Using Hydrogen to Support a Low-Carbon Future
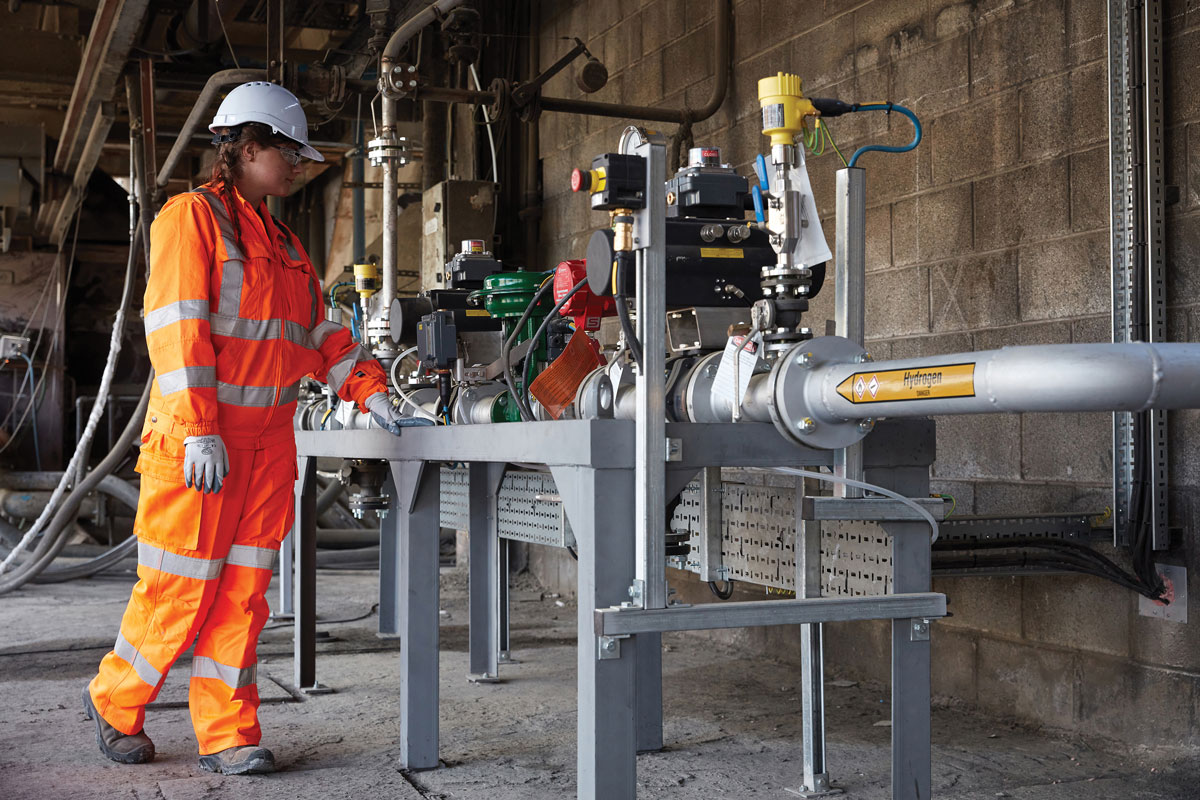
First published in the December 2021 issue of Quarry Management
The UK Government has set out its approach to developing a low-carbon hydrogen sector as part of its plan to ‘build back better’ with a cleaner, greener energy system. Iain Walpole, environmental sustainability manager at Hanson UK, describes three industry-leading hydrogen projects the company is involved with that are important levers in its commitment to reaching net-zero carbon by 2050
Fuel switching to hydrogen has the potential to make significant inroads into carbon-reduction targets and will be key to the future of heavy industry if we are to reach our climate change ambitions.
Hydrogen is a unique fuel as its combustion produces no CO2 – the gas reacts with oxygen to form water and releases energy – which is why it forms a key part of the Government’s industrial decarbonization plans.
In 2019, a feasibility study, made possible by Department for Business, Energy and Industrial Strategy (BEIS) funding provided through the Mineral Products Association (MPA), found that a combination of 70% biomass, 20% hydrogen and 10% plasma energy could be used to eliminate fossil fuel CO2 emissions from cement manufacturing.
We have been testing that theory on an industrial scale at our Ribblesdale cement works in Clitheroe, Lancashire, and, in October 2021, successfully operated a cement kiln at the plant using a mix of 100% net-zero fuels as part of a world-first demonstration using hydrogen technology.
During the demonstration, the proportion of fuels in the cement kiln’s main burner was gradually increased to a wholly net-zero mix, which consisted of tanker delivered hydrogen as well as meat and bone meal (MBM) and glycerine – by-products from the rendering and biodiesel industries respectively. At the 100% net-zero mix, the proportion of fuels in the cement kiln was approximately 47% hydrogen, 12% MBM and 41% glycerine.
The trial demonstrated the pathway to moving away from using fossil fuels in cement and concrete production. If implemented for the whole kiln system, nearly 180,000 tonnes of CO2 could be saved each year at Ribblesdale alone, compared with using traditional coal fuel at the site.
Our fuel-switching trial used ‘grey’ hydrogen as a proof of concept, which can be substituted for ‘green’ hydrogen in the future.
The results from the £3.2 million MPA project will be shared with wider industries and supply chains both in the UK and globally, with the aim of spreading and maximizing the environmental benefits of the technology. It is anticipated that the UK cement industry could save around 2 million tonnes of CO2 a year: equivalent to the annual emissions from 266,000 households.
Our other two projects produce and test green hydrogen as an alternative energy source on site, rather than bring it in by pipeline or tanker.
A green hydrogen demonstration unit has been developed and installed at our Regen GGBS (ground granulated blast-furnace slag) plant in Port Talbot, South Wales, as part of the £9.2 million European Regional Development Fund supported RICE (Reducing Industrial Carbon Emissions) project with the Energy Safety Research Institute at Swansea University.
The aim of the demonstration unit is to replace some of the natural gas used to power the plant with green hydrogen to reduce CO2 emissions and demonstrate the long-term reliability of the combined electrolysis and green electricity production (wind and solar power) to produce hydrogen.
Cement production is energy intensive due to the high temperatures required to produce clinker – the main component of Portland cement. Hanson’s Port Talbot plant produces Regen GGBS, which is used as a replacement for up to 80% of the cement in concrete. Although Regen GGBS is also an energy-intensive product, using large amounts of natural gas and electricity, its carbon footprint is about one-tenth of Portland cement.
Here, a small alkaline electrolyser has been built into a shipping container on site and a set of solar panels and a small wind turbine provide the demonstration unit with electricity that powers it. The electrolyser can efficiently use this energy to split water into hydrogen and oxygen and, in this case, the hydrogen produced is fed directly into the burner. Any hydrogen flowing into the drying system offsets the use of natural gas, reducing carbon emissions.
Oxygen is released into the atmosphere to be consumed by the burner when the hydrogen is combusted. There is no significant change in the combustion fuel, so no modifications to the burner were needed other than an additional feed in, some monitoring equipment, and safety valves.
The oxygen also has value and can be added to any combustion process to improve the burning characteristics, increasing the yielded heat and decreasing the waste gas volume. This would be especially important in a process that burns fuels with a low calorific value, such as refuse derived material, as an enhancement of the oxygen feed in the air intake can have a significant effect on the quality of the combustion process.
The demonstration unit is providing valuable insights into the technology and data are being recorded showing its potential. The next steps are to upscale the technology from this 5–10kW unit to a 100kW unit and then a 200kW unit. These units will fit within a shipping container, leading to an entirely modular design that can be scaled to MW capacity simply by stacking containers alongside one another and connecting them. Each would need to be accompanied by a green energy source that is able to power the units.
Our second trial to produce green hydrogen on site is at Ketton cement works in Stamford, Rutland. It takes a similar approach to the trial in South Wales and mixes the hydrogen produced with fuel for the kiln burner while the oxygen is fed to the main air supply. This is expected to allow an increase in the proportion of alternative fuels and biomass that we burn at the kiln main burner. The main burner of the kiln needs to produce very high flame temperatures to drive the clinker-forming chemical reactions; these temperatures cannot be achieved with biomass fuels alone or even with high biomass content in combination with traditional fossil fuels such as coal.
Hanson are already the largest producers of low-carbon concrete in the UK but the addition of hydrogen in the fuel mix used at the company’s cement plants will help them meet their ambition of supplying net-zero carbon concrete by 2050.
- Subscribe to Quarry Management, the monthly journal for the mineral products industry, to read articles before they appear on Agg-Net.com