Bardon Choose Benninghoven
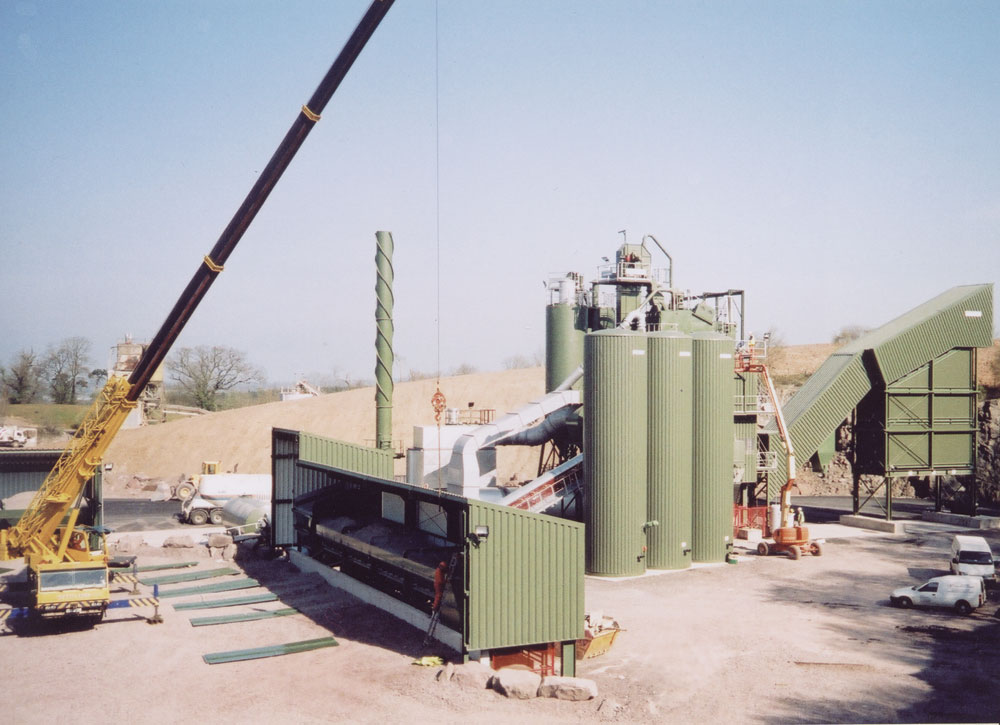
Versatile new plant serves the West Midlands and Welsh Borders region
Haughmond Hill Quarry, which was acquired by Aggregate Industries in 2000, provides a valuable source of high-quality stone for the West Midlands and Welsh Borders region. It is one of just two West Midlands quarries that can provide greywacke with a polished stone value (PSV) of 65. This meets the high-PSV requirements needed for the production of high-performance, low-noise asphalts, which are now the staple highway surfacing materials for Highways Agency and local authority roads.
Bardon Aggregates’ Haughmond Hill asphalt plant, which was commissioned during March 2002, has also been designed to accept and recycle asphalt road planings in line with national and local authority environmental policy. The facility can mix waste asphalt material with bitumen and primary aggregate from Haughmond Hill to produce high-performance materials suitable for all levels of road construction and maintenance.
The location of Haughmond Hill Quarry and the new asphalt plant, close to the end of the M54, is ideally linked to the motorway network and Bardon Aggregates’ other high-PSV stone quarries at Cribarth in central Wales and Cwm Nant Lleici near Swansea.
‘We are now very well positioned to provide high-performance asphalts and highway surfacing services across the West Midlands and Welsh Borders region,’ said Bardon Aggregates’ Midlands operations manager, Dave Lewis.
This has recently been demonstrated, as Bardon Aggregates have secured the asphalt order from Bardon Contracting to supply the Hodnet by-pass project for Alfred McAlpine.
The new Haughmond Hill asphalt plant features 10 cold-feed hoppers, each of 15m3 capacity and each fitted with a frequency- controlled belt feeder for accurate blending of the aggregates. The hoppers were supplied in two banks of five, with one bank situated at right angles to the collecting and inclined conveyor which feeds the reversible slinger conveyor to the dryer. Three of the bins are fitted with vibrators to assist material flow, and both sets of feed hoppers are sheeted on their sides, ends and roofs to help keep the raw materials dry.
The dryer drum, which is 9m long x 2.4m in diameter, is lagged with 70mm thick Rockwool insulation and aluminium clad for heat retention and noise attenuation. The drum is friction driven by all four support rollers through individual 18.5kW geared motor units, thereby eliminating chain noise. The discharge chute is equipped with an infrared pyrometer to control burner settings and material temperature.
The burner comprises a Benninghoven Rax-Jet Turbo, a well proven unit which is able to burn both gas oil and waste oil. This is equipped with a full range of safety devices and delivers high-efficiency fuel usage. A separate waste-oil heating and pumping station was supplied in addition to a gas-oil pumping station.
The plant’s dust-collection system is adequately sized for the dryer unit and mixing section scavenging. It is rated at 58,000Nm3/h and achieves emission levels of less than 25mg/m3. A skimmer unit mounted above the dryer separates any coarse dust, which passes to the hot-stone elevator feed boot via a gravity flap valve and chute, while the fine dust collected in the bag house is fed to a 60m3 reclaimed filler silo by means of a vertical eleva-tor. Any excess dust is processed through a dust-conditioner prior to disposal. An imported filler silo of 60m3 capacity was also supplied.
Hot aggregates are transported from the dryer to the screen by a vertical hot-stone elevator. This is totally enclosed and features a twin-strand chain, wear-resistant steel buckets and replaceable liner plates at impact points. Elevator drive is provided by a 22kW geared motor unit at the elevator head. This is equipped with a backstop facility.
Material from the elevator passes to a six-deck screen which features a by-pass facility and twin-shaft drive via two 15kW motors and V-belts. The drive units are mounted outside the screen housing to allow high-temperature screening.
The hot-storage section has a total capacity of 80 tonnes and comprises six bins, plus the by-pass. The bins are insulated and clad and each has a continuous level indicator and overflow chute. Discharge from each bin is via a pneumatically operated radial door which accurately regulates material flow to the aggregate weigh hopper, from where the aggregates are discharged directly to the mixer.
Separate bitumen and filler weigh hoppers are provided at the mixing level. Bitumen is injected into the mixer from the weigh kettle by a high-pressure injection pump for rapid, homogeneous coating of the aggregates, while filler is introduced by a screw conveyor from the filler weigh hopper.
Mixing takes place in an insulated 3,000kg capacity twin-shaft mixer unit, with drive provided by two 37kW geared motor units through synchronized gears at opposite ends to ensure a rapid but thorough mixing cycle. To reduce noise and provide the plant with a pleasing aesthetic appearance, the mixing section is sheeted in coloured, coated profile sheeting from the screen level down to the discharge level.
The mixed material passes to a 3,000kg capacity inclined skip (retractable to allow direct truck loading) which is driven by a 55kW fre-quency controlled winch. The skip delivers the material to one of three hot-storage bins which provide a total mixed-material storage capacity of 200 tonnes (a 6-tonne capacity foul-batch hopper is also included). All three bins are mounted on load-cells to ensure accurate loading, and each bin is lagged and clad for heat retention and equipped with an electrically heated cone and discharge door. The entire unit, including the skip track, is sheeted with the same colour profile sheeting as the mixing tower.
Bitumen is stored in three of Benninghoven’s latest-design, high-efficiency, electrically heated vertical bitumen tanks, each of 80m3 capacity, one of which is equipped with a stirrer mechanism for polymer bitumen. The tanks were supplied together with all associated pumps, valves and electric trace-heated and lagged pipework.
A gravimetric additive system is also incorporated within the plant to feed either granulate material from a 30m3 silo or pigment pellets from a 3m3 silo. Each batch of pigment or granulate is accurately weighed in a load-cell-mounted weigh hopper prior to dispatch to the mixer.
In addition, an asphalt planings recycling system has been incorporated in the facility to deliver precise percentages of RAP directly into the mixer. The system comprises a steep-sided, 15m3 capacity feed hopper with an oversize grid and vibrator. A 4kW inclined belt feeder mounted under the feed hopper delivers the RAP on to a 30m long inclined delivery conveyor equipped with a belt weighing system. This in turn delivers the material on to a stainless steel-lined chute which directs the material into the mixer. An automatic vent duct at the mixer allows rapid extraction of steam during recycling operations.
The entire plant is controlled by a Benninghoven On-Line Batcher 2002 computer system with a touch-screen monitor, housed in an air-conditioned and heated control cabin. The system is modem linked and provides storage for up to 1,000 asphalt recipes.