Proactive Hydraulic Hose Maintenance
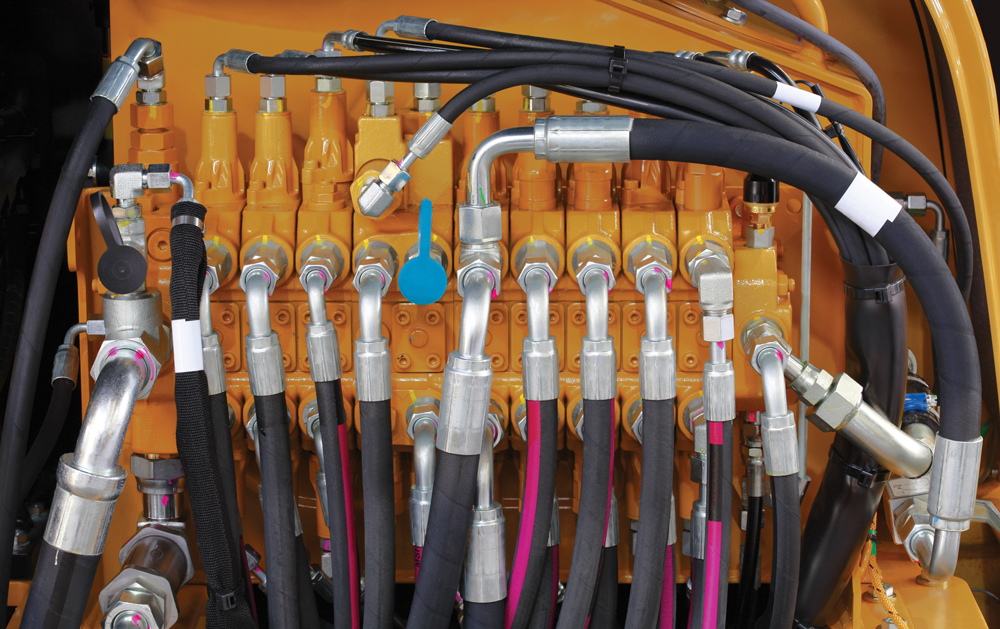
First published in the August 2016 issue of Quarry Management
Terry Davis, national technical manager with Brammer, explains that there is always an indicator that a hose will fail, allowing maintenance engineers to act in time
It is often thought that hydraulic hose failure cannot be predicted, and as a fairly inexpensive component, many production managers accept failure as unavoidable. Equally, it is common for hydraulics users to pre-emptively replace hoses which are still in safe working order, expending time and money unnecessarily. However, the low cost of the hose itself belies the considerable expense associated with oil clean-up and replacement, while a run-to-fail policy also fails to take into account the significant health and safety hazard posed by burst hoses.
Hydraulic systems can contain as much as 2,000 litres of oil, which, due to high pressures, can completely drain out of a damaged hose within just 20 minutes. Even a small pin-prick sized hole can quickly compromise an entire system as, due to pressures exceeding 100 bar or even 200 bar, a tiny hole can split or expand to the size of a golf ball within a very short space of time. While many modern hydraulic systems sit within a bund to collect waste oil, bursts can be unpredictable. The oil may spurt out at an angle, missing the bund altogether and damaging surrounding equipment or worse – causing significant and even life-changing fluid-injection injuries to individuals.
Due to all these factors, the cost of a leak is not limited to the price of the replacement hose, which could be as little as £10. Simply replacing 2,000 litres of oil could cost £1,000 or more, and this may not be accomplished immediately as few lubricant suppliers keep the volumes required in stock – and oil from different sources usually should not be mixed. There is also the cost of downtime to consider, as well as the cost of cleaning up and safely disposing of oil. Should oil escape down drains, environmental fines may also apply, as well as the cost of compensation or fines if an individual is injured as a result of a leak. It is easy to imagine how the £10 cost of a replacement hose could spiral into several thousands of pounds, meaning ‘run to fail’ is neither an economic nor safe option.
Failure can be predicted either by calculating usage, through the use of monitoring tools, or visually. Most hoses will last for around a million cycles, and so by analysing the run time of a piece of machinery, the average lifespan of the hose should be easy to calculate. Alternatively, various monitoring systems exist which can be installed within a hydraulic hose assembly to detect dangerous levels of wear and send an alert at the point at which a replacement is required. Often based on RFID or infrared technology, monitoring systems offer a high degree of reliability as they are not based solely on calculations and so account for any unpredictable wear caused by misuse.
Where monitoring technology is not used, a combination of calculations and visual inspection should be implemented. Before undertaking full inspection – either planned or as a result of spotting a potential fault – the hydraulic power pack should be shut off and depressurized.
A hose consists of an inner metal braid, connected to the ferrule at either end via a robust crimp, and protected by an external rubber sleeve. Should the braid be visible due to rubber wear, the hose should be replaced as this could be indicative of damage to the inside of the hose and leaves the braid open to rust and abrasion. This can be caused by excessive pressure being exerted on the hose, for example being driven over by forklifts or trapped under other machinery.
Where the rubber casing remains intact but the inner braid is damaged, a tell-tale sign is blistering or swelling of the outer coating. Here, oil is seeping through the braid and travelling between the two materials, meaning it is only a matter of time until the rubber housing gives way. Another cause of blistering could be an incompatibility between the hydraulic fluid and the hose materials, again pointing to replacement.
A hard, brittle rubber casing is indicative of its maximum operating temperature being regularly exceeded, meaning it should be replaced with a more suitable product. Conversely, a tube exposed to temperatures below its optimum level will remain soft and flexible but display hairline cracks, in which case either the system temperature should be raised or the hose replaced.
Frays or loose wires at either end of a hose point to excessive hose movement, which may be the result of vibration, pressure surges or too short a hose. If vibration can be identified as the cause, clamps or dampers may be required to support the hose if re-routing is not an option. An amount of slack should always be allowed as assemblies shrink when pressurized, so a longer hose may be required. Hoses should always be specified with a higher maximum operating pressure than the system itself to account for surges, although spiral-reinforced hoses are available specifically for severe pulsing applications if necessary.
Hoses often need to be supported by fittings to prevent them being bent out of shape or exerting pressure at weak points. Fraying can occur as a result, exposing parts which can corrode, wear or rust. As hoses of 6–8m in length and 2.54cm (1in) in diameter are not uncommon, they are typically very heavy and, without support, will put pressure on the crimp and fitting at one end or both. Persistent pressure can distort and break a crimp, and oil drips can quickly become a jet under normal operating conditions. When installing supports for hydraulic hoses, it is recommended to replace the hoses at the same time to account for previous wear and tear when unsupported. Any twists or tight bends should be inspected for damage and, in the case of twists, care should be taken not to over-tighten the fitting as this itself can cause pressure.
When replacing a hose, engineers should ensure it is within its ‘best before’ date. Products should show the date of manufacture of all components along with the date of assembly, as hoses have a shelf life – the nitrile rubber casing loses its effectiveness after around five years due to UV exposure, so care must be taken to ensure the hose is within date and professionally swaged to ensure components have not been changed or replaced. Brammer’s fluid power solutions team has more than 20 years’ experience in the inspection, design and repair of hydraulic hose assemblies.
- Subscribe to Quarry Management, the monthly journal for the mineral products industry, to read articles before they appear on Agg-Net.com