Telematic Technology
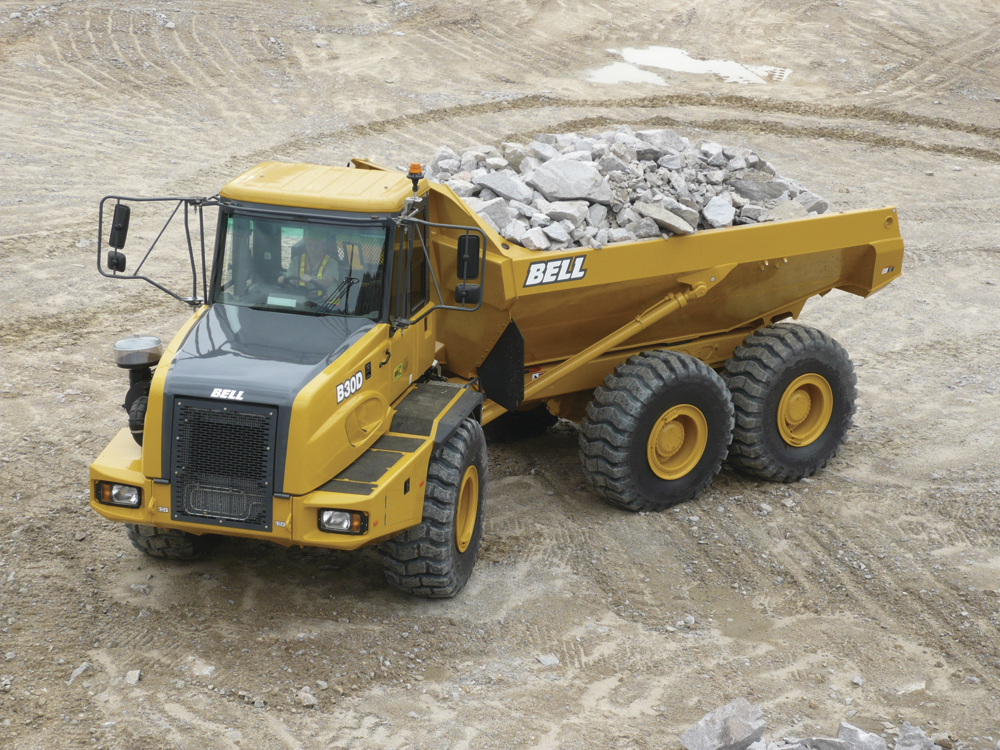
The advantages of telematics in loading and hauling
Technology has improved almost every aspect of modern life, often in ways that have far exceeded people’s imaginations. This is true even in the quarrying industry, where the advent of telematics, particularly in load and haul applications, has brought with it significant increases in productivity, lower operating costs and improvements in safety and security.
Heavy equipment manufacturers Bell Equipment are among the forerunners of telematics technology in the global articulated dumptruck (ADT) market, having developed Fleetm@tic, the company’s own satellite-based fleet-management system.
Recognizing the importance which operators place on having timely and accurate data, Bell have made Fleetm@tic a standard in-built feature on all of their ADTs, giving customers the tools to improve their operation – and bottom line.
The company claims its system is not only the most advanced and comprehensive in the world, but the only one that can provide a true link between machine performance and operational productivity.
Fleetm@tic is now in its second generation and offers specific advantages to the quarrying industry. For example, the latest version of the software includes data capture of both laden and unladen idle times.
According to Trevor Musliah, Bell Equipment’s product marketing manager for ADTs, by providing laden and unladen idle times quarry owners can more easily see where bottlenecks are occurring in their operations.
‘Excessive unladen idle times could suggest a bottleneck in the loading area due to a mismatch of equipment,’ he said. ‘Long laden idle times could be due to the tipping area being too small, the turning circle being too tight or a bulldozer that is too small to cope with the workload.’
Such a situation was identified at an Imerys china clay quarry, near St Austell, in Cornwall, where Fleetm@tic is used on the 50-tonne Bell B50D trucks operated by Denbow International.
Here, the Fleetm@tic reports highlighted a particular spot on the haul route where truck speeds were mysteriously dropping. On investigation, it was quickly recognized that the ADTs were slowing at one particular corner, in case another truck was approaching from the other direction. So Imerys excavated the hillside to create a wider stretch of road and increase visibility – with the effect that haul cycles, and overall productivity, saw immediate improvements.
Fleetm@tic is also able to measure how many tonnes of each type of material have been loaded and offloaded. This feature is particularly useful in crushed rock applications to track the stockpiling of different materials.
Bell’s Fleetm@tic monitors the average payload of an ADT along with the average cycle rate and average fuel burn. ‘Statistics of the average payload allow a fleet owner to check that he’s not overloading or under-loading,’ explained Mr Musliah. ‘Overloading could lead to early fatigue, while under-loading would suggest a fleet owner is not getting the full benefit of his machine.’
Likewise, the bin tip angle can be automatically set to save time and fuel. Depending on site conditions, this could have a safety benefit by preventing accidental damage to overhead infrastructure.
In addition, Fleetm@tic sends critical event notifications in the event of speeding, over-revving or other incidents of machine abuse so that fleet owners are able to take corrective action. ‘Apart from machine abuse, which could affect a machine’s health, these incidents are also linked to site safety,’ said Mr Musliah.
With safety in mind, Fleetm@tic allows fleet owners to geofence areas so that a truck will automatically decelerate or only be allowed to accelerate within certain zones. Within a hopper site, for example, the truck may be geofenced to travel at a slower speed. In addition, a machine can be geofenced to effectively limit it to only operate in a specific geographic area, thus minimizing any potential for plant theft or unauthorized use.
At the heart of Bell Fleetm@tic is a GPS and data transmitter/receiver unit installed inside the ADT cab and integrated into the machine’s CANbus system. The onboard GPS receiver calculates the position of the machine from orbiting GPS satellites and stores position, production and machine data on the onboard memory module.
This data is sent to the Bell Fleetm@tic server via the service provider’s base station, where it is processed into automated reports or stored for viewing from the website at a later date. Fleet managers are issued with a confidential ID and password allowing secured access to their fleet information via the Fleetm@tic website.
A unique characteristic of Fleetm@tic is that one service provider, Iridium, supplies worldwide coverage from pole to pole. This, together with the superior transceiver technology supplied by American-based company Quake Global, allows Bell Equipment to offer their customers what is arguably the best satellite-based monitoring system in the world.
Fleetm@tic offers four levels of reporting, each more advanced and elaborate than the previous level. Fleetm@tic Lite, for example, provides a shift summary for each machine in the fleet, including the machine hours, hours operated in a shift and the average fuel consumption.
Monmouthshire-based Chepstow Plant International were one of the first users of Bell’s Fleetm@tic system in the UK and have played a significant role in sharing information with Bell in order to trigger the continual improvements that Bell have incorporated over the years.
‘We now have a dependency on Fleem@tic,’ said John Corcoran, managing director of Chepstow Plant International. ‘The data it provides for us forms a major part of the monthly reviews we have with our clients. This aspect of Bell’s product capabilities has, in turn, also demonstrated to our clients Bell’s other strong points – such as service, sales management and supporting the overall management of the business. And Bell are always making consistent improvements, which impresses our clients.’
Wiltshire-based Earthline, one of the largest independent earthmoving, recycling and quarrying companies in the south of England, are another company who have improved efficiencies through the use of Fleetm@tic on their Bell B40D trucks.
Earthline director Philip Coplestone said: ‘Fleetm@tic is a brilliant bit of kit. The system allows us to accurately measure production quantities and machine performance, including differentiation between the various materials we are handling. It leaves little to guesswork, meaning we know exactly how we are performing commercially.’
While telematic systems such as Fleetm@tic offer a variety of benefits, Bell’s Trevor Musliah warns that they do not manage a fleet for you. ‘It’s how you interpret and use the data provided by the system that will benefit your business at the end of the day,’ he explained. ‘Fleet-management systems are changing the way customers approach their business, taking a lot of guesswork out of the equation so that they can make more informed decisions.
‘Even better is that our customers can keep an eye on their machines via the website from the comfort of their homes, offices or even while travelling.’
The benefits of Fleetm@tic are further enhanced by the Bell ADTs themselves, which undergo regular upgrades to keep the range competitive, compliant with emission regulations and at the cutting-edge of technology.
All this attention to detail appears to be paying off for Bell. For example, recent independent tests run on simulated quarry conditions at Millbrook Proving Ground, in Bedfordshire, showed that the Bell B30D truck was 17.6% more fuel efficient than the equivalent model from a market-leading rival manufacturer (see page 28).
Meanwhile, in a real-life application, Fleetm@tic has helped Wakefield-based Land Engineering Services (L.E.S) identify a significant improvement in fuel-consumption figures on their fleet of Bell B50Ds compared with the smaller ADTs they had been operating from another manufacturer.
L.E.S director Iain Devine said: ‘Fuel consumption on the Bells is between 18 and 22 litres per hour, depending on conditions, gradient and distance, which is a real improvement on what we were getting before.’