Increasing Loading Zone Efficiency
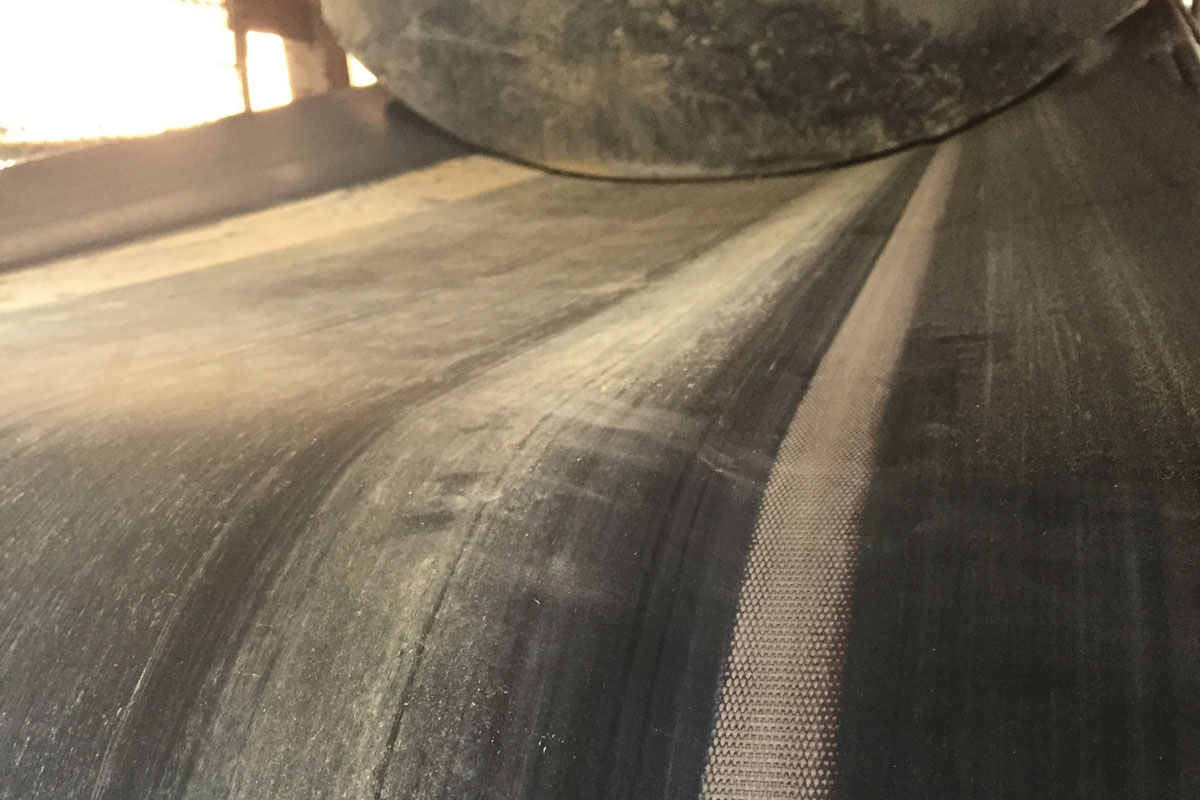
First published in the March 2022 issue of Quarry Management
Assessing your system for challenges and implementing solutions
By Nick Tiplady, head of sales, Flexco UK
When it comes to conveyor systems, sometimes no one realizes that a problem exits until everything comes to a halt and delivery deadlines are missed. That is why so many operations are turning to annual belt conveyor assessments to ensure that all their conveyor components are running smoothly and that potential problems are identified, and plans made to address them.
Whilst assessing the entire conveyor system is important, a large part of any checklist should be focused on the loading zone. The loading zone is important to the life of the rest of the conveyor and should not be ignored, as correct loading of the belt and sealing of the loading zone will help increase belt and splice life and reduce maintenance cost and effort. For those who succeed in moving their materials around without it spilling off the belt, maintenance efforts and outlay can be focused elsewhere.
This article examines a few of the common loading zone issues that may be encountered in a quarry, why they happen, and how they can be addressed before they affect production.
Issue: Belt and splice damage in the impact area
Diagnosis
Incorrect material used for sealing the impact area and the section of conveyor after the loading zone is the culprit here. Using incorrect skirting materials leads to premature wear on other components and requires additional maintenance. It is extremely common for plants to use old belting as skirting material, which can lead to belt and splice damage and require the premature replacement of both.
Solution
Instead of using old belting, consider polyurethane skirting, which has a lower durometer, thereby reducing friction and providing three to four times the wear life of traditional rubber. A lower coefficient of friction reduces strain on the system and soft durometer polyurethane offers exceptional tear resistance to ensure a good seal and long belt life.
Issue: Damage to skirting systems in the impact area, causing long maintenance delays
Diagnosis
Homemade skirt-clamping systems, as well as those made by OEMs, may be hard to adjust, requiring the unbolting/reassembling or torching/re-welding of the entire clamp bar to adjust the skirting as it wears. This requires the belt to be stopped for a longer period for maintenance. Some belts may have skirting running the full length of the conveyor, so the maintenance time required for adjustments adds up quickly when the system is not designed for easy adjustment.
Solution
An engineered skirting system that can be adjusted quickly and utilizes polyurethane skirting is the best choice for the belt. With correct installation, the polyurethane skirting will not drag on the belt causing premature wear or gouge marks in the belt cover, which can reduce belt cleaning efficiency and the life of the belt. An engineered skirting system should be designed with maintenance in mind, so look for one with safe service access.
Issue: Increased spillage and fugitive dust in the loading zone
Diagnosis
Sites may only be looking at skirting as the cause of spillage around the loading zone, as mentioned above, but the components that support the belt are also very important and need to be considered. Sometimes, an incorrect choice of loading zone support can lead to increased spillage and fugitive dust. Many quarries only use impact idlers in the loading zone, which means the skirt systems do not have a continuous flat surface to seal against, so material escapes between the idler sets. This also puts pressure on specific areas of the skirting material, wearing the spots where the belt contacts the idlers faster than the gaps between the idlers. This action breaks the continuous seal and eventually dust and material will start to escape.
Solution
Slider beds are engineered to provide containment around loading zones. In areas where low impact affects productivity, slider beds with impact idlers and adjustable idler sets with impact rolls are key. When combined with skirting systems, slider beds effectively seal the loading zone. When paired with impact beds, slider beds create a holistic loading zone.
Issue: Spillage at the loading zone and beyond
Diagnosis
When material is fed on to a mistracked belt in the loading zone, it tends to hold the belt in the mistracked position over the full length of the conveyor. Off-centred belts going through the loading zone can cause a gap between the skirting system and belt that will let material drop out. In severe cases, the belt can become trapped in this position by the skirting.
Solution
Installing a belt trainer before the tail pulley will centre the belt before it goes through the tail and loading zone, minimizing the issue. Always look for a trainer that provides friction and changes the tension profile by tilting as well as pivoting. When both the friction and tension mechanisms work together, they are over three times more effective than a pivot tracker at restoring belts back to the centre of the conveyor.
Conduct an annual assessment
Dust, spillage, and equipment damage at the loading zone is avoidable. Evaluating and optimizing the belt conveyor at loading points can do wonders for a belt conveyor system and its productivity. Operators should take the time to conduct a proactive evaluation of their system and tackle the challenges before they become real issues that affect their productivity and bottom line.
For more information, visit: www.flexco.co.uk
- Subscribe to Quarry Management, the monthly journal for the mineral products industry, to read articles before they appear on Agg-Net.com