Powerscreen to highlight crushing and screening expertise
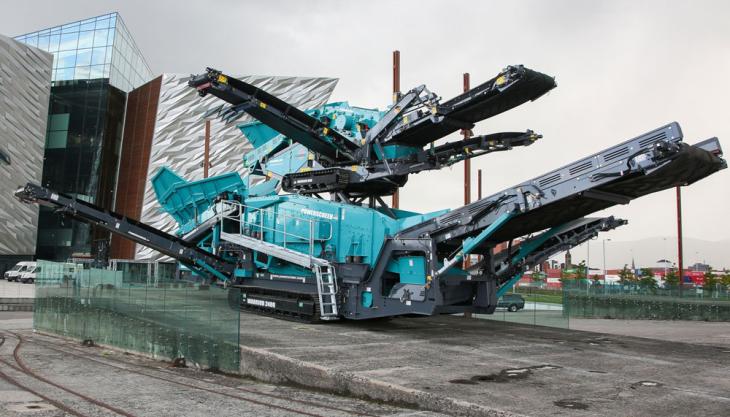
Company announces strong product line-up at the show including Premiertrak 600 jaw crusher
POWERSCREEN, one of the world’s leading providers of mobile crushing and screening equipment, will be displaying three machines – the Premiertrak 600 jaw crusher, Warrior 600 screen and Warrior 2400 unit – at this year’s Conexpo-Con/Agg.
Warrior 600 – this compact heavy-duty mobile screen makes the Warrior range the widest in the market with seven machines of varying size to meet a range of customer requirements. Ease of transport is only one of many key features on this model. The Warrior 600 screen is highly versatile with its groundbreaking simple conversion from three-way split mode to two-way split mode, which can be completed in minutes. The machine has been specifically designed for operators for whom versatility, manoeuvrability and transportation are of key importance.
The Warrior 600 also features a highly aggressive 2.4m x 1.2m screenbox capable of 6g of acceleration. The high-strength, high amplitude, two-bearing screenbox promotes easy handling and separation of large items from material fines in recycling applications, such as fines and rock from overburden and blasted rock. User benefits include a rapid set-up time and ease of operation aided by hydraulic folding side conveyors, rigid feed hopper sides and two-speed tracks.
Warrior 2400 – specially designed for large-scale operators in the quarrying and mining sectors, the Warrior 2400 screen (available with optional dual power) is capable of handling larger feed sizes and throughputs while remaining convenient to move and transport.
It features a heavy-duty inclined screen with a high-amplitude triple-shaft drive mechanism that lends itself to screening, scalping, two- or three-way splitting and stockpiling materials such as aggregates, topsoil, coal, construction, demolition waste and iron ore. The screen will accept a wide variety of media ensuring it is suitable for many applications.
Set-up time and ease of operation are aided by hydraulic folding tail and side conveyors, two-speed tracks, a slide-out tail conveyor facility (for media access) and a load-sensing collection conveyor circuit to avoid blockages. A simple-to-use electrical control system allows operators to monitor and diagnose the machine on site via an LCD display, without specialist tools.
Premiertrak 600 – the diesel-hydraulic and diesel-electric variants of the Premiertrak 600 jaw crusher have been designed and built to deliver maximum production and performance with increased uptime and low running costs.
The high-capacity jaw is fed by a vibrating grizzly feeder with variable-speed control and a large grizzly area to maximize the removal of fine material to extend the wear life of the jaw plates within the crusher chamber. The bypass chute is also fitted with wear-resistant liners as standard, and incorporates an adjustable five-position deflector plate to divert material to either the product or side conveyors.
The machine control system incorporates a state-of-the-art, modern interface with intuitive graphics and high-resolution display for ease of operation. This is further enhanced with automatic start/stop functionality, intuitive diagnostic capability and straightforward machine adjustments.
The speed of jaw crusher on the Premiertrak 600 can be varied to suit the application and, therefore, optimize performance. In addition, the hydraulic system has been designed and configured to increase uptime and fuel efficiency.
The Premiertrak 600E electric variant is equipped with an oversize genset sufficient to run another plant (eg Powerscreen Warrior 1400XE heavy-duty scalping screen) but can be powered from a mains source, which substantially decreases the running costs and environmental impact.
With convenience and safety in mind, the Premiertrak 600 is fully set up from ground level thanks to its hydraulic folding and locking hopper system. It can be adjusted to maximize productivity and can be configured with an independent live pre-screen for the efficient removal of scalped materials either into a waste or sized sub-base product.