Health And Safety In Quarrying
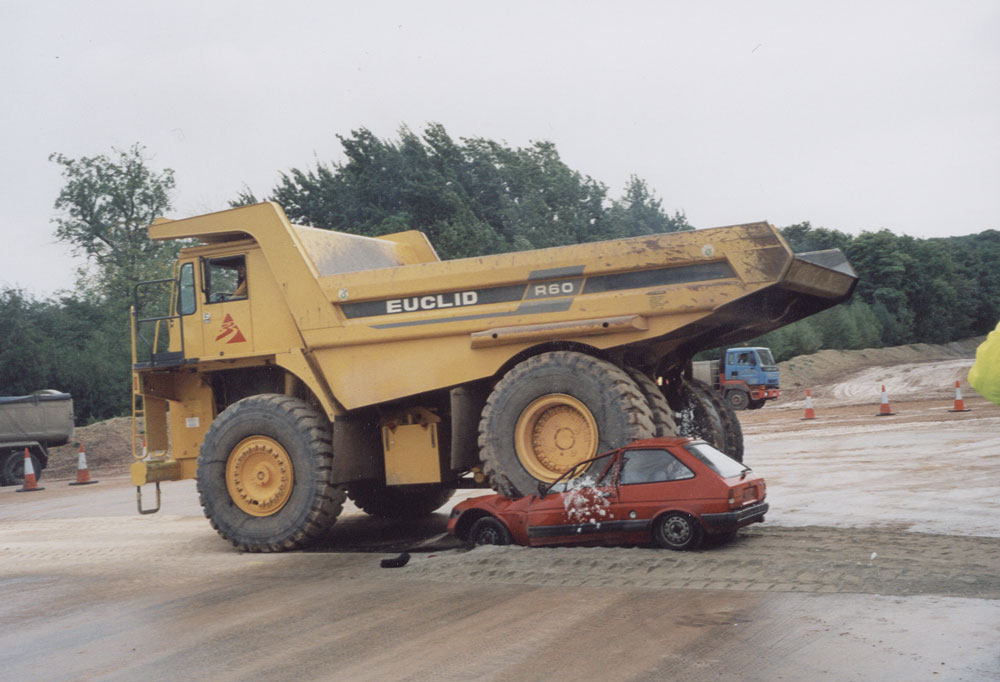
As part of the Government’s ‘Revitalizing Health and Safety’ campaign, the Quarries National Joint Advisory Committee (QNJAC) recommended that all graduates entering the quarrying industry should understand the fundamentals of health, safety and risk management. As a result a CD-ROM of lecture and training material on the fundamentals of health and safety management was prepared by the Camborne School of Mines on behalf of EPIC (NTO) Ltd and the Health & Safety Executive (HSE). This was distributed to all providers of quarry-related courses in higher education as well as to interested parties within the industry. The article that follows is the first of a five-part series that will appear in Quarry Management over the next 12 months based on this material, with the intention of bringing it to a wider audience. In this first article Dr Patrick J. Foster looks at: the reasons for preventing accidents; accident trends in the quarrying industry; and how accidents (in general) are caused.
It is estimated that each year there are some 1.2 million fatalities around the world resulting from work-related accidents or ill health (Takala, 1998). In 1998 some 335,000 people worldwide were killed as a result of accidents at work (Takala, 1998), while approximately 110 million are injured at work each year (Harms-Ringdahl, 1992).
In the UK, the 1990 Labour Force Survey stated that there were an estimated 1.6 million accidents at work, while 750,000 people suffered ill health caused or made worse by working conditions. In total 30 million working days were lost in which 20,000 people were forced to give up work.
Reasons for preventing accidents
Nobody comes to work to get injured or to become ill and no-one likes getting injured or seeing their colleagues or friends injured in accidents. Nothing is more important than the humane aspects of accidental loss: injury, pain, sorrow, anguish, loss of body parts or functions, occupational illness, disability and death. Employers and employees therefore have a moral responsibility to prevent accidents and ill health at work.
Moreover, accident prevention is important in the business sense. Whether or not people are hurt, accidents cost organizations money and the actual injury or illness costs represent only a small part of the total. A recent study by the HSE (HSE, 1997a) has shown that for every £1 of insured costs (ie the actual cost of the injury or illness in terms of medical costs or compensation costs), the uninsured (or ‘hidden’ costs) varied between £8 and £36. This has traditionally been depicted as an ‘iceberg’, as the largest part of an iceberg is hidden under the sea (fig. 1).
In October 1999 the HSE published new data on the costs to the UK of workplace accidents and work-related ill health in 1995/96 (HSE 1999a) which estimated that:
- the cost to employers is estimated at between £3.5 billion and £7.3 billion a year (between 4% and 8% of all gross company trading profits)
- work-related accidents and illnesses cost between 2.1% and 2.6% of the Gross Domestic Product each year— equivalent to between £14.5 billion and £18.1 billion.
Revitalizing health and safety
The Government has also set down targets for all workplace accidents and ill health through the ‘Revitalizing Health and Safety Strategy Statement’ issued in June 2000; this is designed to achieve a step change in health and safety performance over the next decade. The document sets the following targets:
- a reduction in the number of working days lost per 100,000 workers from work related injury and ill health by 30% by 2010
- a reduction in the incidence rate of fatal and major-injury accidents by 10% by 2010
- a reduction in the incident rate of cases of work-related ill health by 20% by 2010
- to achieve half the improvement under each target by 2004.
Accident statistics and trends in the quarrying industry
The quarrying industry is a dangerous industry with a poor safety record. It has injury rates that are greater then those in construction and far higher than the all-industry rates which are shown in table 1 (accident rates are expressed per 100,000 employees).
The actual number of fatalities, major injuries and +3-day injuries over the past five years is shown in figure 2. These are the figures that have been reported under RIDDOR (The Reporting of Injuries, Diseases and Dangerous Occurrences Regulations).
Figure 2 shows only the reportable accidents (ie the serious accidents) and not the minor accidents and near misses. The obvious next question is: How many accidents are there in the industry each year? There is no definitive answer to this, but over the years a number of studies have tried to establish the relationship between serious and minor accidents in industry generally. The results of these studies are presented as ratios, typically in the form of accident triangles. The triangle shown in figure 3 is taken from a recent HSE study (HSE, 1997b) and shows that for every major accident (ie reportable accident) there are seven minor injuries/ill health and 189 non-injury accidents and illnesses. If this trend continued in the quarrying industry then there would be approximately 3,800 minor accidents and 100,000 non-injury accidents/illnesses in the industry each year. If these figures are divided by the number of people working in the industry, then one in nine people would get a minor injury per year and every person would have three non-injury accidents per year.
Some analysis of accident trends in the industry is undertaken by the HSE and reported to the industry through the Quarries National Joint Advisory Committee (QNJAC) and/or in ‘Quarry Fact File’. Analyses of trends within quarrying companies are also carried out in house.
Over the 10-year period 1983–93 there were 81 fatal accidents in the quarrying industry in the UK. An analysis of the generic causes of these accidents was summarized by Scott (1995) and is presented in figure 4.
A breakdown of the causes of the 60 fatalities that have occurred within the period 1989–2000 (presented at the QNJAC meeting in March 2001) shows that accidents associated with transportation have actually increased over the past 10 years
the percentage of accidents associated with vehicles has increased to 54% and those associated with conveyors has increased to 16%.
A breakdown of the generic causes of all the accidents that were reported under RIDDOR during 2001/2 is shown in figure 5 (Baker, 2002). This profile is dominated by three causes, namely: handling (8 major, 80 +3 day); slips and trips (23 major, 41 +3 day); and falls from height (24 major, 18 +3 day).
There are also significant health problems within the quarrying industry, for example respiratory diseases (arising from silica and other dusts), hand-arm vibration syndrome (arising from the use of powered hand-tools), hearing loss (caused by noisy plant and equipment) and musculoskeletal disorders (from lifting and carrying). Cases of ill health are not reported under RIDDOR to anything like the extent of work-related injuries. One reason for this is that there is a long latent period for many occupational diseases to take effect and another is that only some types of ill health are reportable. Health hazards will be looked at in more detail in a later article.
How accidents are caused
Knowing how accidents are caused is fundamental to the effective investigation of accidents. It is also useful in a proactive sense in order to identify what types of failures or errors generally cause accidents so action can be taken to address these potential causes before they have a chance to occur. This section looks at accident causation generally and not in relation to the quarrying industry specifically.
Traditionally the promotion of safety has been largely reactive, concentrating on accident investigation with the primary aim of avoiding repeat events. This arose from too simple an approach to accident causation based on the apparent importance placed on the concept of a single primary cause — either an unsafe act or an unsafe condition. If the former were the case, responsibility was clear and blame could be apportioned; if the latter, then a technical solution could be sought. This approach was also easy to handle and is shown in outline in figure 6 (after HSC, 1993).
One of the first accident causation theories was put forward by Heinrich (Heinrich et al, 1980) and is known as the ‘domino theory’, as the accident sequence was likened to a row of dominoes knocking each other down. These dominos are still used as an illustrationin safety teaching although their application has been updated and changed to reflect the direct management relationship in the causes and effects of accidents (fig. 7).
Shillito (1994) states that all accidents involve a chain of events, which is a feature of the dominos. Accidents are rarely due to a single cause but to a number of causes that develop throughout this chain.
During the past two decades the UK has suffered a large number of tragic industrial disasters. In recent years these have been predominantly associated with the rail industry, but at the end of the 1980s there were four major disasters that occurred over a two-year period, namely: the underground fire at King’s Cross tube station (1987 – 31 killed); the capsize of the Herald of Free Enterprise (1987 – 189 killed); the rail crash at Clapham Junction (1988 – 35 killed); and the Piper Alpha oil rig explosion (1988 –167 killed).
These disasters, following on from earlier incidents around the world (including Bhopal, Seveso and Chernobyl), have served to focus industry and the public’s attitudes and concerns on indus-trial safety more pointedly than had been the case for many years, and made an important contribu-tion to the development of proactive safety management. This was because two common points arose in all the subsequent public inquiries. These were: the influ-ence of human error in the chain of events leading to the accident; and failures in the management and organization of safety.
A study by the ACSNI Human Factors Study Group (HSC, 1993) states that prior to these disasters, senior managers of such organizations ‘propounded the pre-eminence of safety, believing in the efficacy of the regulatory system, in the adequacy of their existing programmes and in the confidence of the skills and motivation of their staff’. However, the subsequent inquiry reports revealed that ‘their belief in safety was a mirage, their systems inadequate, and operator errors and violations commonplace’. The inquiry reports stated that ultimate responsibility lay with complacent directors and managers who had failed to ensure that their good intentions were translated into a practical and monitored reality. This can be shown by the following quotations from the reports:
‘I have said unequivocally that we do not see what happened on the night of 18 November 1987 as being the fault of those in humble places’
Inquiry into the King’s Cross underground fire (Department of Transport, 1988a)
‘All concerned in management, from the members of the board of directors down to the junior superintendents, were guilty of fault in that all must be regarded as sharing responsibility for the failure of management. From the top to the bottom the body corporate was infected with the disease of sloppiness’
Inquiry into the capsize of the Herald of Free Enterprise (Department of Transport, 1988b)
‘The concern for safety was permitted to co-exist with working practices which…were positively dangerous…The best of intentions regarding safe working practices was permitted to go hand in hand with the worst of inaction, ensuring that such practices were put into effect’
Inquiry into the Clapham Junction rail crash (Department of Transport, 1989)
In analysing these accidents Simpson (1992) concludes, in terms of accident causation, that:
- not one of these organizations had, before the accidents, any serious reservations about their ??safety procedures, organization or management, yet there were clearly many problems of which they were not aware
- errors made ‘at the sharp end’ (the immediate causes of an accident) must be seen in the wider context of the organization and management climate in which they were committed.
- active failures have an immediate consequence and are usually made by front line people such as drivers, control room and machine operators. These immediately precede, and are the direct cause of, the accident
- latent failures are those aspects of the organization which can immediately predispose active failures and would include aspects of equipment design, working environment, standard of ??training, quality of supervision etc. They are failures in the organization’s management of safety.
In his classification of active failures, Reason (1990) distinguishes between intentional and unintentional error (fig. 8). Unintentional errors are classified as either slips/lapses or mistakes, while intentional errors are described as violations. These are expanded upon below (after HSE, 1999). In the discussion reference is also made to means to reduce the likelihood of this type of error occurring (after Mason, 1992).
Slips and lapses:
Slips and lapses occur in routine tasks with operators who are familiar with the process and are experienced in their work. They are action errors which occur while the task is being carried out and often involve missing a step out of a sequence, or getting steps in the wrong order, and frequently arise from a lapse of attention. Typical examples are operating the wrong control through a lapse in attention or accidentally selecting the wrong gear.
Design improvement is the most effective route for eliminating the cause of this type of human error. For example, typical problems with controls and displays that cause this type of error (ie operating the wrong switch) include:
- switches that are too close and can be inadvertently switched on or off
- displays which force the user to bend or stretch to read hem properly
- critical displays that are not in the operators field of view
- poorly designed gauges
- displays which are cluttered with non-essential information and are difficult to read.
Mistakes are inadvertent errors that occur when the elements of a task are being considered by the operator. They are decisions that are subsequently found to be wrong, although at the time the operator would have believed them to be correct. There are two types of ‘mistake’ (HSE, 1999), namely rule based and knowledge based. Rule-based mistakes occur when the activity is governed by a series of rules. The error occurs when an inappropriate action is tied to a particular event. Knowledge-based errors occur in entirely unfamiliar situations where the operator has to rely entirely on adapting his/her basic knowledge and experience to deal with a new problem.
Training is the most effective way of reducing mistake-type human errors. The risk of a mistake being made will be decreased if the individual understands the need for, and benefits from, safe plans and actions rather than simply being able to recite the steps parrot-fashion. Training should be based on defined training needs and objectives, and should be evaluated to see if it has had the desired improvement in performance.
Violations:
Violations are any deliberate deviations from the rules, procedures, instructions and regulations, which are deemed necessary for the safe or efficient operation and maintenance of plant or equipment. Examples include driving too fast or removing guards on moving equipment. Violations occur for many reasons and are seldom wilful acts of sabotage or vandalism. The majority stem from a genuine desire to perform work satisfactorily given the constraints and expectations that exist. HS(G)48 (HSE, 1999b) makes a distinction between routine, situational and exceptional violations. Routine violations are ones where the violation has become a normal way of working, while situational violations occur due to the pressures of the job at that time. There is no single best avenue for reducing the potential for deliberate deviations from safe rules and procedures. They should be considered in terms of reducing an individual’s motivation to violate. These may include:
- underestimation of the risk
- real or perceived pressure from the boss to adopt poor working practices
- pressure from workmates to adopt their poor working practices
- cutting corners to save time and effort.
Latent failures are the underlying causes of accidents and are failures that lie in the system that are in turn triggered by these active failures. They are made by people whose tasks are removed in time and space from operational activities. Common examples of latent failures include (HSE, 1999):
- poor design of plant and equipment
- ineffective training
- inadequate supervision
- ineffective communications
- uncertainties in roles and responsibilities.
In September 2001 a major research project was initiated at the Camborne School of Mines in order to identify the specific latent failures in the quarrying industry by looking at the potential for active failures through auditing as well as studying accident reports (Foster, 2001). Latent failures are crucially important to accident prevention for two major reasons. First, if they are not resolved, the probability of similar or repeat events will be high, regardless of what other action is taken to correct the active failure. Secondly, as one latent failure often influences several potential active failures, removing latent failures can be a very cost-effective route to accident prevention.
One of the principal ways of systematically reducing the potential of latent failures is through a health and safety management system. This will be the subject of the next article in this five-part series.
References
BAKER, G.: ‘Hard targets’, paper presented to the QNJAC, March 2002.
BIRD, F.E., and G.L. GERMAIN: ‘Practical loss-control leadership’, International Loss Control Institute, 1986, Loganville, Georgia.
Department of Transport (1988a), ‘Investigation into the King’s Cross underground fire’, HMSO, London.
Department of Transport (1988b), ‘Formal investigation: The Herald of Free Enterprise’, HMSO, London.
Department of Transport (1989), ‘Inquiry into the Clapham Junction rail accident’, HMSO, London.
FOSTER, P.J.: ‘Accident aetiology in the quarrying industry’, paper presented to the QNJAC, October 2001.
HARMS-RINGDAHL, L.: ‘Safety Analysis — Principals and practices in occupational safety’, 1993, Elsevier.
HEINRICH, H.W., PETERSON, D., and N. ROOS: ‘Industrial accident prevention’, 5th edition, McGraw Hill, 1980, New York.
HOYOS, C.G., and B. ZIMOLONG: ‘Occupational safety and accident prevention’, Elsevier, 1988.
HSC (1993), ‘Organizing for safety’, 3rd report of the Human Factors Study Group of the Advisory Committee on the Safety of Nuclear Installations, HSE Books.
HSE (1997a), ‘The cost of accidents at work’, HS(G)96, 2nd edition, HSE Books.
HSE (1997b), ‘Successful health and safety management’, HS(G)65, 2nd edition, HSE Books.
HSE (1999a), ‘The costs to Britain of workplace accidents and work-related ill health in 1995/96’, HSE Books.
HSE (1999b), ‘Reducing error and influencing behaviour’, HS(G)48, HSE Books.
MASON, S.: ‘Practical guidelines for improving safety through the reduction of human error’, The Safety & Health Practitioner, 10(5), 1992.
PEARCE, R.: ‘Personal communication’, 2002.
REASON, J.: ‘Human error’, Cambridge University Press, 1990.
SIMPSON, G.C.: ‘Human error in accidents: Lessons from recent disasters’, Proceeding of the Symposium on Safety, Hygiene and Health in Mining, The Institution
of Mining Engineers, Doncaster, 1992.
SCOTT, A.: ‘Killing off errors’, Mine & Quarry, 1995, vol. 24, no. 9, pp14–18.
SHILLITO, D.: ‘Incident investigation in environmental performance improvement — the jigsaw puzzle’, Environmental Protection Bulletin 25, 1994.
TAKALA, J.: ‘Global estimates of fatal occupational accidents’, International Labour Office Document ICLS/16/RD8, Geneva ILO, 1998.
The author, Dr Patrick J. Foster, is Anglo American plc lecturer in mining engineering at Camborne School of Mines, University of Exeter