MID Offer Solution to Wear in Asphalt Filler Dust-Handling Applications
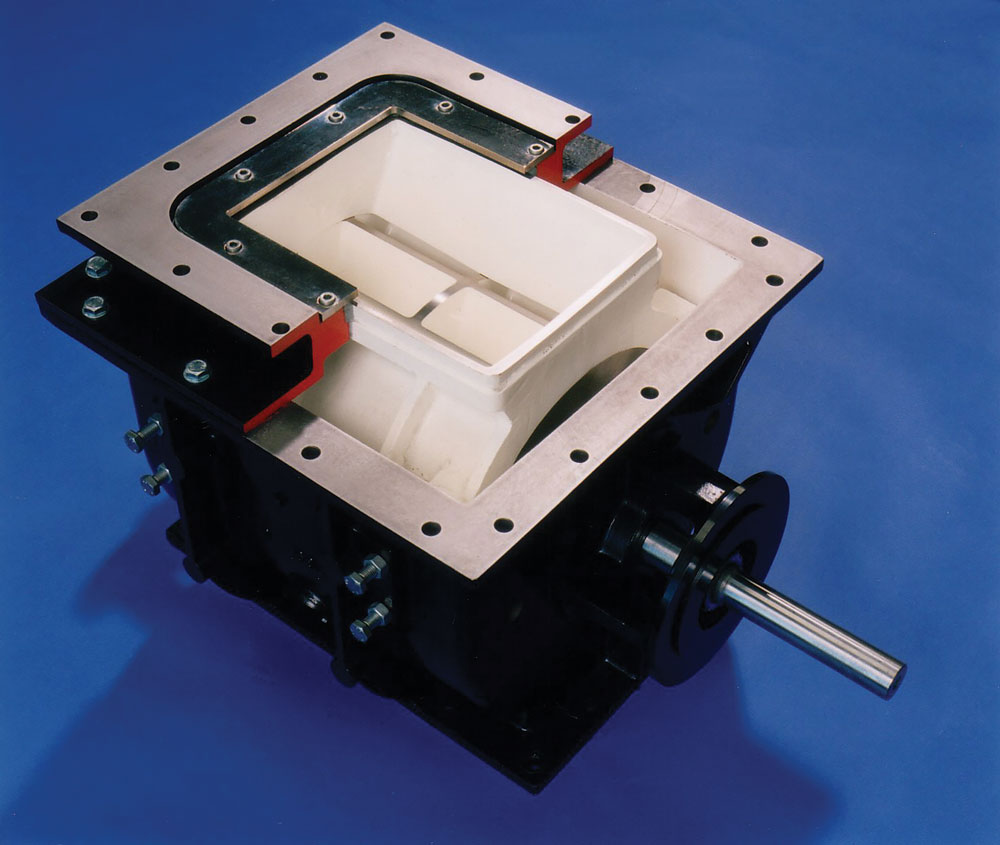
First published in the January 2017 issue of Quarry Management as Fit and Forget
TWA rotary valves from MID provide a cost-effective solution for overcoming wear in asphalt filler dust handling applications
The ‘total cost of ownership’ of any product is a financial estimate of the direct and indirect costs incurred throughout its life, and is a much more useful comparison to make between different products when considering the realistic, overall cost of purchase. Consideration of the purchase price alone could turn a cost-saving intention into a real-life burden, with ever-increasing maintenance costs and loss of overall production.
Asphalt filler dust rotary valve applications are a typical example where decisions made with the intention of spending wisely can very quickly result in ownership of a valve that needs constant attention just to keep it going, turning what was thought to be a balanced, considered decision, into a potential bad choice.
The cost of maintaining the valve can greatly outweigh the purchase cost, and the reason why some people are caught out is that not only are these costs significant, they are often completely hidden at the time of purchase.
MID’s TWA rotary valve was developed in the late 1990s and remains one of the most wear-resistant valves on the market today. Originally developed to handle fly ash for CEMEX, even today it still represents a significant diversion from traditional rotary valve design.
Unlike traditional designs, the outer body is not subject to any wear whatsoever and remains with the valve for life. Instead, the rotor is combined with a liner or ‘saddle’ that sits directly above, in very close proximity, and provides the ‘seal’ that the outer body provides in traditional valve designs.
Designing the valve in this way results in two advantages; first, knowing that there are only two components in the valve that will wear, ie the liner and the rotor, means that, subject to the valve not being damaged in any way, refurbishment costs are fixed, predictable and low, given the extended life of the valve. This allows the user to understand how much the valve will cost to own over a period of years, thereby allowing for more accurate budgeting.
Secondly, the design of the valve internals determines the machining processes that will need to be employed to restore the valve to its ‘as new’ condition. This is important, because if harder, more wear-resistant materials are used in a valve, it is necessary to consider how these materials are going to be machined when refurbishing the valve, and how much this whole process is going to cost. The geometry of the TWA internals is such that diamond grinding is all that is needed, which means that it is now possible to use very hard, wear-resistant materials that are too hard to be processed using traditional machining methods such as boring, turning, milling and drilling.
The TWA comes with two levels of wear resistance. The Nihard version lasts at least five times longer than a standard cast iron valve and can be adjusted to accommodate wear, while the flagship version of the valve comes with 98% alumina ceramic tiles with a Moh hardness of 9 and lasts 10 times longer than a standard cast iron unit. In addition, the fitment of MID’s mechanical seals is standard with these valves, which means that the shaft seal is guaranteed not to leak any product and will not require any routine maintenance for the life of the valve.
Case study
In April 2012, a very large UK-based international quarrying company purchased a ceramic-tiled TWA rotary valve to replace an existing asphalt filler dust valve. Product was pouring out of the shaft seal of the existing unit along with the conveying air, which was also leaking past the rotor rather than conveying the dust into the silos.
The ceramic TWA was fitted and the shaft leaks stopped instantly. Twelve months later the site had some issues with its filter bag house and MID were asked to check the clearance on the valve so it could be ruled out as a potential cause. After 12 months service, the valve had worn no more than 0.001in – and this was in a pneumatic conveying application handling hard, abrasive filler dust; an application that could have worn through a cast iron valve in around six months.
Today, four years later, the valve is still on site, still running, has not leaked any product and has not yet needed to be refurbished. So far, owning the valve has not cost the customer a penny more than the price paid to purchase it four years ago. For more information visit: www.mid.uk.com
- Subscribe to Quarry Management, the monthly journal for the mineral products industry, to read articles before they appear on Agg-Net.com