Reducing the Carbon Footprint of Industrial Conveyor Belt Manufacture
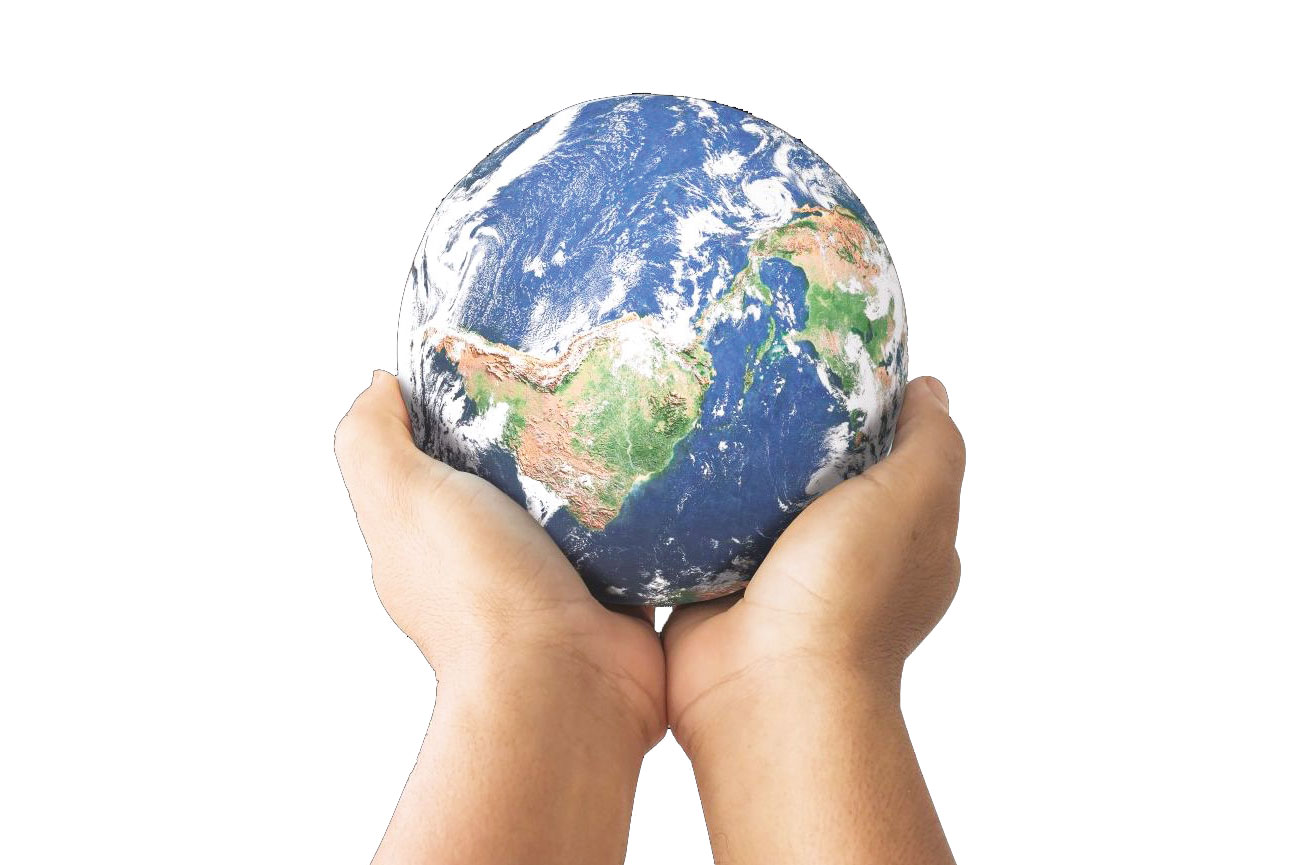
First published in the March 2022 issue of Quarry Management as The Future is in Our Hands
It is undeniable that the manufacturing of industrial conveyor belts produces a big carbon footprint. Andries Smilda, sales and marketing director with Netherlands-based Dunlop Conveyor Belting, looks at the issues facing everyone involved in the conveyor belt industry and the part we can all play in helping to prevent global warming
Never before have the environmental issues facing the world presented a greater challenge or held such a dramatically high profile. It is widely accepted that action urgently needs to be taken by the biggest industrialized nations to slow the global warming process, but what contribution can we all make personally to help prevent catastrophe?
We all have a part to play
There has been enormous media interest surrounding the United Nations COP 26 meeting held in the UK in November 2021. Hopefully, it is a sign that most world leaders are at long last starting to take seriously the threats posed by climate change to the future of our planet and our way of life. Such is the scale of the problem, however, that a concerted and genuine effort is needed, not only by world leaders, but also by every industry, company, and individual. In other words, we all have a part to play.
I passionately believe that each one of us has a responsibility to do whatever we can, not only for the benefit of the present generation, but also the generations to come. It is not for me to preach about what we do in our private lives to protect the environment. In our working lives, however, we all have varying levels of influence. I am proud to say that several years before it became ‘fashionable’ from a company image point of view, Dunlop made a conscious decision to pursue environmentally friendly strategies. This focused on three key areas: product life cycle, the environmental impact of our products, and our production processes.
PRODUCT LIFE CYCLE
There is no denying that manufacturing industrial conveyor belts uses a lot of energy and materials. Consequently, it produces a big carbon footprint. The impact on the environment caused by discarded industrial rubber belting is huge, and the problem is growing. Annual sales of conveyor belts in Europe alone are conservatively estimated to be more than €500 million. In terms of the physical volumes involved, again, very conservatively, that represents some 150,000 tonnes in weight. The amount of conveyor belting we use (and discard) represents the single biggest influence on the industry’s carbon footprint. Consequently, it also represents the single biggest opportunity where every user of conveyor belting can contribute to reducing that carbon footprint. And every little bit helps, as they say.
To fully appreciate why the length of the life cycle of rubber conveyor belts is so important it is first necessary to understand the background. Rubber constitutes at least 70% of the material mass of both multi-ply and steelcord belts. Because of its adaptability, most of the rubber used in conveyor belting is synthetic. Relatively little natural rubber (NR) is used, which is important because natural rubber production from the rubber tree (Hevea brasiliensis) is soon expected to be the leading cause of deforestation in mainland south-east Asia.
The most used types of conveyor belt are rubber ‘multi-ply’ belts, which make up around 85% of industrial conveyor belts used in Europe. This type of belt has multiple layers of polyester/nylon (EP) fabric that are used to create a sturdy carcass. This, in turn, is protected by a thick outer coating of rubber. Most multi-ply belting will have between two and four layers of fabric. This means that some 45,000km of non-biodegradable polyester and nylon fabric is being created and, ultimately, discarded every year, which is more than the circumference of the Earth.
The raw materials such as polyester/nylon fabrics and the components used to create synthetic rubber are virtually all directly or indirectly derived from crude oil. In fact, a typical conveyor belt is effectively 45% oil, and one tonne of scrap rubber will usually contain some 500 litres of oil.
In Europe, nearly 95% of all used car tyres are now recycled. By comparison, the amount of used conveyor belting being recycled is believed to be less than 10%. There are many reasons for this disparity. Recycling conveyor belts is an appreciably slower, more complicated, and expensive process. There is also much less demand for the polyester and nylon fabric inner plies and certainly no practical use for the metal cables found in steelcord reinforced belts.
No matter how much we would like it to be different, the harsh reality is that under foreseeable market circumstances, recycling industrial conveyors is not only ecologically problematic, but also not viable. This is precisely the reason why producing conveyor belts that have the longest possible working life is now more important than ever before.
Increase the life, reduce the waste
From an environmental point of view, it was a happy coincidence that, historically, Dunlop Conveyor Belting’s approach to the market has always been to supply conveyor belts that provide a much longer operational lifetime than those of their competitors. Typically, this can be double the usual lifetime, and in the case of imported belt, it can easily be three or four times longer. On this basis, the amount of belting that needs to be manufactured simply to replace worn-out belting could be reduced by up to 50%. This also means that the amount of belting that has to be discarded could also be halved. The impact this could have on the environment is truly amazing. This kind of reduction represents some 75,000 tonnes of conveyor belting that would not need to be made and transported thousands of kilometres each year. It would also mean that some 75,000 tonnes of rubber, polyester, nylon, and all the associated chemicals would not have to be disposed of, most of which would be buried in the ground.
A frightening statistic
The average modern-day container ship produces the equivalent of 16.14g of CO2 per tonne of goods shipped per kilometre. As the average distance between Asia and Europe is more than 6,000km, this means that some 100kg of CO2 is emitted into the atmosphere for every tonne of imported conveyor belt.
What can you do? The answer is to adopt a policy of buying belts that have been manufactured as physically close to your operation as possible.
If we can persuade people to buy better-quality, longer-lasting belts, albeit at a higher up-front price, instead of buying ‘economy’ low-grade belt, it will create two extremely significant benefits. Not only will it be an enormous help environmentally, but it will also reduce medium-to-long-term cost for the user due to the substantial reduction in ‘whole-life’ cost. ‘Everyone wins’, as they say.
What can you do? The answer: Base your conveyor belt purchasing policy on lowest lifetime cost.
ENVIRONMENTAL IMPACT
The second aspect that Dunlop Conveyor Belting focus on is the chemicals and ingredients used to create rubber and the lasting environmental impact that they could have on the environment, both in the short term and in the future. There are literally hundreds of different chemical components, such as anti-degradants, anti-ozonants, and accelerators. These include primary amine-based sulfenamides such as N-cyclohexyl-2-benzothiazole sulfenamide, and thiazoles such as 2-mercaptobenzothiazole. It is an inescapable fact that to make some rubber compounds, it is necessary to use chemicals that are extremely dangerous. Fortunately for us all, at least as far as Europe is concerned, control mechanisms are already in place because there are very strong regulations, in the form of REACH, designed to protect humans, wildlife, and the environment.
What is REACH?
REACH was established by members of the EU with the specific aim to improve the protection of human health and the environment through the better and earlier identification of the properties of chemical substances. REACH Regulation places direct responsibility on industry to manage the risks from chemicals and to provide safety information. Manufacturers and importers are required by law to gather information on the properties of the chemical substances they use and register the information in a central database at the European Chemicals Agency (ECHA), based in Helsinki.
The Regulation also calls for the progressive substitution of ‘substances of very high concern’ (SVHC) when suitable alternatives have been identified, which is a positive and progressive idea. What I also find positive is that REACH regulations regarding SVHC have become increasingly stringent and demanding. For example, Article 31 of REACH (requirements for safety datasheets) demands that if a product contains SVHC that is more than 0.1% of the total weight of the finished product, the manufacturer is compelled to both register its use with the ECHA and provide their customer with a safety datasheet.
Because Dunlop Conveyor Belting manufacture their own rubber and make every belt themselves, it easier for us to comply with these stipulations compared with most other belt manufacturers, because we have full control over everything that we do.
Accountability and responsibility
As far as I am aware, Dunlop Conveyor Belting were the first major manufacturer of conveyor belts to achieve REACH compliance. Sadly, many European conveyor belt manufacturers have chosen to ignore the legal requirements of REACH either completely or at least partially because of the impact on production costs.
What is most worrying is that most belts used in Europe nowadays are imported, so it is virtually impossible to know how much SVHC and POPs such belts contain. Manufacturers located outside EU member states and the UK are not subject to REACH regulations or even to EU regulation concerning the use of POPs. This means that they are free to use unregulated raw materials even though those same materials may be entirely prohibited or at least have strict usage limitations within Europe.
What can you do? The answer is to always ask for written confirmation from the manufacturer or supplier of the belt you are buying that it has been produced in compliance with REACH EC 1907/2006 regulations. It really is as simple as that.
PRODUCTION PROCESSES
As already mentioned, manufacturing industrial conveyor belts uses a lot of energy and raw materials and, therefore, produces a large carbon footprint. Having worked in the industry for more than 30 years, I cannot deny the fact that reducing the size of that carbon footprint by any significant amount in the short term will be extremely challenging, but fortunately there are things that can be done.
More efficient machinery
The production process used to manufacture rubber industrial conveyor belts has not changed fundamentally for a great many years. Consequently, much of the machinery is old and not always as energy efficient as it could be. Dunlop Conveyor Belting have invested many millions of euros, particularly during the past decade, replacing outdated machines and building new production lines using the most technically advanced equipment available. But we have had an added incentive because anything that reduces our carbon footprint by increasing efficiency also improves the overall efficiency of our business. The company’s steelcord production line is a good example of this, because it combines what were previously separate production stages into one smooth process. Apart from the product quality benefits, this also means that it uses less energy.
When less is more
The demands being placed on modern-day conveyor belts, especially those used in ‘heavy industry’ such as quarrying and mining, mean that belts must be stronger and tougher than ever before. Traditionally, this has meant making belts with multiple plies, so they are becoming increasingly heavy. Naturally, thicker, heavier conveyor belts contain a lot more rubber and fabric. There is, therefore, a parallel increase in the carbon footprint and, ultimately, an increase in potentially unrecycled waste. However, at Dunlop we believe that this upward trajectory is avoidable. In fact, we do not just believe it – we know it.
The Holy Grail?
Despite increasingly thicker, heavier belts, it is estimated that up to 80% of conveyor belts are scrapped prematurely due to damage. The challenge presented to the Dunlop R&D team, therefore, consisted of two major objectives. The first was to design a belt that was much more capable of resisting impact, ripping, and tearing, and the second, to make sure that the belt could be competitive in the market, which might well be regarded by the conveyor belt industry as the equivalent of looking for the Holy Grail. Ironically, the company’s engineers found that the answer to the pricing issue lay in the volume of raw materials needed and the complexity of the production process.
Because we had already developed extremely hard-wearing, long-lasting, rubber cover compounds, our engineers and technicians went back to the drawing board and concentrated on the carcass construction. Instead of persisting with the multiple-ply carcass construction, they created a single-ply carcass using an amazingly tough patented fabric that is exclusively made at Dunlop’s sister company’s in-house fabric-weaving facility in the US. The specially woven fabric uses crimped warp polyester yarns to provide high strength and low stretch, combined with strong ‘binder’ and ‘filler’ yarns to create strength and stability under load. The result was Dunlop Ultra X, a unique single-ply, super-strength belt that has more than three times greater longitudinal rip resistance, up to five times better tear resistance, and a far superior resistance to impact compared with traditional three- or even four-ply belting.
From a production point of view, having a single-ply construction helps to maximize efficiency because there are fewer calender runs. Another advantage is that having no rubber skim between the plies not only results in a thinner, stronger carcass that is less prone to delamination, but it also reduces the amount of rubber needed, thereby keeping the cost down. Yet another advantage was the ability to make longer production runs at maximum width, which further maximizes production efficiency and minimizes the amount of power consumed.
Single-ply conveyor belts – the way forward
At Dunlop, we sincerely believe that the development of a single-ply conveyor belt that not only significantly outperforms its thicker, heavier, multi-ply counterparts, but also has dramatically less impact in terms of its carbon footprint, is a genuine and very exciting game changer.
Although some might throw their hands up at the thought of using a single-ply belt, it should be remembered that single-ply solid-woven belting has been used in underground mines for several decades. I am not advocating single-ply belts simply because we already have a belt that can do all these things, because there is nothing to prevent other conveyor belt manufacturers from following the same path. Replacing thick, multi-ply belts with single-ply belts that are much more durable and long lasting yet use so much less energy is certainly the best way forward in every respect.
What can you do? The first step is to accept that thicker, heavier belts are not the solution for conveyors where belt damage is a problem. I recommend that you explore the possibility of using a single-ply construction belt that provides the necessary tensile strength and resistance to accidental damage. At the very least, fit conveyor belts that have been specifically engineered for purpose rather than a constant stream of low-grade ‘sacrificial’ belts. This will lead to extended operational lifetimes and consequently less waste in every respect.
In our hands
Trust me when I say that the actions I am proposing are not simply some kind of theoretical dream. To my mind, every individual and company has a responsibility to do whatever possible to prevent even more damage being done to our environment. The problems facing our planet today will become even more serious for our children and our children’s children. Their future is in our hands.
- Subscribe to Quarry Management, the monthly journal for the mineral products industry, to read articles before they appear on Agg-Net.com