Topflow Provides The Solution
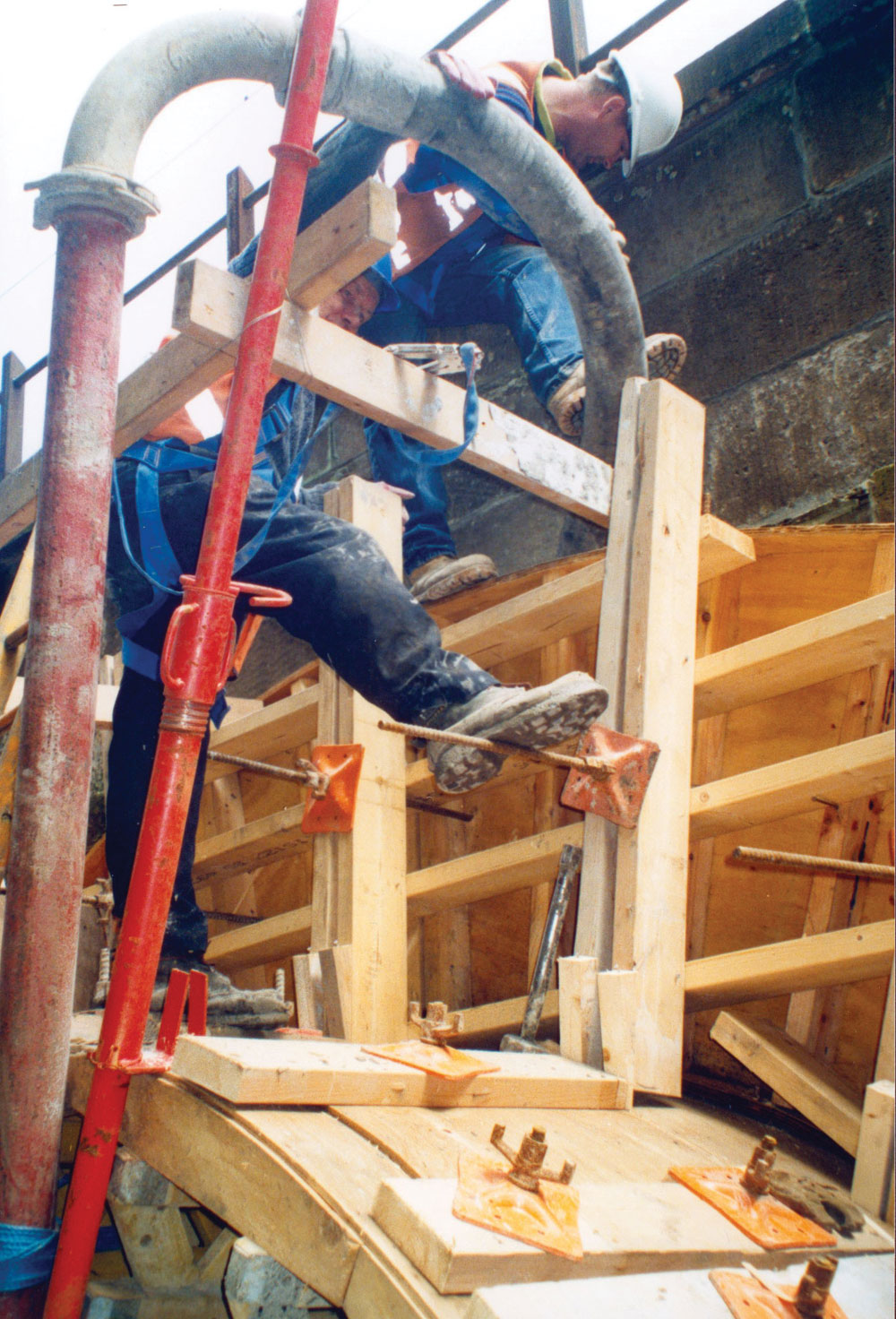
Tarmac highlight some recent uses of their Topflow self-compacting concrete in projects and applications around the UK
A flexible approach to bridge engineering work by Tarmac, using their self-compacting concrete (SCC), recently helped ease potential rail traffic disruption in Scotland. Working for main contractor Carillion Rail, Tarmac were appointed to supply a flowing concrete for the strengthening of the existing masonry arch bridge at Bishopton, north-west of Glasgow.
One of the main challenges to the engineering team was to ensure negligible traffic disruption on one of Scotland’s busier rail routes. The method adopted was to re-line the existing masonry arch, thereby transfering live loads on to new vertical side walls which had been cast earlier using conventional concrete. In addition, the arch had to be cast in one section to ensure total infilling of the arch invert without voidage or construction joints, thereby reducing the need to employ costly secondary grouting.
The use of conventional concrete was ruled out by staff working on the project because congested reinforcement would have acted as a restraint to any material which entered the form. The concrete also had to be placed externally to the ‘live’ side of the line and not via the permanent track, as the line had to remain operational at all times.
As a final architectural touch, the bridge portal was required to have a cast finish replicating the existing block masonry arch, so it was critical that the concrete to be used allowed a superior cast finish.
Tarmac’s Topflow SCC was chosen for the contract as it was felt it clearly addressed the many challenges involved in the project. Topflow’s high fluidity without segregation allowed workers to place the concrete, by pump, from both sides of the bridge. The major benefit arising from this process was that it allowed the busy railway line to remain live rather than reverting to track closures which would have incurred increased costs.
Neil Cochrane, Tarmac Northern’s special products manager, said: ‘This method of placing the concrete proved to be highly successful with little, if any voidage. Our clients Carillion were very happy with the finished product and this was an excellent example of the flexibility and cost-saving benefits associated with using self-compacting concrete.’
The Bishopton Arch contract is just one of several recently completed SCC projects carried out by Tarmac, including work at Napier University in Edinburgh and on the M62 in Leeds.
Topflow SCC is designed to flow under its own weight, filling the available void space without segregation. It flows through or around steel reinforcement, blocks, spacers, saddles, stools or other construction accessories while remaining homogenous. The SCC bond strength has been found to be at least as good as that of conventionally compacted concrete and the material can flow into complex corners without honeycombing or creating voids. The slump flow characteristic is measured using a modified slump test. Typical ‘slump’ or ‘flow’ values fall within the range 650mm to 750mm. Compressive strengths in excess of 80N/mm2 are not uncommon.
An added attraction for the use of SCC could arise from the Physical Agents (Vibration) Directive, which is due to become law by 2005. The proposal will place a range of duties on employers including a requirement to assess the risks to their employees from vibration, to reduce their exposure to vibration and to provide them with information and training on the hazard.?
There is some industry concern that this directive could reduce productivity. SCC, however, offers faster construction, needs fewer skilled workers and its use also eliminates vibration.
More recently, Topflow has been used to construct filter floors and floor-support columns within a complex water works environment. These concrete structures form part of the potable water-processing plant at Welsh Water’s Broomy Hill Water Treatment Works in Hereford, which is being designed and constructed by Laing Construction Utilities Ltd and Paterson Candy, working in partnership with Dwyr Cymru Welsh Water as part of their Asset Management Plan Year 3 programme.
Topflow has been used in two separate areas of the project. First, eight elevated floor slabs and their supporting columns were poured. The Topflow material was required to flow between the complex mat of filtration bushes and reinforcement steel mesh and to flow into the column formwork to cast the reinforced concrete columns beneath, without any physical compaction.
The second application required the addition of stainless steel fibres to the Topflow SCC in order to eliminate the need for reinforcing mesh because the water filtration pipework was too delicate, and hence both the installation of mesh and the use of poker vibrators needed to be eliminated.
Both applications required the flowing nature of the product to encapsulate the intricate pipework fully into the concrete matrix.
Tarmac Western’s special products manager, Richard Hastings, explained why Topflow SCC was used rather than conventional concrete. ‘The first application provided an ideal solution to an engineering problem. It was essential for the concrete to flow under its own weight throughout the filter floor’s permanent formwork and intricate filtration system, and into the reinforced floor-support columns, without the need for applied compaction techniques. A traditional concrete with the required level of flow would segregate and require compaction with vibrating pokers, neither of which were permissible. It was also very important to maintain good level control on the finished concrete surface in order to avoid burying the filter bushes; the high workability of the Topflow made this much easier.’
Laing witnessed the performance of the Topflow in the K-floor and quickly realized a second application for the product. Complex and delicate pipework in the tank base necessitated that the fixing of mesh and the compaction of the concrete be avoided. Topflow, with the addition of DWI-approved stainless steel fibres, was proposed.
Laing project manager, Mike Lancaster, commented: ‘The Topflow concrete has met all of our requirements and exceeded others. It’s easy to place, easy to work with and the early strength gain has been an added bonus. There is a premium on the cost of the material but, given the overall performance, it’s a price worth paying.’
A total of 14 filter floors (K-Floor and D-Floor) were poured during a four-week period. The material was shipped from Tarmac’s Hereford plant, which supplied all Laing’s concrete requirements on site.
One of the more unusual contracts for Topflow SCC took place in Gloucestershire. As part of routine road improvements, Gloucestershire County Council’s Environment Department was obliged to inspect the old mines below the village of Coleford and to carry out any remedial work.
After enlisting the help of a local caving club to survey the network of caverns, which date back to Roman times when miners followed iron ore seams, the council discovered that the caves had become unstable and needed strengthening. This meant that the land needed to be stabilized to safeguard the properties and main road above.
The scheme demanded structural concrete to provide increased integrity to the caverns. However, as the cavern was already unsafe, conventional concrete that would require compaction through vibration was not an option as there was the risk of the cavern caving in. The project’s main contractors, P. Forker Contractor’s Ltd, placed the Topflow using a concrete pump, which pumped down a 20m shaft and along a further 30m through the cavern into the placement area.
A flexible approach to bridge engineering work by Tarmac, using their self-compacting concrete (SCC), recently helped ease potential rail traffic disruption in Scotland. Working for main contractor Carillion Rail, Tarmac were appointed to supply a flowing concrete for the strengthening of the existing masonry arch bridge at Bishopton, north-west of Glasgow.
One of the main challenges to the engineering team was to ensure negligible traffic disruption on one of Scotland’s busier rail routes. The method adopted was to re-line the existing masonry arch, thereby transfering live loads on to new vertical side walls which had been cast earlier using conventional concrete. In addition, the arch had to be cast in one section to ensure total infilling of the arch invert without voidage or construction joints, thereby reducing the need to employ costly secondary grouting.
The use of conventional concrete was ruled out by staff working on the project because congested reinforcement would have acted as a restraint to any material which entered the form. The concrete also had to be placed externally to the ‘live’ side of the line and not via the permanent track, as the line had to remain operational at all times.
As a final architectural touch, the bridge portal was required to have a cast finish replicating the existing block masonry arch, so it was critical that the concrete to be used allowed a superior cast finish.
Tarmac’s Topflow SCC was chosen for the contract as it was felt it clearly addressed the many challenges involved in the project. Topflow’s high fluidity without segregation allowed workers to place the concrete, by pump, from both sides of the bridge. The major benefit arising from this process was that it allowed the busy railway line to remain live rather than reverting to track closures which would have incurred increased costs.
Neil Cochrane, Tarmac Northern’s special products manager, said: ‘This method of placing the concrete proved to be highly successful with little, if any voidage. Our clients Carillion were very happy with the finished product and this was an excellent example of the flexibility and cost-saving benefits associated with using self-compacting concrete.’
The Bishopton Arch contract is just one of several recently completed SCC projects carried out by Tarmac, including work at Napier University in Edinburgh and on the M62 in Leeds.
Topflow SCC is designed to flow under its own weight, filling the available void space without segregation. It flows through or around steel reinforcement, blocks, spacers, saddles, stools or other construction accessories while remaining homogenous. The SCC bond strength has been found to be at least as good as that of conventionally compacted concrete and the material can flow into complex corners without honeycombing or creating voids. The slump flow characteristic is measured using a modified slump test. Typical ‘slump’ or ‘flow’ values fall within the range 650mm to 750mm. Compressive strengths in excess of 80N/mm2 are not uncommon.
An added attraction for the use of SCC could arise from the Physical Agents (Vibration) Directive, which is due to become law by 2005. The proposal will place a range of duties on employers including a requirement to assess the risks to their employees from vibration, to reduce their exposure to vibration and to provide them with information and training on the hazard.?
There is some industry concern that this directive could reduce productivity. SCC, however, offers faster construction, needs fewer skilled workers and its use also eliminates vibration.
More recently, Topflow has been used to construct filter floors and floor-support columns within a complex water works environment. These concrete structures form part of the potable water-processing plant at Welsh Water’s Broomy Hill Water Treatment Works in Hereford, which is being designed and constructed by Laing Construction Utilities Ltd and Paterson Candy, working in partnership with Dwyr Cymru Welsh Water as part of their Asset Management Plan Year 3 programme.
Topflow has been used in two separate areas of the project. First, eight elevated floor slabs and their supporting columns were poured. The Topflow material was required to flow between the complex mat of filtration bushes and reinforcement steel mesh and to flow into the column formwork to cast the reinforced concrete columns beneath, without any physical compaction.
The second application required the addition of stainless steel fibres to the Topflow SCC in order to eliminate the need for reinforcing mesh because the water filtration pipework was too delicate, and hence both the installation of mesh and the use of poker vibrators needed to be eliminated.
Both applications required the flowing nature of the product to encapsulate the intricate pipework fully into the concrete matrix.
Tarmac Western’s special products manager, Richard Hastings, explained why Topflow SCC was used rather than conventional concrete. ‘The first application provided an ideal solution to an engineering problem. It was essential for the concrete to flow under its own weight throughout the filter floor’s permanent formwork and intricate filtration system, and into the reinforced floor-support columns, without the need for applied compaction techniques. A traditional concrete with the required level of flow would segregate and require compaction with vibrating pokers, neither of which were permissible. It was also very important to maintain good level control on the finished concrete surface in order to avoid burying the filter bushes; the high workability of the Topflow made this much easier.’
Laing witnessed the performance of the Topflow in the K-floor and quickly realized a second application for the product. Complex and delicate pipework in the tank base necessitated that the fixing of mesh and the compaction of the concrete be avoided. Topflow, with the addition of DWI-approved stainless steel fibres, was proposed.
Laing project manager, Mike Lancaster, commented: ‘The Topflow concrete has met all of our requirements and exceeded others. It’s easy to place, easy to work with and the early strength gain has been an added bonus. There is a premium on the cost of the material but, given the overall performance, it’s a price worth paying.’
A total of 14 filter floors (K-Floor and D-Floor) were poured during a four-week period. The material was shipped from Tarmac’s Hereford plant, which supplied all Laing’s concrete requirements on site.
One of the more unusual contracts for Topflow SCC took place in Gloucestershire. As part of routine road improvements, Gloucestershire County Council’s Environment Department was obliged to inspect the old mines below the village of Coleford and to carry out any remedial work.
After enlisting the help of a local caving club to survey the network of caverns, which date back to Roman times when miners followed iron ore seams, the council discovered that the caves had become unstable and needed strengthening. This meant that the land needed to be stabilized to safeguard the properties and main road above.
The scheme demanded structural concrete to provide increased integrity to the caverns. However, as the cavern was already unsafe, conventional concrete that would require compaction through vibration was not an option as there was the risk of the cavern caving in. The project’s main contractors, P. Forker Contractor’s Ltd, placed the Topflow using a concrete pump, which pumped down a 20m shaft and along a further 30m through the cavern into the placement area.