The Implications of Stage V Diesel Engine Emissions Legislation for Quarry Equipment
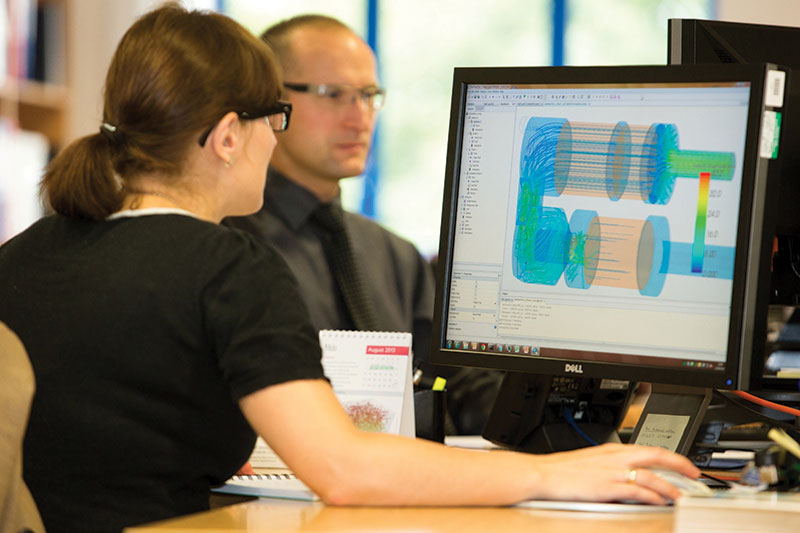
First published in the June 2015 issue of Quarry Management as Evolution of Pollution
Emission standards for diesel engines used for non-road vehicles and equipment have become ever more stringent with each successive update. Jog Lall, sales & marketing director at Eminox, looks at the implications of Stage V on quarry plant and equipment, with the legislation due to be implemented in 2019-20.
The main focus of exhaust emissions standards in recent years, and which will be reflected in the soon to be implemented Stage V requirements, is particulate matter (PM) and nitrogen oxides (NOx). This has happened against a background of evidence on the damaging effects of these components in diesel exhaust. As a result, Stage V will affect a wider range of engines, both larger and smaller, and this will encompass a widened scope of plant and equipment supplied into the quarrying sector.
Of pressing concern are the ultra-fine particles within PM that have been shown to cause damage to the heart and lungs when inhaled. Stage V, therefore, introduces a new particulate number requirement, as well as further reductions in PM mass for many engine categories. For the first time, this effectively mandates the use of diesel particulate filters (DPF) or a selective catalytic reduction (SCR)-coated DPF. Stage V will also focus on further NOx reductions.
Eminox, one of the leading European designers and manufacturers of purpose-designed exhaust and emission-control systems for heavy-duty diesel vehicles and equipment, have been working on technology that tackles both of these issues since the 1990s and, as a result, are in a position to help original equipment manufacturers (OEMs) of quarry plant and equipment to satisfy Stage V requirements.
Stage V proposed emission limits
As can be seen from the table on page 36, Stage V will introduce stringent emissions standards for a widened scope of engines. These include compression ignition (CI) engines below 19kW and engines above 560kW, all of which were previously outside the legislative requirements. The latter will cover new quarry plant and equipment previously excluded, which creates a challenge as it may involve engines that until now have not been fitted with an exhaust gas after-treatment system (EATS). Having previously been regulated to Stage III at best, cost, packaging and development time are, therefore, all essential considerations for OEMs in this scenario.
There are a number of other factors to take into account when developing an EATS. For example, to make things more interesting, OEMs and the customers that supply plant and equipment to the quarrying sector do not want a huge fuel penalty as a result of a drastic increase in back pressure – just one of the many factors that need to be taken into account when developing a Stage V solution.
For those facing such challenges, there are definite synergies from partnering with a company that has a track record of meeting previous legislation. Eminox’s EATS technical team can explore different options to solve these specific issues on a variety of different engines and equipment.
Despite the challenges presented by the addition of larger and smaller engine sizes, and new emission targets, compliance with Stage V does not require a revolution in terms of exhaust after-treatment. Indeed, much of the technology already exists – as in the case of DPF described above – which is widely used to meet current Euro VI legislation for heavy-duty vehicles.
In that sense, it is best to view Stage V as an evolution of existing exhaust gas after-treatment technology. The real challenge will be to optimize the after-treatment architecture for the different applications, whilst keeping one eye on the subsystem cost and packaging limitations.
Stage V challenges
It helps that Euro VI (on highway) and proposed Stage V (non-road) standards are very similar in terms of emissions limits, including the particulate number requirement. That is worth bearing in mind, as an EATS partner that has developed solutions for Euro VI will draw upon that experience when looking for the optimum solution for each application. For instance, Eminox are able to scale up and scale down their Euro VI system approach, making it suitable for smaller and larger diesel engines covered by the new legislation.
Moreover, these insights allow the company to foresee problem areas, such as the fact that larger engines used in the quarrying industry will need to use high-flow injectors to deliver large volumes of AdBlue into the SCR system to trim NOx. Thus, specific attention needs to be given to tuning the spray pattern, ensuring fine atomization for better mixing, minimizing wall wetting and eliminating crystallization of urea on the injector nozzle. All this is important as quarry equipment operators do not want high running costs to be the trade-off for Stage V compliance.
Typically, larger engines used in the quarrying industry are either medium speed (300–1,000 rev/min) or slow speed (less than 300 rev/min); slow speed engines are typically two-stroke units. Drive cycles for these engines are very different to those observed on on-road vehicles. However, a key requirement on all engine sizes is centred on a need for a compact, lightweight EATS that can work within the available space envelope. Past experience in this area has driven Eminox to develop novel approaches such as close-proximity mixing.
In addition, SCR and DPF technology can be combined into a single SCR on filter substrate to optimize space utilization. Again, Eminox can draw upon their experience from Euro VI in terms of close-coupled catalyst systems, while their ongoing investment in 3D scanning and 3D-CAE modelling tools to design compact EATS systems that utilize high-performance catalysts on small-volume substrates helps in this area too. Furthermore, the firm’s computational fluid dynamics (CFD) allows fine-tuning of close-proximity mixing solutions, and represents an in-house capability that is a valuable asset.
Conclusion
It can be seen that, despite a number of challenges, compliance with Stage V does not have to be a revolution in exhaust after-treatment design, but rather an evolution of existing expertise. That is good news for all those involved in the quarrying industry where value for money and access to an effective, workable solution is essential.
The technologies and system architecture to meet the new targets for PM and NOx have already been explored, evaluated and are available for Euro VI today, allowing development times and costs for Stage V to be significantly reduced. Eminox are not only utilizing this existing know-how, but also using direct experience from Stage IV and factoring in the tough working conditions and duty-cycle considerations that off-road quarry equipment has to endure. As a consequence, the company is already working with engine manufacturers to develop a Stage V exhaust after-treatment solution.
Obviously, throughout all this, OEMs need to ensure the EATS maintain their overall value proposition, and the best way to achieve this is to work with a partner that is able to adapt existing solutions and knowledge to provide the most effective approach. Evolution rather than revolution offers the best way forward.
-
Subscribe to Quarry Management, the monthly journal for the mineral products industry, to read articles before they appear on Agg-Net.com