Sand-Ballasted Flocculation Technology
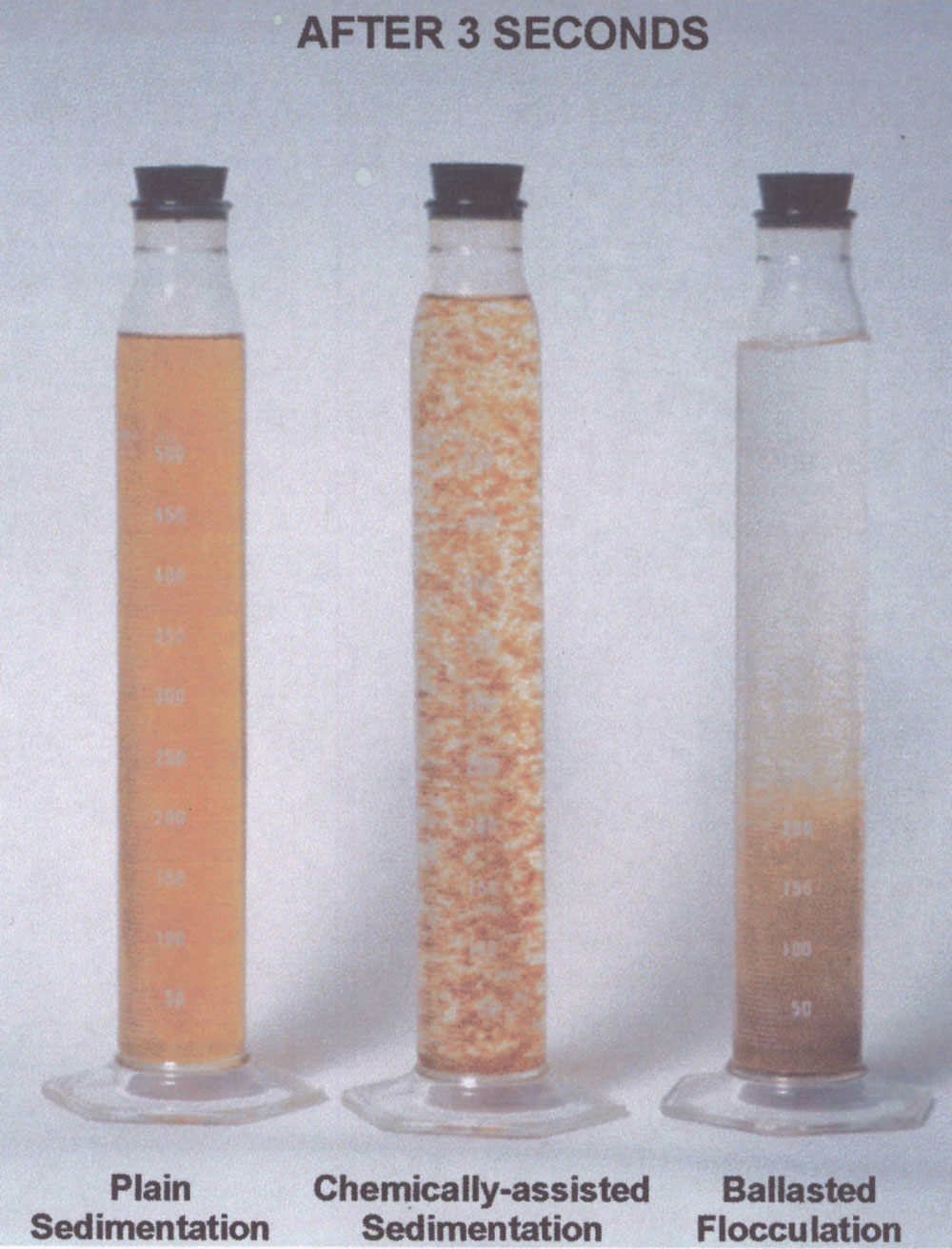
An answer to contaminated water problems
By Philippe Sauvignet
Contaminated waters can harm the environment, and in particular when excavations are carried out there is a high risk of polluting local surface streams or creating highly coloured and turbid run-off. Surface waters are readily contaminated by silt and clay particles and colloidal matter associated with organic debris. These contaminants frequently attract the attention of downstream neighbours and, if they persist, the Environment Agency. Sometimes there is no need to treat these flows immediately or in situ but all too often this is essential. The ideal solution is to treat the effluent as it arises and discharge it to the receiving watercourse fully treated and compliant, thereby causing no harm to the aquatic environment. A frequently adopted solution is the construction of simple settlement chambers or lagoons, but these are notorious for overflowing, leakage or sudden failure and are seldom an effective and secure solution to a difficult problem.
ACTIFLO TO THE RESCUE
The Actiflo system, developed and patented by OTVB’s parent company, Veolia Water Systems, provides an answer to a wide range of contaminated water-treatment requirements. The patented system is based on a sand-ballasted flocculation process combined with simple lamella settlement.
Theory
Actiflo utilizes ballasted flocculation in conjunction with chemical coagulation to rapidly enhance solid–liquid separation. The principal benefits of ballasted flocculation relate to two physical effects induced by the presence of the ballast:
- High specific gravity ballast (normally fine sand) adds weight to the flocculated particles leading to solids settling velocities in excess of 10 times faster than conventional physical–chemical flocculation processes.
- High collision frequencies between the ballast and the flocculated particles dramatically increase the flocculation kinetics, resulting in very short mixing times and a high throughput.
These two effects combine to yield a small-footprint solution with total hydraulic retention times of less than 10min and solids removal efficiencies far in excess of conventional physical–chemical processes.
A simple demonstration clearly and dramatically demonstrates the differences between plain sedimentation, physical–chemical sedimentation and Actiflo-ballasted flocculation settling (fig. 1). In this simple experiment a commonly available ferric sulphate solution is used to produce a ferric hydroxide precipitate to mimic highly coloured and contaminated water. Three graduated cylinders are filled with equal amounts of this solution. The first (left) cylinder has no other chemicals added to it, the second (middle) cylinder has 5mg/litre of a high molecular weight polymer added, and the third (right) cylinder has 5mg/litre of the same polymer and 5% (v/v) of ballast (100µm diameter sand) added. The cylinders are agitated and allowed to settle.
Even after three seconds the ballasted flocculated sample shows significant settling while the chemically assisted sedimentation sample shows floc formation but no settling. After just eight seconds have elapsed the ballasted flocculation sample is fully settled with a clear supernatant and a distinct sludge layer. Settling velocities of over 150m/h have been observed with the ballasted flocculation process as against approximately 1–2m/h settling velocities for conventional physical–chemical flocs. This simple and easily repeated experiment conclusively illustrates both the high settling velocity and the improved solids removal capabilities of ballasted flocculation as utilized in the Actiflo system.
The process train
A coagulant comprising a metal salt — typically ferric iron or aluminum or starch polymer, depending on the requirement — is added to the raw water. The coagulant is added either in-line or in an additional coagulation tank. The dosed water is then fed into an injection tank where the microsand is added and mixed thoroughly. The sand is a specific quartz product (Actisand) with a grain size of 60–180µm. From the injection tank the water continues to a maturation tank and a flocculant is added in the form of an organic polymer. The polymer binds the microsand and the primary particles to form large, settleable flocs. Following flocculation, the water is fed to the lamella separator and here the flocs settle rapidly due to the microsand, which makes them much heavier than in conventional precipitation systems. The Actiflo has an up-flow velocity in the lamella separator some 10–40 times higher than in conventional precipitation plants.
PACKAGE PLANT AND MOBILE FACILITIES
OTVB believe there is considerable potential for the Actiflo process in both new and existing large- and small-scale quarry sites, from small contaminated run-offs requiring temporary treatment before discharge into the local environment to more elaborate facilities treating long-term contamination. Over the years the company have developed and refined the Actiflo product range with the introduction of compact mild steel and stainless steel modular/mobile units. The compact steel units are particularly appropriate for applications where space and construction programme constraints are present. Easily transported by road, the units are also appropriate for larger throughput requirements because of Actiflo’s impressive capacities when compared to the more conventional types of treatment — typically traditional settlement lagoons or settling/flotation units. The compact units are fabricated, fitted-out and tested off-site in a controlled workshop environment before being transported to site for offloading on to precast concrete foundations. OTVB are able to provide a full range of scope of supply for these units ranging from complete design and build to the company’s standard scope of supply for the process units and associated strategic equipment.
The Actiflo package plants are available in four unit sizes, the smallest handling 30– 80m3/h and the largest being able to handle up to 600m3/h. It is possible to combine several units in order to achieve an even greater throughput (up to four units side by side).
SUPPLY AND OPERATION OF ACTIFLO PLANT
The Actiflo package(s) can be hired for any length of time from one month to one year or more and includes the following:
- preparation of the unit for a site-specific application as well as calibration of the instruments
- delivery to and removal from site, including craneage on to a suitable base
- provision of suitably qualified operatives to manage the operation of the unit, provide technical advice, take samples and maintain records
- use of all mobile plant on-site including laboratory equipment and consumables
- provision of a process chemist to carry out one set of jar tests to define the expected performance of the mobile plant based on representative samples of the contaminated water input
- provision and installation of clarified water discharge connections and sludge discharge pipeline ??connections and any measures for the return or disposal of water and sludge to ground level adjacent to the unit
- provision of a coagulant suitable for the application
- maintenance of the units and the provision of microsand (Actisand S or P) and provision of a suitable polymer
- attendance of one of OTVB’s senior technical representatives at progress meetings.
To date there are more than 200 Actiflo plants operating worldwide, with capacities of up to 24m3/s (2,073 million litres per day). Developed to treat both potable and waste water, Actiflo is a stable and efficient process that is able to meet stringent effluent standards even under great load variations. With ever-increasing pressure to protect the environment and meet stringent regulatory requirements, the process offers quarry operators a highly reliable and technically advanced solution to their pollution-control problems.
OTVB, Aqua House, 2620 Kings Court, Birmingham Business Park, Birmingham B37 7YE; tel: (0121) 329 4000; fax: (0121) 329 4001.