Turning C&D Waste into Clean Sand and Aggregate
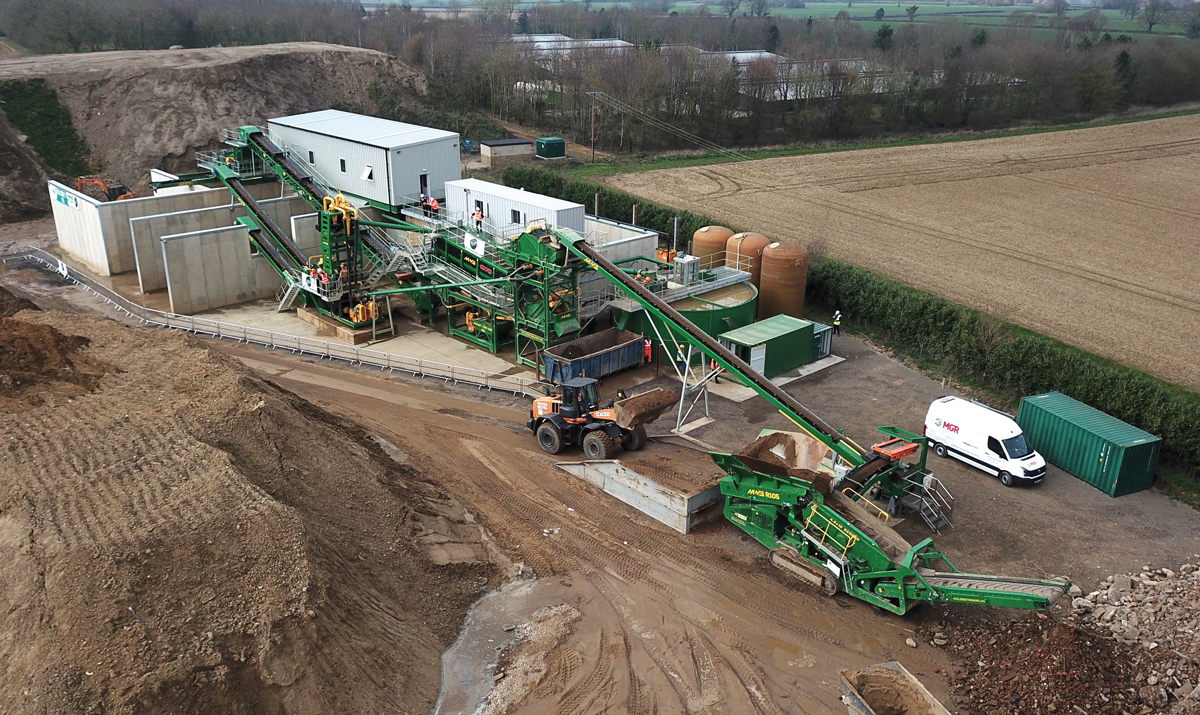
First published in the July 2019 issue of Quarry Management as A Perfect Storm
Monk Plant Hire (MPH) are using a McCloskey modular washing system to turn C&D waste into clean sand and aggregate. Dan Gilkes went along to MHP’s site in Hockering, Norfolk, to find out more.
The first McCloskey modular washing system built around the company’s AggStorm 150 system has gone to work in Norfolk, for plant hire, demolition and recycling company MPH Group. First seen at last year’s Hillhead exhibition in Buxton, the washing system is built from a range of proven McCloskey components to provide a sorting and washing system for sand and aggregate that is being produced from construction and demolition waste.
The installation, to the north of Norwich, has been three years in planning, as MPH proprietor Mark Monk worked closely with the team at McCloskey and their UK dealer Max Innovate to design and perfect the plant. The result, commissioned in December 2018, is an impressive system capable of handling up to 120 tonnes/h of waste and producing more than 1,100 tonnes of clean aggregate and sand per day.
‘We went to McCloskey after researching the whole marketplace. They were new to the industry and their design was way ahead. I spent three years going all over Europe looking at the market and this is exactly what I wanted,’ said Mr Monk.
At a total cost of around £2.5 million, one would certainly hope that MPH are happy with the installation, which has been situated at the firm’s recycling centre in Hockering. It replaces separate crushing, screening and washing machinery, bringing everything into a single, highly productive system.
Construction and demolition waste from the surrounding area is brought in by truck and stockpiled on site. The material is then fed into a McCloskey R105 dual-power scalping screen, to separate oversize material for further crushing. Overband magnets remove any metals and the remaining material is fed by conveyor into a 12ft x 5ft linear pre-screen, where it is rinsed with high-pressure water to remove sand.
From there, the remaining material is fed into a log-washer, where it is further scrubbed by water running at around 2-bar pressure. The log-washer has two counter-rotating log shafts that are timed to overlap their paddles for maximum scrubbing action. The AggStorm system is currently available in three sizes, offering 80-tonne, 150-tonne and 200-tonne capacities, with MPH opting for the mid-range 150 model.
The AggStorm log-washer is different to many competitors in having large access panels built into the sides of the log-wash box. This makes it easy to access the paddles for repair and replacement, if required.
Light materials and trash are removed and dewatered using an 8ft x 4ft linear dewatering screen, with the scrubbed aggregate moving on to a separate 8ft x 4ft linear dewatering screen. Sand and silt are collected and pumped, using a slurry pump, to a holding tank, while the washed aggregates are transferred to a sizing screen and split into three products, before being conveyed to concrete storage bays.
MPH are producing 10mm, 20mm and 40mm aggregate products. In addition, two sand products are processed through a Compact Sand Plant 120 and conveyed to purpose-built storage bays.
Water is in fairly short supply at the Norfolk site, so recycling and re-use was a priority. McCloskey and Max Innovate called in specialist water-treatment company Fraccaroli & Balzan, to design a water-treatment plant as part of the overall system. This involves a 9m diameter circular tank that has a slowly revolving paddle system. Into this tank the company pumps small quantities of flocculent, from a floc station built at the side of the plant, which attaches to the silt and helps it to clump and drop to the bottom of the holding tank.
From here, the silt is transferred to a filter press. This has 152 filter plates, each measuring around 1,500mm by 1,500mm in size, that are hydraulically pulled together to squeeze the water from the silt. Once dried, the waste product drops from the bottom of the filter press. This waste product is being marketed to local farmers as a soil enhancer.
A robowasher cleans between the press plates after each compression. The plant has been so successful in recycling water, that it only takes around 50m3 of new water per week from the local supply to top up the tanks.
The whole project was brought together by McCloskey Washing System’s Coventry-based UK dealer, Max Innovate. It has proven highly effective and MPH report that they can sell all of the aggregate that they can currently produce, back to the local construction sector. Indeed, Mr Monk is so pleased with the installation that he is already planning a second, identical washing plant at another site within the area.
‘We’ve now ordered a second one, for 2020, to be built 30 miles from here,’ he said. ‘It’s exactly the same as this one. I see the geographical potential to serve a 30-mile radius with each of these plants.’
- Subscribe to Quarry Management, the monthly journal for the mineral products industry, to read articles before they appear on Agg-Net.com