Winning Weighs
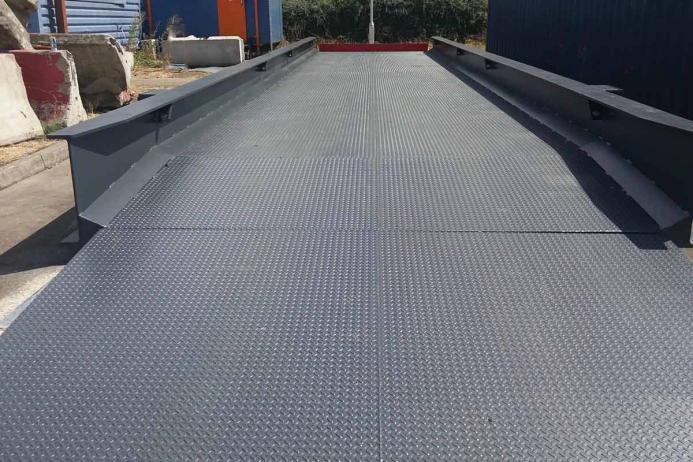
First published in the March 2024 issue of Quarry Management
Improving quarry efficiencies without breaking the bank
The quarrying industry presents a highly challenging environment, demanding high levels of reliability for equipment, machines, and processes. In parallel, the continual management and improvement of health and safety on site is at the heart of every aspect of operations.
Although there have been significant developments in quarry automation over the past two decades, in the majority of cases these have been more conservative compared with those in other less-arduous working environments. One restraint on expanding quarry automation can be the entrenchment of existing, company-specific, site-management systems. In a large number of applications, these are networked across a number of sites throughout the UK and the cost to upgrade the systems in their entirety can be prohibitive.
This is where versatile weighbridge software systems such as Weightron’s WinWeigh have an important role to play. WinWeigh can be tailored to integrate directly with existing bespoke quarry systems and bring important operational benefits in a very cost-effective manner. More often than not the software can be implemented without major changes to the weighbridges themselves.
Traffic management – an integral part of the site weighing processes
One particular area where improvements can be made is in on-site traffic management, including vehicle loading or unloading.
The combination of accurate and efficient weighing together with flexible traffic management brings significant benefits to quarry operations. This can be achieved by implementing versatile weighbridge-management software systems that address both aspects and link seamlessly with proprietary site-wide systems.
In many applications, especially where multiple products are processed and transported, quarry efficiency is directly linked to the expedient loading and management of vehicles. This is particularly true where vehicles are loaded at different site locations via weighing shovels or hoppers. To overcome preloading queueing problems and bottlenecks, on-site operators are issued with robust hand-held PDAs (Personal Digital Assistants) which link directly with site-management systems via WinWeigh to provide real-time information.
Single-product loading points
In a typical example, pre-registered empty vehicles arriving at site are identified via ANPR cameras or RFID tags before being weighed (if the vehicle is not registered details can be manually entered). Large display signs, linked into the system, can be used to show arriving vehicles where to go. If required, vehicles can be directed to a holding point and ‘called’ when a weighbridge becomes empty. WinWeigh stores the first weighing and the vehicle moves off.
WinWeigh will check the queues at each of the listed loading points from the pending pre-loaded records and assign the load for the new weighing record to the next available loading point with the shortest queue (if there is only one loading point associated with the product, all loads are sent to that loading point). Vehicles will then be directed to specific areas for loading. Their details are stored in a pending file and sent to the shovel PDA. The vehicle queue for that loading point is displayed on the PDA with details of vehicle, loading point, and product. The shovel driver can now select the vehicle they want to load. Once this selection has been made, the load automatically disappears from the other PDAs.
The vehicle details are displayed to the driver for confirmation. If they select YES, the process continues to the next step. If they select NO, the process will return to start.
The shovel driver is then prompted to load the vehicle. Once loaded, the driver accepts the load and the process continues. With the load complete, the driver is prompted to enter the amount of product loaded in tonnes. Once entered, the system confirms completion and the process then resets to the start, ready for the next loading cycle.
The loaded vehicle then returns to the weighbridge to be weighed out. Each loading point can have a field associated with it that holds an editable ‘average loading time’. This would typically be defined by the particular site, based on understanding of location and types of material loaded at that loading point. This information can be used to continually adjust the loading time for optimum efficiency.
Multiple loading points
The use of PDAs with WinWeigh can also be used to manage vehicles being loaded with recipe-mixed products, such as asphalt or ready-mixed concrete.
Once the product is edited and a recipe stored, the loading point group is chosen and from that group up to six different loading points can be assigned to the record. When a weighing transaction is started for this Product/Recipe, WinWeigh will check the queues at each of the listed loading points from the pending records and assign the load for the new weighing record in turn to the next available loading point with the shortest queue. Once loaded, vehicles weigh out.
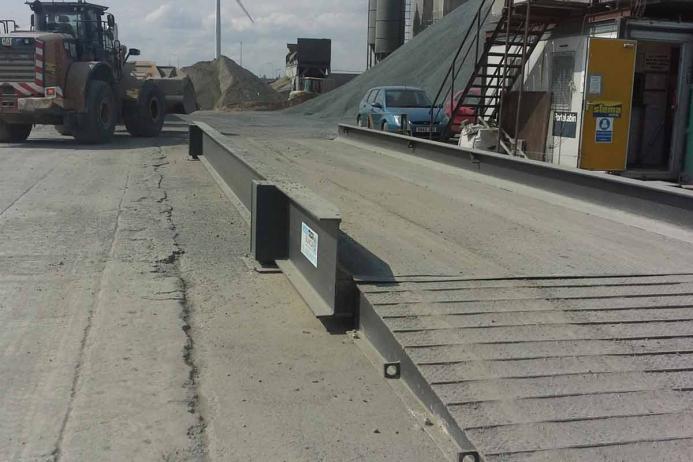
Weighbridge mechanical design developments
Without doubt, weighbridges play a crucial role in the day-to-day running of quarries. This proving ground is second to none and robust design and build criteria continue to be a high priority for any replacements or upgrades.
The Titan low-profile surface weighbridge is designed for reliable, high-capacity vehicle weighing in such harsh working environments. Weightron have been manufacturing this traditional one-piece, side-beam weighbridge design for more than 40 years and the fully welded drive-through steel structure is designed to withstand very high concentrated loads and continual use.
The deep-profile, robust longitudinal beams offer an extremely stiff, yet low-profile structure. The varying concentration of lateral steel beams along the length of the weighbridge deck takes into account high loading areas and the oversized longitudinal side beams are specified for minimum deflection along the length of the deck.
Surface weighbridges are commonplace in quarries and the Titan can be supplied with integrated sloping entry and exit ends. This significantly reduces the height of any ramps that are required, which, in turn, makes it easier for vehicles to drive on and off the weighbridge.
If older weighbridges need replacing, Weightron have the manufacturing versatility to design weighbridges to fit existing pits and concrete ramps. This not only reduces cost, but also minimizes site disruption.
Weightron sales director Nick Burley is clear on how the company can help quarries achieve greater efficiencies in key areas: ‘Bespoke software that integrates directly with established quarry management systems brings a number of advantages in terms of operational costs and traffic management,’ he said. ‘If required, such systems can be implemented in organized stages, without disrupting day-to-day operations. If weighbridge hardware needs upgrading, we have the products and manufacturing versatility to execute these changes quickly and cost-effectively.’
Subscribe to Quarry Management, the monthly journal for the mineral products industry, to read articles before they appear on Agg-Net.com