Hybrid first for KSD Recycled Aggregates
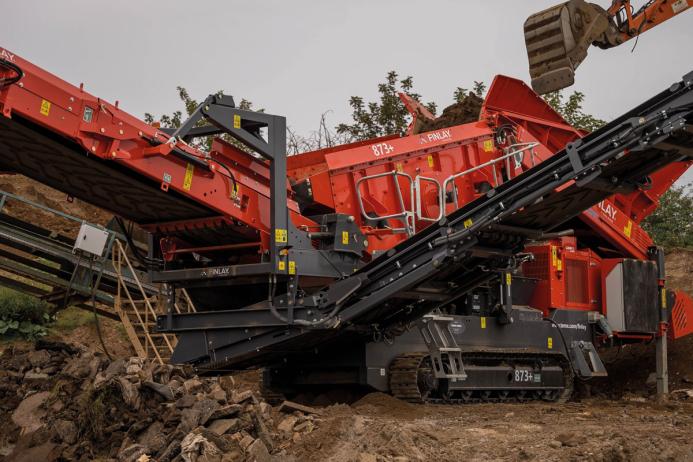
First published in the August 2024 issue of Quarry Management
Midlands recycling firm boosts throughput with new Terex Finlay 873+ Hybrid screener
Ideally situated adjacent to the M42 in the West Midlands, KSD Recycled Aggregates, were formed by Paul Dosanjh more than 45 years ago. Initially supplying virgin material from quarries across the Midlands, the company purchased its own quarry to become one of the Midlands’ leading suppliers of recycled material throughout the last 30 years.
Quick to respond to the changing nature of the industry, Mr Dosanjh purchased KSD’s current base, the huge former Dunton Island Quarry, where he proceeded to recycle the vast quantities of material tipped there to ‘landscape’ the old workings.
‘At the time the quarry shut, the legislation for tipping material wasn’t as strict as it has become,’ explained KSD operations and sales manager Phil Redden. ‘Paul seized the chance to process all of the deposited waste material that had been tipped over the previous years when the quarry was in operation, that he could through one of the very first crushing/screening and washing plants and make the investment in the quarry worthwhile resulting in the first large scale recycled aggregates processing facilities within the Midlands area.’
As the company grew and subsequently invested in further additions to its recycling plant, including a large state-of-the-art washing system, it quickly became apparent that the requirement for virgin aggregates was secondary to that of high-quality recycled material.
With a desire to now become the leading recycled aggregates supplier in the region, Mr Dosanjh and his team set about getting their material tested and certified along with improving their production and processing plants.
A long association with the Terex Finlay brand has seen KSD operate a wide range of crushing and screening equipment from the leading Irish manufacturer. This has recently been bolstered with the addition of a new Finlay 873+ Hybrid screener as their front-line machine for processing incoming material.
While site clearance works is still KSD’s bread-and-butter work, the past few years have seen a huge increase in material coming in from service works across the region. Working closely with their traditional clients for muck-shifting work and contractors undertaking the work on repairing and installing gas, water, electric and fibre services, KSD now receive more than 300,000 tonnes of mixed material per annum with over 1,200 tonnes a day being put through the new Finlay screener.
‘We are currently achieving a 95% recycling rate on all materials entering the site,’ explained Mr Dosanjh. ‘Depending on the quality of the material, we can simply put it through the Finlay before it heads for the wash plant. We carefully select and take out the clay where we can as this just slows down the entire screening and washing process.’
Supplied by the Molson Group, the UK’s sole Finlay equipment dealer, the 873+ is a first for KSD, as it is a hybrid machine capable of running from its own diesel engine or being plugged into the mains, as is the case at Dunton Island. ‘We are always looking at reducing our carbon footprint wherever we can,’ explained Mr Dosanjh. ‘Our entire wash plant runs on electricity and with the ability to purchase the Finlay with the same capability, we jumped at the chance. Even with electricity prices creeping higher and higher, we still believe we are in a favourable position with the hybrid machine compared with a stand-alone diesel version.
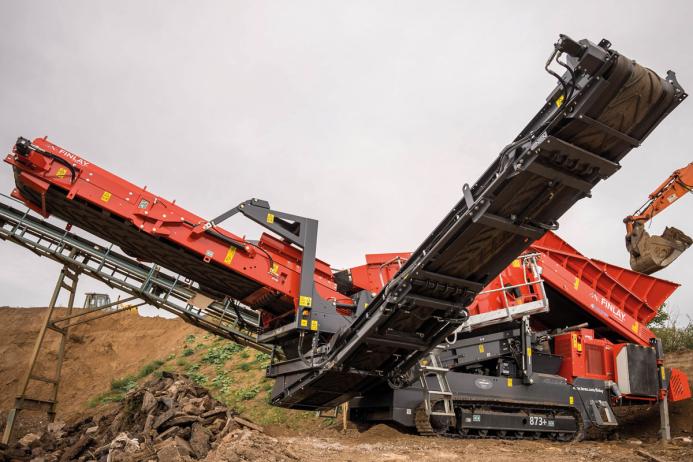
The 873+ is one of eight heavy-duty screeners in the Finlay line-up. With operating weights ranging from 18 tonnes to 48 tonnes, the 873+ weighs in at just under 26 tonnes. Designed as a high-capacity and versatile heavy-duty screener to work with a variety of material, at full speed and with the right material being fed in, the plant has the capacity to process at a rate of up to 450 tonnes/h. Wanting a well-screened, clean material from the mixed material being fed in, the 873+ has been slowed down to produce exactly what KSD require – a variety of accurately screened products ready for the next phase of recycling.
Loaded by a 13-tonne excavator, the 873+ features a heavy-duty 7m3 hopper feeder where the material is steadily deposited. As the material leaves the hopper it drops on to the 3.66m x 1.53m top deck before feeding through to the similarly sized bottom deck, now with a banana profile and increased area to maximize the screening of fine material. A range of easily removable media is available allowing further variations on output size and grade to be processed, whilst changing the screening media has been made even easier thanks to the ability to hydraulically raise the screenbox discharge end by 500mm. The 873+ features three discharge conveyors, each long enough and high enough to allow a good stockpile of material to build up below them before requiring the attention of the site’s loading shovel.
While running the 873+ from the site’s own electrical supply allows for a more cost-effective operation, having the ability to operate under its own power means the Finlay can be utilized on other projects should it be required to do so. Aside from the material being processed, the only noise from the machine comes from the hydraulic system.

‘We looked at a range of options from leading manufacturers before deciding on the 873+ from Molson,’ commented Mr Dosanjh. ‘Having the prior experience of running the Finlay brand gave us the confidence in the build quality and reliability of the machine. We particularly liked the T-Link telematics hardware and software linked to the machine which allows us to monitor its productivity remotely. Since the screen arrived a couple of months ago, it has been a very reliable and productive tool, enabling us to increase our throughput from day one. Dealing with the team at Molson was easy from the start; they have an excellent team of knowledgeable and helpful individuals in whom we have the utmost confidence in a fruitful ongoing relationship.’
Subscribe to Quarry Management, the monthly journal for the mineral products industry, to read articles before they appear on Agg-Net.com