Orica’s Digital Drilling and Blasting Solution
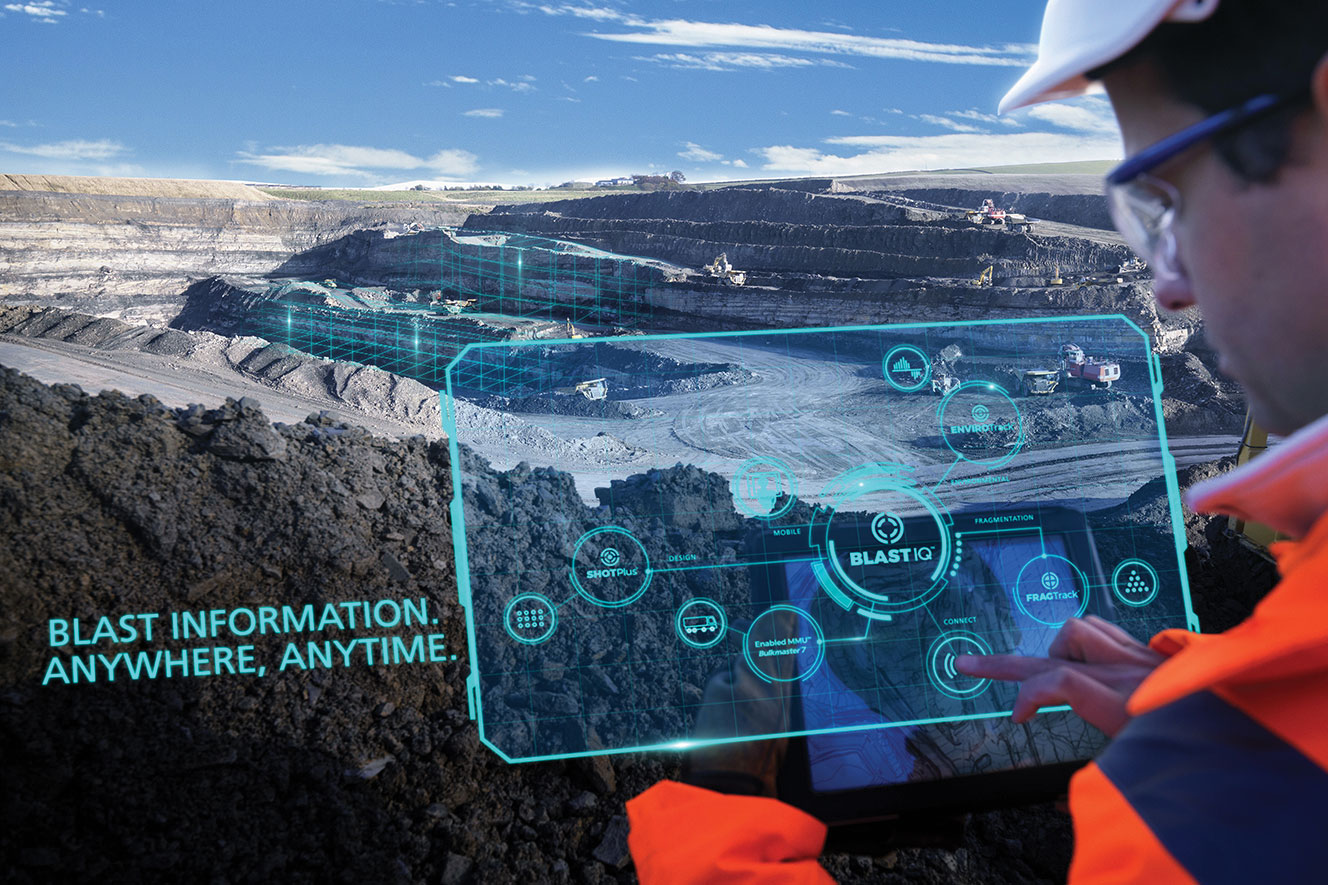
First published in the March 2021 issue of Quarry Management as Orica’s Digital Solution
The digital future of drilling and blasting with Orica’s BlastIQ control solution
The extractives industry is getting smarter. More instruments are recording more complex data than ever before, providing managers with an almost overwhelming amount of information. The challenge quarries face now is how to effectively manage and use the data, thereby creating better decisions for better outcomes. The answer lies in digitalization; integrating data from digitally connected technologies across the quarrying process can deliver sustainable improvements and efficiency gains that reduce the overall cost of operations.
The industry has traditionally been slow to adopt new technologies due to the scale and complexity of operations as well as the heavy costs that can come with change. However, for those companies wishing to strengthen their competitive advantage, the transformation towards digitalization has already begun. Whether it is the magnitude of smart sensors on equipment managing the preventative maintenance schedule or fully autonomous haul trucks, almost every stage of the mining cycle has embraced digitalization to one degree or another.
Perhaps the one exception to this trend is in drilling and blasting, where the transition towards digitalization moves at a slightly slower pace. In fact, it is not uncommon to see some quarries using blasting practices that have remained unchanged for decades. The downstream impact of variable and poorly controlled blast outcomes today can impact as much as 80% of the total processing costs of an operation. This presents an enormous opportunity to deliver value with intelligent data-driven blasting optimization technology.
Digital vision
Orica have a clear vision for the future of drilling and blasting. At the core of this vision is the digital transformation of the blasting process, where rock recognition informs intelligent and dynamic blasting to deliver predictable and consistent outcomes. By effectively capturing and recording data at every stage of the drill and blast process, machine learning principles coupled with regression analysis and automation can be used to generate design inputs targeted at achieving precise blast outputs.
What does this mean in practice? It means that engineers designing blasts in SHOTPlus can use advanced loading rules to generate explosive loading designs based on measure-while-drilling data imported from connected drill rigs. In-built fragmentation prediction tools can then be used to model the expected blast outcomes which have been calibrated based on actual fragmentation data captured using FRAGTrack cameras. Blast designs are communicated directly to the blast crews on the bench using BlastIQ Mobile and, similarly, real-time updates on the blast progress are fed into BlastIQ Insights to allow supervisors to track the blast progress. Moreover, all this information is securely stored on the cloud and accessible at any time, ensuring that the data can be effectively used to drive productivity improvements and efficiency gains.
Today, this is no longer just a vision for Orica, but a reality. Of all the key component technologies to achieve the end goal of a fully integrated system, fundamental amongst these is BlastIQ control. From pre-blast modelling through to post-blast measurement and analysis, the BlastIQ platform delivers the data, benchmarks and insights needed to ensure sustainable, cost-effective improvements in blast performance.
BlastIQ control
Building on more than 140 years of experience and innovation in blasting, Orica are leading the way in the transition to digital with their blast-optimization platform, BlastIQ. Introduced in 2018 and now used extensively in mining and quarrying operations worldwide, BlastIQ is a cloud-based digital platform designed specifically to allow continuous improvement of blasting outcomes by integrating data and insights from digitally connected technologies across the drill and blast process. Consisting of three core software components, SHOTPlus, BlastIQ Mobile and BlastIQ Insights, figure 2 demonstrates how each of these are interconnected.
SHOTPlus blast design
Since its introduction more than 20 years ago, SHOTPlus has garnered a reputation as the premier blast-design package. Ensuring it remains at the forefront of blast-design technology is a team of dedicated developers that continually updates and improve the software. Today, in addition to the features expected from a standard blast-design software, there are a raft of other tools and features designed to add value to any operation, including:
Environmental Prediction: vibration and air-overpressure prediction tools based on regression analysis and arrival times allow users to assess the impact of their blast designs before firing.
Advanced Modelling: utilizing the online Advanced Vibration Modelling service, which provides a full blast waveform based on the charging and timing information supplied from SHOTPlus for blasting in highly sensitive areas.
Fragmentation Modelling: particle size distribution predictions based upon blast designs and geology that can be calibrated from in-field measurements for increased accuracy. Users can compare different blast designs for the optimum fragmentation.
Blast Design Templates: allow blasting parameters to be set to individual quarries or sections of quarries. This ensures that every blast is designed to the same specification no matter who happens to be designing the blast on the day. No more questioning the correct burden or spacing, floor heights or subdrill, just consistent designs every time.
Compatibility with other hardware and software: ensures users can import data from a range of laser profilers and bore-tracking equipment, as well as being able to handle the large data sets that are generated from drone surveying.
Reporting: quick and easy with fully customizable, automatically generated reports ranging from loading diagrams and drill logs to cover sheets and blast quantity summaries.
BlastIQ Mobile
BlastIQ Mobile is a tablet-based software that allows accurate and efficient recording of blasthole data. Blast patterns are imported from SHOTPlus and parameters such as depth, explosive quantity and hole condition are electronically captured on bench. This allows quality assurance of drilling and loading operations and any variations from design are automatically reflected in the loading instruction at point of load, without the need to manually calculate an updated loading plan. GPS functionality available in BlastIQ Mobile allows accurate hole identification regardless of whether hole IDs have been marked on the bench or not. This helps operators to easily identify holes on the bench, reducing errors from potential confusion over hole ID and ensuring accurate recording of which holes have been dipped or loaded.
BlastIQ Insights
Rounding out the BlastIQ control solution is the powerful insights and analytics engine incorporated into the BlastIQ platform. BlastIQ Insights ingests data from BlastIQ Mobile and SHOTPlus and produces automated insights and analytics to help the drill and blast team seamlessly measure and manage blasting KPIs. The data are easily accessible from any connected computer or smart phone via the BlastIQ Insights webpage and provide quarry managers with the tools to monitor performance over time. For example, compliance to minimum specified tolerances, such as over/under-loading and over/under-drilling, are automatically generated for every blast. Figure 5 is an example from the BlastIQ Insights webpage showing a hole collar accuracy report that has been automatically generated.
In addition to the automatically generated insights, the BlastIQ public API (application programming interface) and soon-to-be-released database allows users to export the raw data into their own custom reporting system. An area manager overseeing several sites could use this API to design their own custom reports for all the sites, allowing them to make comparisons between the relative performance of each quarry and highlight any areas of concern or potential for improvement.
FRAGTrack
FRAGTrack is a state-of-the-art fragmentation measurement system that uses advanced machine vision technologies to perform automated fragmentation capture, analysis and reporting. FRAGTrack differentiates itself from other fragmentation measurement systems by the quality of image analysis as well as its reliability when working in harsh operating environments. It uses dual cameras and automatic triggering to efficiently capture representative samples only. The stereoscopic images are automatically processed using a combined 2D/3D technique to provide fragmentation distribution curves. Historical trends are presented graphically via the FRAGTrack web portal, and filters can be applied to focus on specific passing sizes, time windows or user preferences. Utilizing FRAGTrack closes the drill and blast loop by providing fragmentation results which engineers can use to calibrate the fragmentation prediction model in SHOTPlus and make tweaks to their designs. The cyclical approach of design, implementation and validation can be used to optimize blast outcomes for maximum efficiency.
Boosting productivity with technology solutions
For quarrying operations, achieving consistent, high-quality blast outcomes which comply with vibration, safety and environmental constraints saves time and money. Utilizing BlastIQ adds value at every stage of the drill and blast process. Automated designs using templates and loading rules ensure consistency no matter who is designing the blast. The SHOTPlus vibration and fragmentation prediction tools make sure that not only do blasts adhere to strict environmental constraints, but they also deliver on fragmentation. Once completed these designs can be sent wirelessly, via the BlastIQ cloud, to the BlastIQ Mobile tablets for use by the blast crew on the bench.
As loading progresses and data are entered into the tablets, this information is available instantly to view on BlastIQ Insights. This not only allows managers to monitor blast progress in real time from their office, but also ensures that missing or wet and illegible loading sheets are a thing of the past. After blasting, all the data remain securely stored in the BlastIQ cloud and are quickly and easily accessible at the click of a button. Having this centralized storage facility aids regulatory compliance by ensuring information is readily available rather than having to search filing cabinets full of paper-based blasting specifications.
For area managers and supervisors overseeing multiple operations, BlastIQ allows them to analyse blasts in a matter of minutes from the comfort of their own office. From pre-blast modelling through to post-blast measurement and analysis, the BlastIQ platform delivers all the data, benchmarks and insights needed to ensure sustainable, cost-effective improvements in blast performance. For further information, visit: www.orica.com/BlastIQ
- Subscribe to Quarry Management, the monthly journal for the mineral products industry, to read articles before they appear on Agg-Net.com