Processing versatility at Creeton Quarry
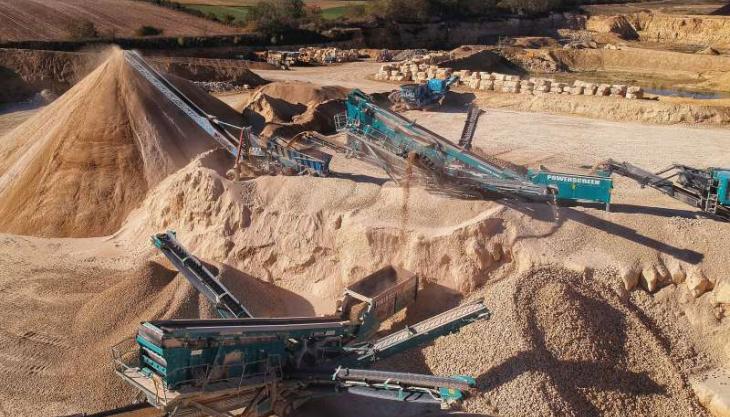
Creeton takes delivery of Powerscreen Chieftain 2200 triple-deck mobile screen with new auxiliary radial conveyor
FOLLOWING on from the purchase of a Premiertrak 400 XA jaw crusher in 2017, Creeton Quarry, in Lincolnshire, has recently taken delivery of a new Powerscreen Chieftain 2200 mobile screen to help grade and separate the site's crushed limestone material, which is utilized in a wide range of masonry projects.
Whilst processing operations at the site can change depending on requirements, a typical set-up is for stone from the quarry face to be loaded in to the Premiertrak 400 XA, which reduces the material to –100mm before feeding it to the new Chieftain 2200 triple-deck screen to create four sizes of product.
These include an agricultural lime, a 2in clean and a Type 1 that is fed to a second screen, a Chieftain 2100, for a specific job where the stone is further separated into 40–20mm and 20–5mm fractions, as well as further quantities of lime dust.
The fourth product, the oversize, is extracted via the Chieftain 2200’s new auxiliary radial conveyor, which can rotate through 0–70 degrees. Depending on customer requirements, the oversize can be fed to an impact crusher before being recirculated to the Chieftain 2200.
The new Chieftain 2200 incorporates two triple-deck screenboxes and can switch between a two- and a four-bearing arrangement. The machine has an integrated, high-capacity, variable-speed belt feeder and its heavy-duty, single-shaft screenboxes can be adjusted for stroke, angle and speed. Another key feature of the Chieftain 2200 is hydraulic screen tensioning on the bottom deck.
Steve Johnson, the quarry manager at Creeton, said: ‘We purchased the machine so we could go a bit faster and harder, and get a better, cleaner product. The aggressive nature of the screenboxes also means the Chieftain 2200 can handle the British weather.’
The quarry’s new 2200 model replaced an earlier Chieftain 2100, which Mr Johnson says was one of the key reasons why he did not have to look any further than Powerscreen when upgrading the unit. ‘The last machine was twelve-an- a-half years old and we sold it no problem. It was still working hard until the day it was taken away on the low-loader, it’s just that newer machines are superior and more advanced, so we upgraded,’ he said.
With the older machine, there were times the Powerscreen crusher feeding it had to be turned down, whereas the new 2200 model is capable of processing considerably more tonnage per hour, which means the operators and crusher can work at their maximum capacity, making the site as efficient as possible.
The end products are being used for a range of purposes from electric substations, roads and private driveways to piling mats. Helping to make a clean product are the Major Wire screens within the Chieftain 2200. These media help reduce blinding in wet conditions and by offering longer life are expected to reduced wear costs considerably.
Blue Machinery salesman Ian Taylor commented: ‘Like many quarrymen, Steve just wants to get on and produce. One of the reasons he chooses Powerscreen is because he knows that Blue and Powerscreen are there to support him in reaching his objectives.’