A Time For Change
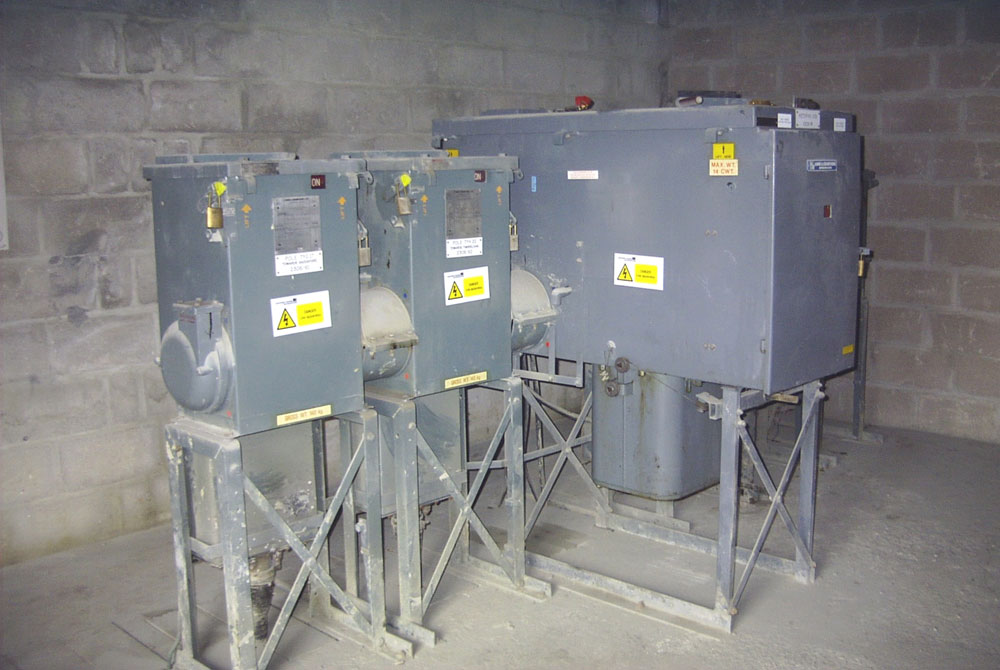
The safety of electrical installations at quarries
The Health and Safety Executive guidance on electrical equipment for quarries is about to be changed. The Approved Code of Practice — The Use of Electricity in Quarries — will be withdrawn and a guidance note — Electrical Safety in Quarries — will be issued in its place.
The guidance note will provide practical guidance on electrical safety in higher-risk areas of quarries and is intended for quarry management rather than electrical experts. For electrical engineers, the guidance note will provide a framework for the safe management of electrical equipment in quarries but will not contain information on detailed electrical requirements.
The guidance note seeks to move the quarrying sector away from the traditional ‘manager’s scheme’ required by former quarry electrical regulations to a comprehensive ‘operator’s safety management system’ for electrical installations as required by the Quarries, Electricity at Work, Management of Health and Safety at Work and other regulations.
This article discusses the background to electrical safety requirements at quarries, the ‘operator’s safety management system’ and compliance with the relevant health and safety legislation.
Background to legislation and quarry electrical practices
The first electrical regulations for quarries were introduced in 1938. These were written in a prescriptive format, requiring the quarrying sector to comply with absolute requirements. Although the 1938 regulations were replaced by the Quarries (Electricity) Regulations 1956 (QER), the main requirements remained unchanged:
- all cables above 25V to be armoured or to have metallic covering
- the cable armour or metallic covering to have a conductivity of not less than 50% of the largest conductor of the cable
- insulation resistance to restrict leakage current to one ten-thousandth part of the maximum current
- periodic tests of insulation resistance and the conductivity of the earthing conductor at not less than six months
- report of tests to be on M&Q 260.
The periodic testing and with inspection of installations provided the basis of what was called a ‘manager’s scheme’, which still is in place at many quarries today. At most (but not all) sites six-monthly tests of 50% conductance and insulation resistance were carried out religiously and compared with the requirements of the Quarries (Electricity) Regulations. Where in-service inspection bodies associated with insurers, or others, carried out the work, inspections were also made of equipment and defects identified for remedy (or not) at a later date.
The six-monthly tests of insulation resistance and conductivity did not ensure safety. It was possible to have 50% conductance or more on a circuit but for the circuit to be dangerous should a fault occur.
Other tests had been developed which could show whether a system was safe but these were not used in quarries because of inertia and the prescriptive requirements of quarries’ law. The tests made under the ‘manager’s scheme’ had remained unchanged since 1938, had not benefited from any technical progress, were costly and did not provide sufficient information to say whether or not an installation was safe.
The Quarries (Electricity) Regulations 1956 were replaced by the Electricity at Work Regulations 1989 and an Approved Code of Practice: The Use of Electricity at Quarries. The purpose of the ACoP was to provide practical guidance on compliance with the regulations — in essence the guidance given was to retain the culture of the ‘manager’s scheme’. The introduction of further legislation over the past 10 years or so has exposed the ACoP further. It is now outdated and provides inadequate practical advice to operators on the application of the Electricity at Work Regulations and must be withdrawn.
Current legislation applicable to quarry electrical installations
Much of the legislation governing health and safety at work has resulted from membership of the European Community, particularly implementation of Directives dealing with a common standard for workplace health and safety and the single internal market. Directives have been adopted and implemented into UK legislation, including the following:
- Management of Health and Safety at Work Regulations 1999
- Provision and Use of Work Equipment Regulations 1998
- Quarries Regulations 1999
- Supply of Machinery (Safety) Regulations 1992
- Electrical Equipment (Safety) Regulations 1998
The above legislation operates in conjunction with existing acts and regulations such as:
- Health and Safety at Work etc Act 1974
- Electricity at Work Regulations 1989
All of the above sets of regulations work together as an integrated package of regulations detailing requirements to have a management system in place which ensures that electrical installations are properly managed in such a way that the installation is safe at all times. The management system must ensure that electrical installations are designed, used and maintained so as to be safe. This may best be achieved by having a comprehensive ‘operator’s safety management system’, to ensure that compliance with the above legislation can be demonstrated.
Guidance is given by the HSE on effective safety management systems in HS (G) 65 ‘Successful Health and Safety Management’. A model of an ‘operator’s safety management system’ for electrical installations is set out in figure 1. It has been developed to meet the requirements of the Quarries, Electricity at Work and other regulations mentioned above, and HS (G) 65 ‘Successful Health and Safety Management’.
An operator’s safety management system may be used in quarries and plants not subject to the Quarries Regulations, in which case it becomes an employer’s safety management system.
The health and safety document and employer’s health and safety policy
The purpose of the health and safety document is to provide practical information to persons working at the quarry about the safety measures used and the roles of the persons responsible for implementing the safety measures. The document is the operator’s declaration of how the quarry will be managed with regard to health and safety, in other words it is the operator’s health and safety management system. It must cover all activities, including the use of electricity, and give detailed information on how electrical safety is managed.
For plants outside the scope of the Quarries Regulations, the operator’s (or more correctly, the employer’s) safety management system holds true. It details the health and safety arrangements, management structure and systems and measures concerning the design, use and maintenance of the electrical equipment as required by the Health and Safety at Work etc Act 1974 and subordinate legislation.
The details of what must be included in a health and safety document are set out clearly in Regulation 7 of the Quarries Regulations 1999. The requirements apply equally to all risks including the use of electricity. The health and safety document should include details of how the risks from electricity are dealt with and contain information dealing with the following measures:
- management
- design
- safe use
- examination, maintenance, inspection and testing.
Measures concerning the management of the electrical systems
Management structure
The way electrical systems are managed governs whether systems are safe or not. The person(s) responsible for ensuring the safety of the electrical equipment at any particular site must be clearly identified in the management structure set out in the health and safety document. Electrical safety is a complex topic and requires technical knowledge and experience to be certain that all matters are dealt with correctly. Where a person is identified in the management structure as being responsible for electrical systems but is not himself competent in electrical matters, he should appoint a competent person who has the necessary technical knowledge and experience to advise on electrical safety matters.
Responsible electrical person, authorization and duties of competent electricians etc
At all quarry and non-quarry sites it is advisable to have one or more persons (whether a contractor or not) identified as the responsible electrical person for the site whose duties include advising the operator on electrical matters and managing all work on the electrical system. The responsible electrical person should be authorized in writing as to his/her duties, clearly defining what he/she is and is not responsible for. The responsible electrical person should authorize all other persons, including contractors, who carry out work on the electrical system at the quarry, ensuring that they are competent to carry out the work and have the appropriate equipment, including suitable test instruments, to allow them to carry out the work safely.
It is a management responsibility to ensure that all accidents and near misses are properly and thoroughly investigated so that a prime cause can be established and action taken to prevent similar occurrences. Where events are reportable to the HSE, or where a claim may be made against the operator, the operator’s health and safety advisor, supported by a competent electrical engineer, should carry out the investigation.
Risk assessments
In the most commonly used risk assessment methodology, risk is defined as the product of a number of qualifying factors including chance and maximum probable injury. For electrical work minor incidents can result in death through electrocution or serious burns through short-circuiting. To have an acceptable risk assessment in these circumstances, the chance of an accident happening must be, at least, very unlikely and at best, impossible. The control measures used for electrical work must, therefore, be adequate to prevent the likelihood of contact with live parts or of causing short circuits when persons are near the conductors.
It is clear from enforcement action taken by the HSE that risk assessments for electrical work are seldom carried out and when they are, they are not performed correctly. It has been the experience of the HSE that countermeasures employed by electricians rely as often as not on chance as they do on the use of effective control measures to prevent accidents.
It is evident from the above that quarry operators cannot rely on electrical technicians or electrical contractors for ensuring that risk assessments are adequate; it is the operator’s duty to comply with the requirements and, therefore, it is for the operator to ensure that the risk assessments are adequate.
The responsible electrical person should therefore ensure that generic risk assessments have been completed and are included in the health and safety document for all work involving potential contact with live conductors. In any particular case, work should be carried out in a manner detailed in the generic risk assessment or, where different conditions apply, a job-specific risk assessment/method statement should be completed. A non-exhaustive list of generic risk assessments may include the following:
- use of electricity at the quarry
- operation and use of high-voltage equipment, including maintenance
- periodic inspection and testing of all installations and equipment
- operation and use of low-voltage equipment
- fault finding on live low-voltage equipment
- testing isolated equipment to prove it to dead
- protection against contact with overhead lines and underground cables
- installation of equipment including cables
- access to equipment at high levels
- off-site risks from overhead line contacts by drivers of quarry-owned vehicles and contracted vehicles.
Where contractors are used to carry out work, it is essential that adequate risk assessments and/or method statements are documented and the safety procedures agreed between the quarry operator and the contractor before work starts.
Measures concerning the design of an electrical installation
Integrity of equipment
Electrical equipment that has been properly designed, constructed, installed and maintained does not present a risk of electric shock or burn injury when properly used. The general requirement for the design and construction of electrical equipment is that it is suitable for its intended use and the environment in which it is to be used.
Electrical equipment is susceptible to failure from water and dust ingress, damage by impact and general deterioration, and should therefore be pro-tected from these effects by installing it in a dry environment free from the risk of damage or in suitable weather-proofed and protected enclosures.
Electrical equipment should be constructed in accordance with relevant British, CENELEC and IEC standards and should be marked with an appropriate CE marking. Of particular importance is the requirement of the Provision and Use of Work Equipment Regulations 1998 relating to machinery control systems. The control systems, including emergency stops and interlocking systems for safety guards and gates, must ‘fail to safety’ in the event of a fault. It is important that new and existing machinery is assessed to see if the safeguards provided give adequate protection. Where they do not comply the control systems should be modified to ensure failure to safety.
All installations, including those for the control of motor drives, must be capable of being effectively isolated by readily accessible, lockable isolating switches. The means of isolation (isolating switches, fused isolators, circuit-breakers etc) must be capable of being locked in the ‘open’ or ‘off’ position and clearly labelled to show the equipment or circuit that it controls.
Equipment must be designed to withstand all foreseeable excess currents and protected against faults such as short circuits, earth faults, sustained overloads etc. The electrical protection used, whether simple fuses or complex tripping systems operating circuit-breakers, should be set at the correct level to trip in the minimum time consistent with avoiding nuisance trips.
The design of switchboards is an important feature for electrical safety. Switchboards must be safe when being commissioned, tested and maintained. To ensure that such equipment is safe when commissioning or fault-finding is being carried out the risk of contact with dangerous live parts should be prevented. The internal conducting parts of switchboards should be arranged so that when the doors are opened, all live conductors over 50V inside the switchboard are covered so that accidental contact cannot occur. It would be advantageous to build integral test circuits into motor-control switchboards to allow the testing of control circuits (normally live at 110V) without the power circuits being energized.
High-voltage systems
High-voltage (HV) equipment is technically complex and, if not correctly managed, can be a source of great danger. All high-voltage systems should be placed under the control of a competent engineer (whether contracted or not) who has the necessary training and experience to properly design, use and manage the HV system on behalf of the operator.
Installation standards
The normal guidance for low-voltage electrical installations, BS7671 – Requirements for Electrical Installations (the IEE Wiring Rules 16th Edition), was not commonly used within quarries until relatively recently. It is now generally accepted that BS7671 should be the governing standard for the safety of electrical installations within quarries, and all electrical equipment within quarries should now be installed to be in compliance with the requirements of this standard.
For all quarries, excluding offices, mess rooms and weighbridges, the part of BS7671 that should be adopted as the standard is that set out in Section 604 - Construction Site Installations. For offices, mess rooms and weighbridges the part of BS7671 that should be adopted is that for general applications.
The goal-setting requirements of the Electricity at Work Regulations allow advantage to be taken of technical progress with the advantages of better systems at lower costs for the sector. These advantages can be seen in the cost of cables; three-core armoured ‘M&Q Regulations’ type cables cost 50% more than modern four-core cables which do not comply with M&Q Regulations but which provide better earthing and insulation and are readily available from stockists.
Where contractors carry out work installing electrical equipment at quarries, the competence of the contractor should be assessed. They may be accredited by NICEIC (National Inspection Council for Electrical Installation Contractors), holders of the safety passport issued by EPIC or separately assessed by a competent engineer. In all cases, contractors should issue completion certificates when installations are completed; the completion certificate should conform to that in Appendix 6 of BS7671.
Earthing of electrical installations
Proper and effective earthing of the electrical system at all quarries is necessary to ensure the safety of the electrical installation. There are a number of ways of earthing an electrical system at a quarry; the quarry may have its own separate earthing point to which the supply system is connected or the electricity distribution company (formally called the regional electricity company) may provide an earthing connection to which the quarry supply system will be connected. Whichever system is in place the earthing must be properly designed to ensure that the system is disconnected safely when a fault develops.
For earthing to be effective, the resistance of all earth paths from any equipment must be sufficiently low to ensure that, should a fault occur, the power will be disconnected in as short a time as possible. For quarries, the time taken to disconnect a circuit within the quarry and plant areas should be no more than 0.2s, and for offices, weighbridges and mess rooms no more than 0.4s.
Residual-current circuit-breakers (RCDs) should be used to protect all 230V circuits within offices, weighbridges and mess rooms. In other areas it is recommended that earth-fault protection be fitted to main circuits.
Measures concerning the safe use of equipment
In the past the majority of serious electrical accidents within quarries occurred when electrical staff were working on electrical equipment without taking adequate precautions to ensure their safety. When the work was being carried out on dead equipment, the equipment should have been properly and effectively isolated. When the work was being carried out on live equipment, such as diagnostic testing to locate a fault, the safety precautions taken should have been sufficient to prevent an accident.
The measures concerning the safe use of equipment identified in the health and safety document should include written procedures for the effective isolation of electrical equipment and machinery, procedures for work on or near live equipment, and permits to work.
Isolation procedures
A great number of accidents occur in all industries, including quarries, when electrical equipment or machinery is not isolated when work is being carried out on or near it. It is of crucial importance that proper isolation takes place before work is carried out on any equipment. Effective rules for the isolation of electrical equipment, sometimes called plant lock-off procedures, will provide the necessary framework for such proper isolation. Where possible, the isolation rules for electrical equipment should be incorporated within the site lock-off procedures. Where this cannot be achieved separate electrical procedures should be drawn up. For sites with high-voltage equipment, separate HV isolation rules, including HV permits to work, will be necessary.
Isolation is defined as the disconnection and separation of the equipment from every source of energy or harm in such a way that the disconnection and separation is secure. The procedures must ensure that equipment cannot be made live or machinery does not move while it is isolated.
The isolation rules for low-voltage equipment require that work should not be undertaken on equipment unless it is:
- dead
- isolated at all points of supply, locked in the off position and caution notices applied
- verified as being dead at the point of work by measurement or with voltage indicators which have ??been proved before and after the verification
- where appropriate, released for work by a permit to work.
The isolation may be carried out by competent electricians authorized to undertake low-voltage isolations.
For high-voltage equipment additional precautions are necessary to prevent danger. Work should not be undertaken on any high-voltage equipment unless it is:
- dead
- isolated at all points of supply, including voltage transformers, locked in the off position and caution notices applied
- connected to earth at all points of isolation and if not in sight of a point of isolation, earthed at the?point of work
- screened from all adjacent live equipment, with ‘danger live’ notices applied to all live equipment
- released for work by the issue of a permit to work; the permit must be issued to the person in charge of the working party.
A person with relevant high-voltage competence, normally authorized as a senior authorized person by the operator, should carry out the isolation and issue of the permit to work. It is important that high-voltage permits to work are reviewed and authorized by the competent electrical engineer to ensure that isolation rules are strictly observed.
Live-work procedures
The live-working procedures should be drawn up to detail when work on or near live equipment is allowed and what precautions should be in place to ensure that the work is carried out without the risk of injury. Work on or near live low-voltage equipment should not occur other than in exceptional circumstances. The work should not be carried out unless agreed by the person identified in the management structure and a risk assessment or method statement has been agreed prior to the work. In many quarries a special test arrangement is designed into motor-control switchboards allowing testing of low-voltage, low-power circuits with the main power being isolated. Such an arrangement allows electrical staff to undertake fault-finding without exposing themselves to the risk of serious burn injuries from high-power circuits. It would ‰ be advantageous if all quarries could introduce such a feature in new and existing motor-control switchboards.
The operator should draw up live-working rules which must detail the precautions necessary for live work. The precautions usually comprise the following:
- the equipment being worked on is safe to work on and all conductors are covered or screened so that they cannot be touched or have tools dropped on them
- test leads and probes are fitted with fuses, in accordance with HSE guidance note GS38, and ??tools are insulated
- persons are competent to undertake the work and recognize the precautions necessary to avoid danger.
Written scheme of systematic examination, inspection, maintenance and testing
Periodic examinations, inspections and tests have been a requirement of quarries law for over 125 years and are continued in the Quarries Regulations 1999. The objective of periodic examinations etc is to ensure that work places and equipment are safe, in other words maintained in an efficient state, in efficient working order and in good repair. Not all defects can be identified by inspection — it is necessary to carry out tests on parts of the installation, particularly on earth-fault paths and electrical protection systems, to ensure that the equipment is safe.
Maintenance of electrical equipment is necessary to ensure safety and for the prevention of loss. The degree of maintenance will depend on many factors such as safety, duty of equipment, potential loss etc. It is necessary to have a comprehensive preventative-maintenance system that includes periodic examination, inspection and, where appropriate, testing to ensure safety and productivity are maintained.
The written scheme of examination, maintenance, inspection and testing required by the Quarries Regulations 1999 should be in line with the new guidance note issued by HSE, with a proviso that operators should select the frequencies following an assessment of the risks at the site. Where insurance companies or contractors carry out the work it is important that the operator dictates what will be done rather than letting others decide on what will ultimately be the operator’s responsibility.
By ensuring an effective examination, maintenance, inspection and testing system, it will be possible to reduce the disruption caused by the testing in particular, having most of it conducted during normal working hours, thereby reducing costs. An example of testing with suggested frequencies includes the following:
- earthing and bonding of highrisk moveable plant six months
- earthing and bonding of other plant between six and 12 months
- earth-loop impedance and disconnection times — between six and 12 months
- earth electrode resistance — 12 months in dry periods.
Conclusions
Electrical installations in quarries can be a source of great danger if not properly managed. It is no longer appropriate to use the ‘manager’s scheme’ to ensure compliance with revoked regulations; what must be used is a comprehensive ‘operator’s safety management system’ for electrical installations in line with the model shown in figure 1.
The former prescriptive regulations have been revoked and goal-setting regulations put in their place. A change to the engineering practices adopted in most other sectors can be used with the advantage of lowering costs and maintaining or improving standards. It is time for the industry to change to a comprehensive safety management system.
Acknowledgement
The author wishes to thank to Mr J. A. McLean, Health and Safety Executive, and Mr B. Holmes, Brian Holmes Associates, for their assistance in the preparation of this article.
The author, Windsor Coles, is former Principal Electrical Inspector with the Health and Safety Executive. He is currently a consulting engineer working principally in the quarrying and allied industries