Centralized Lubrication Systems
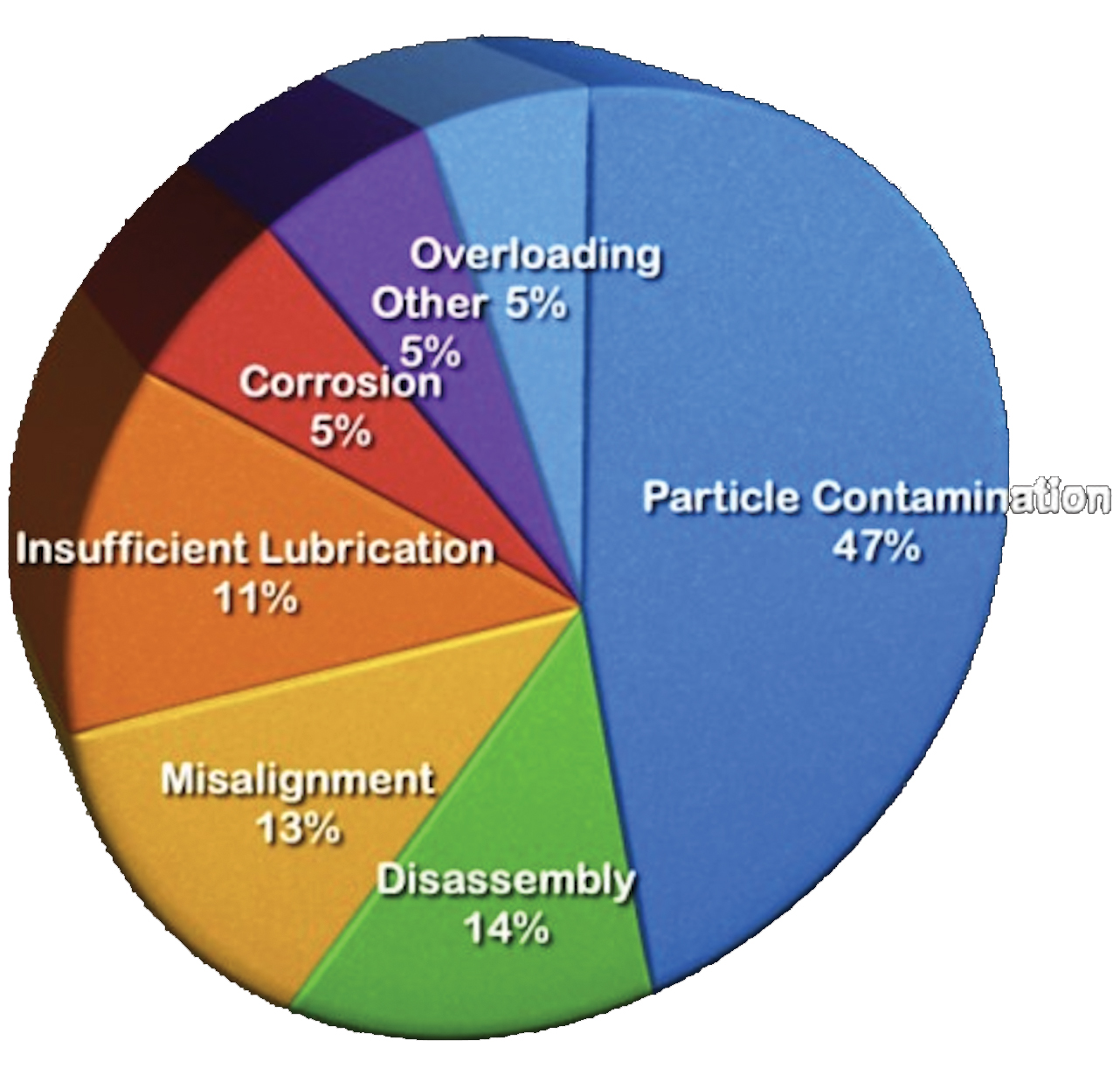
First published in the July 2020 issue of Quarry Management
The key to unlocking the full value and potential of machinery
Construction plant and machinery operates in some of the hardest and harshest conditions. With companies requiring reliability and value from their equipment, getting the most from their bearings, without incurring any unnecessary operating costs, is key. It is not only the heavy loads and rough working conditions that apply pressure on modern construction machines and equipment, but also the users’ ever-increasing demand for performance and cost-efficiency.
In a study conducted by a major component manufacturer, it was found that more than 60% of bearing failures were the result of inadequate lubrication, bearing contamination and corrosion (see fig. 1). The ramifications of this are, not surprisingly, costly and can cause massive disruption to production.
Obviously, effective lubrication is paramount, but manual lubrication can be inconvenient. Stopping a machine at regular intervals to lubricate bearings is expensive, both increasing downtime and reducing manpower. As a result, businesses will never be able to maximize the performance and value of their equipment. Moreover, too much lubrication can potentially create a safety or environmental hazard, whilst too little causes bearing friction and wear.
According to lubrication system experts Lube-Spec Ltd, the use of centralized lubrication systems can eliminate the ‘feast or famine’ conditions associated with manual lubrication. A centralized system applies smaller amounts of lubricant more frequently while the machine is in operation, effectively keeping bearings in the optimum lubrication zone (see fig. 2). The application of lubrication to a bearing is far more efficient in smaller quantities at shorter time intervals with the bearing in motion – a formula that is near impossible to maintain with manual greasing.
With a centralized lubrication system, all bearings are lubricated regardless of location and only when the equipment is in operation, ensuring even distribution and maintaining a level of lubricant around the bearing contact surface areas. This results in a number of benefits including: lower energy consumption, due to less friction; reduced wear on the components, resulting in extended bearing life; fewer breakdowns; lower replacement and maintenance costs; and increased productivity. A centralized lubrication system also eliminates a number of safety hazards, such as having to climb over equipment and/or enter confined spaces to access bearings requiring lubrication.
Lube-Spec Ltd have been assisting their customers for more than 30 years in maintaining and protecting machinery through the use of centralized lubrication systems. Company director Mark Cherry said: ‘Maintaining properly lubricated machinery is an important part of any lubrication programme. Without administering the proper amount of lubricant at correct intervals, a machine can experience costly failures.’
Centralized lubrication systems distribute a measured amount of lubricant to a specific location at specific times through the use of the programmable controllers, timers and lubrication pumps, distribution blocks, and metering units or injectors.
Centralized systems were introduced in the mid-1930s and since then much research has focused on resolving the flow issues of various lubricants, eg delivering grease effectively to its designated points. Advances in technology have created today’s modern centralized systems featuring precise delivery methods for a wide range of applications.
Centralized lubrication systems are sometimes referred to as ‘automatic lubrication systems’ because the process of dispensing the lubricant is mostly computerized. The systems eliminate the risk of human error and increase precision when an application requires the lubrication of different sized bearing components on numerous machines.
When delivering lubricants to bearings, the lubrication pump is activated by the controller. This creates pressure and distributes the grease/oil to the system distribution block or injector, which is pre-set to deliver a specific amount of lubricant at a specific time interval. Lubricant flows through the grease lines and the distribution block/injector, which, in turn, feeds grease/oil into the bearing. A pressure switch can be incorporated in the system to deactivate the pump once the lubrication cycle is completed. The last step in some types of centralized lubrication systems is a unit that can detect any lubricant pressure remaining in the grease line, which is then delivered back into the reservoir.
The latest technological advancements have seen the introduction of many products for controlling and monitoring centralized lubrication systems. Distribution blocks/injectors, grease lines and lubricant reservoirs are now commonly monitored by visual and/or audio signals. For example, an alarm is sent when an undesirable flow pattern exists or when the lubricant reservoir is low. Incorporating such alarms into a system is useful in preventive maintenance. If a machine has prolonged maintenance intervals, high-capacity lubricant reservoirs can be utilized, typically holding double the volume of a common reservoir.
Mr Cherry concluded: ‘A centralized lubrication system is key to achieving peak performance from any operating equipment, whether it’s a dumptruck, mobile crusher or static industrial machinery.’
- Subscribe to Quarry Management, the monthly journal for the mineral products industry, to read articles before they appear on Agg-Net.com