivering increased production, often at short lead times and with penalties for late delivery. In the face of fierce competition, producers recognize the importance of having reliable plant and equipment to maximize and protect their profit margin. It is vital, therefore, that producers ensure their production machinery is working at the highest possible level of availability.
Don Valley Engineering understand these requirements and have been working closely with their customers to achieve high reliability and availability of plant such as linear screens and vibrating equipment, to ensure it offers longevity of service at maximum operating levels. With these goals in mind, Don Valley Engineering have developed a condition-monitoring system that can be fitted to key components which have the potential to fail or cause serious plant downtime and affect production output.
The aggregates industry is a very aggressive industrial environment for all types of machinery. Certain types of plant, such as vibrating screens and rotating machinery, by the very nature of their operation, can fail catastrophically. Therefore, the basic design criteria for manufacturers of today’s screening technology is that it must be built fit for purpose. The demand from material producers and end-users is for better screening performances, better quality end products, reduced handling logistics and competitive prices, whilst construction industry requirements include a wide range different material size fractions and fines.
Difficult-to-handle abrasive materials and particulates increase the risk of possible plant failure through their contact with, for example, bearings or wear parts. Wear surfaces can be protected to some extent with new lining technologies and other protective methods. However, for moving parts, the solution is not so simple. It is necessary, therefore, to identify where the potential risk occurs and to provide preventive maintenance, or at least to have the facility to monitor the condition and any change to the key components during normal operation. An early warning alarm can be provided that triggers further investigation of a component before it fails completely, thereby reducing the risk and high cost of a breakdown.
This drive to achieve high reliability and availability of equipment is what led Don Valley Engineering to consider the use of condition monitoring and preventive maintenance systems to identify potential problems before they happen.
Many factors influence the reliability and availability of plant and machinery, including: the age of the plant and its production equipment; the ability to maintain the equipment; sufficient skilled and specialist staff; the resource available to carry out critical maintenance routines; the availability of spares; component lead times; commercial justification for strategic and critical spares holding etc. The use of best practice, process flow and equipment design is critically important and certain questions need to be considered, such as: Is the equipment fit for purpose? Are there safety margins built in or, in cases of old equipment, have the operating parameters changed from the original design criteria? Has the equipment been correctly installed to maximize production? Is the plant being operated at higher production levels than the operating design parameters it was designed for? Are new throughput rate and material characteristics or size fractions required of the screen in line with the manufacturer’s recommended standards? Is there a planned maintenance schedule in place and is it carried out as per the plan? Is there a preventive maintenance system in place?
One consideration is the condition monitoring of key components. This can be used to continuously examine the performance of these components so that an intervention can be planned before total failure occurs. It can establish that something has changed within a component which is critical to the operation of the machine or within the equipment before it fails. This could be the measurement of vibration, temperature, rotation, ground vibration, oil level or electrical conditions. It could include the use of accelerometers or vibration sensors to measure changes in vibration frequency or noise within a bearing housing, or temperature sensors to measure any thermal increase in a component’s normal operating conditions.
Don Valley Engineering now offer condition monitoring for the measurement of screen vibration on their exciter-drive range of gearboxes (bearing vibration, shaft rotation, drive rotation, oil presence, oil or bearing temperature in some cases pressure loss within auto-grease systems, ground vibration, electrical instrument detection of voltage, current and power etc). One example involves measurement of the vibration frequency of the main bearing within the housing of a linear screen exciter unit – the main drive mechanism that creates the vibrating movement of the screen in a upwards and forwards motion. This vibration, which promotes the movement of material on the screen media surface to create particulate and size fraction separation, is typically generated by either a single exciter gearbox unit or series of exciter gearbox units connected in line by means of a cardan shaft connected to the main drive.
Each exciter unit consists of a sealed mild steel fabricated boxed housing arrangement, complete with two shafts, mounted in parallel, each fitted with a helical gear arrangement. Each shaft is supported by an independent bearing housing mounted either side of the gearbox. The gearbox is oil filled and sealed, and at the end of each shaft a set of out-of-balance offset weights is positioned to provide an adjustable degree of vibration and the linear motion of the screen.
Condition monitoring of the exciter shaft bearing is key to establishing early signs of bearing failure. This is achieved via an accelerometer sensor fitted to each bearing housing that measures the fine vertical movement generated by the bearing’s natural vibration and signals the frequency of this vibration to a processor control panel. Vibration sensitivity can be pre-set to represent normal minimum and maximum operating conditions.
If the vibration frequency departs from the pre-set parameters, the change in frequency is detected by the sensor and a signal is sent to the remote processor and indicator. The adjustable pre-set points can be set for each sensor port. A visual indicator shows the level of vibration from each accelerometer, and its set points. If the set point is breached the system will issue an alarm signal to the local processor, triggering a visual alarm in the form of a flashing beacon, and also via Ethernet to the main SCADA system. The alarm and optional beacon (if fitted) provide a visual display local to the main control room and local to the machine itself, indicating that further investigation may be warranted to establish if action is required.
The system processor is fitted local to the equipment and connected by means of braided cable from the processor port to each sensor. The processor itself is housed within a GRP panel and features a 3.5in TFT touch screen with an easy-to-navigate menu that allows users to: set data sampling periods, alarm threshold levels, and delay times on a channel-by-channel basis or across all channels. The system accepts 4–20mA inputs and can be used to monitor many different types of sensing device. AC outputs are available via door-mounted BNCs for easy analysis. Modbus and remote PC monitoring are also available as options. The general-purpose top entry constant current accelerometer with isolated AC outputs is robustly constructed from stainless steel, offer long-term vibration analysis in harsh environments. Internal electronics are isolated to minimize vibration noise with increased bias stability. The units are sealed to IP67 and include integral stainless steel over-braided ETFE cable with a wide range of fittings and mountings.
Condition monitoring can be used to establish a wide range of equipment parameters, to provide an early warning that conditions have changed. Don Valley Engineering can provide and install condition monitoring for their own range of screens, feeders and centrifuges, as well as for third-party screening machines and material-handling equipment.
Vibration sensors have proven to be a valuable asset in the toolkit of plant and maintenance engineers, but are only effective when specified and installed correctly. If this is achieved, accelerometers will play an important role in helping aggregate producers meet growing demands for material by ensuring optimum machine availability, productivity and profitability is achieved.
For further information visit: www.donvalleyeng.com
- Subscribe to Quarry Management, the monthly journal for the mineral products industry, to read articles before they appear on Agg-Net.com