Martin Engineering’s Conveyor Inspection Programme
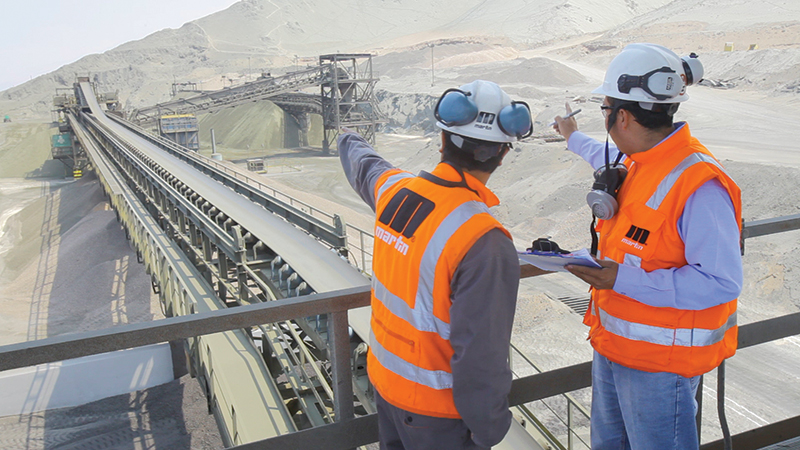
First published in the August 2014 issue of Quarry Management as Walking the Belt
Martin Engineering explain how their Walk the Belt programme can reduce costs and improve safety
One of the global leaders in bulk material handling technology is helping conveyor users reduce operating costs and improve safety with inspection and maintenance programmes designed specifically for each individual system. The Walk the Belt programme from Martin Engineering provides regularly scheduled reviews of belts, cleaners, tracking, chutes, dust control and other components by experienced specialists with the training and expertise to maximize productivity and reduce downtime.
Featuring immediate transfer of data and photos to facility managers, the programme establishes an evolving record of each belt for current analysis and future reference. By taking responsibility for routine maintenance and identifying potential issues before components fail, technicians assist customers in maintaining system performance and extending service life, while minimizing fugitive material and unplanned shutdowns.
‘Every conveyor is different, even within the same facility,’ observed Martin Engineering’s global market development manager, Mark Stern. ‘So we create a specific inspection plan based on the design, capacity, throughput requirements and the desired level of fugitive material abatement.’
Mr Stern said that while it is common for conveyor owners to perform service on their systems only when a component fails, it is actually less expensive in the long run to incorporate continuous maintenance into a plant’s operational plan. ‘Routine inspections can extend the life of the belt and conveyor components by preventing correctable issues from turning into major and costly headaches,’ he explained. ‘These programmes help our customers maximize the throughput and safety of their conveyors, while reducing the chances of catastrophic failure that could interrupt production.’
Conducting conveyor inspections and maintenance can pose significant risks to employees, as these activities bring workers into close proximity with the conveyor system under potentially dangerous conditions. Staff members are exposed to moving belts, rolling components and pinch points, all in an environment that can be dirty, distracting and noisy. Outsourcing these functions to trained professionals will relieve system managers of this burden.
Finding a specialist
As plants across many industries struggle with staff reductions, some facilities now entrust some or all of their conveyor equipment installation and maintenance work to outside contractors. This approach keeps maintenance management in the hands of the plant, while outsourcing the actual labour.
One of the advantages of the Martin Walk the Belt programme is that it allows plant personnel to be relieved of a duty for which they may not be well trained, allowing them to remain focused on core business activities. ‘Our technicians are a specialized group with the expertise necessary to achieve high conveyor efficiency and keep the system running at maximum productivity,’ added value stream manager Mark Strebel. ‘They’re well-versed in current best practices and regulations, and able to advise customers on proven solutions for common industry issues such as safety, dust management and spillage reduction.’
Fugitive material management is a key element of the inspection programme and one of Martin Engineering’s specialties. As problems from the creation, accumulation or escape of dust are multiplied by the increased possibility of regulatory citations, fines and shutdowns, it is imperative that plants prevent the escape of fugitive particles. A key to minimizing the release of dust is the proper maintenance of components such as belt cleaners, transfer point seals, dust curtains, suppression systems and air-cleaning equipment. Proper adjustment and timely service will minimize carryback and dust issues all along the conveyor.
However, Martin Engineering technicians do more than just walk along the length of the belt. Indeed, one of their inspection techniques is to stand stationary at a number of points along each conveyor and watch one or more complete revolutions of the belt, noting its condition, tracking, carryback and other observations. They take detailed notes, identifying trouble spots by component name and location as they are found, often immediately logging data directly into a smart phone or tablet at the site. Digital cameras and other devices allow the technicians to take photographs, record video, make rough measurements and perform other tasks, then share a wealth of information with customer operations personnel for discussion and prioritizing.
Maintenance and repair tasks can be included in the programme and performed routinely, or scheduled upon request. Martin Engineering professionals can also provide a comprehensive survey of the entire plant’s material-handling system, including measured levels of respirable and fugitive dust and spillage. This report delivers grid-based results, giving the client real information that can be used to prioritize needs and avoid misplaced spending.
‘A conveyor is a complex system of interlinked components,’ said Mark Strebel. ‘If even one component or subsystem stops functioning, processes both upstream and downstream will be affected, potentially leading to a shutdown or worse. In a large facility, even a fraction of a percent of system availability could be measured in millions of dollars,’ he added.
‘It’s like buying a car,’ Mark Stern concluded. ‘Effective upkeep will reduce the total cost of ownership. Finding a capable and trustworthy professional mechanic helps avoid unexpected breakdowns, saving time, trouble and money over time.’
Safety first
As well as their Walk the Belt programme, Martin Engineering offer a suite of products and services to protect workers from fast-moving rollers and belts, helping bulk material handlers maintain safer and more productive operations. Various components and training can be used separately or together to help prevent accidents and injuries, reducing risk while benefiting productivity.
Designed to prevent workers from being drawn into a moving return roller, the Martin return-roller guard is an economical way to raise safety awareness and reduce injuries. The solid upper section delivers pinch-point protection and the slotted lower area allows visual inspection while preventing contact with the roller.
Installation is straightforward, with brackets included to mount the guard directly to either the side or bottom of the stringer. Quick-release pins allow easy servicing, with side and bottom panels that swing open for cleaning or maintenance, and removable end plates that provide access to the roller bearings. The guards are designed to fit all major roll manufacturers’ sizes (CEMA C, D & E). Installation is recommended on all return rollers that are less than 2.13m from the ground, or in locations where the roller is otherwise within reach of workers.
The Martin return-roller basket is designed to prevent a return roller from falling in the event of a mechanical failure, and this time is recommended for rollers that are more than 2.13m off the ground and out of reach of workers. The combination of guards and baskets provides a systematic approach to conveyor guarding that is easy to use and safety compliant.
Like the return-roller guard, slotted panels allow easy inspection while keeping workers protected. Brackets designed to fit all major roll manufacturers’ sizes are included to mount the basket directly to either the bottom or side of the stringer. Quick-release pins allow easy access, and side panels swing open from either top or bottom for clean-out or service. Both the roller basket and guard are available in painted steel and two grades of stainless steel.
Likewise, Martin conveyor guards simplify conveyor guarding to improve plant safety and productivity. The heavy mesh guards allow easy inspection, while keeping moving components and pinch points isolated from workers. Their rugged modular design is supported by a supplied angle iron structure and attachment to the conveyor equipment is not necessary. Installation is straightforward, with wedge clamps that allow panels to be removed and reinstalled quickly.
The guards conform to OSHA 29 CFR 1910.217 when installed with a minimum of 140mm between the guard opening and hazard. Available in a range of sizes from 610mm x 610mm to 914mm x 1,270mm, they feature a universal design that can be used in a variety of combinations to fit almost any application. Systems can be easily expanded or relocated as needed.
Safety training
Martin Engineering have also expanded their Foundations training programme on the design and development of more productive belt conveyors to offer three customizable seminars. Training is available to suit individuals with varied levels of experience and responsibility from new hire to senior engineer. Attendees attain a better understanding of conveyor safety and performance, helping to justify upgrade investments and increase profitability.
The Foundations Workshop series has been teaching bulk-materials handling personnel how to operate and maintain clean and safe belt conveyors for nearly 20 years. All programmes offer the opportunity for customization/localization to feature specific images, conditions and problems from the customer’s site, and are flexible in terms of location and length. The presenters, who are highly trained and have many years of hands-on experience around conveyor systems, aim to keep the programmes lively and interesting, while giving attendees a new outlook on conveyor operations.
For further information visit: www.martin-eng.com
- Subscribe to Quarry Management, the monthly journal for the mineral products industry, to read articles before they appear on Agg-Net