Progressing Digitalized Capabilities, Sharing Expertise
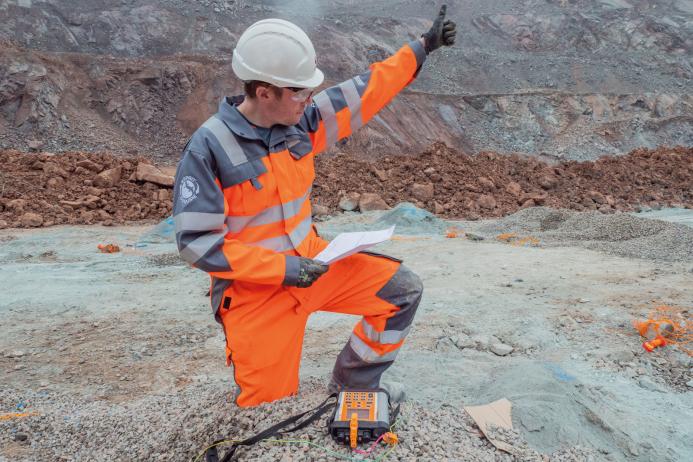
First published in the April 2023 issue of Quarry Management
An expert part of EPC-UK’s expanding team of specialist ‘Blast Doctors’, QM shines the spotlight on renowned industry authority Dr Liam Bermingham and discovers more about his achievements and capabilities as well as the sector-related ventures he is involved in at present, before hearing how Anthony Evans’ digitalized role with EPC-UK has taken flight with his progression from driller to drone pilot
With the digitalized quarry fast evolving and technologies advancing at pace, Dr Liam Bermingham’s role at EPC-UK is more multifaceted than ever. Believing that effective research and development is key to sector progression, he is currently furthering his studies into understanding the effects of transient pressures through the measurement of in-hole acceleration generated during a blast. He is also looking at the effects of in-hole static pressure on explosive performance and working on the development of a dumptruck GPS tracking device for integration into the fragmentation monitoring system, in a move to help quantify blast performance.
Dr Bermingham’s schedule concentrates on work to improve optimization at
EPC-UK’s customers’ sites, where he combines professional expertise with academic understanding to successfully deliver cost benefits through collaborative projects. The achievements that contribute to his knowledge and expertise include: first-class degrees in Mechanical Engineering (Hons) and Mining Engineering; his PhD thesis, ‘The Prediction and control of air overpressure that arises as a result of quarry blasting’; and his membership of the Federation of European Explosives Manufacturers (FEEM) blasting working group.
Presenting at Fulmination
Dr Bermingham’s passion for industry progression through knowledge sharing is another key area of his work, and in April he will once again be taking to the conference stage at Fulmination 2023 (Ordnance Munitions & Explosives Conference) to deliver his latest ground-breaking presentation, ‘Digital Blasting – Creating the Platform to Achieve Net Zero’.
The event, hosted by the Institute of Explosives Engineers (IExpE) and held from 18–20 April at East Midlands Conference Centre, will see Dr Bermingham present findings on how EPC-UK’s digital technologies, including drone photogrammetry surveys, cloud-based storage of digital blast specifications, and applications to record infield drilling and explosives measurements, are being used to accurately record key data within the drill and blast process.
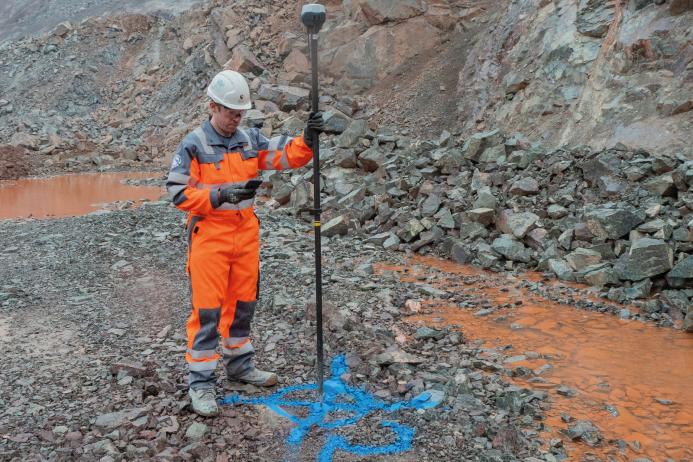
Advanced possibilities
The data he will reference is enabling the EPC-UK and EPC Metrics teams to review blast performance and drive continuous improvement in the field, fully digitalizing the blasting process whilst improving site sustainability and reducing operations’ carbon footprints.
Detailing aspects of the presentation, Dr Bermingham said: ‘The possibilities now available for us to digitally measure, store and analyse data throughout the entire drill and blast process – from surveying and designing the blast to measuring the resulting blast performance – are impressive and advanced, enabling those working in the field to design and implement a fully digitalized blasting process.
‘My presentation at Fulmination will explain how, by storing digital information on a cloud-based platform, we can perform in-depth analysis of key blasting data in conjunction with KPIs measured downstream of the drill and blast process. The development is allowing us to accurately review and quantify the impact the blasting process has on a quarrying operation’s overall efficiencies. It’s also creating a platform from where we can drive continuous improvement to reduce the quantity of waste that the blasting process creates, the energy demands of an operation and primary crusher, and consequently, the overall carbon footprint.’
Chairing the QNJAC Working Group
EPC-UK have been successfully strengthening their team of specialist Blast Doctors in recent years, bringing more industry expertise to the company with the passion and innovation to develop digitalized blasting processes, fit for the future. Sharing his knowledge with the wider industry, Dr Bermingham has recently been appointed as the new chair of the QNJAC drilling and blasting working group, succeeding EPC-UK’s Dr Rob Farnfield. As chair, Dr Bermingham will continue to demonstrate his own and EPC-UK’s commitment to industry progression. His first meeting within the new role saw recent incidents involving fires on vehicles transporting explosives discussed and the current guidelines for emergency preparations reviewed.
Dr Bermingham explained that during the meeting National Occupational Standards, a drill and blast self-auditing tool, and blasting training and competency schemes were further critiqued. The event also presented an opportune platform for two new sub working groups to be created, one for black powder usage, and one to focus on training and competency assessment.
Published papers
More about Dr Bermingham’s research and findings can be found through his series of published papers, including:
Effects of topography on air overpressure from quarry blasting – a case study – ISEE
A preliminary study into the relationship between air overpressure and face velocity in quarry blasting – ISEE
Investigation to determine the origin of air overpressure from quarry blasting – ISEE
Low-cost method for monitoring shock-tube detonator and explosive product performance in blastholes – ISEE
Control of air overpressure from quarry blasting? It’s about time – ISEE
Potential impact of blast layout, sequence and detonator timings on air overpressure from blasting – ISEE
Implementation of technology to fully digitalize the drill and blast process in a remote setting – EFEE
Phase – the forgotten problem of blast vibration prediction – Fragblast.
Supported by the expertise of specialists such as Dr Bermingham, EPC-UK’s work and research to fully digitalize the blasting process, reduce emissions and accelerate sustainable processes will only advance, improving safety, value added results, and the operating environment, industry wide.
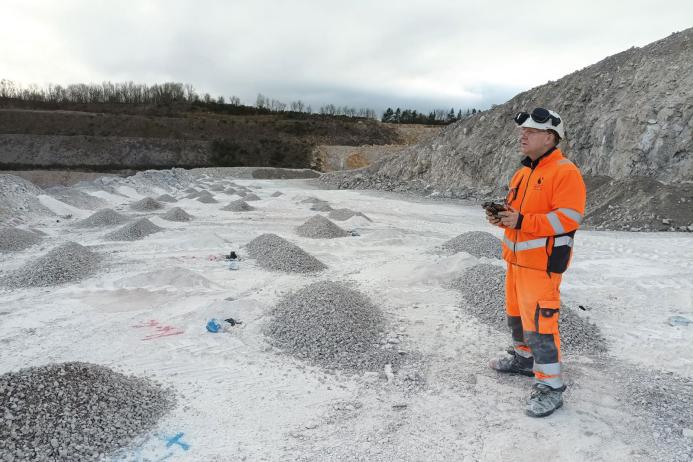
From Driller to Drone Pilot
Unquestionably, digitalization is reshaping quarrying operations at a progressive pace. The equipment and technologies used by drillers and shotfirers within the drilling and blasting industry have advanced significantly over the past three decades, leading processes to become safer, leaner, less environmentally impactful and increasingly efficient.
EPC-UK’s own digitalized innovations are enabling them to develop blast design management and optimization software, progress full rock-on-ground services for customers, and, critically, work more sustainably and safely year on year.
Seeing the progress being made first-hand is Anthony Evans, an EPC-UK explosive supervisor based in North Wales. Mr Evans has been with the company for 35 years, and during that time has seen a series of remarkable transitions and improvements take place within the sector.
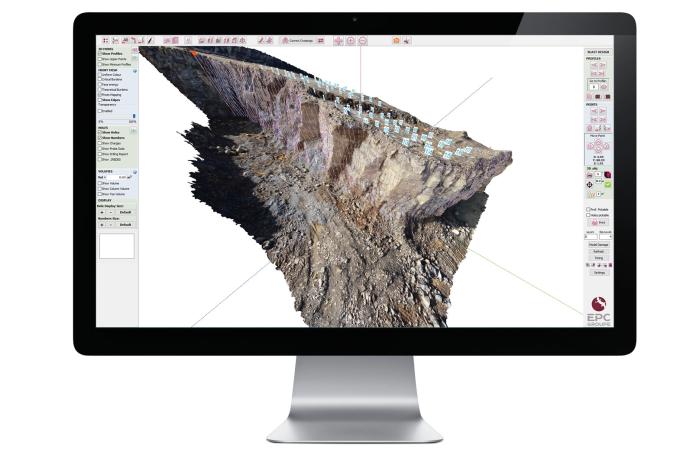
Safety first
Mr Evans started his career in the 1990s as a driller, before soon adding to his skill set by training as a shotfirer. His overall position currently is explosive supervisor; however, he also performs the role of profiler, and has recently qualified as a drone pilot.
Back in the 90s, Mr Evans worked on motorway civils projects as well as in the quarrying environment. He saw how developments in drilling technology and machine design quickly enabled improvements in working conditions, allowing operators to control equipment from within air-conditioned cabs.
‘EPC-UK have been at the forefront in terms of using technology to prioritize health and safety within their operations, spearheaded by our managing director, Ben Williams,’ said Mr Evans. ‘Under his leadership and uncompromising approach to ensuring teams have state-of-the-art safety equipment, it’s not just operations that have become safer, but operators’ mindsets too. We’ve become a team that instinctively notices unsafe conditions in and out of our working roles, understanding that better, technically advanced equipment – whether that’s a machine, PPE or a digitally supported tool – can make operations safer. Customers see the difference when a supplier makes health and safety matter, with our higher standards serving to set the benchmark and improve industry safety standards for all.’
Plant machinery progress
‘As with the automotive industry, the vehicles we rely on in the quarry or on civils site have advanced significantly in recent years. More fuel efficient and with tech on board that’s supported by Wi-Fi connectivity, the drill rigs EPC-UK operate now are more economical to run and are increasingly instinctive. Earlier in my career, drillers would need to rely on their ability to listen to different sounds within the rock to identify issues. Advancing technology has led to considerable safety improvements in this area. The developments made in our own Expertir software – impressively and passionately progressed by EPC-UK’s Dr Geoff Adderley – have been marked, allowing drone-gathered data to be captured and applied to more parameters, then measured more easily – leading to increasingly desirable blasting outcomes.’
Expertir’s capabilities for advancing blast designs using drone imagery and models have recently been incorporated into EPC-UK’s Vertex system, which comprises two other digital elements: Expertab – a tablet-based software used with drills and MEMUs to capture blast data in the field; and ExplOre – a web-based platform for users to store blast information digitally and log and track KPI data.
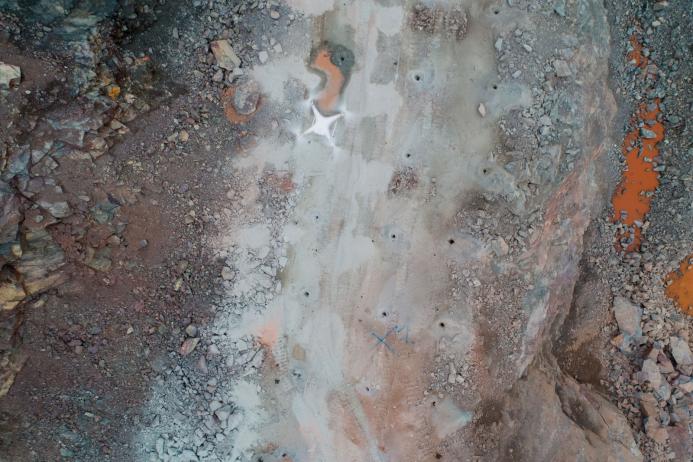
The sky’s the limit
The introduction of EPC-UK’s drone technology has seen Mr Evans’ role evolve yet further over the past three years. ‘You never stop learning when you work for EPC-UK,’ he said. ‘The company’s commitment to training is taken very seriously, as it’s the lifeblood that keeps us safe and enables us to grow. Our team progresses its qualifications and knowledge base all the time, primarily through a dedicated learning and development centre with its team of industry experts who deliver specialist training programmes and qualifications. This ‘in-house’ expertise has recently enabled me to train and qualify as a drone pilot, adding another string to my professional bow.
‘Flying the drone is as enjoyable as it sounds, and we have more EPC-UK pilots qualifying to fly in quarries across the country all the time. I’ve been trained to Civil Aviation Authority (CAA) standards and can use the drone and its photogrammetric capabilities to map a face profile and full quarry site in incredible detail. We can even use the drones to film a detonated shot, which keeps helping us to learn and develop.
‘The technology that’s coming to the fore is truly enabling, however the human minds we have within the team are equally impressive. The young, qualified talent that are applying their expertise at EPC-UK are the force that’s enabling our technological progress to materialize. These are the people who are realizing the incremental improvements and software advancements that continuously take place, making operations safer, smoother, leaner and greener.’
John Morgan, EPC-UK area operations manager West, knows Mr Evans well, describing him as ‘a valued member of the EPC-UK team in North Wales who harnesses a vast amount of experience and, most importantly, respect from his peers and quarry managers’. ‘I have known Anthony for more years than either of us can remember,’ he said. ‘His passion and drive for the job have not diminished, and I continue to be impressed by his ability to embrace change, never shying away from the challenge of new technology.’
In a career that is still advancing, just like the industry he works within, Mr Evans is continuing to learn and develop: ‘From performing my duties using a worksheet and intuition in the 1990s, to drawing on all the advanced capabilities technology has to offer today, I’ve chosen to remain working in a profession that’s dynamic and rewarding, and for a company that prioritizes its employees’ safety, well-being and personal development,’ he said. ‘I value and feel supported by the people that I work with and consider that, as a team, we are the best in our industry at what we do.’
Looking to the future
‘There is much to anticipate on the horizon, as the technology we’re implementing now paves the way towards a more environmentally sustainable future. The building blocks for essential change are already being put in place and I’m glad to be where I am, seeing the technology for tomorrow’s quarry performing in the field today. Of course, these capabilities will only develop further in a short amount of time, and with the people and passion of EPC-UK at the helm, the results will be, quite literally, ground-breaking.’
Subscribe to Quarry Management, the monthly journal for the mineral products industry, to read articles before they appear on Agg-Net.com