Investing In Hope
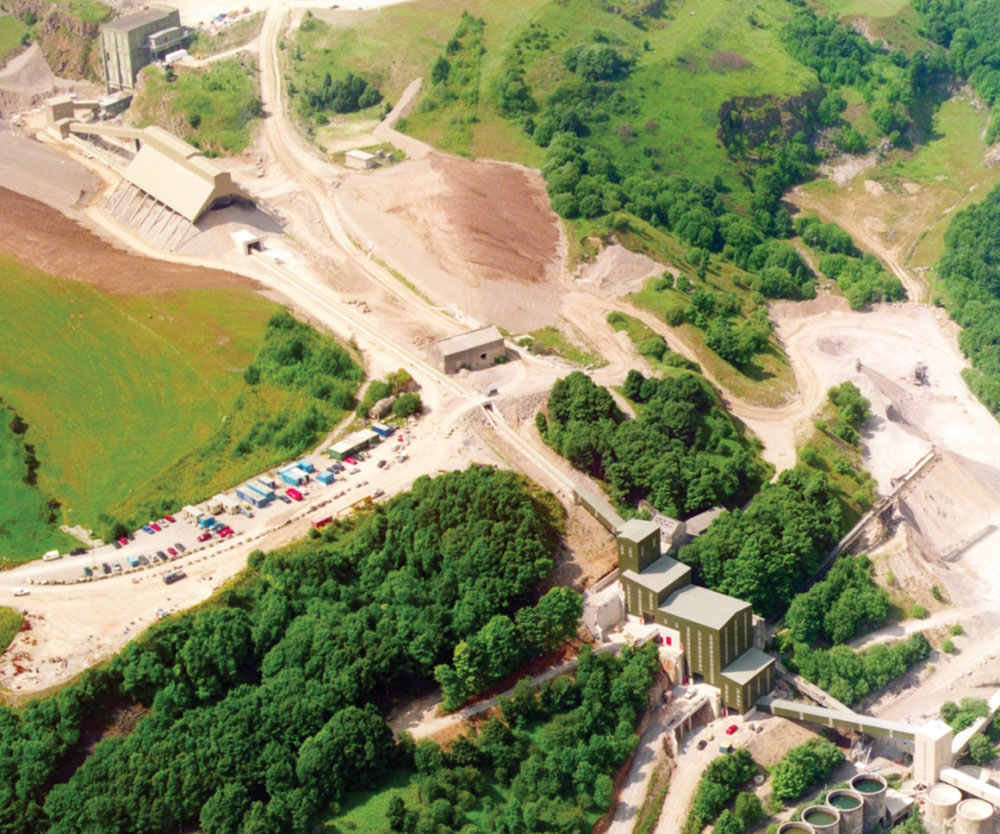
Quarry upgrade and primary crusher improvements boost production and increase cost-efficiency for Lafarge Cement
Lafarge Cement UK (formerly Blue Circle Cement UK) have invested substantially in measures to increase production and cost-efficiency at their cement works in the Hope Valley, Derbyshire. The work was conducted as part of a wider programme of plant improvements at three of the company’s core works: Cauldon, Dunbar and Hope. Fairport Engineering Ltd were successful in being awarded two elements of this investment programme — the Hope Quarry upgrade and the Hope Quarry primary crusher improvements.
Limestone for cement production at Hope is sourced from a quarry located at the top of an adjacent hill, some 75m above the level of the cement works. The quarry produces two types of stone (high silica and low silica) which are used in approximately equal quantities. The two types are quarried at different times during the week and are handled and stored separately, although a small amount of cross-contamination is unimportant. The limestone has a bulk density of 1.5–1.7 tonnes/m3.
The original limestone-handling installation at Hope conveyed primary crushed stone from the primary crusher house at the quarry level, through secondary crushers on the hillside, down to the cement works level where it passed through tertiary crushers, before eventually being deposited in a covered crushed-stone store.
At the primary crusher house the existing installation dated back to the 1950s. The improvements required necessitated stripping out the original equipment and installing a new fabricated-steel receiving hopper; a 2.5m wide by 9.5m long free-issue vibrating screen feeder; new chutework, steelwork and flooring; a dust-suppression system; lighting, cabling and CCTV; a hydraulic pick; and an acoustic control room. All of this work, including the stripping out of the old and installation of the new, had to be carried out and the new plant brought into operation within a four-week shutdown period.
The upgrade was designed to increase the throughput capacity of the material-handling plant to an average of 1,000 tonnes/h, and to provide a buffer facility by constructing a stockpile for primary crushed stone.
All the upgraded equipment had to be installed, tested and commissioned with material prior to changeover from the original installation to the new installation. This changeover had to be completed within a three-week kiln shutdown.
An alternative tender
The tender enquiry set out Blue Circle's requirement for the conveyor from the primary crusher building to feed to a transfer house and from there to a primary stockpile comprising two fall-out towers, giving a total capacity of 20,000 tonnes, some 8,000 tonnes of which was to be live capacity. Fairport’s tender expressed concerns that the fall-out towers would not permit free flow of the crushed limestone, particularly in the absence of any weather protection; that they would provide only half the required gravity reclaim capacity; and that they would not provide any dust control. As an alternative, Fairport proposed a steel-framed and clad stockpile canopy, with stone fed on to the stockpile by a shuttle conveyor and drawn off the stockpile into a reclaim tunnel conveyor via six variable-speed vibrating feeders. The design included the facility to run stone on to the stockpile, or to by-pass the stockpile and run straight from the primary crusher, through the reclaim tunnel direct to the new secondary/tertiary crusher building, as required by Blue Circle. This proposal was accepted by the company.
Detailed process route
As described above, a belt conveyor carries the primary crushed stone from the primary crusher building to a transfer house. A bunker in the transfer house has an overspill chute that feeds a belt conveyor which carries the stone up to the shuttle conveyor in the penthouse of the primary crushed-stone stockpile canopy. The shuttle conveyor allows the stone to be deposited at either the high-silica or low-silica end of the stockpile.
Meanwhile, a vibrating feeder mounted on the bottom of the transfer house bunker can feed the stone on to another belt conveyor which runs at ground level, through the reclaim tunnel under the primary stockpile, then through a cutting and finally along a gantry before discharging into a 140-tonne bunker in the new secondary/tertiary crusher building located on the hillside.
Six vibrating feeders are mounted in the roof of the reclaim tunnel. These can be selected to draw stone off the stockpile and feed on to this conveyor.
The primary crushed stone is drawn from the 140-tonne bunker in two process streams, each fed by a variable-speed vibrating feeder. Each stream comprises a free-issue Svedala secondary crusher, a conveyor feeding a free-issue Svedala screen, the oversize material dropping via a chute into a receiving hopper above a free-issue Svedala tertiary crusher, which in turn feeds on to a conveyor that discharges into a Y chute. At this point both streams combine before leaving the building.
The secondary/tertiary crusher building is located on a hillside which slopes at approximately 45°. Although this created some problems during construction, the final installation is extremely impressive visually.
The stone is conveyed from the secondary/tertiary crusher building to a new transfer house, which was built around and over an existing transfer house and eventually replaced it entirely once the shutdown changeover had been completed.
This transfer house allows a portion of the stone to be diverted, via a fixed-speed vibrating feeder, to the minor added-constituent (MAC) system. The transfer house also houses a sampler system that draws off stone samples for size and chemical analysis.
The majority of the stone, however, transfers on to an existing conveyor that was widened as part of the upgrading work, and is fed into an existing stone store building via a new shuttle conveyor. This conveyor allows the segregation of high- and low-silica stone to be maintained by depositing the material at opposite ends of the building as appropriate.
Fairport Engineering Ltd say that to deliver a project such as this on time and to a high quality, a number of key issues have to be addressed in a detailed and specific manner, and these need to be harmonized into an overall contract strategy that will, even at the pre-contract award stage, convince the client of the company’s ability to achieve the contract objectives in the most appropriate manner for all concerned. To this end, for the Hope project Fairport Engineering Ltd established a dedicated task-force team that was matrix-managed by an appointed contract manager. This team worked closely with the corresponding Blue Circle team to address and jointly resolve all issues arising.
The end result was the completion of a multi-million-pound contract to the satisfaction of the client — in terms of equipment performance, operation and quality of construction — and within the required timescale.