A Practical Guide to Dust Suppression
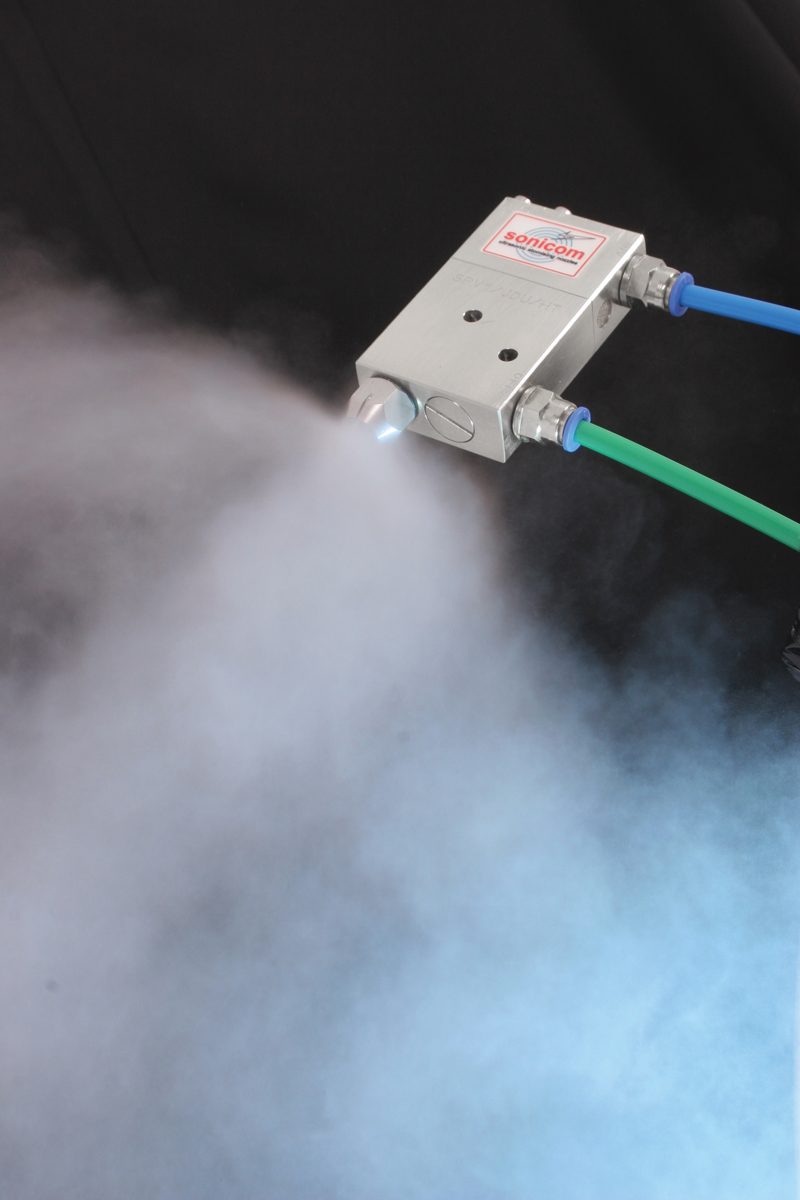
First published in the December 2015 issue of Quarry Management
JD Ultrasonics examine some of the key methods and technologies used to combat airborne dust
When silica, limestone, cement, coal, aggregate and other respirable dust particles ranging in diameter from 0.1 to roughly 70 microns are airborne, they become an occupational nuisance, not to mention health hazard. As a source of physical discomfort, lost materials and wear on conveying pulleys, idlers, belting and motors, such dust is a significant factor in reduced productivity and added operating costs.
Conveyor transfer points are a prime source for fugitive material, both as spillage and as airborne dust. Although it is unlikely that dust can be completely eliminated, a change in system design or production technique will minimize the amount of dust produced. However, since this may not always be possible, dust-suppression systems must also be employed.
DUST SUPPRESSION
Dust suppression is the application of water and/or chemicals either to the body of material to prevent fines from being carried off into the air, or to the air above the material to return fugitive airborne fines to the material bed. There are a number of systems used for this purpose, ranging from ‘garden hose’ technology, through water and surfactant sprays, to foam- and fog-generation systems. These various suppression technologies call for different volumes of moisture to be added.
Wet suppression
By wetting the fines, the weight of each dust particle is increased so they are less likely to become airborne. The moisture creates larger, heavier groups of particles and makes it more difficult for air movement to carry away the dust particles.
This can be achieved by applying water through a series of properly sized spray nozzles at a point where the material expands and takes in air, such as during discharge from the head drum in a transfer chute. Water can also be applied to create a ‘curtain’ around a transfer point, so any dust fines that become airborne come into contact with the water sprays surrounding the open area around the chute.
The effectiveness of water spray systems is dependent on the velocity of applied water, the size of the nozzle orifice and the location of the spray nozzles. The most effective sprays come from low-velocity systems, as high-velocity air movement can keep dust particles in suspension.
The techniques to improve plain water spray dust suppression include a reduction in droplet size, an increase in droplet frequency, an increase in droplet velocity, or a decrease in droplet surface tension, making it easier to merge with dust particles.
The application of dust-suppression water and/or chemicals at transfer points must be controlled automatically so that water is applied only when the conveyors are running and there is material present. This can be accomplished with conveyor system interlocks and other sensors, including microwave (or similar) sensors that read both material on the belt and loaded belt movement.
Unfortunately, however, the application of water has several liabilities that need to be considered.
For example, many bulk solids are hydrophobic, so to achieve effective suppression, more water is used. Uneven or patchy absorption can lead to material build-ups on chute walls, screens and conveyor belts. For mineral handling in general, the addition of excess moisture prior to screening can cause material to adhere to a screen cloth, blinding the equipment. Excess water may promote belt slippage and increase the possibility of wet (and hence sticky) fines accumulating within chutes and around the transfer points.
Excess moisture in the material can also downgrade future performance in power generation or other thermal processing. Specifically, excess water addition to coal and coke used for boiler fuel results in a BTU penalty. The more water added, the greater this penalty.
Methods to improve dust suppression while limiting the addition of water include the use of a ‘dry fog’ or the addition of surfactant chemicals to water, which is then applied as a spray or foam. To improve the wetting characteristics of water, reduce overall water usage and minimize the drawbacks associated with excessive moisture addition, it is a common practice to add chemical surfactants, though these are not always desirable additions.
Dry-fog suppression
An ultra-fine-fog suppression system acts like a fabric filter in that a dust particle cannot pass through it without colliding with a droplet. Atomization reduces the surface tension of the water droplets while increasing the number of droplets in a given area, thus eliminating the need for the addition of surfactants or other additives. The reduced amount of water added through the fog/mist systems – typically at 0.01% to 0.05% by weight of the material – generally will not degrade the performance of the material.
The fog should be generated above the dust problem area and contained in a properly designed shrouding to eliminate dissipation as a result of wind. Dust control is achieved only at the point of application, so several fogging devices may be required for a conveyor system with multiple transfer points.
With fog, foam, water and water/chemical spray applications, the sites chosen for nozzle placement and suppressant delivery patterns are as important as the selection of material to be applied. Even the best-designed programme will fail if the suppressant material is not delivered to the correct location to allow intimate mixing with the dust fines.
Other systems
Sprinklers: Used mainly where wetting is required over a wide area, such as roadways and open yards.
Rain guns: Dust-suppression rain guns have been specifically designed to provide immediate and efficient dampening/wetting over large areas with minimal water consumption. Sprinklers and rain guns can be used together to achieve an overall suppression effect over areas of concern and provide the best-possible results with budget costs and water conservation in mind.
Water spray nozzle systems: These types of nozzle systems are a low-cost option for material-handling processes/site boundaries where wetting is not a problem.
Fog cannon: When vast open spaces require dust suppression and a semi-permanent system is not a practical option, the solution may lie with the introduction of a fog cannon to the site. These large, mobile units throw the droplets many metres towards the source of the dust activity. The droplets scatter in a plume of relatively soft spray and can capture fugitive dust before it becomes airborne and a major problem. QM
Edited from ‘A Practical Guide to Dust Suppression’, by David Blyth of J D UltraSonics Ltd. A full copy of the guide and catalogue can be downloaded here
- Subscribe to Quarry Management, the monthly journal for the mineral products industry, to read articles before they appear on Agg-Net.com