The Importance of Equipment Maintenance
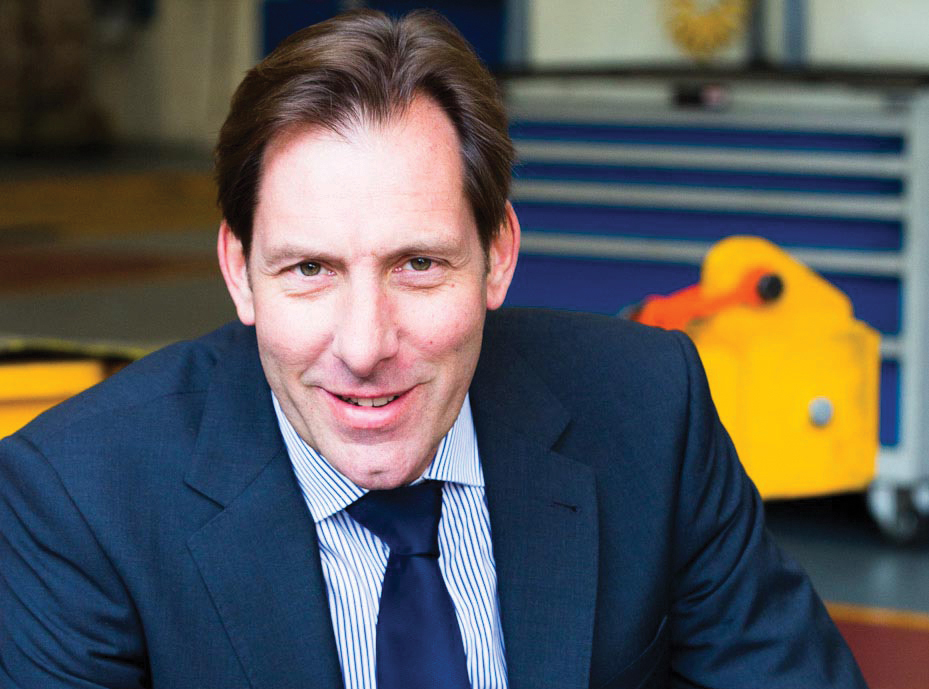
First published in the August 2016 issue of Quarry Management as Are You Ready for the Challenge?
A secure and reliable domestic supply of minerals products will be essential to the UK’s economic recovery, and investment in equipment maintenance will be fundamental to achieving this, argues Tony G. Locke, managing director of Weir Minerals Europe
The performance of the construction sector is seen as a major marker for the health of the UK economy, but there is another sizeable industry that is closely linked – quarrying and mineral products manufacturing. According to the Mineral Products Association (MPA), the industry is worth more than £9 billion and is the biggest supplier to the construction sector by a considerable margin.
The Government has introduced a number of initiatives to boost the demand side of the construction industry. The Help to Buy scheme has already had a significant impact on demand for new-build housing and this is backed up by ambitious targets for building new homes – the then-Chancellor, George Osborne, announced the biggest house-building programme since the 1970s in last year’s Autumn Statement.
Meanwhile, proposed large infrastructure projects such as HS2 and the planned nuclear new-build programme both represent undertakings for the construction sector that are unprecedented in recent times.
This activity will inevitably put pressure on the whole of the construction supply chain, of which quarries, sand and gravel sites and aggregates processing plants across the country are a critical part. It will be vital, therefore, that the minerals products industry is able to meet the demand reliably, safely and in an environmentally friendly manner.
Investing in performance
One of the biggest factors that determines the productivity, efficiency and reliability of any mineral processing plant is the suitability and condition of the equipment it uses. As a supplier to some of the biggest quarrying and mineral processing businesses in the UK, Weir Minerals are committed to improving the performance of processes on site. In recent years, the company has invested heavily in product development to bring innovations to the market, both in terms of new designs and advanced materials that will help operators to maximize performance.
A mineral processing plant is a dynamic system, and processing hundreds of tonnes of abrasive rock every hour understandably takes its toll on every piece of equipment along the line. Achieving efficient and reliable performance means using the right pieces of equipment for each individual process along the line, regularly monitoring the performance of this equipment, and scheduling and conducting proactive maintenance.
Minerals processing is often a relatively low-margin business and it can be difficult to justify significant expenditure on new equipment in the absence of a clear and immediate uplift in demand. Operators, therefore, cannot afford to under-invest in maintenance of the equipment they already have on site.
The costs of downtime caused by an unexpected equipment failure can quickly have a significant impact on overall productivity and this outweighs the level of expenditure required for an effective maintenance programme. The impacts are not only financial – poor equipment performance can also lead to excessive fuel and water consumption, which increases the impact of the process on the environment.
Proactive maintenance
There remains a tendency for the maintenance of process equipment to be carried out on a reactive basis, despite the number of significant disadvantages to this approach.
By only responding when the performance of a particular piece of equipment becomes compromised, there is the potential for an operator to find unexpected failures in the system. Many modern processes run end to end, with carefully calculated flow rates at each stage ensuring that materials and water flow through the system without building up, allowing the process to run continuously.
The period of lost productivity caused will vary depending on the scale of repairs required, the availability of replacement parts and how long it takes a qualified engineer to travel to the site. In the worst case scenario, the process can be halted for a number of days, with serious implications for profitability.
Quarry operators can significantly reduce their risk of suffering a loss of productivity by putting in place a proactive maintenance regime that will reduce the prospect of unexpected equipment failures occurring.
Regularly performing ‘health checks’ on the system, particularly the parts that are most likely to be subject to wear, allows the condition of parts to be tracked and scheduled replacements to be carried out towards the end of their functional life, in advance of any failure occurring.
While these checks may require brief periods of downtime, the net effect will be increased productivity by avoiding unscheduled emergency repairs, which can take longer to perform. Constant monitoring of the system’s efficiency by tracking flow rates, fuel or power consumption and vibration levels is also important, as this will alert operators to problems without interrupting the process.
There is no standard approach, and the intensity of monitoring and maintenance required will vary depending on the operation. It is important to find the right balance between process performance and maintenance spending.
The critical figure that quarry operators should bear in mind when it comes to their equipment investment is the whole-life cost of ownership – that is, the overall impact that the selection of any given product has on their bottom line, taking into account the performance it delivers throughout its whole lifespan.
Looking at this figure, the initial capital cost of any piece of equipment will often be vastly outweighed by the impact of different levels of performance, and this demonstrates the vital importance of equipment maintenance.
The British construction sector looks set for a period of growth, and it is vital that the mineral products industry is able to deliver the raw materials this activity will require. This represents a significant opportunity for quarry owners in the UK, but it is vital that their equipment is equal to the challenge.
- Subscribe to Quarry Management, the monthly journal for the mineral products industry, to read articles before they appear on Agg-Net.com