Asphalt and climate protection go hand in hand
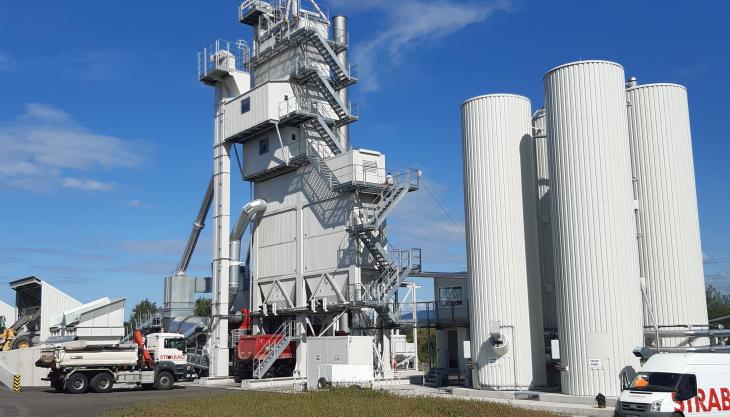
STRABAG gain production and environmental benefits from Ammann ABA UniBatch mixing plant
FOR nearly 1,000 years, Zvolen has been one of the most important transport hubs in Slovakia. Numerous trade and logistics companies have been located there, where the routes connect the North, South, East, and West.
With the construction of the new R2 motorway, STRABAG are pursuing a demanding infrastructure project in this area. With a project of this magnitude, an uncomplicated, reliable supply of asphalt must be ensured, but that is not the only reason the company opted for a new Ammann ABA 160 UniBatch asphalt mixing plant at Kalinovo.
The ultra-modern plant combines productivity with an elaborate design and systematic energy savings, keeping emissions to an absolute minimum. This important environmental angle took priority for the decision-makers due to the proximity of the Low Tatras National Park – and because it fits well with STRABAG’s own sustainability strategy.
The Ammann ABA 160 UniBatch is described as a fully equipped ‘climate protector’: additions for agents, fibre, and cold recycling ensure that the right mix can be prepared for every application. Volumes and additions can be controlled with total flexibility thanks to the latest version of the as1 control system.
Covered metering devices protect the aggregates from moisture, saving on fuel for drying. Also, by enclosing the bucket conveyor, the resulting bitumen vapour is exhausted completely and supplied to the afterburning system, preventing odour pollution for residents and resulting in low exhaust values.
Project manager Thomas Barth supervised the installation of the ABA 160 UniBatch – the sixth Ammann asphalt mixing plant in Slovakia. ‘The Kalinovo location was previously running an old Teltomat 5, and the technology was no longer in line with the times,’ he explained.
‘With the Ammann ABA 160 UniBatch, the company now has an ultra-modern plant with a leading recycling addition. Up to 40% reclaimed asphalt can be added to production, saving resources, and reducing emissions.’
During installation, special attention was paid to routine maintenance. Large pedestals offer convenient access to all standard control and operating points, although much of the work handled by the Ammlub lubrication system.
Installed at the maintenance point, the intelligent system triggers automatic bearing lubrication at short intervals and without interrupting operations, resulting in reduced maintenance effort. Continuous component lubrication prevents downtime and iincreases the plant’s operational reliability.
More than 60,000 tonnes of asphalt were produced at the plant between its commissioning in April 2021 and the year end. A similar utilization rate is planned this year, as there are still many kilometres of motorway paving ahead.
Despite these high volumes, the plant’s new filter technology ensures energy savings and much lower emissions, which is not only good news for local residents, but also for the surrounding nature reserves.