Tunnelling Into The Future
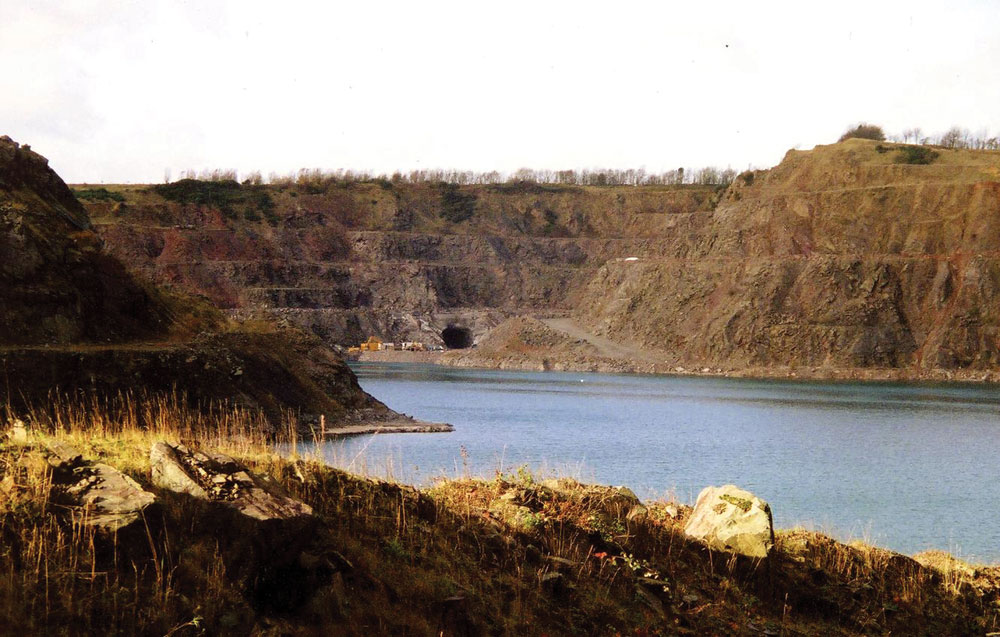
Major tunnel project gives Old Cliffe Hill Quarry new lease of life
With rock extraction at Midland Quarry Products’ New Cliffe Hill Quarry now entering its final phase, work is currently well under way on the construction of a tunnel that, later this year, will link the site with neighbouring Old Cliffe Hill Quarry in order to release previously sterilized reserves of granite. Marking the latest phase in a long-term plan for the development of the two sites as a cohesive, single operating centre, the resumption of extraction at the former quarry will ensure the continuing supply of high-quality aggregates and safeguard the livelihoods of many directly and indirectly employed workers in and around north-west Leicestershire.
In 1983, when planning permission was first granted for the development of New Cliffe Hill Quarry in an area known as Stud Farm, some 2km west of Old Cliffe Hill, a 50m wide ‘corridor’ of land was allocated through which the two quarries would eventually be linked, thereby obviating the need to transport primary crushed material via public roads. This corridor passes just north of the village of Stanton under Bardon, which is located on a narrow isthmus of land that separates the two quarries.
The quarry link itself was originally to have been made by means of an overland conveyor and bridge, but this method was subsequently revised in favour of a tunnel, part of which was to be constructed using a cut-and-cover technique. However, owing to concerns over possible disruption to the northern end of Stanton under Bardon, this proposal was further revised and, after consultation with the quarry liaison committee and a public exhibition in Stanton Village Hall, a scheme involving an underground tunnel located entirely within the granite bedrock was put forward.
Offering a much more environmentally friendly solution with no visual disturbance and less noise and dust, and with blasting no closer than previously approved, permission for this wholly underground link was granted by Leicestershire County Council in March 2002. Following a subsequent competitive tendering process, tunnelling specialists Thyssen Technical Services Ltd were awarded the contract to construct the tunnel.
Preparatory work on the project involved surveying the tunnel’s line and position, and the drilling of exploratory boreholes at a number of points along this line to confirm the depth of the granite rock head. Survey accuracy was extremely important, as the tunnel’s course does not follow the centre line of the permitted corridor but must remain within its boundaries. S.V. Modelling were contracted to carry out control surveys using GPS technology to check the traverse and to fix baseline co-ordinates.
At the same time, pumping began at Old Cliffe Hill to remove 1.7 million m3 of accumulated water from the void. This is being discharged into a local reservoir and is due to be completed in June 2003. The reduction in the water level is being closely monitored by both MQP and The Environment Agency to ensure that there are no adverse affects on local watercourses during this dewatering process.
Construction of the tunnel itself commenced in mid-August 2002 with initial operations centred on the creation of the tunnel portal at Old Cliffe Hill. This involved stabilizing the face by removing up to 5m of loose, blast-damaged rock left over from former quarrying activity, followed by the pouring of a 10m x 10m x 1m concrete slab on the bench immediately above the entrance. The granite mass forming the roof of the portal was then ‘tied’ to this support slab using 128 8m long tie bars, with further reinforcement achieved through the application of layers of mesh and fibre-reinforced shotcrete. With a stable portal position established, tunnel blasting at Old Cliffe Hill commenced in mid-September.
Meanwhile, at New Cliffe Hill the design change to a wholly underground tunnel resulted in a delay to the planned October start date for tunnelling operations, as additional preparatory work was necessary to get the quarry faces into the required position. At this site, modern smooth-blasting techniques were used to develop a safer, more stable face at the portal position, which was established in December 2002. Tunnel driving from the New Cliffe Hill side began in early January this year.
At the time of writing [March] the tunnel had advanced 230m from the Old Cliffe Hill entrance and 40m on the New Cliffe Hill side, with no unexpected rock conditions encountered so far. On both sides an initial rate of advance of around 7m a week was achieved until the tunnel entered competent, fully stressed rock, at which point the rate of advance was increased to 25–30m a week.
When completed later this year, the 9m wide by 6m high tunnel will extend a total of 714m from end to end, running more or less horizontal for almost two-thirds of its length. However, owing to a 25m difference in the elevation of the two tunnel entrances, the Old Cliffe Hill side will descend at a gradient of 1 in 10 for a distance of 250m before levelling out. This profile will maintain an adequate rock head of at least 8m of solid granite above the roof of the tunnel, on top of which lies up to 30m of Keuper Marl.
At the outset, planning consent for the project permitted tunnelling operations between the hours 7am and 7pm from Monday to Friday, however this was later extended to bring the tunnelling work into line with quarrying activities at the site (ie 6am to 10pm, including Saturdays), with the undertaking that any work carried out during the extra hours would be conducted within the tunnel itself. The exception to this is blasting, which can only be carried out between 10am and 6pm.
The tunnelling work is being carried out by two teams of five (three miners, one electrician and a mechanical engineer) under the supervision of a site engineer from Thyssen and a resident engineer from MQP, with a Cornish-based team working the Old Cliffe Hill side and team from Byrnecut (a division of Thyssen Australia) engaged on the New Cliffe Hill side.
The safety of the two mining teams is paramount, with all those working on the project having to undergo full site induction and strict assessment procedures. Moreover, every task carried out on site requires a full risk assessment and method statement, and all drilling, blasting and bolting operations are recorded in detail, signed off by the operative involved and logged for future reference. Thyssen and MQP are aiming to maintain their current ‘zero’ lost-time incident record throughout the duration of the project, and to this end have adopted a ‘no blame’ culture to encourage the reporting of any incidents.
Driving the tunnel through the granite bedrock is a cyclical four-stage process involving: drilling and blasting; debris clearance; cleaning and scaling; and drilling and bolting. All drilling operations in the tunnel are performed by an Atlas Copco L2C Twin Rocket Boomer — a 23-tonne, computer-controlled, diesel–electric underground drilling machine equipped with two independent drilling arms and an integral hydraulic service platform.
Full face blasting is carried out using packaged Dynaroc explosives with Pentaflex 100 and Nonel LP detonators, all supplied by Exchem. Each round consists of 128 blastholes measuring 43mm in diameter and up to 4m in length. The permitted vibration level allows a maximum peak particle velocity of 6mm/s at the nearest property, which, at the closest approach, is 94m from the tunnel line. Exchem have hired seismographs to assist Thyssen and MQP with continuous vibration analysis. Each trace is examined prior to designing the subsequent round, with control of vibration achieved by fine-tuning the maximum instantaneous charge on any individual delay period detonator in the round, and by adjusting the loading rate of the explosives in each of the holes.
The Cliffe Hill quarry blasting sub-committee, comprising one MQP employee, one representative from Leicestershire County Council and three residents of Stanton under Bardon, meets every six weeks to deal with issues relating to both quarry and tunnel blasting operations, with the aim of minimizing any impacts on the local community.
After each blast, once the area has been inspected and declared safe, a Cat 988F wheel loader is used to check and scale the face and to clear away the debris pile; the material extracted from the New Cliffe Hill side is being sent for processing and sale, while the spoil from the Old Cliffe Hill side is being stockpiled for processing at a later date once the new primary crusher is in place. When the tunnel face is clear of debris a Cat M312 wheeled excavator equipped with a hydraulic breaker attachment is used to scale the roof and sides of the tunnel in preparation for bolting and stabilization work.
To date, the tunnel has encountered mainly competent, fully stressed rock conditions and, as a result, bolting is largely being carried out in accordance with Support Classification A, with a row of 12 holes being drilled in an arc across the sides/roof of the tunnel, into which 4m long x 37mm diameter, full-column, resin-bonded bolts are inserted and secured. Subsequent rows of bolts are spaced 1.5m apart, but where rock conditions dictate an intermediate row of 2m long bolts and/or occasional spot-bolting is used, with the addition of shotcrete if necessary.
When complete the tunnel will provide an environmentally acceptable route for the transportation of primary crushed material from Old Cliffe Hill Quarry to the existing processing plant at New Cliffe Hill. As part of the development plan for the combined operation, some 360,000m3 of overburden has been cleared from the area of the former processing plant at Old Cliffe Hill — releasing a substantial tonnage of previously sterilized reserves — and a new 2,500 tonnes/h, semi-mobile primary crusher is due to be installed at the site in the near future. Primary crushed material from this plant will be delivered to New Cliffe Hill by a 1.6m wide field conveyor system which will travel along one side of the new tunnel. The remaining 6.5m of tunnel width will accommodate a single-lane, traffic-light-controlled roadway for dumptrucks carrying overburden to New Cliffe Hill for use in ongoing restoration works.
Completion of the tunnel and further developments at Cliffe Hill will be covered in a future issue of Quarry Management.
Acknowledgement
The editor wishes to thank Midland Quarry Products for permission to visit the site and, in particular, Ian Conway, company engineering manager, Chris Oldroyd, resident engineer, John McMurdo, Thyssen’s site engineer, and Phil Robinson of Exchem for their help in preparing this article.