First Liebherr Batching Plant For London Concrete
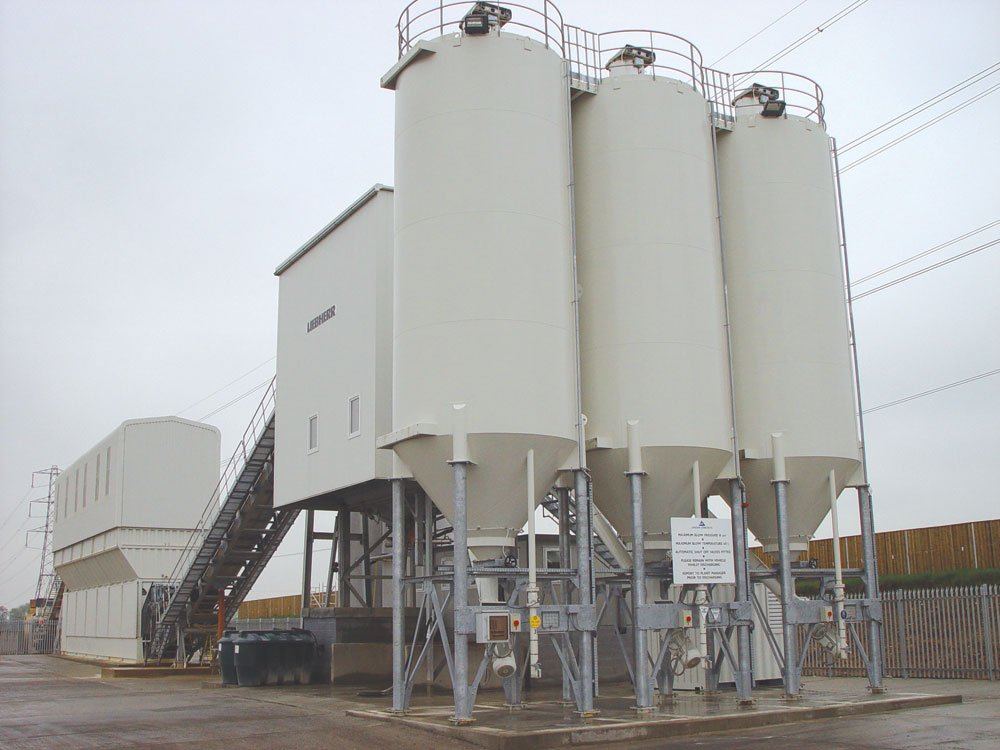
New £1.8 million facility at Denham
Located on a sizeable purpose-built site within the perimeter of Summerleaze’s new sand and gravel quarry, near Denham, London Concrete’s latest ready-mixed concrete facility comprises a high-volume Betomix 4.5 mixing and batching plant, designed, built and installed by Liebherr. As part of the Aggregate Industries group, London Concrete have been associated with Liebherr for many years and own a large fleet of 8m3 HTM 804 truckmixers, five of which are currently operating out of the new site. However, the new £1.8 million facility at Denham represents London Concrete’s first-ever acquisition of a Liebherr concrete production plant.
Comprising a number of modular elements and designed for high-speed mixing and rapid turnaround, the Betomix 4.5 is one of the larger wet-batch mixing plants in the Liebherr range. It features a twin-shaft paddle mixer, six large-volume automated aggregate and sand bins, three large cement silos and automatic dosing facilities for up to eight different admixtures. The plant came on stream in March 2009 and, when operating at full capacity, is capable of producing high-quality concrete at rates of up to 120m3 per hour.
A particular advantage of the new London Concrete facility at Denham is that the site offers plenty of space, which allowed the configuration, materials flow and discharge area to be optimally designed. Vehicle access is excellent and there is plenty of space around the plant for truckmixers, delivery vehicles, wash-out/recycling facilities and plant/site maintenance operations. Perhaps the biggest benefit, however, is that the plant receives its sand and gravel supplies direct from Summerleaze’s adjacent quarry’s stockpiles.
Aggregate/sand feeding and storage
Sand and gravel are introduced to the concrete plant by loading shovel via a ramp and ground-level feed hopper. From here, the materials are delivered to storage by a fully enclosed 1m wide x 25m long inclined chevron belt conveyor. This, in turn, discharges on to an 800mm wide x 10m long tripper conveyor, powered by direct-geared electric motors, which automatically discharges the sand or aggregate into the appropriate hopper.
A total of six 80-tonne capacity in-line storage compartments cater for two different grades of sand and four aggregate sizes. Material levels in the hoppers are monitored by sonic-type indicators and the two sand bins are equipped with moisture meters and vibrators. Mounted at ground level beneath the storage hoppers, a 1m wide x 25m long horizontal collecting conveyor, equipped with a 12,000kg maximum-load electro-mechanical belt weigher, delivers the required materials on to a fully enclosed 1.2m wide x 27m long inclined feed conveyor, which, in turn, discharges into the mixing plant aggregate weigh hopper.
A wall and roof structure, specially designed and built to fully enclose the storage hopper and tripper conveyor installation, provides total weather protection and contributes to the control of dust and noise emissions.
The mixing section
At the heart of the concrete plant is a Liebherr DW 4.5 twin-shaft paddle mixer, which features twin 75kW electric motor drives, has a single batch volume of 4.5m3 of compacted concrete and incorporates a high-pressure automatic washdown system. Electro-mechanical systems are used to weigh the cement and water, with three 90-tonne capacity cement storage silos, each equipped with a reverse-air-type exhaust filter for dust-emission control, feeding the cement weigh hopper via three 13m long screw conveyors. A recycled water system and fresh water pumped from an on-site borehole provide the mixing operation with a dual water supply. Once again, the entire mixing section is fully enclosed for complete weather protection.
The control centre for the plant is housed within a 7m x 4m cabin located adjacent to the mixing section. This features a Command Alkon plant-control system, which provides the necessary interface with the Liebherr starter panel, as well as a Bellboy telematic stock-control system. Also included within the cabin is an array of video monitors linked to strategically located CCTV cameras, which provide continual images from critical points around the plant.