Calcium Carbonates Without the Carbon - Longcliffe Quarries committed to net-zero carbon challenge
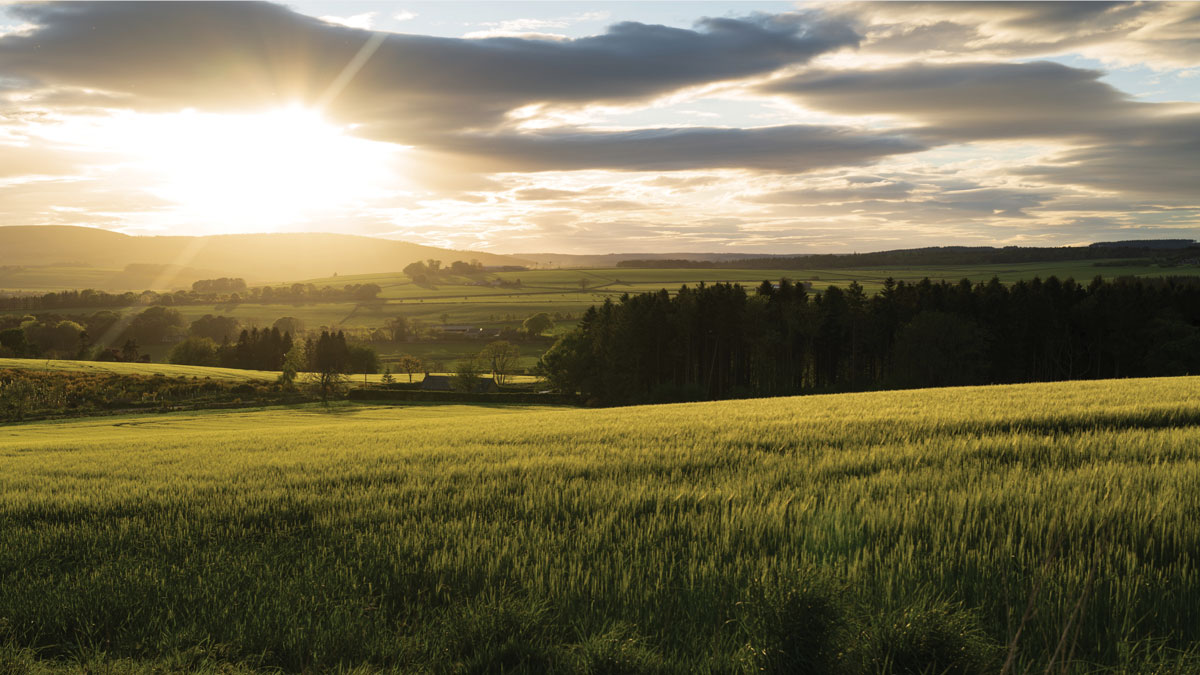
First published in the June 2021 issue of Quarry Management
Already recognized for their forward-thinking approach to fleet and energy management, Derbyshire-based Longcliffe Group have set themselves the ambitious target of being carbon neutral by their 100th anniversary in 2027. Group energy director John Shields explains how the company’s complex jigsaw of efficiency savings, wind/hydro/solar generation, investment in new transport solutions, and farm and forestry offsets make for a heady mix
Longcliffe, the UK’s leading independent suppliers of pure limestone powders, granules and aggregates, have been quarrying at Brassington Moor Quarry in Derbyshire since 1927 and to this day remain a family business. Like any quarrying business, we are intimately tied to the local landscape, and our core purpose as a company is to provide sympathetic and sustainable stewardship of that landscape over time, guided by a strong loyalty to our customers and to local residents and businesses. We are determined that quarrying not only continues to be, but is also seen to be, a positive force in that landscape.
It should be no different for carbon, and we have set ourselves the ambitious target of reaching Net Zero by our hundredth anniversary in 2027. The journey from hard rock to the huge range of limestone products we all use every day is intrinsically ‘high energy’. With carbon taxation and its proxies hugging our industry at every turn, it is easy to veer between extremes of lofty ambition on the one hand, and despondency on the other. However, by outlining our own journey, I hope to provide an encouraging demonstration as to what I think is achievable.
Since 2010, we have done a number of things to reduce our carbon footprint, much of which will be familiar ground. We have been accredited to ISO 50001; we are reducing process waste through the installation of a new wash plant; we have installed new inverters and variable-speed drives; we are updating compressors, gearboxes and motors to the latest standard; and we are introducing low-loss transformers and better power factor correction.
In addition, we are bolstering operator training and setting new procurement standards. Managers and operators are fully conscious of the need to reduce energy consumption, but the more critical question is whether energy management can be incorporated successfully into everyone’s day job. Automated metering, recording etc all help, but ultimately – like so many other things – it comes down to culture: are people sufficiently eager to make the necessary changes and sufficiently empowered to take ownership of them?
All this has come with results: we have cut electricity and gas usage per tonne by some 25%, and load and haul fuel usage by 12%; our tankers have improved their miles/gal by some 25% in the last five years; and we have received an FTA award for fleet management. We have also, it is fair to say, benefitted from decarbonization of the grid – emissions factors for grid-imported electricity have halved.
Perhaps most notably, in 2015 we installed two 2.3MW wind turbines at Ryder Point Quarry. We installed these after five years of public consultation, planning and site preparation, and we did this without a single formal objection from any member of the public or statutory consultee, which I think is testament to what can be achieved through honesty and open dialogue with local residents and stakeholders.
Inevitably, however, there is still a way to go to get to Net Zero. Figure 1 shows a simple breakdown of our 15,000 tonnes/annum-CO2e. We are after an ‘honest’ Net Zero, scoping only those things within our control, but including all proper carbon protocol ‘Scope 3’ emissions that are associated with upstream production and distribution of energy sources. So, how are we going to go about it?
Plant efficiency savings
The first step is plant efficiency savings. This is clearly a critical component and vital in order to avoid building redundancy into processes: you start with usage efficiencies; then try to flatten load; and only then look to generation and other big-project solutions. If you do not bring your existing assets to heel in this manner, you simply build redundancy into any subsequent capex.
Efficiency savings broadly fit into three categories. The first is process savings through better use of variable-speed controls; redesign of older screens, mills and filters; elimination of bottlenecks, wastage and unnecessary internal movement etc. The second category is electrical and thermodynamic efficiencies, ie more efficient motors and heat recovery from fluid-bed driers etc. The third category is the human element: the benefit of motor and drives training, for example, and better monitoring. There are standard protocols for estimating the potential of this area.
Taken together, these savings on gas and electricity consumption get us over 10% of the way there (see fig. 2).
Fuel savings
Fuel is the big one. But, whilst we may be the first generation to have to address climate change in this manner, we are not the first generation to have to seek alternatives to diesel vehicles. The change to red diesel taxation is going to further press this matter, but we can expect changes in mobile crushing, conveyor use and electric pumps; we can also expect greater use of rail and shifts in where value-added processes take place.
For our purposes, I have presumed the 30% improvement in diesel usage expected by Volvo and other manufacturers for road haulage over the time period we are looking at – which would be largely in line with the improvements we have seen over the last six or seven years. I have set a more modest target for quarry vehicles, and this may even be an underestimate as to what is achieved given the pressure from changes to red diesel taxation.
We estimate a further 2,000 tonnes/annum saving here (see fig. 2).
Generation source
Next come generation. Subsidies may no longer be available, but embedded generation with on-site users is getting more and more attractive, particularly as technology costs fall. It is now possible to buy the same wind turbines as six years ago some 15% cheaper in Sterling terms – despite the latter’s fall in value.
Solar also continues its inexorable decline, with the levelized cost of generation expected to be below £40/MWh by the end of the decade.
Longcliffe generate more than 11,000MWh in any given year from solar, hydro and wind. We think we can push this further still, and we remain in close dialogue with the embedded generation team at Western Power Distribution over how best to achieve this.
This brings us to about 7,000 tonnes-CO2e.
Whether or not you have renewable generation assets on site, you will likely be reliant on some degree of grid import. Naturally, anyone aspiring to Net Zero should be looking now at options for the purchase of certified renewable electricity.
Modelling our on-site generation and plant usage, we will still be importing from the grid. Ensuring this import is green takes us to 9,000 tonnes (see fig. 2).
Offsetting
Trees
It is said that the best time to plant a tree is 20 years ago. Carbon credits are only available for planting from 2015, but we have been planting new woodland at quite a pace since 2010, currently 117ha and counting. We are calculating annual sequestration according to Woodland Carbon Code models regarding age, species, class, density and cropping rates.
With sympathetic planting this can also be combined with biodiversity targets. Nearly all of our woods are planted at low density and with an appropriate species mix. And even accounting for these, the unsubsidised cost of woodland creation remains well below most projections for the long-term cost of carbon.
Whilst annual gains in 2027 will still be modest, we expect this additional planting to have sequestered some 35,000 tonnes-CO2e by 2060.
The Game & Wildlife Conservation Trust is also looking at certification of hedgerows, which may be an option in more open landscapes. Although Longcliffe are currently planting hedgerows at a rate of approximately 2.5km per year, they are not included in our calculations, which, nonetheless, still take us to 9,500 tonnes (see fig. 2).
Farmland
Changes in arable practice, in particular, offer another UK-based opportunity for offsetting at scale. Whilst we have long been involved with agri-environment schemes aimed at bolstering biodiversity, we are currently at a very early stage with regards to soil and regenerative farming.
Alterations to farm practice do require upfront support to cover yield loss in the first three years, but improvements to soil and lower operating costs would normally be expected to outweigh these from year five at the latest. With changes to farming and agri-environment payments already under way, by mid-decade this gap may be all but closed.
I have ignored for the time being the potential of fully organic mixed farming rotations, and of microbial or basic rock silicate quarry waste applications. We are trialling these – and the latter will be of interest to granite operations – but have instead simply assumed a relatively modest 5% annual increase in soil organic carbon through transition to zero till, companion cropping and more judicious use of agrochemicals across only 250 acres.
This takes us to 12,205 tonnes – a shade shy of 82.5% of total emissions and well in excess of our footprint excluding road transport (see fig. 2). As mentioned earlier, we are after honest figures, and this is where our plans have got us to date – some 11% from plant efficiencies, 14% from fuel savings, 37% from changes to generation source, and 21% from offsetting.
Importantly, I have not included any magic bullets. These are the savings that we have modelled to date based on known plant loads and costed measures over the coming six years. I have left out any potential savings from green fuels, such as HVO or ‘green gas’; incorporating electric vehicles along the lines of the Volvo-Skanska collaboration at Vikan Kross; the use of alternative drying technologies such as infrared and microwaves; and hydrogen. Any and all of these may well come into play, and allow us to close – and surpass – that final 17.5%.
I genuinely think we are within touching distance of the prize, but I will end with a ‘positive word of caution’, as we have been here before. In the late 1760s, Arkwright’s mills, just down the road from Longcliffe in Cromford, started using the reliable river levels that local limestone geology affords to lead the way with water-powered spinning frames. But, by the 1790s, the shift was starting towards coal power, a transition that was almost entirely complete by 1830. Within 60 years, that shift in energy source saw all the growth move to Lancashire, and places like Preston, ironically Arkwright’s home town.
It is now almost 30 years since the Rio Summit and we are living through an even more dramatic energy shift. Uncomfortably, we are a target industry for regulators: concrete and cement have been in the spotlight for a while now, and the changes to red diesel taxation demonstrate quite how vulnerable the wider quarrying industry is to regulatory change. Bluntly, as technologies mature, it becomes easier – and indeed more efficient – for a simple producer responsibility obligation to force businesses to internalize carbon costs.
But, as the cement industry is showing by spearheading CCS, having big mountains to climb makes you a good mountaineer. Our sector has the expertise and the opportunity to make a huge contribution to Net Zero at genuinely meaningful scale. Let us embrace this challenge, and get to it.
- Subscribe to Quarry Management, the monthly journal for the mineral products industry, to read articles before they appear on Agg-Net.com