Powerscreen Unveil New Machines at Hillhead 2018
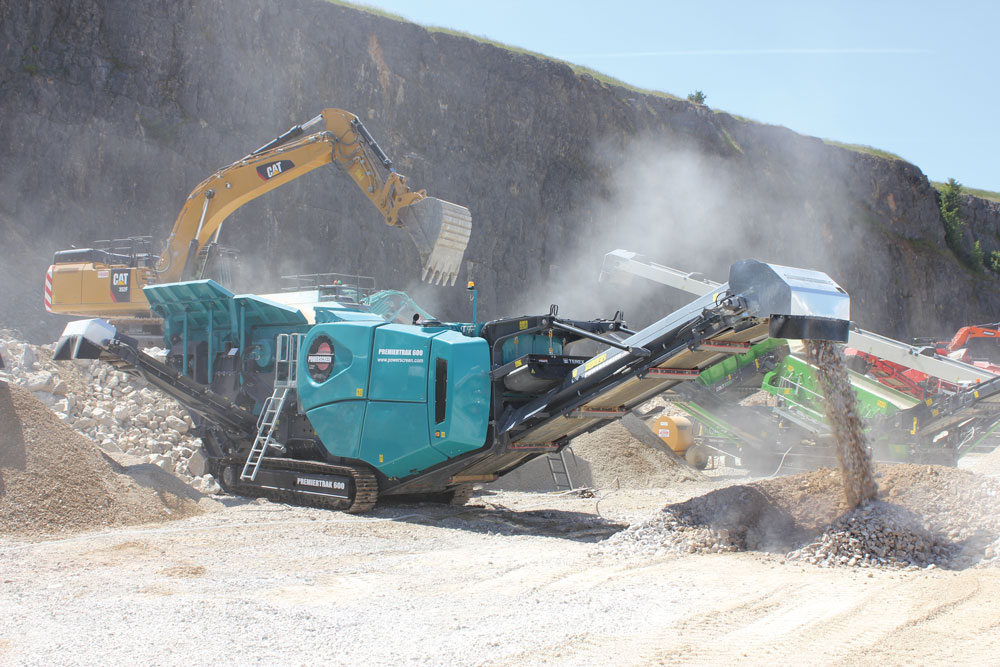
First published in the September 2018 issue of Quarry Management as Pure Power
Powerscreen unveiled their latest mobile crushing equipment and technological innovations at Hillhead 2018
Powerscreen celebrated another successful year at Hillhead 2018 by launching a number of new products, including the Powerscreen Premiertrak 600 and Metrotrak jaw crushers, as well as a ‘never seen before’ working demonstration of the Trakpactor 550SR impactor.
Commenting on the biennial show, Dearbhaile Mulholland, marketing manager for Powerscreen, said: ‘Hillhead is always an exciting show for us and this one was no different. We successfully showcased our newest developments and demonstrated how we are looking to the future and being more forward-thinking with our technological innovations.’
The Premiertrak 600 jaw crusher features a unique XL feeder designed for maximum strength, particularly for large quarrying applications where hard rock may be present or large tonnages are required. The diesel-hydraulic and diesel-electric variants of the Premiertrak 600 jaw crusher help deliver maximum production and performance with increased uptime and lower running costs.
The high-capacity jaw is fed by a vibrating grizzly feeder with variable speed control and a large grizzly area to maximize the removal of fine material, extending the wear life of the jaw plates within the crusher chamber. The bypass chute is fitted with wear-resistant liners as standard and incorporates an adjustable five-position deflector plate to divert material to either the product conveyor or side conveyors.
The machine controls incorporate a modern state-of-the-art interface with intuitive graphics and high-resolution display for ease of operation. There is an automatic start/stop and diagnostic and machine adjustment capability. For optimum performance, the speed of the jaw crusher on the Premiertrak 600 can be varied to suit the application and feed materials.
The Premiertrak 600E electric variant is equipped with an oversize genset designed to run another plant, such as the larger Powerscreen Warrior 1400XE heavy-duty scalping screen. The 600E jaw crusher itself can also be powered from a mains source, reducing running costs and environmental impact.
With convenience and safety in mind, the Premiertrak 600 can be fully set up from ground level, thanks to its hydraulic folding and locking hopper system. It can also be adjusted to maximize productivity in any application and configured with an independent pre-screen for the efficient removal of scalped materials either into waste or sub-base materials.
The new Powerscreen Trakpactor 550SR horizontal-shaft impactor crusher has been designed for processing primary and secondary materials such as natural rock and construction-derived materials, including asphalt and demolition waste.
Offering low-cost-per-tonne productivity, the machine’s robust impact chamber features a four-bar rotor, twin-apron design with hydraulic release aprons, adjustment assist and hydraulic overload protection.
The Trakpactor 550SR is also equipped with GRP guards and Powerscreen’s Pulse intelligent remote-monitoring system as standard. The machine has also been designed with ease of maintenance in mind. Hydraulic banks, battery access and control valves are easily accessible, while the post-screen and recirculation section is fully detachable using quick-release hydraulics and electrics.
Building on the success of its predecessor, the new Powerscreen Metrotrak is a high-performance mobile jaw crushing plant ideally suited for operators in the quarrying, mining and recycling industries. In particular, the machine is suitable for those operating on urban sites where working and transport space are restricted, thanks to its small footprint.
A compact and aggressive tracked jaw crusher, the Metrotrak has been redesigned with the operator in mind, therefore ease of use, serviceability/maintenance and material flow are all major factors in the design of the machine.
Other features include a variable-speed vibrating grizzly feeder (VGF) with bolt-in stepped grizzly cassettes and a rotating mesh deck. The jaw crusher is also equipped with a larger three-way bypass conveyor, which is easy to set up, inspect and maintain.
Another upgraded component is the product belt conveyor. Relocated belt tensioning bolts help keep the belt tracked, clearance under the chamber has been increased and operators can now fully lower the conveyor to ground level for maintenance and service tasks, whilst revised skirting helps eliminate snagging points, thereby improving material flow.
One of the key features of the Metrotrak unit is the chamber unblock feature, which, with the aid of a motor attached to the flywheel on the chamber, will ‘rock’ the chamber back and forth until blockages are cleared.
- Subscribe to Quarry Management, the monthly journal for the mineral products industry, to read articles before they appear on Agg-Net.com