R. Collard install bespoke MRF from BlueMAC
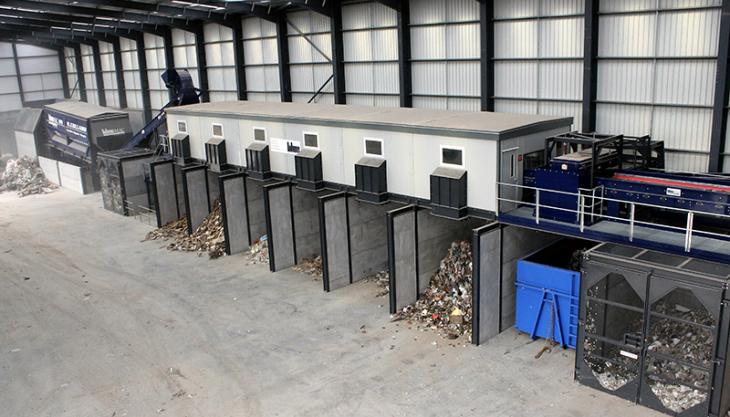
New materials recovery facility (MRF) in operation at state-of-the-art recycling centre in Hampshire
A TAILOR-made MRF solution – designed and built by BlueMAC – has been supplied to demolition contractors R. Collard Ltd. The new materials facility, which was distributed by Blue Machinery London, has been created to meet Collard’s specific requirements and is incorporated into a 80m x 30m undercover building at the company’s recently opened recycling facility in Eversley, Hampshire – one of four recycling centres operated by Collard.
The new MRF is part of a planned expansion of the contractor’s recycling activities and is a necessary investment to help cope with the steady rise in waste material volumes available for recycling, which is largely as a result of Collard’s increased demolition work and expanding skip hire activities.
As well as contributing to Collard’s growth in waste management, the MRF will also play a major part in ensuring minimum ‘tip-to-landfill’ from the incoming waste-stream, as well as producing high volumes of clean, saleable recycled materials. The MRF will predominantly process construction and demolition waste but, with future proof versatility built in, will be more than capable of handling other waste materials such as C&I (commercial and industrial) as the need arises.
Commenting on his company’s new acquisition, managing director Rob Collard said: ‘We’ve been working with Blue Machinery London for many years and found their experience and expertise on this project to be invaluable. From the outset at the concept stage right through to installation, the communication and attention to detail were second to none.’
The BlueMAC MRF begins with a variable speed belt feeder steadily conveying the incoming waste stream into a 2510 trommel, which removes fines at 50mm and then transferred on to a 50m long transfer conveyor to the fines clean-up system at the other end of the building. En route the fines pass an overband magnet which removes any ferrous metals.
The material is transferred into the fines processing system by a conveyor fitted with a magnetic head roller for smaller ferrous metal extraction, which is collected via a chute into a skip. The remaining material passes over a flip-flow screen for processing of fines to –10mm.
The 10-50mm is then segregated through a GK air classifier for heavy and lights separation, the light fraction being ideally suited to the production of SRF (solid recovered fuel).
After the trommel, the 50mm+ material passes an air separator before entering the picking station, which has been purpose-designed in a six-bay, double-sided configuration with six additional drop boxes for high value material such as non-ferrous metals or cabling.
The station features an extra wide cabin for operator safety and has been supplied complete with industrial specification on wiring, heating and lighting for a comfortable and safe working environment.
The picking station’s 1,500mm wide conveyor belt, with variable speed, provides optimum material spread allowing maximum recovery. After the picking station, the overband magnet cleans up the remaining material, dropping ferrous metals into the same collection area as that on the fines transfer belt. The last part of the process sees the material conveyed past a secondary air separator to give a final clean to the hard core.