New MVX Valve from MID
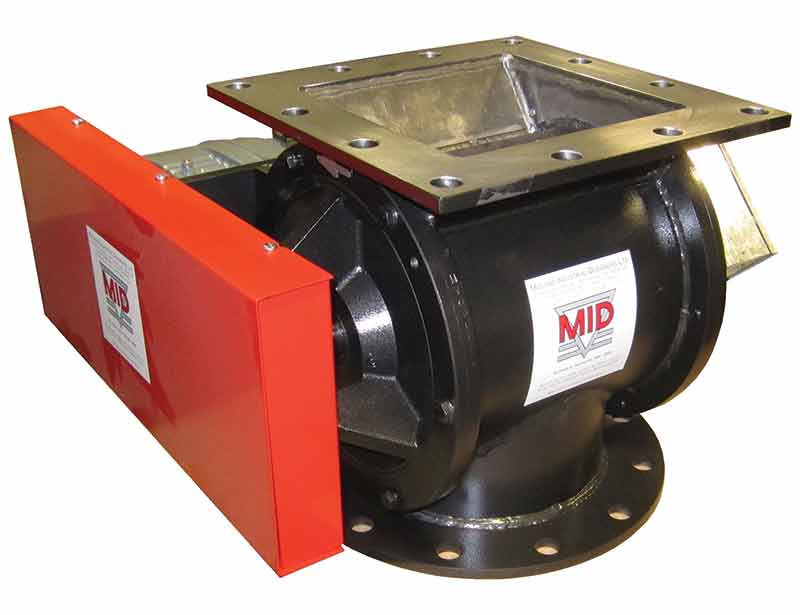
First published in the August 2015 issue of Quarry Management as Valuable and Versatile
New MVX rotary valve from MID lasts four times longer than a cast iron valve and can be made to fit anywhere
Over the last 50 years, Nottingham-based MID have earned a reputation for designing valves that save their customers money. Robustness, reliability and, in many cases, completely maintenance-free operation go some way to reducing operating costs, but, ultimately, it is the length of the valve’s useful life and the frequency and cost of refurbishment that more directly influence the cost of ownership.
There are many cast iron rotary valves on the market today, and most manufacturers offer a range of hard coatings on wear components to extend the useful life of their valves. If the coating remains intact, a valve should show some improvement in its ‘life’ compared with a cast iron version, but a dropped spanner or some other contaminant that finds its way through to the valve could cause the coating to start peeling off sooner rather than later.
In addition, the lack of dimensional flexibility in the casting process means that unless the installation meets with the standard ‘off-the-shelf’ valve dimensions available, standard cast valves often will not fit.
One of the inevitable consequences of mechanical wear is a component’s dimensional loss from its original state, and in the case of rotary valves this can cause a loss of process efficiency at best, and at worst can bring production to a halt. Either way it will cost the operator money.
Most engineers understand the effect of wear on their equipment’s performance and this will be factored in to their preventative maintenance schedules, but how much time and money could be saved if the maintenance intervals were significantly extended? How much product is lost through having to stop production to remove and replace a rotary valve? How much more time could be directed towards other parts of the process that might need attention? It is rare to find any maintenance department that has the luxury of being over-manned, so focusing on reducing the effect of wear is hugely beneficial from a cost-of-ownership perspective.
Operators are repeatedly asked to make choices between different products pitched at different prices, and in many cases spending less on a product does not necessarily ensure a better deal – in many cases the complete opposite is true.
When purchasing a rotary valve, the operator is also ‘buying’ an obligation to maintain it throughout its useful life – however long that may be. Whether they actually measure and record every occasion they tighten the packing on the shaft, or every time they have to free the valve after it has seized, or every minute spent sweeping product off the floor, is irrelevant – ignorance in this case simply means that they are not aware of what the valve is costing them to ‘own’.
The length of the useful life of a rotary valve is one of the biggest factors that influence the ‘cost to own’. Repetitive maintenance costs can mount up, but the losses incurred when having to stop the valve to replace it are significant. Even planning to do this during ‘shutdown’ makes no difference – it is time spent on an activity that could be avoided, thereby allowing labour to be directed elsewhere.
MID are capable of manufacturing fabricated versions of all of their cast rotary valves, and the new MVX range is manufactured with 400 wear plate in the bore and 400 wear plate on the rotor – immediately extending the life of the valve by a factor of four (fig. 1). So, if an operator usually plans to replace/refurbish a cast iron rotary valve after six months in service, this interval immediately extends to two years – a significant difference that will have an immediate impact on productivity and overall costs.
MID’s rotary valves range from the cast iron MV valve to the alumina ceramic-lined TWA valve – the only other rotary valve that has an even lower cost of ownership than the MVX. The fabricated MVX can be manufactured to replace any existing rotary valve and, compared with the TWA range, its price is more accessible for most maintenance budgets.
The graph in figure 2 shows a comparison between the MVX and virtually any other cast iron/hard-coated rotary valve on the market.
As soon as a cast iron or hard-coated valve is purchased, the maintenance clock begins ticking, and it may not be long before there is a need to retighten or replace the gland packing to prevent shaft leakage – a highly repetitive activity which slowly increases the cost of ownership. When the valve reaches the end of its useful life it will need to be replaced or refurbished, but either way production will have to be stopped, and this is undoubtedly where the biggest costs of ownership are incurred.
Conversely, an MVX will not leak any product from the shaft, and when a cast iron valve is coming to the end of its useful life, the MVX will still only be a quarter of the way towards needing to be refurbished. Not only will this have an impact on productivity and costs, but it will also help reduce employees’ exposure to risk by not having to replace the rotary valve three times.
MVX rotary valves are fitted with MID’s mechanical shaft seals, which drives down costs even more. Guaranteed to not leak any product from the rotary valve shaft for the life of the valve, they are preset in the factory before despatch, so operators will not need to spend any time maintaining the seal. Moreover, as product losses are completely eliminated, the working environment will be cleaner and safer.
Many material-handling systems are designed around standard products – and understandably so. But there are many occasions where this is not possible. An operator might need a valve with a larger capacity than the available space allows, or perhaps one with a much longer body or with an offset inlet to marry up with other pieces of equipment. In all of these cases, and many others, the MVX can be designed to fit neatly and tidily into a scheme.
Long wear life together with a rotor shaft that is guaranteed to not leak product means the MVX is not only one of the most adaptable highly configurable valves on the market today, but also one of the cheapest to own. For more information visit: www.mid.uk.com
- Subscribe to Quarry Management, the monthly journal for the mineral products industry, to read articles before they appear on Agg-Net.com