Modern Gravel Works For A Difficult Deposit
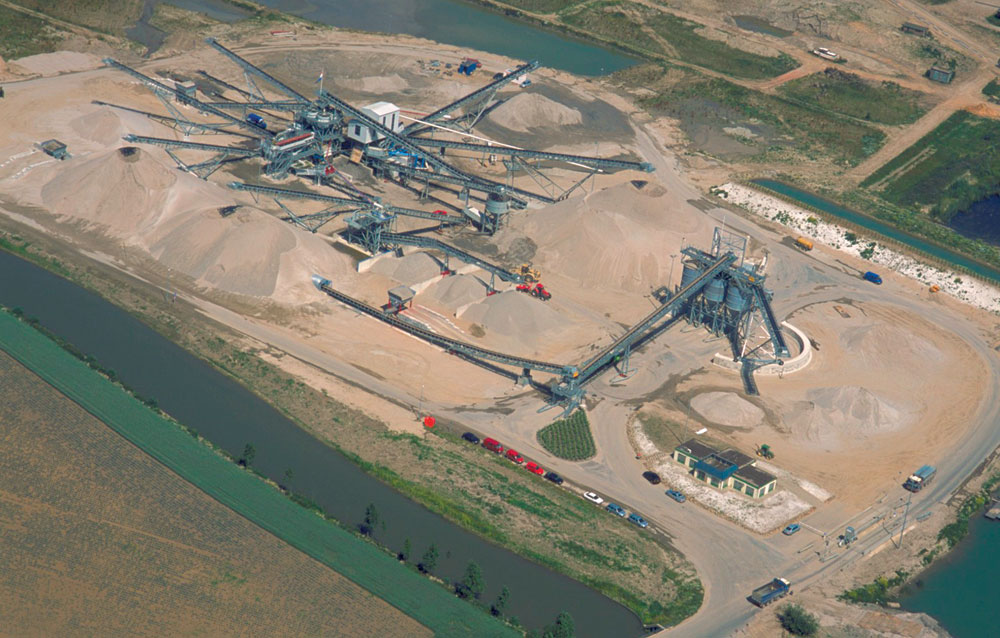
German company Bräuer Aufbereitungsmaschinen GmbH & Co. Förderanlagen KG have recently constructed a modern sand and gravel plant between Nijmegen and Rotterdam, Holland. In designing the new plant, provision had to be made for both the fluctuating flow rates from the raw material dredging operation and the varying composition and particle size distribution of the raw material itself. In addition, fine sand losses had to be minimized. The plant was commissioned two years ago and to date is said to have demonstrated impressive performance in the production of high-quality sands and gravels
In April 2000 Bräuer Aufbereitungsmaschinen GmbH & Co. Förderanlagen KG were awarded a contract by the Dutch company Zem K3 for the design and construction of a brand new sand and gravel processing plant to be located adjacent to the A15 road near Echteld, between Nijmegen and Rotterdam. After a five-month construction period, the plant commenced operations in March 2001.
The gravel mixture fed to the plant is extracted from the Lingemeer area by suction dredger at a rate of 2,000–2,500m3/h. In its raw state the material is highly impure, containing both organic matter and a high proportion of very fine particles (loam and clay), as well as displaying wide variations in particle size distribution. Using an appropriate design and layout, the new processing plant had to make provision for the variations in the throughput of the suction dredgers and the heterogeneous particle size distribution of the raw material, while producing high-quality finished products with no loss of fine sands greater than 60µ in size.
To ensure a uniform feed to the processing plant, generously sized surge storage units were set up between the scalping and washing station and the processing plant. With this balancing of the material flow, the extraction operation and the processing plant can be run independently of each other.
The plant’s scalping and washing station was also designed to allow for peaks in the delivery of raw material from the extraction operation. Although the average feed rate is 950 tonnes/h, the plant is capable of handling up to 1,600 tonnes/h depending on the particle size distribution of the raw feed.
Following turbulence reduction in a dead-box arrangement, all +32mm material is removed from the solids/water mixture by the upper deck of an 8.0m x 2.7m Bräuer scalping screen and sent by chute to an oversize stockpile. The lower deck of this screen sizes at 3mm, with material in the range –32mm +3mm being fed to a Bräuer twin-shaft log-washer where it is pre-scrubbed prior to delivery to a buffer silo with an overflow facility.
The solids/water underflow from the scalping screen (maximum 150 tonnes/h) is dewatered in an Eagle Iron twin-shaft sand screw, with the sand sent by belt conveyor to a 0–3mm raw sand buffer stockpile.
During dewatering, a large proportion of fine sand in the size range 0–1mm is removed from the raw sand and discharged, together with large quantities of organic components and waste water, in the screw overflow. The organic components are removed by means of a Bräuer fibre screen and delivered to a storage bay for subsequent removal, while the 0–1mm underflow from the screen is dewatered in a Bräuer fine-sand bucket wheel, with the sand product being sent to a series of ground stockpiles via a slewing conveyor.
Meanwhile, all fine sand greater than 60µ in size contained in the overflow from the fine-sand bucket wheel (around 2,500m3/h) is recovered by means of two Bräuer lamella thickeners. A pair of solids pumps are then used to deliver this sand to a multicyclone plant which discharges on to a Bräuer dewatering screen. The 60–250µ material which is dewatered in this way is delivered to stockpile by an inclined belt conveyor.
From the –32mm +3mm buffer silo mentioned earlier, pre-scrubbed gravel is discharged by a metering belt at a rate of 80 tonnes/h and fed to a second Bräuer twin-shaft log-washer where it is cleaned before being sent to a jig unit which removes any lighter organic components.
The clean gravel is then separated and graded on a Bräuer screen equipped with water sprays and the three fractions produced (–32mm +16mm, –16mm +8mm and –8mm +3mm) are conveyed to stockpiles. The screen underflow is fed, with the help of a solids pump, to an Eagle Iron sand classifier and used as washing water.
Raw sand in the size range 0–3mm is drawn from the base of the buffer stockpile by a series of three belt feeders and fed by conveyor at a rate of 450 tonnes/h to four Bräuer Astro 3000 dense-medium separators with special nozzle plates. To avoid problems caused by the presence of foreign bodies in the feed, a protective screen is arranged at the feed inlet of each separator, while within the Astro 3000 separators any remaining organic components are removed from the sand, which is then discharged into the Eagle Iron sand classifier where it is separated into two controlled grades.
These two grades are dewatered in a pair of Eagle Iron sand screws and then sent via slewing conveyors to 0–2mm and 0–3mm ground stockpiles respectively. During the classification process, an uncontrolled fine sand is also produced, which is sent, with the help of a solids pump, to the fine-sand bucket wheel and then added to the 0–1 mm fine sand stockpiles.
To remove deleterious particles from the fine sand, material in the size range 0–1mm (or alternatively 0–0.25mm) is sent via a feed hopper with a metering belt to two further Bräuer Astro 3000 dense-medium separators with special nozzle plates. As before, a protective screen is arranged ahead of the separators. In the dense-medium separators, the sand is cleaned (maximum feed rate 100 tonnes/h) and any organic components are removed, after which the material is dewatered in a second Bräuer fine-sand bucket wheel and stockpiled by means of a slewing conveyor.
The concrete sand is loaded at a rate of up to 800 tonnes/h via a recovery tunnel and metering system located under the 0–2mm and 0–3mm sand product stockpiles. Two feed hoppers with metering belts also feed on to the main loading conveyor to allow the fine sand and gravel sizes to be loaded or blended too. However, a change-over flap can also be adjusted to send the final products to a shuttle conveyor mounted above three 200m3 capacity storage/loading silos, below which are three loading lanes for delivery vehicles. Alternatively, sand blends or winter stocks can be delivered to ground stockpiles via a slewing conveyor.
A freshwater basin with an independent water supply forms an integral part of the new plant, and a series of freshwater pumps are installed on a fixed frame above the water level. For supply to the plant there are two pumps with a flow rate of 350m3/h and one with a flow rate of 700m3/h. Another pump with a flow rate of 350m3/h is installed solely for plant cleaning purposes. In addition, all intake pipes can be automatically filled by a separate submersible pump when necessary.
The entire plant is operated and controlled by means of a PLC control panel, with the help of a PC-based visualization system in the main office building. All monitors for the gravel works, the control of lorry loading and the Eagle sand classifier are housed in this building, and only one operative is required to control the entire sand and gravel plant and loading operations.
Bräuer Aufbereitungsmaschinen GmbH & Co. Förderanlagen KG; Goethestrasse 11; D-64625 Bensheim; Germany; tel: +49 62 51-70 97-0; fax: +49 62 51-70 9719; email: post@braeuer-gmbh.de; website: www.braeuer-gmbh.de