Understanding Bearing Vibration Analysis
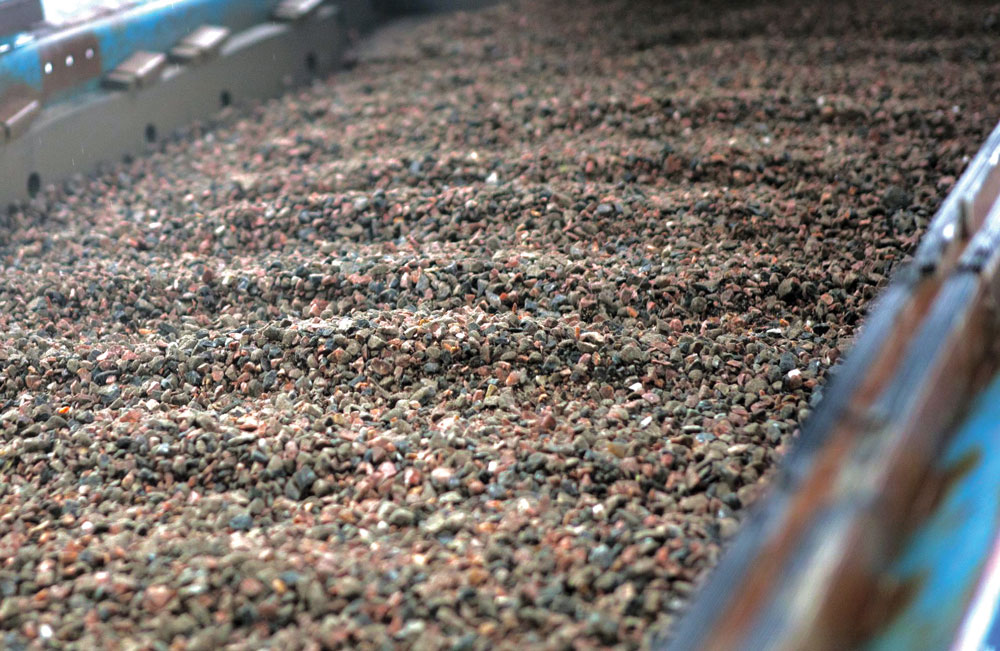
First published in the May 2017 issue of Quarry Management as Fundamental Frequencies: Understanding bearing vibration analysis
Vibration analysis plays a critical role in the condition-based maintenance of rotating equipment. Alan Shire, contract manager, service delivery - reliability systems at SKF, explains how vibration signals can be interpreted to provide early indicators of developing problems.
The shift from time-scheduled to condition-based maintenance is transforming equipment performance in the quarrying, mining and aggregates sector, reducing unplanned outages, improving availability and cutting costs. Fundamental to most modern condition-monitoring systems is vibration measurement – vibration, and particularly variations in vibration characteristics over time, being key indicators of the state of a machine’s mechanical health.
Abnormal vibrations – ie excursions from the normal vibration ‘signature’ of a machine – are often the first indication of a potential machine component failure. Conditions that can cause these vibrations are numerous, but can include imbalance, misalignment, loose parts, poor lubrication, a deteriorating rolling element bearing or gear damage.
Vibration analysis instruments and systems can help detect many serious problems at an early stage, allowing personnel to undertake remedial work in a timely manner and avoid deterioration in machine efficiency or, at worst, machine failure. Various techniques are available to diagnose machinery condition from vibration data, including time waveforms, spectral analysis, phase measurements, and amplitude measurement methods.
But before any analysis can be undertaken, the first step is to choose appropriate vibration measurement sensors and, importantly, ensure their correct installation on the machine or equipment. Inappropriate sensor choices and inadequate installation methods can easily give misleading data or, in some cases, cause a critical machine condition to be completely overlooked.
The three parameters representing motion detected by vibration sensors are: displacement, velocity and acceleration, with corresponding sensor types including eddy current probe displacement sensors (used on machines utilizing sleeve/journal bearings) and accelerometers.
By far the most popular and reliable sensor for vibration monitoring is the accelerometer. With their wide frequency range, accelerometers are suitable for all types of vibration measurement and the signal-processing techniques that can be applied to accelerometer measurements are particularly useful. For example, acceleration integrated to velocity opens up a low-frequency measurement capability, while acceleration signals in the high-frequency range can be processed using a variety of techniques, such as acceleration enveloping (gE), which is useful in identifying repetitive impact-type vibrations generated by rolling bearing damage, machinery faults due to loosened components, gear faults, and lack of lubrication.
Sensors can be permanently mounted, and the mounting configuration (adhesive patch, magnet or threaded stud) will depend upon the dynamic measurement requirements, such as frequency and amplitude range. Other factors to be considered when deciding on the appropriate mounting positions are prohibitions (safety, hazardous environments etc), accessibility and temperature.
In addition to permanent mounting, there is growing interest in the use of hand-held devices, such as the SKF Microlog series of data collectors and analysers, which can be used by maintenance staff as part of a routine ‘walk-around’ machine or equipment health monitoring programme. The main task of such programmes is basic screening and seeking changes in trends, rather than absolute measurements. These instruments are becoming increasingly powerful in terms of their waveform-processing and display capabilities.
Fault detection
An interesting vibration measurement based machine fault monitoring system, developed specifically for mining, quarrying and cement production environments, is SKF Copperhead, which comprises rugged, permanently mounted combination vibration/temperature measurement sensors and enclosure-mounted alarm, display and transmitter modules. The system was first used, with a considerable degree of success, on vibrating screens, which represent a notoriously punishing application for bearings.
In contrast to condition monitoring, which requires a certain level of expert interpretation, fault detection requires little operator training and can be set up quickly to provide a useful machine health monitor that delivers either periodic or continuous readings, according to user requirements or resources. Fault detection is dependent on electronic filtering, which discriminates between vibrations in the frequency range that indicate the onset of a fault condition while ignoring all other frequencies. The frequencies of interest are further processed and compared to an alarm set point in the system. If the overall ‘bad’ vibration level exceeds the set point, an alarm is initiated and the operator is alerted to a possible component malfunction.
While it will not necessarily provide the root cause of a fault – which demands further signal-processing capabilities – once integrated into a plant automation system, SKF Copperhead can communicate critical data worldwide, via a web-based link, for more advanced data analysis either by SKF personnel or third party qualified individuals.
An example of the analyses that can be undertaken remotely include the aforementioned acceleration enveloping (gE). This is a particularly useful analysis technique for vibrating screens. It is able differentiate between normal vibrations, due to the passage of minerals through the machine, and abnormal vibrations, due to machinery process faults, such as a loose mesh or a common phenomenon with vibrating screens – ‘bottoming out’.
Advanced analyses
Diagnosing the behaviour and condition of rotating machinery can involve one or more of several waveform-analysis techniques. These might include fast Fourier transform (FFT) spectrum analysis, which can isolate the highest vibration peaks from a spectrum to identify signals indicative of specific machine problems, such as misalignment, imbalance or bearing faults; and time waveform displays for acceleration, velocity, displacement or enveloped acceleration measurements.
Users of hand-held vibration measurement instruments, such as the SKF Microlog series, can take advantage of SKF’s Analysis and Reporting Manager (ARM) software, which is a PC-based Microlog support application providing automatic transfer, display and analysis of measurement data generated by the application modules embedded in Microlog instruments. ARM’s post-processing features allow time domain data to be processed using FFT routines into spectra and more complex waveform analyses, while time-series data may also be processed using SKF’s acceleration envelope (gE) technology for rolling element bearing analysis.
In-depth analysis – particularly of online, multi-point condition-monitoring systems – can be achieved remotely and in real time via a web link or wide-area network, using sophisticated software. A good example is the SKF @ptitude Analyst software suite, which incorporates innovations such as SKF-patented algorithms, CTA (cyclic time average) overlay, and HAL (harmonic activity locator) analysis. A CTA overlay, for example, enhances time waveform analysis when diagnosing broken gear teeth, while HAL provides harmonic series recognition of impact failures.
Conclusion
Whether derived from a fully integrated, remotely monitored condition-monitoring system or an on-site fault-detection system, machine vibration data can reveal a great deal about the health of machinery. Vibration data analytical tools can be used to detect a variety of machine failure modes; just how complex that analysis needs to be will depend on the application, but primarily it will come down to simple economics and the difference between the costs of implementation and the price to be paid for machine or equipment failure.
- Subscribe to Quarry Management, the monthly journal for the mineral products industry, to read articles before they appear on Agg-Net.com