Apprenticeships – Skills for Life
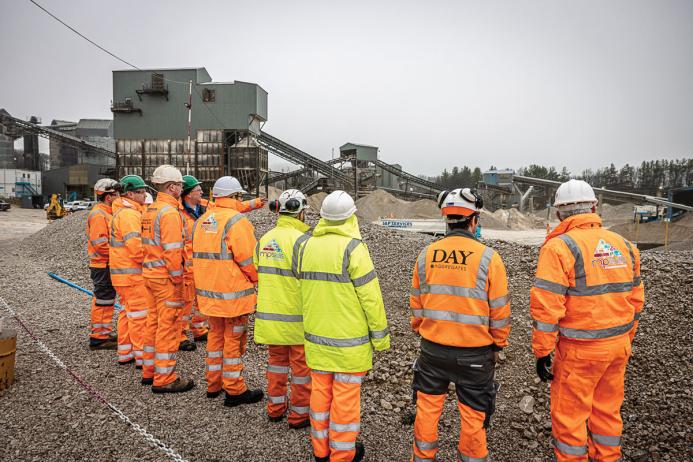
First published in the February 2023 issue of Quarry Management
National Apprenticeship Week brings into sharp focus the value of and need for high-quality apprenticeships within the mineral products industry
Taking place this month (6–12 February) with the theme ‘Skills for Life’, National Apprenticeship Week will bring into sharp focus the value of and need for high-quality apprenticeships within the mineral products industry. The Institute of Quarrying (IQ), Mineral Products Qualifications Council (MPQC) and Minerals Matter are all very active in the apprenticeship space, engaging with National Apprenticeship Week events including the Big Assembly, which was broadcast live to more than 100,000 people across the UK and hosted at the National Stone Centre in Wirksworth, Derbyshire.
Alongside on-the-job training, apprentices spend at least 20% of their working hours completing classroom-based learning with a college, university or training provider, which leads to a nationally recognized qualification.
Modern apprenticeships have long been on the national agenda. The UK Government’s pre-pandemic ‘2020 Vision’ clearly outlined the advantages of apprenticeships, citing them as raising skill levels in the economy, driving productivity, and boosting national prosperity.[1]
For the apprentices themselves, the training they receive is a driver for greater personal economic wealth by gaining additional skills and qualifications as they progress their careers. These benefits can translate into significant cumulative monetary returns for individuals over a working life (average 40 years) – between £48,000 and £74,000 for Level 2 apprenticeships, and between £77,000 and £117,000 for Level 3 apprenticeships.[2] Those completing an apprenticeship at Level 4 or above could earn £150,000 more, on average, over their lifetime.[3] Apprentices are also clear that their apprenticeships have increased their productivity and prospects. Eighty-five percent of apprentices said their ability to do the job had improved, and 83% said their career prospects had improved.[4]
Nationally, across all sectors, in academic year 2021/22, intermediate (Level 2) apprenticeships represented 26.2% (91,500), advanced (Level 3) apprenticeships 43.3% (151,300), and higher (Level 4 and above) apprenticeships 30.5% (106,400). Degree-level (Level 6 and 7) apprenticeships represented 12.4% (43,200) of all starts for 2021/22.[5]
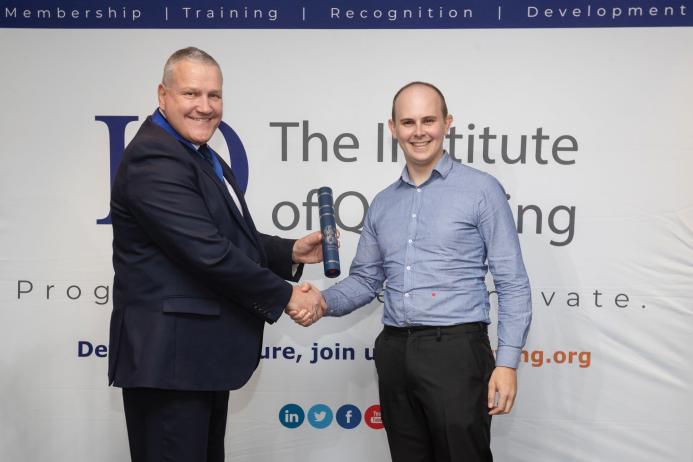
Success stories can be found within the mineral products industry itself, such as Lewis Coxon, University of Derby, Higher Apprentice winner at the 2022 IQ Fellows Awards. His journey outlines one route into the sector, with help from The Institute of Quarrying.
‘I studied the Mineral Extractives Foundation Degree at the University of Derby Centre for Mineral Products; the course was developed in partnership with the Institute of Quarrying,’ said Mr Coxon. ‘At the beginning of the course, I was fresh into a trainee manager role at CEMEX UK. I preferred this route of learning over the NVQ alternative as it offered flexibility when it came to my studies and the opportunity to meet like-minded individuals who were in similar roles.
‘Some sessions were hosted in a classroom setting with an industry-experienced lecturer, whilst other sessions took place online. This offered greater convenience that worked around my work and home life. Throughout the course, I was set assignments to evidence my skills and knowledge in areas such as restoration schemes, site inspections and key responsibilities of a site manager. In addition to my studies, off-the-job training was allocated to me on a regular basis by my employer to ensure I was up to date with my modules.
‘As a result, a few months into my second year of studying I was promoted to quarry manager at CEMEX UK’s Hatfield Concrete Plant and Quarry. The course offered more general information surrounding different aspects of quarry management. Some of the modules, such as accountancy and workforce management, helped ease the transition from my previous role. There were also modules on dealing with asphalt, concrete and electrical equipment. With wider knowledge of all aspects of a working site under my belt, I felt more confident in my role.
‘More recently, I was able to support an assistant quarry manager who had newly joined the business. During their induction I was able demonstrate best practices on site, along with general site maintenance and day-to-day operations. These skills were acquired both from my qualifications and on-site experience.’
Mr Coxon has high future ambitions: ‘I would be interested in pursuing an additional year for my qualification. The extension focuses on certain individual aspects of the industry, such as cement, concrete and asphalt, as opposed to the mineral products industry as a whole. Completing a WAMITAB (Waste Management Industry Training and Advisory Board) qualification is another ambition of mine, as there is a landfill on site.’
The need for more apprentices like Mr Coxon is pressing. Post pandemic, those sectors more prone to wholesale shutdowns have taken longer to bounce back, with apprenticeship numbers down by 25% in manufacturing since 2019/20, and down by 12% in construction.[6]
All this means that there is work to be done, but the good news is that collaborative approaches are happening and bearing fruit.
MP Skills’ latest Level 2 Static and Mobile Plant apprentice cohort recently benefitted from an engaging day at Longcliffe Calcium Carbonates’ Brassington Moor and Ryder Point quarries, demonstrating that industry has a vital role to play in making the apprenticeship experience more job relevant and engaging.
MP Skills trainer Julie Edwards explained: ‘Longcliffe Calcium Carbonates provided an exceptional ‘off-the-job’ experience for our cohort. As soon as we arrived on site, we were welcomed by the management team – operations director Chris Wainwright, health and safety manager Anthony Woodroffe, and quarry manager Jon Murgatroyd. We were given a thorough induction covering geotechnical features of the site and how production works, shown drone footage of the entire operation to explain different parts of the quarry, and given a clear safety briefing. As we were taken to each part of the quarry, discussions and conversations were very relevant to our course training, such as the use of the crushing and screening plant, innovative processing systems, future quarry development, as well as blasting techniques and geotechnical designs.’
Having senior experts devote time and interact with apprentice visits is critical to demonstrating that apprentices are valued.
Commenting on the visit, Longcliffe Calcium Carbonates’ operations director, Chris Wainwright, said: ‘We are continually looking for ways to promote the opportunities offered by the quarrying industry. This was a very positive and effective way to give these students an insight into the work that we do here at Longcliffe. Through the involvement and support of many members of the teams at Brassington Moor and Ryder Point quarries, and in other departments, we were able to present a comprehensive picture of the complex processes we manage in order to make over 100 products for essential markets such as animal feeds, glass, and adhesives.’
Active participation in apprenticeship events is another way to promote the mineral products industry as an exciting career opportunity. That starts within education and is why Minerals Matter, the mineral products industry’s cross-sector approach to future skills, took an active role in the 2023 Big Assembly, in partnership with the D2N2 Local Enterprise Partnership. The Big Assembly is hosted by ASK, the Apprenticeship Support and Knowledge programme for schools and colleges that is funded by the National Apprenticeship Service and the Department for Education. Broadcast live to an invited audience of more than 100,000 people across the UK and hosted at the National Stone Centre (NSC) on 7 February, the event brought together a panel of apprenticeship ambassadors, including support from Longcliffe Calcium Carbonates, to discuss apprenticeships from a variety of angles.
Emily Noble, future skills manager with Minerals Matter, said: ‘We were delighted to support ASK and the Big Assembly team with this fantastic event. Seeing examples of former and current apprentices, hearing their stories, and listening to employers of apprentices and education providers is inspiring. By hosting it at the NSC, we also put mineral products high on the map of opportunity, helping to showcase the industry as being so much more than first meets the eye.’
In addition, Minerals Matter was actively involved in National Apprenticeship Week, supporting the week’s activities online, including a mineral-products-specific webinar with support from Ibstock, Breedon, Hanson, and Cornish Lithium, and a double-page magazine feature in conjunction with Careermag, a renowned career choice publication for school leavers.
‘We need to celebrate our apprentices’ achievements, showing the positive impact they have on businesses and communities. These people will be role models for the next generation and advocates of how a career in the mineral products industry can provide an enriched career,’ added Ms Noble.
So, what of the future of apprenticeships? Discussions will long continue but six key apprenticeship trends for 2023[7] may well be worthy of consideration:
Drive for quality – the need for value-for-money apprenticeships that measure up to need
In-work apprenticeship growth – upskilling those in work, not just recruiting those out of work
More nurturing apprenticeships – creating a clear growth path to retain skilled talent
Data analysts and digital transformation – key drivers for future growth
Cyber talent – needed for essential security
Developing your own sales talent pipeline – in-house training rather than importing salespeople.
Apprentices can be looked upon as future leaders within our sector. Devoting time and energy to their development is, therefore, both essential and exciting.
REFERENCES
London Economics (2011) – BIS Research Paper Number 53, Returns to Intermediate and Low Level Vocational Qualifications
AAT and CEBR (2013) University education – is this the best route into employment?
Apprenticeship Evaluation: survey of learners (2014)
explore-education-statistics.service.gov.uk
FE Week 17 Jan 2023 - https://feweek.co.uk/six-key-trends-that-will-define-apprenticeships-in-2023/
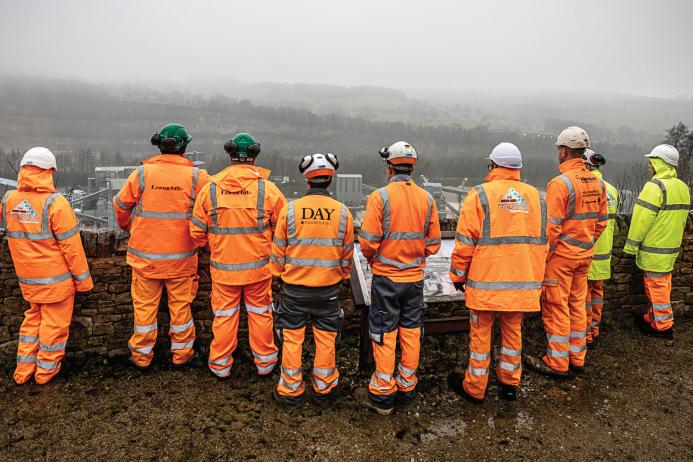
Subscribe to Quarry Management, the monthly journal for the mineral products industry, to read articles before they appear on Agg-Net.com