Use of Concrete in the Construction of a New Cancer Centre
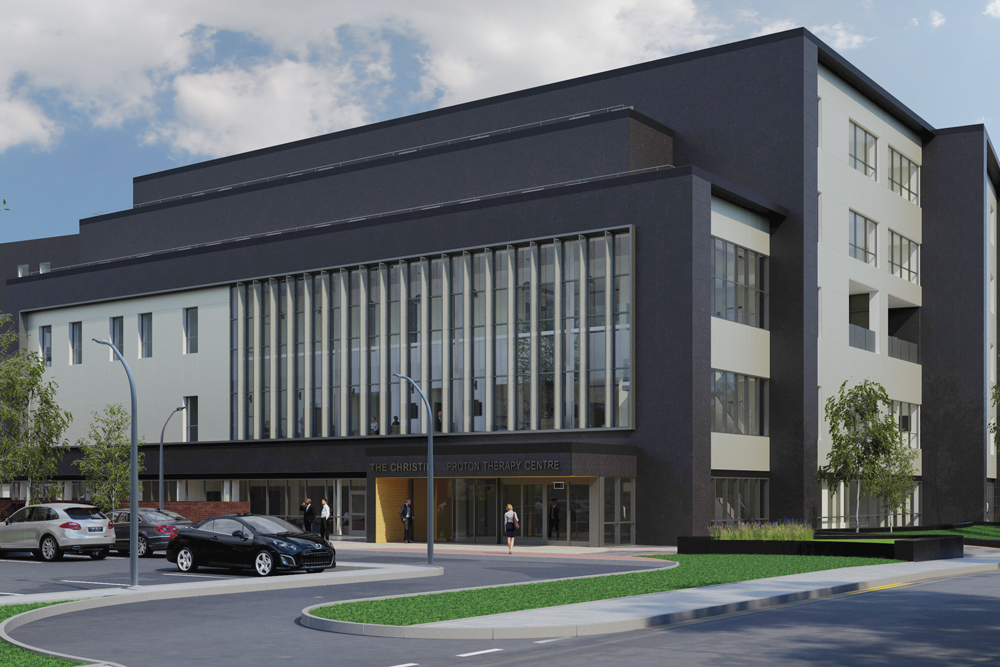
First published in the December 2017 issue of Quarry Management as Beam Blocker
A robust shielding wall is needed to protect medical staff from the potentially harmful effects of regular exposure to proton beam therapy, used in cancer treatments. Christie Hospital in Manchester is the first facility in the UK to use solely concrete in its new treatment centre to meet the exacting radiation shielding requirements
Proton beam therapy is a highly specialized form of radiotherapy that can precisely target inoperable tumours, increasing survival rates in patients and reducing the harmful side effects associated with other cancer treatments. It uses protons – positively charged particles – accelerated to extremely high speeds to produce a high-energy beam. These beams are harmful to those exposed to them over a long period of time, so protecting hospital staff using the equipment was a high priority in the design of Christie NHS Foundation Trust’s new treatment rooms.
Specialist concrete provided the ideal solution for the project — one of the largest cancer treatments centres in Europe — with a 6m thick reinforced barrier providing a robust shielding wall and ensuring against thermal cracking, radiation leakage and shrinkage.
The project involved two separate concrete elements: the first was to hold three treatment rooms and a research and development room; and the second was to house the ‘cyclotron’, an innovative particle accelerator, the size of a saloon car but weighing the same as a jumbo jet. Included within each of the treatment rooms is a 360° gantry and steel structure that weighs 180 tonnes and requires a space as tall as a three-storey house to allow it to operate.
The scale of this project was immense, with Hanson providing concrete for the 20,000m3 pour and 1,700 tonnes of reinforcement over 12 months. Each pour had to be completed during a working day and could not be stopped once started. With more than 100 separate controlled pours, the shielding wall was made up of large geometric shapes between 2m and 6m thick to prevent radiation leaking at stop ends. These form a ‘joggle joint’ arrangement to ensure that there is no direct route for the neutrons to pass through, which would have been the case with a traditional construction joint.
Much of the concrete installation programme was dependent on the ‘striking time’. Since ambient temperature is a key influence in this aspect, a full-scale test pour was carried out close to Hanson’s supply unit with the peak temperature of the concrete, its core and surface being monitored. Thermal cracking and failure to meet the thick density requirement posed high risks to the success of the shielding properties of the concrete. Both were carefully controlled through early engagement and detailed methodology with consulting engineers Arup, and the concrete will continue to undergo ongoing radiation leak testing.
Various specification constraints on the mix composition further added to the overall complexity of the project. Although a relatively high concrete density was required, the thermal constraints and coefficients of thermal expansion limited the coarse aggregate type to carboniferous limestone. In addition, the inclusion of 70% Regen ground granulated blast-furnace slag (ggbs) – with a maximum specified cementitious content of 355kg/m3 and a maximum free water cement ratio of 0.40 – limited the free water content to only 142 litres/m3. The concrete also had to be pumped into the structure within a consistence range of 180mm to 220mm, with 200mm being the optimum target.
‘In isolation, any of these parameters is not difficult to achieve,’ said Terry Balmer, Hanson Concrete’s technical services manager, ‘but in combination they presented a number of potentially conflicting concrete mix design challenges.
‘From early engagement through innovative design to execution, the specialized concrete mix composition had to perform on numerous complex levels outside the parameters that would be expected in conventional construction. Our collaborative work with Heyrod Construction, Interserve and Arup at an early stage helped deliver this bespoke concrete solution that met the onerous project requirements.
‘Other similar facilities will be built in the future and the Christie facility is being promoted as best practice for others to follow.’
- Subscribe to Quarry Management, the monthly journal for the mineral products industry, to read articles before they appear on Agg-Net.com