Volvo CE Celebrate Half a Century Milestone with Launch of New Hauler
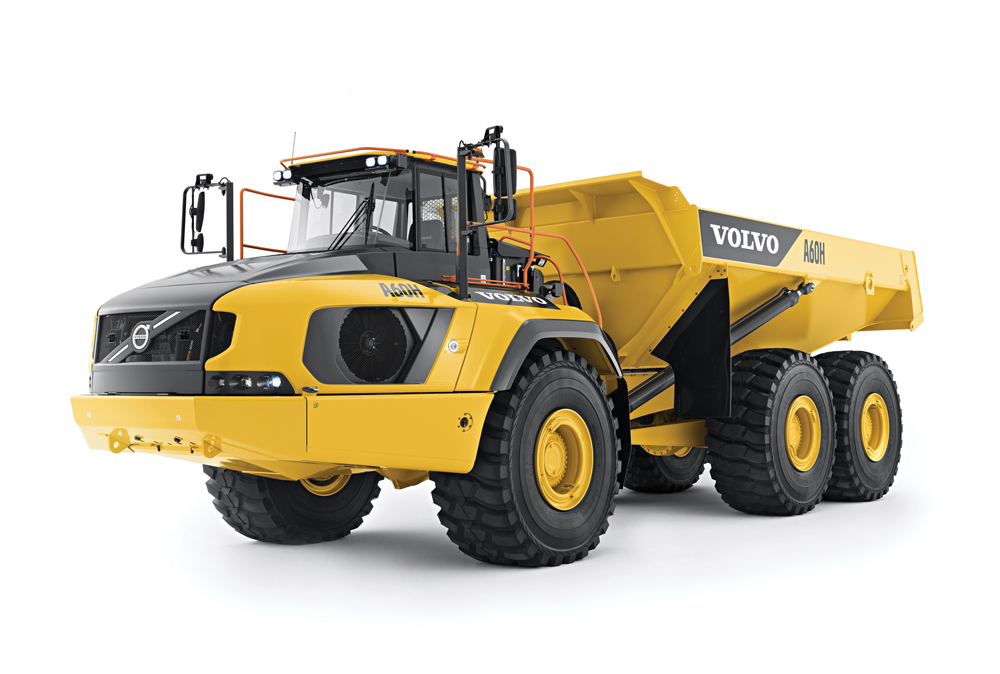
First published in the November 2016 issue of Quarry Management as Half a Century of Success
Having commercially launched their articulated hauler concept in 1966, this year saw Volvo CE mark the 50-year milestone with the launch of their biggest-ever production hauler
The articulated hauler concept is celebrating its 50th anniversary this year, marking five decades of transporting earth, sand, gravel, rock and a host of other materials over rough, muddy, slippery, steep or otherwise impassable terrain. And the company that is widely accepted to have commercially launched the concept in 1966 – Volvo CE – still lays claim to being the market leader. Moreover, in 2016 Volvo CE continue to innovate with the launch of their H-Series range – which includes the company’s biggest-ever production articulated hauler – the 60-ton (55-tonne) capacity A60H.
Genesis of the articulated hauler
In 1966 the Soviet Union’s Luna 9 made the first rocket-assisted landing on the moon, the Cultural Revolution began in China, England won the World Cup and the Rolling Stones were banned from 14 New York hotels. With so much going on it was easy to overlook the launch of the DR631 – regarded by many as the birth of the articulated hauler. Essentially a development of an agricultural tractor (which Volvo then made) and a trailer, they were permanently joined via an articulating hitch, and the front axle of the tractor removed. Nicknamed ‘Gravel Charlie’, it may have had only a meagre 10-ton payload capacity, but it set the stage for greater things to come. Perhaps surprisingly though, its popularity grew only slowly to start with, with sales in the early years being confined to its home market in Sweden.
One of the main reasons for the ongoing popularity of Volvo’s haulers has been the consistent development of the concept. Only one year after its launch, in 1967, the company introduced the DR860, the first articulated hauler with a bogie, meaning that the material in the load body remains level and stable (reducing spillage) while the wheels cope with very uneven road surfaces. The first hauler with a turbocharged engine – the DR860T – arrived in 1970, and in 1979 things literally started to speed up with the launch of the 5350. Capable of 50km/h, the ‘Off-road Express’ was able to maintain previously unheard of speeds thanks to a suspended front axle and an automatic transmission. Traction was further increased with the addition of a six-wheel-drive system.
The A-Team arrives
The A20 was launched in 1986 with a 200hp engine and a 20-ton payload capacity, but things soon got a lot bigger in 1987 with the advent of the 35-ton abilities of the A35, which also featured a retarder built into the transmission to reduce wear on the service brakes.
The range was given a major overhaul in 1993 with the introduction of the C-Series, which featured a low-emission engine, fully automatic transmission and 100% differential locks. The 40-ton class hauler was launched in the mid-1990s in the shape of the A40, powered by a 400hp engine and stopped by oil-cooled wet disc brakes.
Bigger, stronger, more reliable, easier (and cheaper) to operate, safer for the environment and the operator, the D-Class of articulated haulers from Volvo CE were introduced in 2000. Covering payloads ranging from 24 to 37 tons, all D-series Volvo articulated haulers – A25D, A25D 4x4, A30D, A35D and A40D – featured a comfortable cabin and required no daily greasing. For the first time diagnostic electronics also alerted both the operator and the technician of problems before they became failures; thus increasing uptime.
Developments such as automatic traction control (ATC) once again helped set Volvo CE apart in the hauler market. ATC relieves the operator from manually operating differential locks and drive configurations (6x4 or 6x6) as driving conditions change. Multiple sensors constantly check the speed differences within the driveline and select the best drive combination for the conditions. This also reduces tyre wear, driveline stress and fuel consumption.
Full suspension
In 2007 Volvo CE decided to adopt a radical approach with the introduction of hydraulic suspension with automatic levelling and stability control on all wheels. This ‘full suspension’ variant provided excellent off-road performance, allowing the hauler to travel at much higher speeds and increasing productivity. Even when fully loaded, the E-Series haulers’ ability to ‘float’ over rough ground without bouncing and rolling improved operator comfort and safety. These benefits increase with the length of haul road, effectively absorbing all rough spots and allowing operators to maintain considerably higher average speeds – with or without a load. A hauler traveling at 55km/h over rough haul roads was now possible, with minimal bouncing rolling or shaking.
Arrival of the F-Series:
2010 heralded the arrival of F-Series haulers that not only met the demanding standards set by the Tier 4i (US) and Stage IIIB (Europe) emissions legislation, but also featured a package of improvements in functionality, design and maintenance. The F Series also saw the fitment of Volvo’s CareTrack telematics system as standard, allowing remote monitoring of a wide range of machine functions (eg location, fuel consumption, service reminders etc), thereby optimizing customer operations.
Volvo CE’s articulated haulers took another step forward in 2014 with the launch of the
G Series, which not only met the stringent Stage IV/Tier 4 Final emissions regulations, but also offered new features designed to improve comfort and productivity. The proven concept of oil-cooled wet multiple-disc brakes on the A35 and A40 models was also introduced on the A25G and A30G, reducing maintenance costs and increasing uptime, even on muddy or dusty job sites.
The larger models in the range were also offered with Volvo’s award-winning on-board weighing system, which allows for precise machine productivity monitoring, helping to optimize payload and minimize wear, tyre damage and fuel consumption. The system monitors weight, relaying information to load software integrated into the machine’s electronics. Indicator lights tell the hauler operator, as well as the operator of the loading unit, whether the hauler is at part or nominal load, or whether it has been overloaded.
The new H-Series
The H Series, launched in 2016, is the culmination of 50 years of Volvo engineering and innovation. Responding to a growing demand among customers for articulated haulers with larger payloads, the H-Series also saw the addition of the 60-ton (55-tonne) capacity A60H to the Volvo range.
The A60H’s higher payload – a 40% increase on Volvo’s previous largest hauler, the A40 – significantly lowers the cost-per-tonne ratio for hauler customers. The new size also offers a viable alternative to rigid dumptrucks and construction trucks operating on soft, uneven or steep roads, allowing a similar amount of material to be hauled in a shorter cycle time. Good stability, comfort and high hauling speeds are ensured by the H-Series, thanks to matched drivetrain, automatic drive combinations (including 100% differential locks), all-terrain bogie, hydro-mechanical steering and active suspension.
Today, Volvo continue to be the world’s leading manufacturer of articulated haulers. Having introduced the concept in 1966, they have been developing and building these machines ever since. The story has come a long way since the original 10-ton ‘Gravel Charlie’, but with proven success over the years, the new H-Series machines are continuing the tradition of delivering innovative technology, reliability, comfort, quality and low cost of ownership.
The A60H – Volvo’s biggest articulated hauler
Shown for the first time in Great Britain at Hillhead 2016, Volvo Construction Equipment’s largest articulated hauler to date, the A60H, has been designed to provide reliability and durability in heavy hauling in severe off-road operations, including quarries, opencast mines and large earthmoving operations.
With its 55-tonne (60-ton) payload capacity, the A60H is said to bring a new dimension to reducing the cost per tonne of material moved using tried and tested frame and powertrain designs with the emphasis on fuel efficiency. Powered by a 16-litre Volvo engine delivering 495kW and 3,200Nm of torque, the A60H has a maximum speed of 54.9km/h and shares many of the same features and benefits in terms of design and overall layout as its smaller brothers in the Volvo articulated hauler range, but with a 34m3 body capacity.
Moreover, with the A60H, valuable data is on hand to improve on-site efficiency and save costs. With intelligent Volvo systems such as MATRIS, CareTrack and on-board weighing, customers can optimize production and minimize operational costs. The on-board weighing system, for example, guarantees the optimal load every cycle, thereby maximizing production, boosting fuel efficiency and reducing machine wear in all site conditions and operations.
With its matched drivetrain and automatic drive combinations, including 100% differential locks, all-terrain bogie, hydro-mechanical steering and active suspension (with an active hydraulic front suspension for higher hauling speeds in tough conditions), Volvo say the A60H optimizes operator comfort and stability during travel, allowing more material to be moved in a shorter time for unmatched productivity. In addition, the A60H’s dump support system, hill assist and load and dump brake, help the operator to stay in control at all times, for extra safety.
• Subscribe to Quarry Management, the monthly journal for the mineral products industry, to read articles before they appear on Agg-Net.com