Manor Farm Quarry Comes On Stream
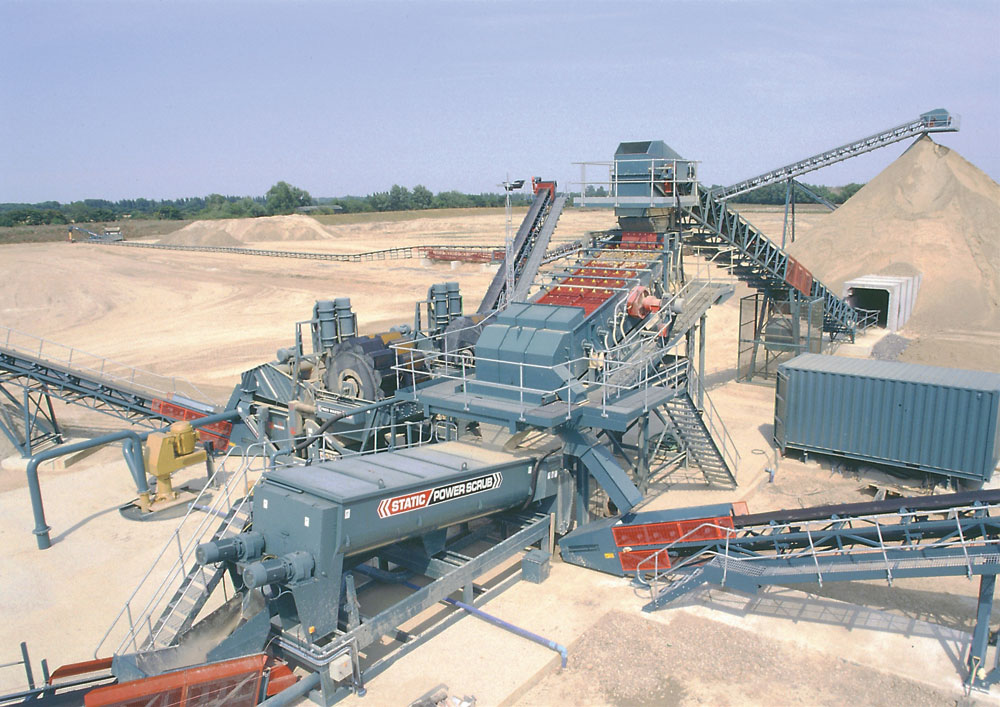
Bardon Aggregates ensure continuity of supply in the Cotswolds
Manor Farm Quarry, one of Aggregate Industries’ newest greenfield sand and gravel operations, commenced production at the end of June 2003 with the primary aim of ensuring continuity of aggregates supply in and around the Cotswold region. Operated by Bardon Aggregates, the aggregates and asphalt business of Aggregate Industries, the quarry is located between the villages of Kempsford and Whelford on the Gloucestershire–Wiltshire border, just a stone’s throw from RAF Fairford, and has been developed to replace the depleted reserves at the company’s Cleveland Farm Quarry near Ashton Keynes.
Land for the Manor Farm site was acquired as far back as November 1989 and planning permission for the extraction of 2.7 million tonnes of sand and gravel over a six-and-a-half-year period was granted in August 1992. The permission was subject to a number of conditions including engineering and surfacing work on Washpool Lane — the quarry’s main access road — and a Section 106 agreement covering further improvement works to surrounding public roads.
In addition, the site’s close proximity to the main armaments compound at RAF Fairford called for a number of other extraordinary safeguards over and above the more customary planning provisions. Following consultation with the Ministry of Defence, an inner ‘blast zone’ extending over a distance of 400m from the ammunition bunker was designated, within which the installation of any buildings used for the ‘congregation of staff’ is not permitted, a safety measure which necessitated a change in the planned location of the quarry’s office, weighbridge, workshop and welfare facilities.
Also, in response to the RAF’s concerns over the possibility of birdstrikes, the quarry will be worked dry to minimize the amount of standing water and hence reduce the site’s attraction to waterfowl. With the water table lying just below ground surface, this involves perpetual pumping and the licensed discharge of around 7,000m3 of water a day from a newly created perimeter drainage ditch into the local Dudgrove brook.
With extraction operations at Cleveland Farm winding up and due to enter their final phase this summer, the construction of the processing plant at Manor Farm Quarry was originally scheduled to commence in September 2002, however a pre-commencement condition specifying a detailed archaeological investigation of the site unearthed findings that led to a four-month delay. As a result, construction of the new 300 tonnes/h processing plant finally got under way in January 2003, with Powerscreen Washing Systems taking on the role of principal contractor and main equipment supplier for the project.
Because of the height of the water table and the consequent likelihood of seasonal flooding, initial development work at the site focused on raising the road, plant and office area by 0.5m using as-dug material from the construction of silt lagoons.
The deposit at Manor Farm comprises a relatively clean and consistent sequence of oolitic sand and gravel which averages 3.5–4.0m in thickness. This rests on top of the Oxford Clay and is in turn covered by a thin veneer (around 30cm) of overburden. Grain sizes within the deposit generally average less than 28mm and the new plant is designed to produce six final products ranging from fine building sand to +20mm oversize.
At the working face a new Cat 980G wheel loader extracts the sand and gravel and feeds it into a Powerscreen Powertrack 1400 vibrating scalping/feeder unit. Located close to the face, this fully mobile, track-mounted machine removes any large lumps of clay or oversize and in turn feeds on to a 200m long field conveyor designed to accept up to 400 tonnes/h of –100mm raw material. Powered by a 45kW drive unit, this 750mm wide conveyor is fitted with Cannoflex EP500/3 heavy-duty belting and features a heavy-duty tail-end loading section and a 9m long hand-winch-type loop take-up unit. Another field conveyor will be linked to this belt at a later date as extraction advances.
The field conveyor, in common with all other conveyors at the site, was supplied by Canning Conveyor and is powered by a high-efficiency drive unit from Brook Crompton. It features a galvanised walkway along one side and around the head drum, together with a full-length emergency stop pull-wire from Davis Derby and guarding in accordance with both Bardon Aggregates’ specifications and current legislation. Mato scrapers are used throughout, and close-pitched rubber-covered impact idlers are fitted at all loading and transfer points.
As the field conveyor approaches the processing area it discharges on to a 750mm wide x 45m long stockpiling conveyor. Powered by a 30kW drive unit, this belt elevates the material and discharges it to a conical ground stockpile of around 7,500 tonnes total capacity.
Material is recovered from the stockpile via a 46m long reclaim tunnel constructed from 23 reinforced cast-concrete segments (2.5m square section) supplied by Tarmac Precast and installed by Wildgoose Engineering. This tunnel is somewhat unusual in that it passes through the entire stockpile, providing access from both ends. In addition, a slight gradient from one end of the tunnel to the other improves natural drainage and greatly assists in the hosing out of any spillages from the 750mm wide x 60m long reclaim/main feed conveyor.
This conveyor is charged by two twin unbalanced motor Skako vibratory feeders each designed to deliver up to 200 tonnes/h, making them more than capable of meeting the processing plant’s consistent feed requirement of 300 tonnes/h. Once clear of the reclaim tunnel, the conveyor climbs at an angle of 18º to feed the plant’s primary screen some 9m above ground level.
The primary screen, which was supplied and installed by Finedoor, comprises a 6.1m x 2.1m twin-deck vibrating unit with a full-length rinsing system. The screen is equipped with polyurethane modular screen decks from SCS and features a rolling chute arrangement and all-round galvanized walkway for ease of access.
All +20mm oversize rejected by the top deck of the screen is delivered to an adjacent ground stockpile via a 12m static conveyor, while the –20mm +5mm fraction passing the top deck is discharged into a Powerscreen Powerscrub 120R log-washer. The –5mm water/sand/silt underflow passing the lower deck is fed directly to a pair of Powerscreen Fines Master 120 sand-classification units which operate in tandem.
Capable of producing up to 120 tonnes/h of contaminant-free sand and gravel, the Powerscrub 120R unit comprises an inclined trough fitted with two counter-rotating axles with high-tensile exchangeable blades and an elevated spray-bar system. The unit mixes incoming feed while milling and washing the material at the same time. Any lumps of earth or clay are broken down during this process and carried away in the wash water, while any lighter particles are floated off through specially designed outflow exits. Two spray bars are mounted at the discharge end of the unit to give the –20mm +5mm product a final rinse before being fed on to a 30m transfer conveyor for delivery to the final screen.
To improve performance and serviceability, the lower bearings on the Powerscrub 120R are fresh-water flushed to prevent wear from small particles, while all bearings feature remote greasing. In addition, the machine’s rounded-hull trough design reduces water consumption and minimizes any material build-up within the trough. The unit is also fitted with a walkway and steps to one side of the machine to facilitate maintenance and access.
The final screen, which is identical to the primary screen except that it is fitted with a partial rinsing system, splits the –20mm +5mm into three final single-size products: 10mm, 14mm and 20mm. The two larger sizes are delivered to their respective ground stockpiles by 24m long static stockpiling conveyors, while the 10mm product is discharged to a larger capacity stockpile via a 24m long, electrically powered radial stockpiler fitted with a chevron belt.
To minimize sand losses from the plant, the overflow from the Powerscrub 120R and the water/fines underflow from the final part-rinser screen is sent via pipework to a ground sump and then by Warman pump to the sand plant where it joins the –5mm underflow from the primary screen.
Working in tandem for maximum sand grade flexibility, the two Fines Master 120s produce a combined total of around 200 tonnes/h of concrete sand and building sand. Each machine comprises a twin bucket wheel, a centrifugal slurry pump, twin hydrocyclones, a collection tank and a high-frequency 12ft x 5ft dewatering screen mounted on a single carrier chassis to produce up to two grades of product. At Manor Farm, one of the machines is dedicated to coarse sand production, while the other can be configured to produce both fine and coarse sand in varying proportions according to changes in demand.
The concrete sand produced is delivered to stockpile via a 12m collection/transfer conveyor and a 24m long, electrically powered radial stockpiler, while the building sand is delivered to a smaller stockpile by a 12m static conveyor. Water containing –75µ fines removed from the sand products by the two Fines Master units is pumped to the site’s silt lagoon system via a ground sump and Warman foul-water pump for subsequent recirculation and reuse.
The remaining plant infrastructure at Manor Farm is centred around the site’s fully surfaced one-way system and comprises a brand new Hippowash wheel wash facility from CDM Steels, a second-hand weighbridge from Weightron Bilanciai, and a ‘rapid-construct’ workshop facility supplied by Kitpac Buildings, together with separate office and welfare/mess cabins for the quarry’s eight staff.
The entire plant is PLC controlled, via a system of soft start/stop drives, from a containerized control room located adjacent to the processing plant, with 415V, 3-phase mains electricity supplied via a transformer unit located next to the control room. The control room also houses the controls and displays for three Siemens Milltronics belt scales which are fitted to the plant’s reclaim/main feed conveyor, concrete sand stockpile conveyor and transfer conveyor to the final screen. All electrical installation work at the site was carried out by QES.
Operating from 7.00am to 5.00pm Monday to Friday, and from 7.00am to 11.00am for sales only on Saturdays, one of the quarry’s biggest customers is Aggregate Industries’ own Bradstone reconstituted stone business in and around the Cotswold Water Park, while various ready-mixed concrete plants operating throughout the Cotswold/Swindon region take a large proportion of the remainder of the plant’s output.
Final restoration at Manor Farm Quarry will be to agriculture utilizing a mix of backfilling to existing levels using silt and clay from the extraction process, together with low-level restoration for the remainder of the site. Low-level restoration will be achieved using the underlying Oxford Clay to create a sealed drainage basin which will be surcharged with site-generated subsoils and topsoils. A small pumping facility will be required to remove excessive rainfall from this basin. The final restoration will also enhance the existing footpath network to the benefit of local residents.
Acknowledgement
The editor would like to thank Aggregate Industries for permission to visit the site and, in particular, Peter Restorick, Wessex engineer, and Peter Mole, quarries manager, for their help in preparing this article.