Concrete Sustainability
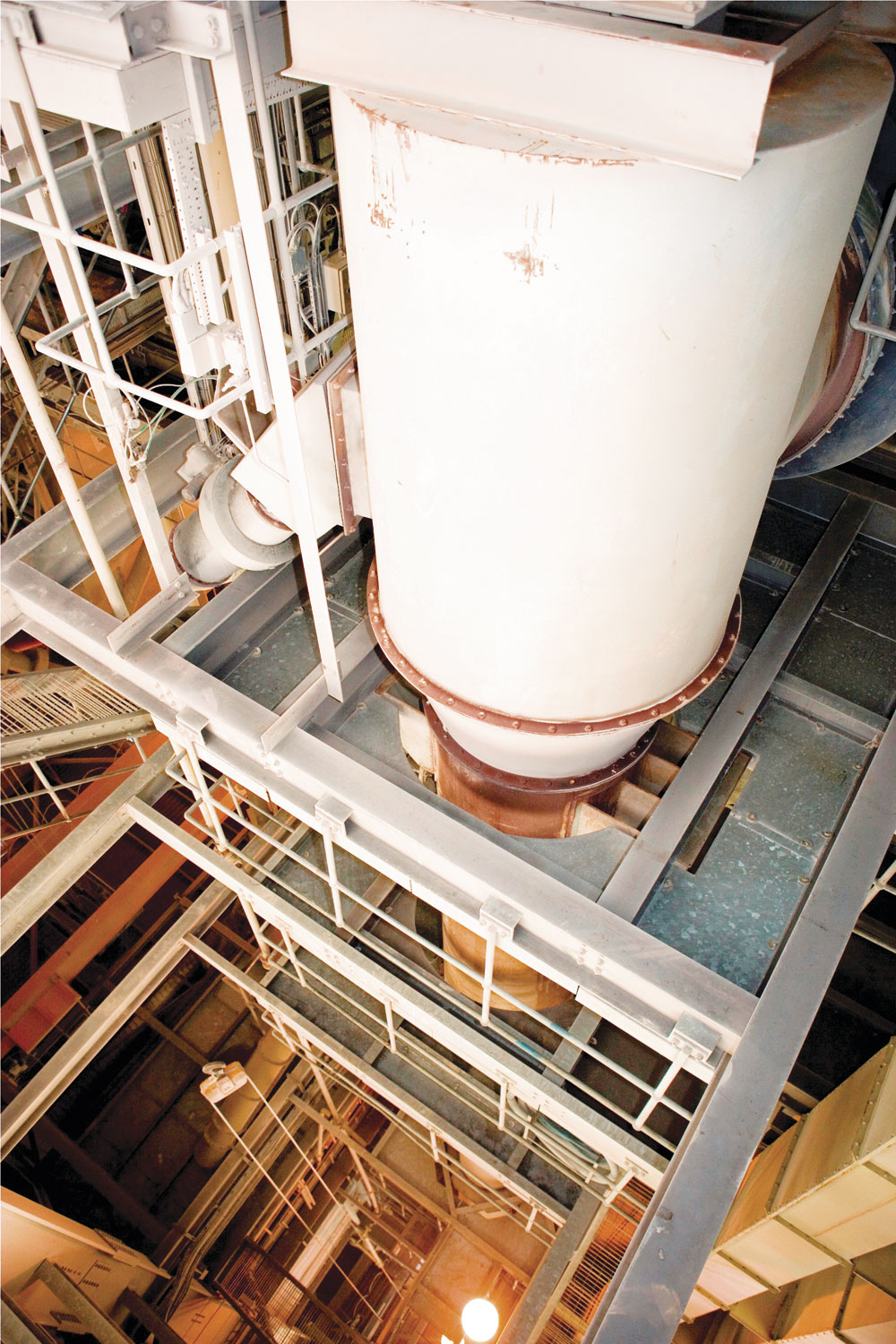
With the appetite for more environmentally friendly concrete continuing to grow, Hanson’s Regen sustainable cement replacement is helping to reduce the carbon impacts of concrete production and use
As the UK construction industry seeks to reduce its carbon footprint, the demand for building products that reduce the environmental impact of a project is increasing.
Concrete is generally regarded as a high-emissions product, but using cement replacements, such as ground granulated blast-furnace slag (ggbs) and pulverized fly ash (PFA), can significantly reduce its energy use and carbon emissions.
Hanson Cement are the only UK manufacturers of ggbs, which they sell under the Regen brand. It is a by-product of the iron-making industry and its use in concrete reduces embodied CO2 emissions by 900kg per tonne of cement – making it the most sustainable cement replacement product on the market.
Production process
The cementitious properties of blast-furnace slag were discovered in the late 19th century and it has been used in concrete manufacture for more than 100 years.
Blast-furnaces operate at temperatures of up to 2,000°C and are fed with a carefully controlled mixture of iron ore, coke and limestone. The iron ore converts to pig iron, which sinks to the bottom of the furnace while the remaining materials form a slag that floats on top of the iron.
The molten iron and slag are drawn off at regular intervals and the slag is monitored to check the performance of the furnace and to ensure that it has a consistent chemical composition.
After being tapped from the furnace and separated from the iron, the slag is rapidly cooled in water. This process is known as granulation as it produces glassy granules, similar in appearance to coarse sand, which have excellent cementitious properties.
Ground granulated blast-furnace slag can be used as a replacement for cement because the hydration process is very similar to that of Portland cement. When Portland cement reacts with water, the insoluble hydration products form close to the cement particle. The more-soluble product of hydration (calcium hydroxide) precipitates as discrete crystals, surrounded by large pores. When ggbs particles are also present, both the ggbs and Portland cement hydrate.
Additionally, the ggbs reacts with the excess of calcium hydroxide to form a finely dispersed hard gel, which fills the larger pores. The result is a hardened cement paste which contains far fewer calcium hydroxide crystals and, therefore, has fewer larger capillary pores. The reduction in free calcium hydroxide makes concrete chemically more stable, and the finer pore structure limits the ability of aggressive chemicals to diffuse through the concrete.
Sustainability
Regen reduces the carbon impact of concrete through both its manufacture and use.
As Regen is made by reusing the slag produced in iron-making, its manufacture requires a lower amount of energy and produces around one tenth of the CO2 emissions of Portland cement.
It also produces very low emissions of the harmful gasses SO2 (sulphur dioxide) and
NOx (nitrogen oxides), requires virtually no quarrying or mineral extraction and its use prevents thousands of tonnes of waste being disposed to landfill.
The production of 100m3 of concrete uses 32 tonnes of cement. Replacing 50% of the cement with Regen saves 12.96 tonnes of CO2, which is equivalent to taking 42 cars off the road for one year, or 41 years of electricity usage in the average home.
The increased durability of concrete manufactured using Regen further reduces a project’s environmental impact by reducing the amount of repair and maintenance required and by extending the service life of the structure.
Durability
Concrete produced with Regen has a lower heat of hydration, which reduces the risk of early-life thermal cracking – a factor that is critical on large pours. The percentage of Regen used directly affects the heat of hydration: a replacement level of around 70% (resulting in a temperature reduction of up to 40%) is recommended for large pours such as in the construction of The Shard in London, which involved the UK’s largest ever concrete pour.
Concrete can often come under attack from sulphates which occur naturally in the ground and can sometimes have a harmful effect on the concrete, causing it to crack and disintegrate.
The main sulphate reactions are known as ettringite and thaumasite, and the use of Regen in concrete is recognized greatly to increase resistance to this type of attack. Indeed, in the latest British Standard for concrete (BS 8500), the only recommendation for the most severe sulphate exposure is a concrete with a cement replacement of at least 66% ggbs.
Ettringite is the primary sulphate reaction that causes disruption of hardened concrete and is associated with one of the minor compounds in Portland cement – tricalcium aluminate. This can combine with sulphate ions that have penetrated the concrete and form a new hydrate (ettringite) which occupies a volume greater than the original constituents. This generates high internal stresses in the concrete that can cause it to crack and disintegrate.
Thaumasite is another form of sulphate attack and has been recognized as a problem after the discovery of its effects on some M5 motorway bridges. Thaumasite is a hydrate which forms at temperatures below 15°C through a reaction between cement paste hydrates, carbonate and sulphate ions. Its formation reduces the cement paste to a soft mulch, undermining the concrete’s durability and stability.
Concretes are also at risk from chloride attacks which break down the passive layer that protects steel reinforcement. This layer is formed on the surface of the steel as a result of the high-alkaline environment produced by hydrating cement. Certain types of concrete are more vulnerable to attack because it is easier for the chloride ions to reach the steel reinforcement.
When Portland cement hydrates, the resultant pores are relatively large and can easily allow chloride ions to penetrate into the heart of the concrete to attack the embedded metal. The result is rapid corrosion of the steel reinforcement, which can take the form of localized pitting or general corrosion.
To prevent the penetration of chloride ions, a dense concrete of very low permeability needs to be produced and this can be achieved by incorporating ggbs.
Where structures are subject to attack from chlorides from an external source, a minimum of 50% ggbs should be used, with a higher proportion used in areas where high levels of chlorides will be encountered.
Appearance
Another benefit of specifying Regen is its appearance. It provides a lighter-coloured finish than concrete made using Portland cement-only mixes, providing greater reflectivity and better visibility – and therefore safety – in dark environments.
Using Regen also reduces efflorescence, the process whereby soluble salts which occur naturally in Portland cement migrate to the surface of the concrete forming a white deposit.
Because of its near-white colour, Regen can be used as a replacement for white cement, with only a minimal difference in whiteness.
Applications
Regen is particularly suitable for projects where sustainability and durability are essential requirements. It can be used in all types of concrete and in all parts of a structure – from piling and floors to columns and roofs.
It is commonly used in soil-stabilization work; to replace a proportion of the cement when preparing mortars; in precast concrete structures; and in paving and street furniture.
It can also be used for specialist projects, such as the encapsulation of radioactive material, sea defences and the construction of wind farms.
Moving forward
Hanson research has shown that there is a huge appetite for more sustainable concrete, but more needs to be done to ensure the benefits of additions such as Regen are readily understood at the early design and specification stages.
As part of their ongoing support for the brand, Hanson offer RIBA-accredited continual professional development (CPD) presentations on the specification and the use of Regen and other cement substitutes in sustainable construction. For further information visit: www.hanson.com/uk/regen