MAJOR introduce crown curve updates
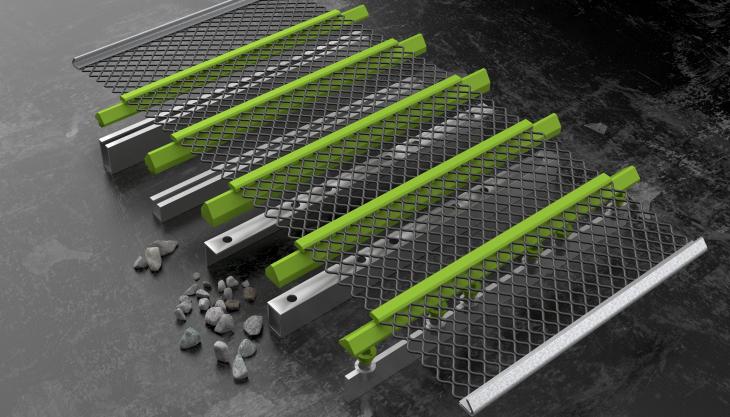
Screen media manufacturer optimizes Flex-Mat performance with improved crown curve calculation
MAJOR, one of the world’s leading manufacturers of high-performance wire screening media, have introduced a new crown curve calculation and updated crown curve adaptors that offer customers even greater performance from their tensioned Flex-Mat high-vibration wire screens and other screen media products on screen decks originally designed for modular panels.
According to the Canadian manufacturer, a proper curve on the screen deck will allow producers to tension the screen media correctly, which is vital to maximum performance and wear life.
‘We are dedicated to our customers’ screen performance and profitability, which is why we are continually making improvements to our screen media products,’ said Lars Bräunling, MAJOR’s director of product technology. ‘These crown curve updates will help maximize the screening capabilities of our innovative Flex-Mat high-vibration wire screens and contribute to a low cost per tonne for our customers.’
MAJOR’s crown curve adaptors allow producers to modify a flat vibrating screen deck for use with tensioned screen media and to try out tensioned media without the time and expense of a deck conversion. The update is a response to dealer and end-user feedback regarding the overall depth of the curve and its impact on material flow.
The change optimizes the performance of MAJOR’s tensioned screen media, including their signature Flex-Mat system, which is said to set a new standard in performance for aggregate, mining and industrial producers. The product’s high-frequency movement makes media an active part of the screening process, improving efficiency compared with static media such as woven cloth or synthetic panels.
MAJOR bond Flex-Mat’s wires with high-density polyurethane strips instead of weaving them. This allows wires to vibrate independently from hook to hook under material contact. The high frequency of the wires (8,000–10,000 cycles per minute) adds to the vibration of the screen box (800–900 cycles per minute) to speed up material separation and passing.
These features are said to improve material throughput while virtually eliminating near-size pegging on the top decks and fine material blinding and clogging on the bottom decks, reducing the cost of production per tonne.
The screen media also offers as much as five times longer wear life than traditional woven wire. The long wear life and minimized screening issues contribute to less downtime spent cleaning and replacing screen media, resulting in a lower cost per tonne and improved profits. It also means cleaner retained product through the middle decks and less risk of material contamination.
Unlike some self-cleaning screens, MAJOR design Flex-Mat to fit all decks, from scalping to finishing screens. It also features up to 40% more screen capacity than traditional woven wire and up to 50% more than traditional polyurethane and rubber panels.
Flex-Mat’s distinctive lime-green polyurethane strips bond independent OptimumWire wires. These long-lasting steel wires with an optimum carbon and manganese content provide the best combination of hardness and tensile strength, making them resistant to abrasion. They are also less susceptible to damage during high-impact conditions compared with standard oil-tempered or high-carbon wires.
Flex-Mat also provides a perfect 90-degree angle on its square pattern and +/–3% tolerance level of opening. Moreover, its optimum ductility allows perfect crimping of the wire without causing micro-damage, which can cause early failure of the wire during use.
MAJOR can manufacture Flex-Mat with either the patented OptimumWire or 304 stainless steel wire. The company also offers Flex-Mat in either side or end tension as well as most standard modular panel formats. It is available in five opening patterns, offering the widest range of openings on the market.