Automated Weighing
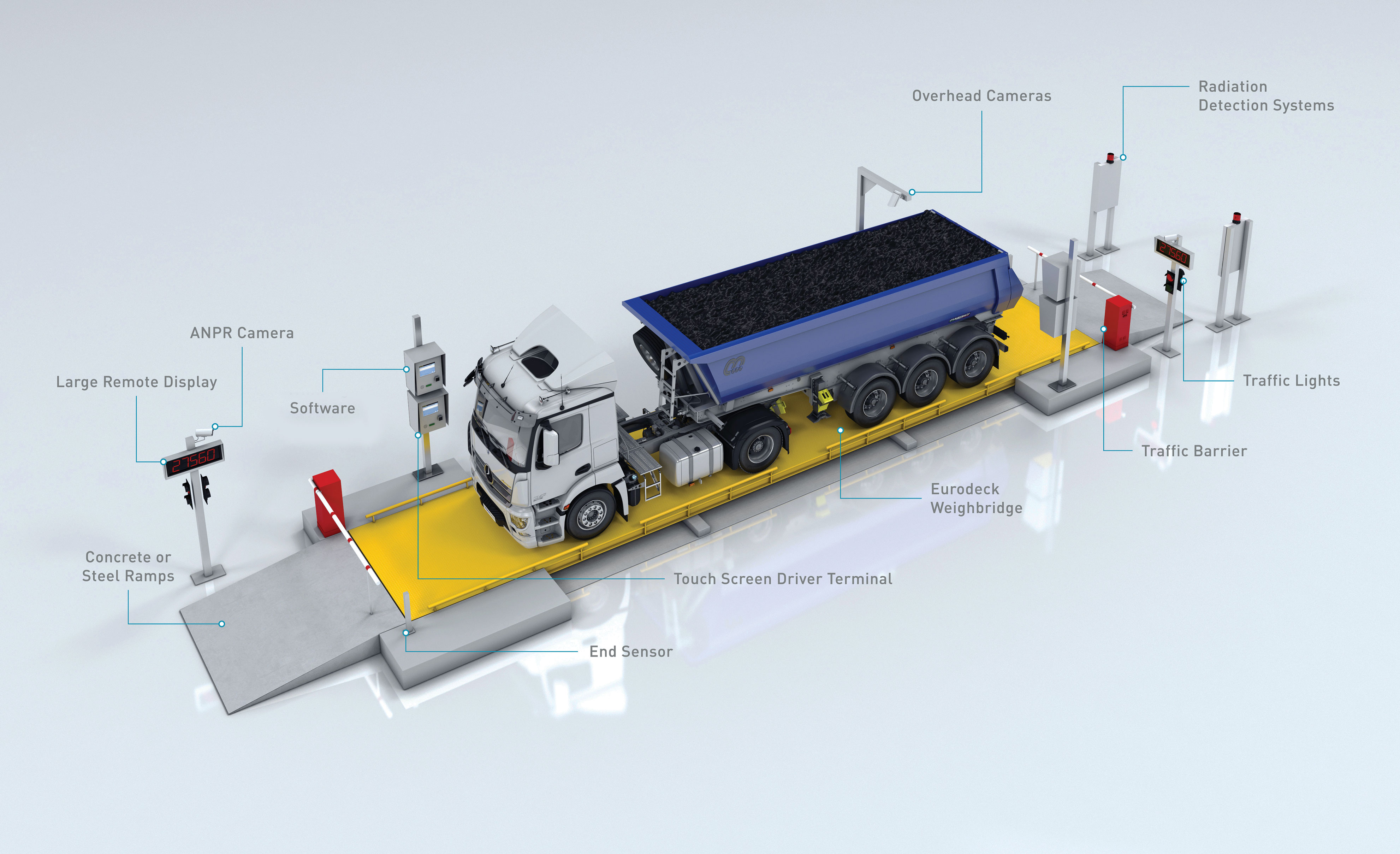
First published in the February 2022 issue of Quarry Management
Understanding advanced weighbridge technologies
By Nick Burley, sales director, Weightron Bilanciai Ltd
Automated weighbridge systems are now used in a growing number of quarrying applications and the range of technologies used in these has increased over the past decade. It is important to note that so-called automated weighbridges legally require physical intervention by the driver to ensure they are classified as non-automatic weighing instruments (NAWIs).
A key part of these systems is automatic vehicle recognition, typically using either radio frequency identification (RFID) or automatic number plate recognition (ANPR) techniques. In parallel, driver-operated weighbridge terminals with versatile software and associated control equipment are removing the need for fully manned weighbridge offices. These combined, remote-entry/exit capabilities, allow controlled access for delivery and collection vehicles to specific site areas, providing advanced site security. They also speed up the weighing procedures and extend operating hours, removing the need for manned weighbridge offices in a growing number of applications.
RFID or ANPR?
The choice of system will depend on a range of factors and a comparison chart is provided (see table. 1) showing the pros and cons of each technology. In some applications, both technologies can be used alongside each other. When making a choice, it is important to understand the basics of the two technologies.
RFID
RFID refers to a technology where data are encoded digitally in the form of RFID tags and a reader is used to detect these data through radio waves. RFID is used to automatically identify and track a diverse range of people and objects. Everyday examples include personnel entry into buildings, vehicle entry to car parks, and vehicle tags used to identify and levy charges for vehicles using toll roads. RFID technology is, therefore, well suited to automated weighbridge systems. Typical working ranges vary from less than 100mm up to 7m, depending on operating frequency.
Typical RFID systems consist of three components: an RFID tag or smart card carried by the user, an RFID reader, and an antenna.
The RFID tags (or cards) contain an integrated circuit and an antenna, which are used to transmit data to the RFID reader. The tag reader interface then converts the radio waves to a digital signal that can be processed by the system computer. The system cross-references the data stored on the tag with its own database and if it matches, an applicable action can be granted. RFID technology can incorporate various frequency levels that determine the reading range. The lower the frequency, the shorter the reader’s range. In vehicle identification, the most common frequencies used are 125kHz (short range) and 860–980MHz (long range).
ANPR
An ANPR camera automatically captures the vehicle license plate in real time, compares it with a pre-defined list and triggers appropriate actions such as opening a gate or barrier. ANPR technology has advanced significantly over the past decade and the latest cameras are easy to install and can provide up to 97% reading efficiency, even under poor operating conditions (earlier cameras relied on outdated FTP technology to analyse data from the camera and were susceptible to false readings).
The system software uses multiple images to take into account plate orientation and skew to mitigate errors and crosscheck for accuracy. To read the licence plate information, the ANPR adjusts the brightness and contrast of the image so the optical character recognition (OCR) or pattern recognition can easily identify the letters and numbers. This information is converted to text data and sent to a central database where it can be compared with stored vehicle details.
Although the layout of automated weighbridge systems varies from one installation to another, there are four common types of operation:
ANPR only
Induction loops in front of the weighbridge can be used to detect the presence of the vehicle as it drives on to the weighbridge. The loops may control traffic lights and/or barriers if they are installed.
To initiate the weighing process the driver must press a button on the driver terminal. If the captured registration of the vehicle is stored in the database, the weighing can then take place. If not, the driver either has to fill out the relevant information on the screen or is prompted to contact the weighbridge office via the integral intercom. The vehicle is not usually allowed to leave the weighbridge until the weighing has been completed successfully.
ANPR and short-range RFID
The overall weighing process is as above. In this case, the ANPR is used to identify the vehicle, whilst the RFID tag usually identifies the driver. The latter may include details of any required site induction training undertaken or other relevant information, together with the validity. The reader can either be separate or incorporated in the driver terminal.
Short-range RFID only
The RFID tag is typically used to identify the details of the vehicle but can also identify the driver.
Long-range RFID only
This application uses a long-range RFID key fob. As the vehicle approaches the weighbridge, the driver presses the fob’s button which then sends a code to the associated antenna. This identifies the vehicle and once stationary on the weighbridge, the weighing is carried out. Typically, traffic lights control entry/exit to the weighbridge. Such systems are well suited to weighing off-road vehicles where their design makes it difficult for the driver to interact with a weighing terminal without getting out of the vehicle.
Driver-operated weighbridge terminals
These versatile instruments are proving to be invaluable at busy or remote sites, speeding up the weighing process and extending operating hours. Interlinked terminals can also be used to control non-weighed vehicles entering or leaving site via dedicated control points or bypass lanes.
The latest terminals provide drivers with a clear and easy-to-use touch-control interface, accessible directly from their cab. Where required, dual-height arrangements can be installed to accommodate different vehicle designs. The on-screen prompts take the driver through the weighing process and the use of pictograms can further facilitate ease of use. At the end of the weighing process, drivers can be provided with a printout of the weighing data. Intercoms fitted to the terminals allow direct communication between drivers and site-based or remote personnel if issues arise.
Such driver-operated systems can also be part of a wider vehicle-management system to ensure smooth vehicle flow, starting when vehicles arrive at site, through to loading or unloading, and finally to vehicle departure. Large LED screens can be linked into the system to provide drivers with key instructions and information.
The future
Versatile and effective software is a vital part of driver-operated weighbridge systems, bringing together overall functionality and interfacing directly with wider site-operational software. This ‘local’ software can now be linked to cloud-based software, which offers two distinct advantages to the operator.
First, it can act as a versatile back-office management tool, providing operators with remote, real-time information relating to key site data, including weighings taking place, materials delivered, and vehicle movement. The users can view and download a wide range of reports and, depending on the permissions set, share certain data with third-party contractors. This visibility can be useful to highlight potential bottlenecks, especially at busy times, allowing rapid changes to be made based on live information from site. Secondly, such cloud systems can act as effective remote maintenance tools.
This technology is set to revolutionize weighbridge support by allowing engineers to view individual weighbridge performance remotely in real time. With such a system installed, engineers can log in to view the performance of a weighbridge, showing them comprehensive site data including the exact location of the weighbridge, details of load-cells and instruments, together with clear and detailed graphs of weighbridge usage, deadload readings, and loading patterns. The system will immediately flag up any system malfunction via its comprehensive alarm functionality.
This real-time vision allows rapid response to site issues and ensures that engineers know what the problem is before they arrive, thereby ensuring minimum downtime for the operator. Such detailed information can also help establish optimized service patterns for individual weighbridges.
For more information, visit: www.weightron.com
- Subscribe to Quarry Management, the monthly journal for the mineral products industry, to read articles before they appear on Agg-Net.com