Tarmac's New Toplight C Lightweight Concrete
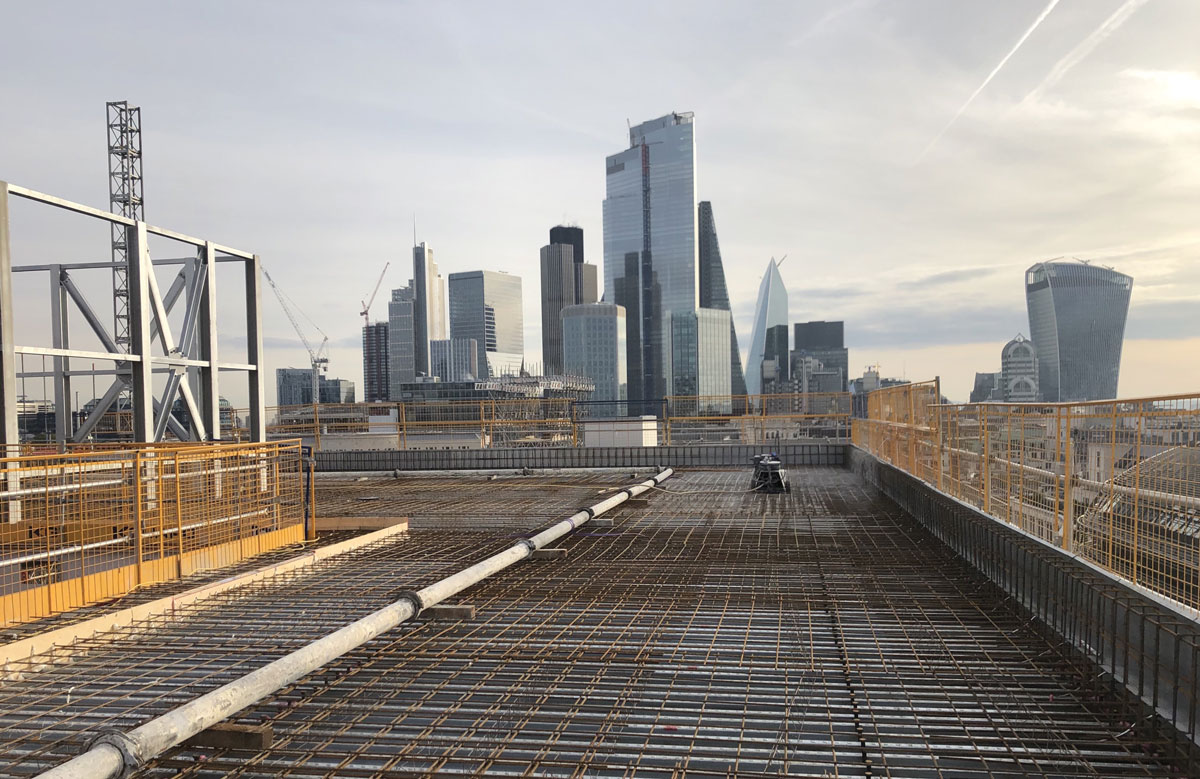
First published in the December 2020 issue of Quarry Management as Reaching New Heights
Tarmac’s new Toplight C lightweight concrete helps construction reach new levels of sustainability
Climate change is influencing UK policy and public opinion like never before, with the Government now committed to legally binding targets to deliver net zero carbon by 2050 and local authorities across the country declaring climate emergencies.
With the built environment contributing a significant percentage of the UK’s carbon emissions through construction and operation, finding new ways and opportunities to collaborate and embrace proactive change is becoming increasingly critical.
Enhancing the longevity of taller buildings and maximizing the time that resources are in use to extract their full value is, therefore, an essential part of a future circular economy, and vital to unlocking more sustainable infrastructure.
The materials we select now as we build for the future are key to extending the usable life of our buildings, providing new opportunities for refurbishment, adaptation and reuse later down the line.
A new, innovative, lightweight and high-strength structural concrete developed by sustainable construction solutions business Tarmac is helping asset owners to achieve some of these objectives and allowing existing buildings to be refitted and repurposed.
Technical director, Brian Kent, explained: ‘When it comes to designing structures that are highly durable and long-lasting with strong frames and cores, building in concrete is the logical choice. To regenerate our city centres, we’re increasingly being asked by clients to provide solutions that help to extend, repurpose and reuse existing buildings – essentially preventing the need to knock down and rebuild that comes with high associated financial and carbon costs.
‘Our new lightweight concrete, Toplight C, has been developed specifically to save weight and provide much lower densities compared with standard conventional concrete. By using an expanded clay aggregate it is possible to construct much lighter flooring decks, for example, which can allow new storeys and extensions to be added on existing foundations and footprints without the need to demolish and start again.’
Expanding horizons
Expanded clay aggregates are not uncommon in the US and in continental Europe, where their use has been well established over several decades in proven materials that can be safely used in all climates. But despite its many benefits, it has yet to be widely adopted in the UK market.
The clay used in the product is dredged from the bottom of rivers and canals and has no special requirements other than needing to remain saturated and stored accordingly to prevent it from drying out.
To manufacture the aggregate, the clay is pre-treated and processed in rotary kilns where it is heated. As the hot clay cools, cold air is warmed and used to dry, heat and expand the clay in the kiln – transforming it into various-sized lightweight aggregates with a hard, ceramic shell and a porous core. This can then be used in the same way as other traditional aggregates to produce a concrete mix that complies with all modern British standards.
Mr Kent continued: ‘The main characteristics of the expanded clay are its low density, being some five times lighter than loose gravel or crushed stone, and its high strength – helping to reduce the weight of some concretes by almost 50%.
‘Toplight C can be produced with a typical density of 1,800–1,900kg/m3 with structural concrete strengths up to 50N/mm2. Put simply, you get more performance from a much lower volume of raw material, as it produces 300% more aggregate per cubic metre than quarried aggregate.
‘The benefits of this work two ways. When used in structural elements such as flooring, the concrete slabs are significantly lighter, making it much easier to add additional storeys to a structure. Equally, if you are constructing a building from scratch, the weight saving means less material is needed overall in its foundations.’
To date, the main applications for the new lightweight concrete have predominantly been in floors and screeds, particularly in steel-framed buildings that include concrete decks and any other situations in retrofit programmes where weight saving is key. However, in practice the material can be used in any structural elements in the same way as any other traditional concrete product – and it is able to be pumped as a ready-mixed concrete or used in precast blocks.
Performance benefits
Tarmac have also adapted a mix to incorporate steel fibres on some projects, eliminating the need for a traditional steel mesh. This not only cuts down on the need for additional steel fixings, but from a practicality perspective it also cuts down on the need for large steel deliveries, which, in turn, reduces the amount of storage needed on site – especially useful on a city centre refurbishment project with limited space.
Mr Kent added: ‘Alongside its overall versatility and ability to save weight, Toplight C additionally delivers improved thermal performance. Building on concrete’s thermal mass properties – that is to say its ability to absorb, store, and release heat slowly, which helps to reduce heating and cooling costs – the ‘air bubbles’ in the expanded clay make it an even better insulator, as well as delivering improved acoustics. The fact the material is also already exfoliated helps to improve its fire resistance over normal-weight concrete.
‘Furthermore, it can be pumped, placed and compacted more easily than similar conventional concretes as well as delivering better floor finishes, which are easier to achieve than traditional lightweight concretes. The reduced weight also helps to reduce deflections and its greater tensile strain capacity can reduce the risk of cracking.’
Practical applications
Despite having only been made commercially available relatively recently, the material has already been used on several major construction projects in the UK. The majority of these have been developments with the circular economic principles of refurbishing, reconfiguring and reinventing buildings to give them a new lease of life.
Alistair Legg, commercial technical manager at Tarmac, explained: ‘We were recently approached to help construct a one-storey rooftop extension at the luxury Nobu hotel and restaurant in London’s Shoreditch, which is famed for blending Japanese design simplicity with the best of British industrial chic.
‘The use of lightweight structural concrete in a pump mix was perfectly suited to the client’s requirements, ensuring a maximum weight loss of 35% with no compromise on structural concrete performance. Pumped 40m vertically on to the new composite deck floor, by adding steel fibres into the mix the composite metal deck system could be installed without the need for traditional expensive and slow steel reinforcement.
‘By reducing the total load, the existing structure did not need to be reinforced or underpinned. This meant the construction programme time was also reduced considerably, ensuring the work could be achieved in the shortest time possible and the hotel could quickly resume business as normal.’
With the circular economy coming under increasingly sharp focus across the built environment, fresh thinking continues to be demanded from every participant in a building’s lifecycle, from materials suppliers and contractors to clients and investors. Brian Kent concluded: ‘The positive collective drive for more sustainable construction means it’s encouraging to see more being done to extend the usable life of our buildings.
‘Many of the barriers that clients face in refurbishing older structures can be solved if materials suppliers are engaged early and able to recommend products such as lightweight concrete at the design stage. Adopting the principles of the circular economy and designing for the long-term will only help us to better meet the challenge of balancing the relationship between longevity and sustainability.’
- Subscribe to Quarry Management, the monthly journal for the mineral products industry, to read articles before they appear on Agg-Net.com