Telescopic Conveyor Technology
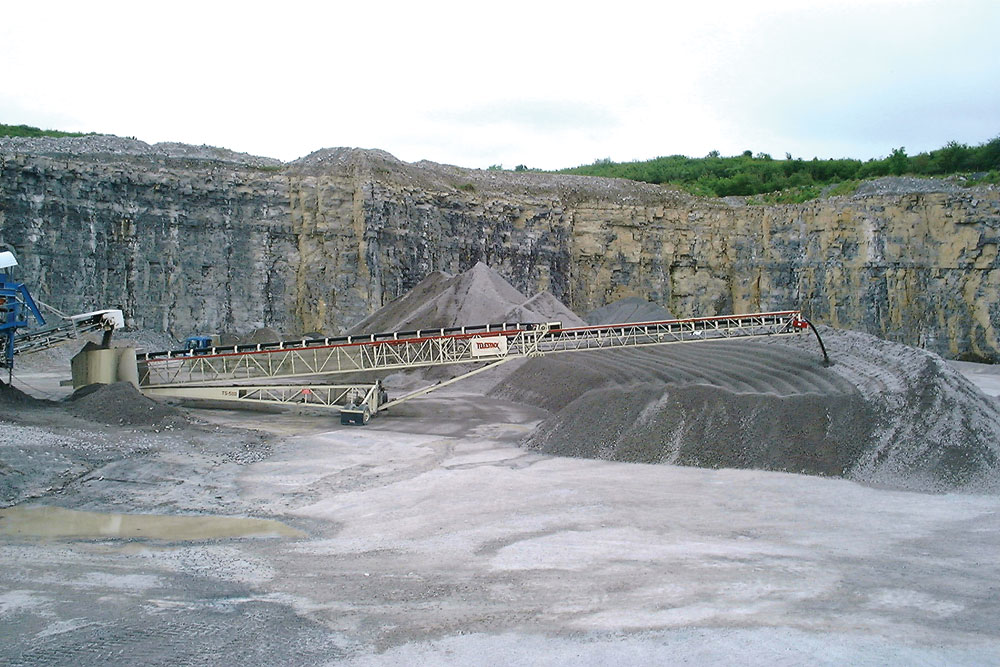
Reducing stockpile segregation and degradation
Stockpiles provide the quarry manger with flexibility between the amount of material being produced and the amount sold. They are an essential tool for effective quarry management. However, stockpiling incorrectly can cause an ‘in-specification’ material to become ‘out-of-specification’.
The use of a sub-base or unbound roadbase material containing too high a fines content may substantially reduce the load-bearing capacity of a road and lead to premature failure. Alternatively, the same material with too high a proportion of coarse aggregate will not compact. With bituminous-bound materials, especially the new proprietary thin-surface materials, it is essential to control particle-size distribution, as this is crucial to load transfer and performance.
Problems associated with stockpiling
The most common stockpiling problems are segregation, degradation and contamination. Segregation has been defined by Nohl and Domnick1 as ‘the separation of material by particle size’. Degradation is reduction in particle size by abrasion.
Segregation is caused by a number of factors in the stockpiling process. Agitation between idlers on a belt conveyor causes fines to migrate to the bottom. Differences in velocity between coarse and fine material at the discharge pulley cause the coarser particles to travel further from the conveyor and the finer particles to drop closer to the conveyor. Once the coarser particles land on the stockpile their greater momentum carries them further down the side of the pile. This is referred to as overrun and is the primary cause of segregation; it can also cause degradation by abrasion of particles moving down the side of the pile. Environmental factors such as wind can also cause segregation by changing the trajectory of fine material. When stockpiling from a static belt conveyor in strong winds there will be a much higher proportion of fines on the leeward side of the pile.
Current stockpiling techniques
Current techniques for managing or preventing stockpile segregation are often time-consuming and create additional problems. Blending of material from the stockpile can be used to reduce segregation but this places responsibility on the loader driver to maintain consistency. Building the stockpile with a wheel loader will reduce segregation, however the primary cause of stockpile degradation is trafficking by heavy plant. The repeated use of loaders and tracked vehicles on a stockpile ramp causes the larger particle sizes to break-up and compact, particularly in the wheel-paths. Loader-formed stockpiles also carry the risk of contamination with, for example, clay.
Evidence of segregation and degradation in conventional stockpiles
Particle size distributions carried out on samples from stockpiles formed by a wheel loader, static belt, and telescopic conveyor have been analysed. Figure 1 compares the particle-size distributions for samples taken from a stockpile of the same crushed material formed using:
Particle-size distributions were determined on samples of coarse aggregate taken from two loader-formed stockpiles. The first set of samples had a similar grading to Type 3 granular sub-base (NI), as defined by the Specification for Highway Works2. Figure 2 compares the grading of samples T2/T3, taken from the distinct wheel paths on the stockpile ramp, with sample T1 taken from untrafficked areas on the ramp.
Samples T2 and T3 have significantly higher fines content than sample T1. This is evidence of degradation caused by the movement of heavy plant on the stockpile.
Samples were also taken from a loader-formed stockpile of material similar in grading to Type 1 granular sub-base, as defined by the Specification for Highway Works. Samples S1, S2 and S4 were taken from areas on the stockpile ramp were the loader had formed distinct wheel paths. Samples S3 and S7 were taken from untrafficked areas on the ramp. Samples S5 and S6 were taken from the top and base, respectively, of the overrun slope. Comparing the particle-size distributions of S1, S2 and S4 with S3 and S7 shows that samples taken from the wheel paths have a finer grading than samples taken from other areas across the ramp. This is evidence of aggregate degradation caused by movement of heavy plant. Comparing samples S5 and S6 shows that S6 has a significantly coarser grading than S5. This is evidence of segregation at the top and base of the stockpile.
Telescopic conveyors
A telescopic conveyor (figure 4) greatly reduces segregation and degradation by stockpiling in a series of low-level windrows. The aggregate has an average fall height from the conveyor of 2m and is locked into channels within the stockpile. Each of these channels confines particle distribution to a very small area, thus maintaining the required mix throughout the entire stockpile. Telescopic conveyors create these windrows by utilizing their radial, telescopic and elevatory functions and automating them with an on-board PLC system. The telescopic conveyor shown in figure 4 has an output of 500 tonnes/h.
Conclusions
Sieve-analysis tests have shown that conical and wheel loader-formed stockpiles suffer from segregation and/or degradation. This has the potential to produce material with particle-size distributions which are out of specification, and thereby cause costs to be incurred due to premature failures. Stockpiles formed using telescopic conveyors have been shown to produce material of a consistent particle-size distribution throughout, saving money and time while producing a better product.
References
Stockpiles provide the quarry manger with flexibility between the amount of material being produced and the amount sold. They are an essential tool for effective quarry management. However, stockpiling incorrectly can cause an ‘in-specification’ material to become ‘out-of-specification’.
The use of a sub-base or unbound roadbase material containing too high a fines content may substantially reduce the load-bearing capacity of a road and lead to premature failure. Alternatively, the same material with too high a proportion of coarse aggregate will not compact. With bituminous-bound materials, especially the new proprietary thin-surface materials, it is essential to control particle-size distribution, as this is crucial to load transfer and performance.
Problems associated with stockpiling
The most common stockpiling problems are segregation, degradation and contamination. Segregation has been defined by Nohl and Domnick1 as ‘the separation of material by particle size’. Degradation is reduction in particle size by abrasion.
Segregation is caused by a number of factors in the stockpiling process. Agitation between idlers on a belt conveyor causes fines to migrate to the bottom. Differences in velocity between coarse and fine material at the discharge pulley cause the coarser particles to travel further from the conveyor and the finer particles to drop closer to the conveyor. Once the coarser particles land on the stockpile their greater momentum carries them further down the side of the pile. This is referred to as overrun and is the primary cause of segregation; it can also cause degradation by abrasion of particles moving down the side of the pile. Environmental factors such as wind can also cause segregation by changing the trajectory of fine material. When stockpiling from a static belt conveyor in strong winds there will be a much higher proportion of fines on the leeward side of the pile.
Current stockpiling techniques
Current techniques for managing or preventing stockpile segregation are often time-consuming and create additional problems. Blending of material from the stockpile can be used to reduce segregation but this places responsibility on the loader driver to maintain consistency. Building the stockpile with a wheel loader will reduce segregation, however the primary cause of stockpile degradation is trafficking by heavy plant. The repeated use of loaders and tracked vehicles on a stockpile ramp causes the larger particle sizes to break-up and compact, particularly in the wheel-paths. Loader-formed stockpiles also carry the risk of contamination with, for example, clay.
Evidence of segregation and degradation in conventional stockpiles
Particle size distributions carried out on samples from stockpiles formed by a wheel loader, static belt, and telescopic conveyor have been analysed. Figure 1 compares the particle-size distributions for samples taken from a stockpile of the same crushed material formed using:
- a telescopic conveyor and the windrow concept (samples 1–5)
- a conical stockpile (samples 6–8)
- directly from the telescopic conveyor belt (samples 9, 10).
Particle-size distributions were determined on samples of coarse aggregate taken from two loader-formed stockpiles. The first set of samples had a similar grading to Type 3 granular sub-base (NI), as defined by the Specification for Highway Works2. Figure 2 compares the grading of samples T2/T3, taken from the distinct wheel paths on the stockpile ramp, with sample T1 taken from untrafficked areas on the ramp.
Samples T2 and T3 have significantly higher fines content than sample T1. This is evidence of degradation caused by the movement of heavy plant on the stockpile.
Samples were also taken from a loader-formed stockpile of material similar in grading to Type 1 granular sub-base, as defined by the Specification for Highway Works. Samples S1, S2 and S4 were taken from areas on the stockpile ramp were the loader had formed distinct wheel paths. Samples S3 and S7 were taken from untrafficked areas on the ramp. Samples S5 and S6 were taken from the top and base, respectively, of the overrun slope. Comparing the particle-size distributions of S1, S2 and S4 with S3 and S7 shows that samples taken from the wheel paths have a finer grading than samples taken from other areas across the ramp. This is evidence of aggregate degradation caused by movement of heavy plant. Comparing samples S5 and S6 shows that S6 has a significantly coarser grading than S5. This is evidence of segregation at the top and base of the stockpile.
Telescopic conveyors
A telescopic conveyor (figure 4) greatly reduces segregation and degradation by stockpiling in a series of low-level windrows. The aggregate has an average fall height from the conveyor of 2m and is locked into channels within the stockpile. Each of these channels confines particle distribution to a very small area, thus maintaining the required mix throughout the entire stockpile. Telescopic conveyors create these windrows by utilizing their radial, telescopic and elevatory functions and automating them with an on-board PLC system. The telescopic conveyor shown in figure 4 has an output of 500 tonnes/h.
Conclusions
Sieve-analysis tests have shown that conical and wheel loader-formed stockpiles suffer from segregation and/or degradation. This has the potential to produce material with particle-size distributions which are out of specification, and thereby cause costs to be incurred due to premature failures. Stockpiles formed using telescopic conveyors have been shown to produce material of a consistent particle-size distribution throughout, saving money and time while producing a better product.
References
- NOHL, J.P.E., and R. DOMNICK: ‘Stockpile segregation, superior industries’, 2001, technical paper T-SU551, Morris, Minesota.
- Highways Agency (1998), ‘Specification for highway works’, vol. 1, series 800, HMSO.