Long-term Asphalt Storage Solutions
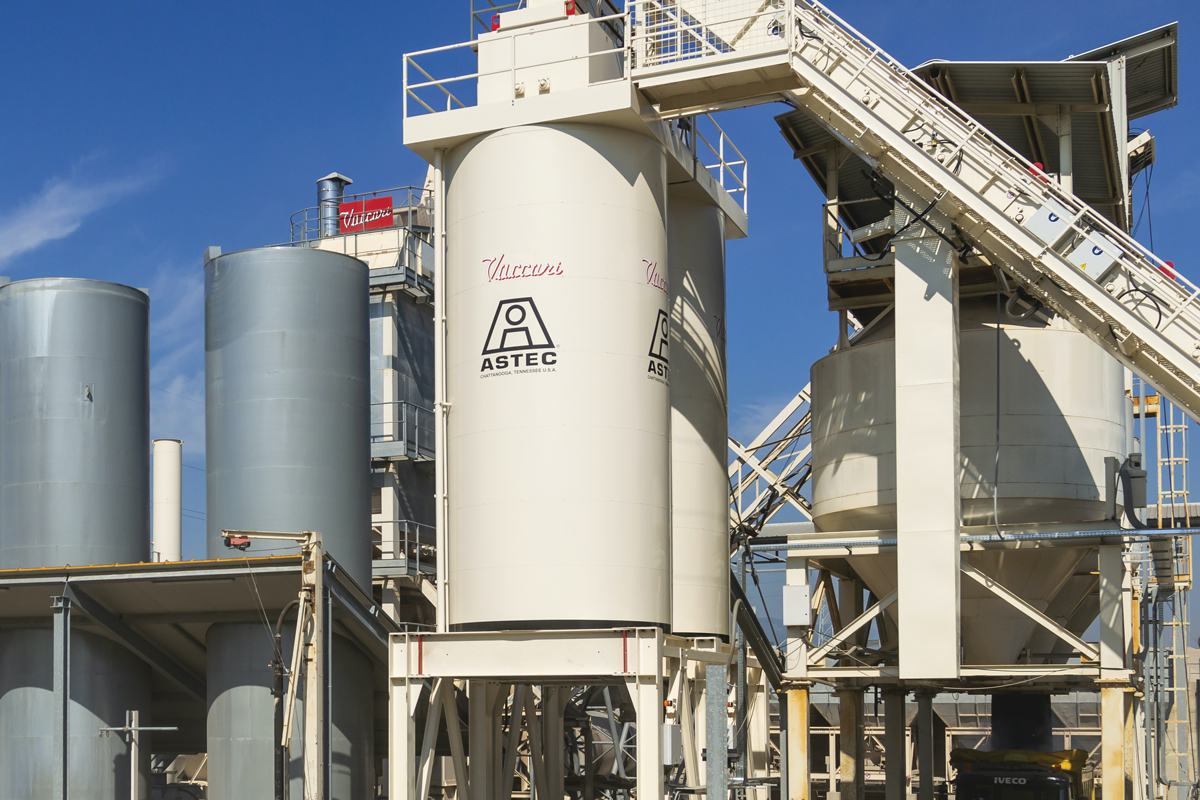
First published in the January 2020 issue of Quarry Management as Sophisticated Silos
Andrew Pettingale, managing director of BG Europa, discusses the technological and commercial benefits of a long-term asphalt storage solution from Astec
Having a clear market vision is anything but simple, especially at a time when trends and responses are rapidly changing. The evolution of market demand requires increasing flexibility in terms of how asphalt is produced and stored, based on the relatively limited shelf-life of the finished product. To be successful, producers need to formulate a strategy that meets the demands of the market, while limiting excess production of unused asphalt and enhancing production efficiency.
‘The desire to embrace more environmentally responsible technologies, together with the economic advantages of inclusion of high levels of recycled products within asphalt is encouraging producers to evaluate their production methods,’ said Mr Pettingale. ‘However, to enhance the economic and environmental benefits requires production equipment to be utilized at maximum efficiency. This is often in conflict with a requirement to fulfil small orders (especially when different mix designs are required for these smaller orders) which are difficult to manage in a rational way, but often represent an important part of the overall volume the producer turns out.’
The biggest problems relate to the preservation of the mixed material when stored for long periods of time, associated with:
- The demands of a market that often presents fragmentation of supply to many jobs, each requiring small or medium amounts of asphalt, making it difficult to efficiently satisfy every request
- The proliferation of mixes that often require the production of the same product on multiple occasions throughout the day, together with the costs associated with either starting or cleaning out the production plant to satisfy this requirement
- The increasing frequency of night and weekend works that require mixes outside the normal operating hours of production facilities and the support network for such
- The requirement for mixes within conurbations and the difficulties associated with the operation of production facilities close to these sites of product requirement.
Technology and potential
‘Opportunities exist for producers to satisfy changing market requirements, providing their customers with a ready supply of quality mix. Astec long-term storage silos have particular characteristics which allow the producer to insulate the material for up to four days, with the guarantee of preserving the technical characteristics of the mix,’ continued Mr Pettingale. ‘At first sight, they look like simple silos, however within they contain sophisticated technology that comes from an in-depth knowledge of the material and the dynamics of oxidation and loss of the mix’s physical and chemical properties.’
Astec long-term storage silos allow producers to use the silos as a conventional surge bin during the busy time of the day. At the end of the day, time-consuming start/stop operations can be avoided and silo filling can commence while load-out continues. The next working day, mix can be sold straight away from full silos, without awaiting plant start-up. No one needs to wait for mix and any delays to production plant start-up can be mitigated. Uninterrupted production runs allow producers to maximize equipment efficiency and reduce material waste.
Incorporating multiple silos into production plant layouts ensures producers are ready to meet customer needs for a number of different mixes, whilst reducing operating costs and improving plant operating efficiency.
In addition, the potential to store mixes for up to four days without loss of mix quality (polymer-modified, open-graded and SMA mixes excluded) is guaranteed in writing by Astec. This allows producers to further optimize and rationalize production facilities by utilizing the concept of satellite storage, providing customers with a readily available supply of high-quality mixed material in areas unsuitable for the location of production facilities, due to either environmental concerns or economic constraints.
More than simple silos
Astec long-term storage silos are not just insulated containers, but a storage system in which all the elements, from the loading hopper, through the elevator conveyor and transverse conveyor up to the silo batcher, to the silo and lower cone, are designed to optimize the process. The main elements that make it a unique technology are:
Insulation
To keep the mix hot, the silos feature 300mm of insulation on their top, 100mm around the cone, and 150mm along the length of cylinder. Batchers are insulated too, because uninsulated batchers are a major source of heat loss. Two layers of stiff sheet insulation are staggered to eliminate heat-leaking seams along the silo cylinder, with Astec using thick, full R-value, non-compressed insulation for this purpose.
Top seal
In storage mode, the cylinder-operated gate at the top of the batcher is completely sealed. The gate runs in rails which tightly wedge it against a ring of grease. This forms a tight seal and prevents air from entering at the silo top.
Bottom seal
Astec’s patented discharge gate seals the bottom of the cone when the silo is in storage mode. The heated and insulated discharge gate closes to completely cover the cone opening. Oil is pumped into the gate to seal the bottom silo opening. The oil reservoir is located by the silo legs, with a motor-driven pump moving the oil from the reservoir into the gate. A sensor monitors the oil level in the gate and controls the pump.
Lower cone
The lower cone has a specific inclination of 66o, which naturally prevents segregation and build-up of the material. To prevent wear caused by the material, the interior is lined with wear-resistant steel although optional ceramic liners can be installed.
Cone wall heating
A silicone electric heating blanket surrounds the lower cone section and a thermostat activates the blanket when the temperature drops below a set point. This sensor saves money, because energy to heat the cone is only used when required. Hot-oil heating is available as an alternative to the electric blanket.
Material transport
The drag conveyor extends to the top of the silo, with strong, wear-resistant, roller chain running from bottom to top, with deep, steel slats attached every 300mm. This heavy slat-chain assembly resists hydroplaning of the mix. Depending on required capacity, Astec offer either single- or dual-chain configurations. The drag conveyor discharges into a traversing conveyor on top of the batcher.
Batcher
When the batcher on top of the silo is full, it releases the slug of mix, which drops through a rapid-opening double-clam gate into the silo and flattens on impact. Astec’s double-clam gates are not like the conventional pinch-closed style double-clam gates. The overlapping gates slice through the material flow as the gate closes. This slicing action with the overlapping gates results in better gate wear resistance compared with pinch-closed style gates. The double gates also centre the drop into the silo and form a flattened mix surface, which prevents mix segregation.
Silo pressure equalization
As the mix level rises it displaces air in the silo. Integrated vents inside the batcher enclosure allow bi-directional airflow and equalize silo pressure as the mix level changes during filling and load-out.
External coating
The outer casing of the silo is made of aluminium and finished with a coating that maintains its quality characteristics over time. Paintwork can be in the official Astec livery or in the customer’s choice of colour.
Support structures
The walls of the silo are made from rolled-steel plate joined by structural weld. Jogged radial joints form a smooth inner surface, reducing wear at the joints. Standard silo legs provide 4.0m of clearance for trucks from the top of the weighbridge. The legs and silo support frame, which are made from heavy, structural, wide-flange beams, are designed to meet the site-specific design criteria at the installation location.
Advantages of the Astec solution
The possibility of planning plant production in a more linear way is the first and most obvious advantage of the silos. By storing up to four days’ worth of material with Astec’s guarantee of the quality, producers can cope with the peak loads, small supply requirements and intelligently use production plant downtime.
Being able, in a logical way, to schedule when to start a plant and when to shut it off is also an advantage. With the silos, it is possible to cope with the first load flow very quickly and to shorten the loading times, as material can be prepared continuously and loaded quickly when trucks arrive.
The ability to store mixed material to overcome short-to-medium-term interruptions to paving operations, without wasting mix, is another advantage. Where projects require high volumes of mixed material, production capacity can potentially be exceeded, necessitating the production of a buffer of material prior to the commencement of works. Disruption to paving operations, either due to equipment breakdowns or changing weather conditions, can be mitigated by storing material for up to four days without loss of quality.
A further advantage is the potential to maximize production plant capacity/efficiency, eg by filling either plant-based or satellite storage facilities on a Friday afternoon and then providing customers with high volumes of quality mix early Monday morning, without waiting for production plant start-up.
‘Astec long-term storage silos revolutionized asphalt production methods in the US, allowing customers to take advantage of clean technologies, such as the Double Barrel, for high-capacity recycling of asphalt products, whilst maintaining the flexibility in supply to their customers,’ said Mr Pettingale. ‘Recently, our customers in Europe, by utilizing Astec silos for satellite storage applications, have taken these advantages one step further by consolidating production at highly efficient, environmentally responsible production facilities.
‘Investment in long-term storage solutions allows producers to position themselves differently in a competitive market and take advantage of clean, efficient technologies and production methods, whilst enhancing service to their customers.’
For more information visit: www.bgeuropa.co.uk or www.astecindustries.com
- Subscribe to Quarry Management, the monthly journal for the mineral products industry, to read articles before they appear on Agg-Net.com