Liebherr Introduce new 100-tonne Rigid Dumptruck
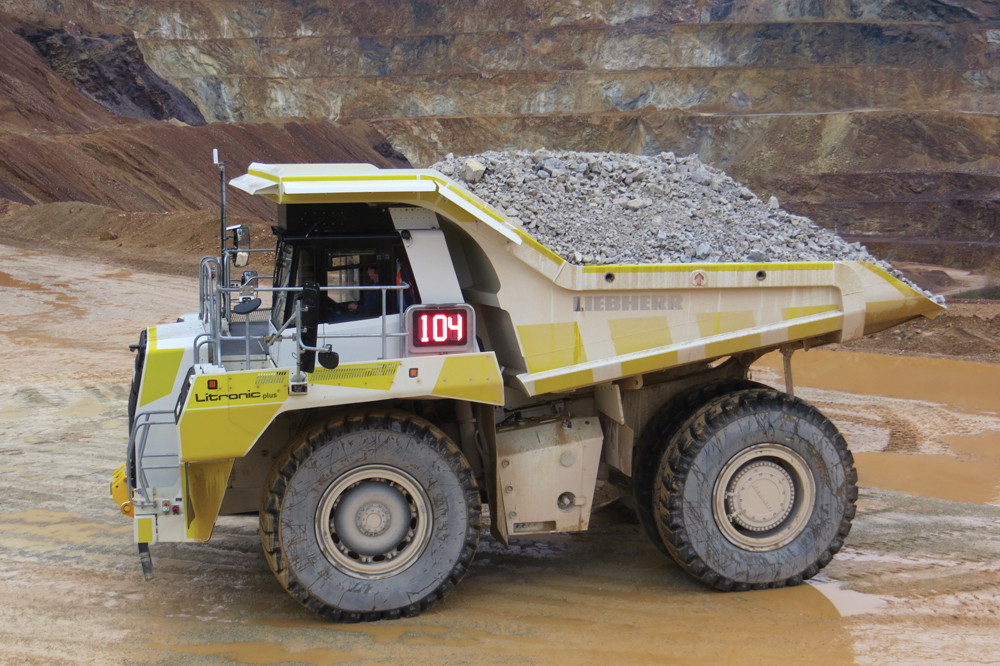
First published in the January 2018 issue of Quarry Management as New Direction
Liebherr enter the 100-tonne class rigid dumptruck market with new hybrid T 236
More than 1,000m above sea level in the Austrian Tyrol a 100-tonne Liebherr T 236 rigid dumptruck is helping the company VA Erzberg to deliver 3–4million tonnes of iron ore a year to fellow Austrians Voestalpine.
Voestalpine make top-quality, lightweight steels for the automotive industry. They are VA Erzberg’s only customers, and VA Erzberg are using the only Liebherr T 236 in the world at their opencast mine.
Erzberg translates as ‘iron mountain’. Ore has been extracted from the mountain for around 800 years. These days, the mine is worked 24h a day, 330 days a year. In the 19th century 300 women from the nearby village sorted the ore by hand. Now a clever system identifies the minerals in the crushed rock and uses air to separate the iron ore from the limestone as it drops from a conveyor, so that Voestalpine receive Fe2CO3 at about 30% iron.
It is a good testing ground for the T 236 because of the conditions it offers. There are some fairly steep slopes to ascend and descend, and temperatures vary from +40°C in the summer to –20°C on snowy winter nights.
The T 236 made its debut at Minexpo 2016 in Las Vegas. The rigid dumptruck marks Liebherr’s entry into the 100-tonne class, with the company estimating potential sales of more than 700 units a year.
Following the successful completion of the T 236 testing phase, it is now on its first field operation trials at the Erzberg mine and, all being well, should be on general release in 2018. One T 236 is already in production to go to South Africa. It is slightly different to the one in Austria as the machines can be tailored to each customer’s specific requirements.
Like its biggest brother, the 400-tonne Liebherr T 282, the 236 is actually a hybrid, with a diesel-electric drive system.
The T 236 capitalizes on decades of Liebherr experience of off-highway truck technologies to introduce a vertically integrated Litronic Plus Generation 2 AC drive system to the 100-tonne dumptruck class.
This advanced active front-end technology makes use of electrical energy during retarding, so the alternator is used as a motor to propel the vehicle. Engine friction is used for retarding and provides power to the auxiliary drives on the back axle, delivering controlled engine speed with hardly any fuel consumption.
Liebherr are also particularly proud of this being the first diesel-electric in its class with a four-corner, oil-immersed braking system.
The 100-tonne class machines that VA Erzberg are currently using dig out a bit of the haul road with every gear change. And as all the drivers are trying to get the best out of their trucks all the time, the gear changes tend to be at the same spot on the road all the time. That creates troughs and ridges that make an already jerky ride even more uncomfortable.
Not with the T 236. It responds smoothly to the pressure on the accelerator and drivers even find they do not need to rely on that four-corner braking in many of the spots where they would have been on the brakes with the existing machines.
Naturally, that takes a little getting used to, but when the drivers are used to it the result is exceptional fuel efficiency from the 900kW (1,200hp) engine. The drivers also praise the manoeuvrability of the truck, helped by the fact that the left and right wheel speeds change automatically when the steering wheel is turned, and they like the ergonomic cab and comfortable front-wheel suspension.
As Dr Burkhard Richthammer, managing director of Liebherr Mining Equipment Colmar SAS, explained: ‘Liebherr are committed to designing mining trucks that operators want to drive. The result: comfort, safety and improved productivity with lower fuel consumption.’
Liebherr pride themselves on the quality of the components in all their machines, saying they are designed and built for high performance and longevity in the most extreme mining conditions. But smoothing the running of the machine so the engine stays at the most fuel-efficient 1,800 rev/min also gives the components longer life, allowing longer intervals between services. All of which saves time and provides a cost-per-tonne advantage.
The variable hydraulic system reduces machine parasitics to provide maximum power, whilst decreasing fuel consumption when power is not required.
Designed to carry a 100-tonne payload (but with up to 10% overload expected and catered for), when paired with Liebherr’s R 9100, R 9150, R 9200 or R 9250 mining excavators, the T 236 is said to provide the most complete high-performance and scalable truck–shovel match, delivering a good combination for production requirements.
When it is time for maintenance or a service, an industry first is Liebherr’s Litronic Plus Isolation system, designed to keep maintenance personnel safe by eliminating hazards. The T 236 is equipped with double-pole battery, starter motor and hoist system isolators as standard. In addition, there is a drive system inhibitor, electrically interlocked to grounding devices for each plug and drive power module. And operating on a voltage level of 690V AC and 900V DC means site technicians can carry out system maintenance.
The in-line electrical power train layout minimizes cable length, while the maintenance free IP 68-rated plug and-drive power modules ensure reliable operation in all weather conditions. Ground-level service points also contribute to maximum uptime.
The new 100-tonne dumptruck was put through its paces at the VA Erzberg mine during this year’s Liebherr Information Tour for the international trade press in October, when the company also introduced new telehandlers and showed off a new dozer.
This year, Liebherr plan to launch eight new telescopic handlers in 26 different versions. There will be top-of-the-range models for materials handling and production work, and simple, cost-optimized models for stacking and lifting.
This month will see the launch of three, 7m models with load-bearing capacities of 3.2 tonnes, 3.6 tonnes and 4.1 tonnes; a 6m model with a load-bearing capacity of 3.5 tonnes; and a 10m model with a load-bearing capacity of 3.3 tonnes.
During the year these will be joined by: 7m models with load-bearing capacities of 4.6 tonnes and 5.5 tonnes; and a 9m model with a load-bearing capacity of 6 tonnes.
All will have established Deutz diesel engines complying with Stage IV/Tier 4 final emission standards thanks to the diesel oxidation catalyst (DOC) and selective catalytic reduction (SCR). The bigger machines will have diesel particulate filters as standard and these will also be available as options on the smaller machines.
The new PR 766 dozer is an update of the PR 764, which it replaces in the 50-tonne class. It is driven by the latest-generation Liebherr 310kW (422hp) V8 engine that not only complies with Stage IV/Tier 4 emission standards, but exceeds them by some margin.
It achieves that with an optimized combustion process that minimizes the particles inside the engine followed by exhaust gas treatment using selective catalytic reduction.
The innovative engine management also includes proactive power adjustment and Eco mode to optimize machine performance and fuel consumption, whilst the ergonomically designed cab maximizes safety and comfort, and the Liebherr drive technology ensures reliability.
For more information visit: www.liebherr.com
- Subscribe to Quarry Management, the monthly journal for the mineral products industry, to read articles before they appear on Agg-Net.com