Kleemann prioritize personal protection
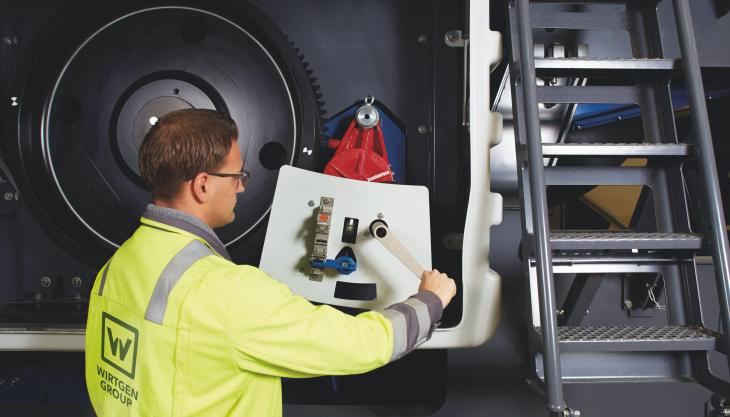
Safety and ergonomics of play major role in operation and maintenance of Kleemann machines
THE operation of large crushing and screening machines is often associated with an increase in potential danger, which is why Kleemann have made personal protection their highest priority.
However, safety should not impede the operator and must be integrated imperceptibly into the work process. As the complexity of modern plants increases, parallel to this the development team at Kleemann ensures that operation and maintenance remain as quick and simple as possible.
The interface between human and machine is the control system, and Kleemann’s entire PRO line, and the Mobirex MR 130 Z EVO2 impact crusher, can be comfortably operated via the company’s intuitive SPECTIVE control concept.
The control system’s 12in touch panel simplifies work as all functions are visible at a glance and clear symbols direct the user. Moreover, the user interface is not affected by dust, is splash-proof and can be easily read in difficult lighting conditions.
Simple menu guidance ensures that only the information that is currently required is displayed on each page, making it possible to fully utilize the functions of the crushing plant properly and in a simple manner.
In everyday operation, however, not only is a simple control system important, but also easy access to the machine. Thanks to Kleemann’s intelligent machinery design, all relevant service areas are easily accessible.
For example, it is possible to refuel the Mobicon MCO 11 PRO cone crusher comfortably from the ground, whilst the pre-screen coverings for the Mobirex MR 110 and 130 Z EVO2 impact crushers can be easily changed via an extra platform.
Moreover, the EuroTEST-certified ‘Lock & Turn’ system (pictured) on the mobile impact crusher provides the highest level of safety during rotor ledge changes and when releasing bridging.
Here, special keys are used in combination with the machine control system which only permit work in danger areas when they are locked. Only then can the operator open service flaps or move and exchange components. If the user wants to work on another area, the keys must be removed, which automatically blocks the area worked on previously.
A particular highlight of this system in terms of safety and convenience is the rotating device for the rotor. It allows the rotor of the crusher to be turned and blocked manually, via a gear unit, in any position from the outside. Thus, the exchange of rotor ledges and the elimination of bridging can be carried out even greater safety.
In addition, new, optional package for noise reduction ensures comfortable and safe work close to the impact crusher. Noise-protection flaps mounted on the side at the same height as the engine deflect sound upwards. These flaps are folded in for plant transport and therefore have no bearing on transport width.
Also, the bottom of the unit is sealed, reducing the volume of noise the user experiences by 6dB (a reduction of 3dB has the effect of halving the amount of noise perceived by the human ear). This award-winning feature not only ensures a quieter work area for operators within a significantly smaller radius around the machine, but also protects the environment and makes urban operations much more acceptable.