Magnesian Limestone Aggregate In Concrete
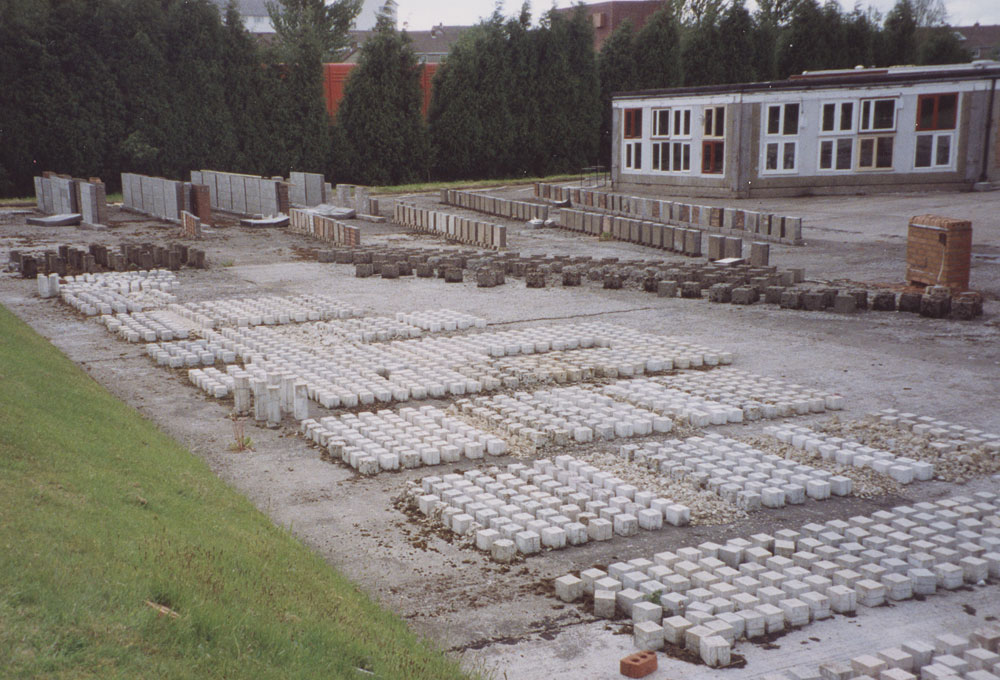
A long-term durability report
Although extensively used in concrete, Magnesian limestones have often been compared unfavourably with Carboniferous limestones because of the wide variability in the aggregates available. A lack of information on the extent of this variability and its effect on performance in service was highlighted when the resource potential of Magnesian limestone outcrops was being assessed in the mid–1980s1. This is the background to a testing programme begun by the Building Research Establishment (BRE) in 1988 — good comparisons have already been recorded for durability data up to five years2 and more data up to 13 years are discussed in this report.
Thirty sources of material were sampled to represent the whole of the Magnesian limestone outcrop, which stretches for a distance of about 150 miles from Nottingham to Newcastle, but which is never much more than about five miles in width. Table 1 shows that, in comparison with other types of limestone, bulk aggregate properties covered a very wide range.
On average, the Magnesian limestones were significantly harder and less porous than the Jurassic limestones, and some of them had properties similar to Carboniferous limestones. Nevertheless, quite a few were extremely weak and porous. In several quarries different horizons had very different properties, but the lateral variation was found to be fairly small. Sometimes up to three distinct layers were quarried separately. In one instance where the output from the different layers was re-sampled after a period of three years, the properties of each were found to remain fairly constant. Two other quarries sampled for the BRE crushed-rock programme3 were re-sampled after a period of 18 years and again, very little difference was found. Petrographic examination of samples frequently showed quite a high variability on the microscopic scale, but bulk properties of the aggregate from a single source were found to be fairly constant over time.
PREVIOUSLY REPORTED RESULTS
The following conclusions were reached after five years2:
- Concretes to a consistently high grade can be made from combinations of Magnesian limestone coarse aggregate and natural sand; wide variations in the strength and porosity of the coarse?aggregate have minimal effect.
- Crushed Magnesian limestone sands are suitable for use in concrete, especially those from?sources where the coarse aggregate absorption value is less than 4%. Sands from sources where the coarse aggregate absorption value is in the range 4–7% may also be acceptable in many circumstances, however an increased requirement for dust removal is likely.
- Excellent frost resistance in a severe outdoor exposure test on concrete was obtained for all coarse aggregates with water absorption values up to 3.5%, or up to 6.5% where the median pore diameter was above 5mm.
- Excellent frost resistance has also been obtained for five years in a less-severe outdoor exposure test in which pore space was introduced into the aggregate by a partial natural drying of the concrete before exposure. This was achieved in natural sand mixes with coarse aggregate absorption values up to 10%, and in all-in mixes with coarse aggregate absorption values up to 7% for all samples of Magnesian limestone.
- Bulk permeability measurements for Magnesian limestone concrete are good, suggesting that these concretes will not increase corrosion risks for reinforcement at recommended depths of?cover. There are, however, increased risks for poor cover, particularly for aggregates with larger pores if these are interconnected.
Exposure site studies up to 20 years recently reported for concretes made with Jurassic limestone aggregates4 provide some insights on testing in the longer term. Some of the test concretes fully exposed to the weather on the BRE exposure site in Watford had sustained corrosion damage to steel reinforcement with a low depth of cover (10mm). Although this had occurred mostly with the highly porous aggregates, the more significant correlation was with the strength grade of the concrete. Following a detailed consideration of these observations alongside data on general site practice, it was concluded that no additional cover was required for porosity in Jurassic limestone aggregates. Current specifications including achievement of the required strength grade for the concrete, were sufficient to ensure that quality in the built environment was not reduced.
Carbonation tests were carried out using a phenolphthalein indicator to show the extent of neutralization of the alkaline environment in the concrete by the ingress of atmospheric carbon dioxide. Very little carbonation was observed for the outdoor specimens. Gas diffusion is blocked by pore water in damp concrete, however the carbonation reaction requires water so that it cannot occur if the concrete is too dry. Concretes stored indoors at a constant relative humidity of 65% generally show the highest rates of carbonation, and this has been found to correlate with the total water/cement ratio of the concrete.
It has been noted4 that the minimum recommended depth of 20mm for reinforcement cover in ‘mild’ conditions could be reached in 5–10 years with Jurassic limestone aggregate (or less time where a particle of aggregate bridges between the surface and the reinforcement) rather than 25–35 years with low-porosity aggregates. However, corrosion of steel reinforcement in the absence of chlorides is only significant when the relative humidity of the concrete is above 80% (BRE Digest 444, Part 1)5. The minimum cover specified for mild conditions is designed mainly to assist full compaction of the concrete and should also be sufficient to provide protection during the construction period. Subsequent exposure to moisture would constitute a change to ‘moderate’ exposure conditions and the concrete would be susceptible to corrosion damage whether or not porous aggregates were used.
Similar exposure regimes have been used for concretes containing Magnesian limestone aggregates. In addition, some specimens were placed in a sheltered outdoor environment (exposed to outdoor temperature and humidity but protected from rain) equivalent to moderate conditions.
DURABILITY RESULTS
A number of different exposure conditions have been used in this testing programme to simulate both ‘normal’ and ‘worst-case’ conditions. Concretes were made with aggregates which had been allowed to saturate in water for either three or five days. For the worst-case conditions, the resulting concretes were placed on the BRE exposure site at East Kilbride in mid-December with no opportunity for drying before the onset of winter. Compressive strength tests carried out on 100mm cubes after 10 years’ exposure revealed no significant extra deterioration, giving further support to the guidance on freeze/thaw resistance given after five years. In addition, a number of other specimens have been examined for carbonation and damage due to reinforcement corrosion.
Reinforcing bar specimens on BRE outdoor exposure sites
Concrete prisms measuring 100mm x 100mm x 300mm were prepared with rusty and shot-blasted reinforcing bars buried at depths of 10mm and 20mm (ie Four bars per specimen) and placed on various BRE outdoor exposure sites. The preparation of the specimens included a standard water cure up to 28 days and allowance for a short period of drying before the onset of any frosts. A cement content of approximately 330kg/m3 was used with and without air entrainment. Mixes were prepared either all-in or with a natural siliceous sand. Figure 1 gives the results for all-in specimens placed outdoors at BRE Watford and in the spray zone at BRE's sea water exposure site at Shoeburyness. Corrosion damage was visible on a total of 12 all-in specimens and only one of the specimens with a natural sand.
The amount of damage observed on the two sites was roughly equivalent, with six or seven specimens from each site showing spalling of the cover over rusty bars buried to a depth of 10mm. In only one case was spalling observed over a clean reinforcing bar, and no damage was observed over bars buried to a depth of 20mm. All specimens in the spray zone were air entrained; only six of these mixes were used on the Watford exposure site, the remainder did not contain air-entraining agent.
Although there is a reasonable amount of scatter in figure 1, the most dominant factor for determining the risk of damage appears to be the strength of the concrete. Nearly all the specimens with strengths in the range 20–30N/mm2 showed some damage, but for 30–40N/mm2 they were mostly undamaged. Nevertheless, specimens in the range 40–50N/mm2 were not completely immune — there is one instance of damage for an aggregate with a fairly high absorption value (6.5%). It is interesting to note that duplicate prisms showed different results at the two exposure sites. In figure 1 it can be seen that for aggregates of absorption value 6.5% there is another data point for an undamaged yet low-strength prism. The aggregate for this was taken from a different source (over 50 miles away) but had an identical absorption value and very similar pore-size distribution.
With regard to the prisms made with natural sand, all had strengths above 35N/mm2; the only one showing any damage contained coarse aggregate with an absorption value of 10.3% and had a strength of 37N/mm2.
The meaning of these results in relation to the design life of structures needs to be interpreted with caution. For a design life of 50 or 100 years, a cover of at least 40mm or 50mm would be specified, and an extrapolation of results obtained for a cover of 10mm after 11–13 years is not directly comparable. Nevertheless, it is useful to consider this as a basis for further discussion. Assuming a ‘root square’ law for the progression of damage with time, adequate protection at 10mm after 11–13 years extrapolates to 50 years for 20mm and 200 years for 40mm (nb. the depth of cover achieved on construction sites may frequently vary from the target value by ±20mm5). In normal practice, a concrete strength grade of not less than C35 would be specified for this degree of exposure, and this is approximately the criterion for ‘no damage’ which may be inferred from figure 1.
Corrosion of reinforcement requires oxygen and water but is normally initiated by carbonation or the ingress of chlorides. The normal mechanism for carbonation is through gas diffusion of carbon dioxide from the atmosphere into the concrete, neutralizing the alkaline protection to steel provided by set cement paste. When fully exposed to the weather the concrete remains wet for long periods, thus blocking gas diffusion. Sufficient drying of the concrete to support carbonation occurs only during brief periods, and thus the observed depth of carbonation in the cement paste after 10 years was only 1–2mm. Porous aggregates had a two-fold effect. First, pore water in particles at the surface tended to be fully neutralized (but with no visible effect on cement paste at greater depths), and secondly, the higher total water content of the concrete delayed drying of the concrete, thus reducing the opportunity for carbonation. The result of these effects would be to increase the risks of corrosion for poor cover (up to about 20mm) and to reduce risks at greater depths of cover.
With regard to exposure to salt in the Shoeburyness spray zone, specimens showed some uptake of chloride but not at levels sufficient to be the sole cause for the initiation of corrosion. For specimens exposed at both sites, it would appear that long-term protection to reinforcement could be controlled by liquid diffusion/ permeation processes just below the surface few millimetres of the concrete.
Permeability
Table 2 shows, from a few examples, that liquid water permeability measurements for Magnesian limestone concretes give no cause for concern in relation to other concretes. Measurements were made using 150mm diameter and 50mm thick discs following curing in water for 28 days in a ‘Cembureau’-type permeability cell, as in previous experiments6. For structural grades of concrete, the permeability is controlled by the cement paste and not by the porosity of the aggregate.
Durability in sea water
In addition to the reinforcing bar specimens placed in the spray zone at BRE’s exposure site at Shoeburyness, similar specimens, but this time containing only one reinforcing bar (with 45mm of cover), were placed in fully immersed and tidal environments. Although the cement content of about 330kg/m3 in these specimens was too low to prevent the ingress of chloride sufficient to initiate corrosion, no evidence of this (eg cracking) was visible on any of the specimens after 11–13 years of exposure. Some corner loss was evident on the immersed specimens, but there was generally little surface damage on the tidal specimens, most of which were air-entrained. Table 3 indicates that chloride ingress was significant even at a cement content of 480kg/m3. For results expressed with respect to the weight of cement, these figures should be multiplied by a factor of about five. The concrete made with the high-absorption aggregate has taken in higher levels of chloride, however it should be recognized that this has been assisted by the higher total void space in the concrete. In particular, the chloride content in the surface 10mm is closely related to the total water content in the original concrete mix, ie the chloride concentration in the pore water is approximately the same in all three examples.
Protection of reinforcement in sheltered environments
The highest rates of carbonation are achieved at a constant relative humidity of 65%, but in the absence of chlorides the rate of corrosion of steel reinforcement is insignificant unless the relative humidity is allowed to rise above 80%. Indoor environments are classified as ‘mild’ because they should not reach such humidities, and certainly not for any extended period of time during which the internal humidity of the concrete at the reinforcement could equilibrate at a humidity of greater than 80%. Consequently, fairly low depths of cover to reinforcement are permissible. Nevertheless, rates of carbonation can be high, and reinforcement may be subject to corrosion should there be a sustained change to much wetter conditions (eg through persistent problems of leakage or condensation).
Porous aggregates have been shown7 to increase rates of carbonation in concretes kept at a constant relative humidity of 65%, but this in itself could not support increased corrosion. Since variability in cover achieved on construction sites is similar to the depths of cover required for ‘mild’ conditions, it must be assumed that carbonation will have reached at least some of the reinforcement within a few years of construction. Thus any subsequent change to ‘moderate’ or ‘severe’ conditions will lead to corrosion of the reinforcement, whether or not porous aggregates were used in the concrete.
Moderate conditions may allow for an intermediate rate of carbonation and support corrosion of embedded metal, and thus a number of examples of Magnesian limestone concretes were placed in a sheltered environment protected from rain but fully exposed to atmospheric humidity and temperature conditions. Some results are given in figure 2 for concrete mixes made with natural sand and a cement content of 330kg/m3. All the concretes were at the same free water/cement ratio and the specimens were cured in water for 28 days before exposure for approximately 13 years. Average and maximum carbonation depths were recorded and when plotted against the water-absorption value of the coarse aggregate show correlations which are significant, although this is only a weak correlation for the mean depth of carbonation.
Some further results are given in figure 3 for concrete mixes made with crushed rock fines and a comparison is made against the equivalent mixes using natural silica sand (ie with the same coarse aggregates and cement content of 330kg/m3). With the all-in mixes, mean carbonation results were much higher and gave a stronger correlation with the water-absorption value of the coarse aggregate. These results are in line with earlier work2 on the strength of concrete containing Magnesian limestone aggregates, which indicates that for natural sand mixes the strength is only weakly correlated with the porosity of the aggregate, but that this is more evident if crushed rock fines are substituted. Figure 4 shows the mean carbonation results plotted against concrete strength. The strong negative correlation supports the concept of durability grades rather than cement content for ensuring adequate carbonation resistance in concrete. Where the substitution of an aggregate reduces the strength of the concrete, the cement content needs to be increased to compensate. For Magnesian limestones, this applies particularly to the use of a fine aggregate produced from the same source as a high-absorption coarse aggregate.
CONCLUSIONS
Durability tests up to 13 years for concretes containing Magnesian limestone aggregates have confirmed a good all-round performance for these aggregates as long as good practice is followed. In these latest studies, the results have emphasized the importance of concrete cover and strength grade to achieve adequate protection for steel reinforcement in ‘moderate’ and ‘severe’ environments. A concrete grade of at least C35 and preferably C40 should be ensured. This is essentially what British Standards have required in recent years, but it seems particularly important to emphasize this in relation to the use of porous aggregates. A good-quality cement paste is required to control the access of aggressive agents through the aggregate pores. While it has been found that a consistently high-strength grade can be achieved for most Magnesian limestone aggregates in conjunction with a natural sand, this is not necessarily so if this sand is substituted by crushed Magnesian limestone fine aggregates. In these cases it will often be necessary to increase the cement content to achieve the correct grade of concrete appropriate to long-term durability.
The previously reported conclusions listed at the beginning of this paper remain unaffected by these latest results.
ACKNOWLEDGEMENT
This work has been funded by the Construction Directorate of the Department of Trade and Industry.
REFERENCES
- Rendel Geotechics Ltd, ‘Outline study of the Magnesian Limestone in the United Kingdom’, DOE Contract PECD 7/1/88, London, Rendel Geotechnics, 1988.
- COLLINS, R.J.: ‘Magnesian limestone aggregate in concrete’, BRE Information Paper IP1/98, BRE, Watford, 1998.
- TEYCHENNE, D.C.: ‘The use of crushed rock aggregates in concrete’, BRE Report, Watford, 1978.
- COLLINS, R.J.: ‘Porous aggregates in concrete: Jurassic limestones’, BRE Information Paper IP7/01, BRE, Watford, 2001.
- BRE Digest 444, ‘Corrosion of steel in concrete. Part 1: Durability of reinforced concrete structures’, BRE, Watford, 2000.
- COLLINS, R.J.: ‘Lower-grade aggregates in concrete: long-term durability report’, Quarry Management, 1995, vol. 22, no. 12, pp13–21.
- COLLINS, R.J.: ‘Carbonation:comparison of results for concretes containing pfa, cementitious slag or alternative aggregates’, Materials Science and Technology, 1987, vol. 3, pp986–992.